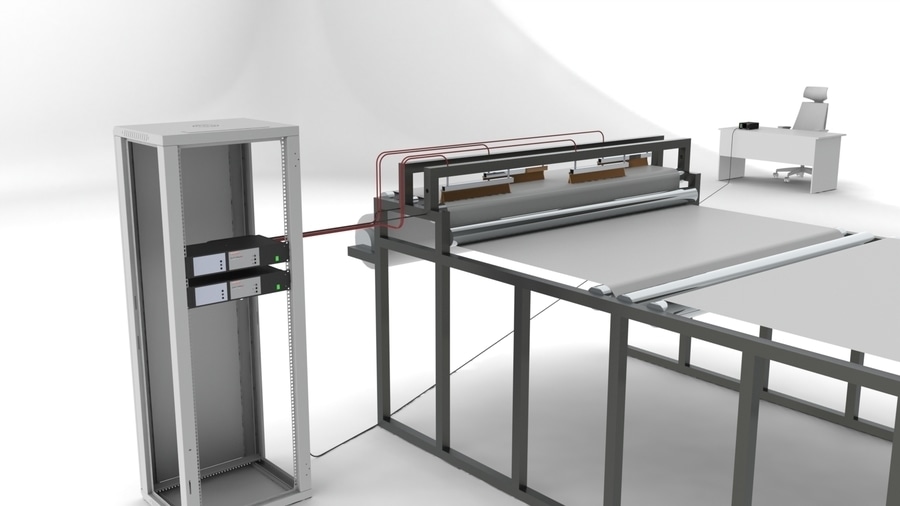
Automatische Übersetzung anzeigen
Dies ist eine automatisch generierte Übersetzung. Wenn Sie auf den englischen Originaltext zugreifen möchten, klicken Sie hier
#White Papers
Prüfung von stranggepressten Plattenmaterialien
Die Produktreihe DCCT Pro2
Einführung
Die Herstellung von Polymerfolien und -platten erfolgt in der Regel mit Hilfe einer Plattenform, die mehrere Meter breit sein kann. Solche Formen werden in der Regel von einem oder mehreren Schneckenextrudern beschickt, und die Folie wird durch Kalanderwalzen geführt und beim Abkühlen gestützt. Anschließend kann sie gewalzt oder in Platten geschnitten werden, je nach Dicke.
Siehe Abb. 1, Typischer Extrusionsprozess
Obwohl die Extruderlinien zuverlässig sind, kann es wünschenswert oder notwendig sein, das extrudierte Material elektronisch auf Löcher zu prüfen, was in der frühestmöglichen Phase des Prozesses am effizientesten ist. Die Elektroden werden auf beiden Seiten des zu prüfenden Materials angebracht, und das Gerät legt eine kontinuierliche Ladung an die obere Elektrode an. Jede Fehlstelle im Material lässt einen Funken zwischen den Elektroden passieren, der vom Gerät erkannt und gemeldet wird.
Siehe Abb. 2, Lage der Testelektroden
Die DCCT-Geräte von Buckleys sind für diesen Zweck ideal geeignet, da sie einen hochstabilen Hochspannungs-Gleichstromausgang mit einem einstellbaren Empfindlichkeitsalarm liefern. Darüber hinaus sind diese Geräte mit softwaregesteuerten Nullspannungs-Relaisanschlüssen ausgestattet, die synchron mit dem Alarm arbeiten und eine Verbindung mit SPS-Steuerungen oder einer Vielzahl anderer Geräte, z. B. einem Farbsprühgerät zur Markierung, ermöglichen. Darüber hinaus ist das Gerät mit Verriegelungsanschlüssen ausgestattet, so dass der Hochspannungsausgang ferngesteuert und deaktiviert werden kann, falls der Sicherheitsfall dies erfordert. Außerdem ist ein Fehlerzähler vorhanden.
Das Gerät ist in der Lage, 0,9-40kV zu erzeugen, und die Alarmschwelle reicht von 10 bis 400uA. Beide Werte können vom Benutzer festgelegt werden, und die Einstellungen können mit einem vom Manager definierten Passcode gesperrt werden.
Die Mindestspannung, die für die Prüfung eines bestimmten Materials erforderlich ist, hängt von der Dicke des Materials ab. Die maximale Spannung, die verwendet werden kann, hängt von der Dicke und der Durchschlagfestigkeit des Materials ab. Üblicherweise werden die Prüfspannungen zwischen diesen beiden Grenzwerten festgelegt, um sicherzustellen, dass nicht senkrechte Fehler im Material erkannt werden, während gleichzeitig das Risiko, dass die Prüfung selbst den Schaden verursacht, der erkannt werden soll, minimiert oder idealerweise ganz ausgeschlossen wird.
Koronaentladung und Materialstromaufnahme
Während wir Luft als einen äußerst effektiven elektrischen Isolator kennen, sind wir auch mit Funken vertraut, die sich durch die Luft bewegen - Blitze sind ein offensichtliches Beispiel, aber die Zündkerzen von Benzinmotoren und Piezo-Gasfeuerzeuge sind vielleicht noch relevanter. In diesen Fällen sorgt die Konstruktion des Systems dafür, dass die Elektrodenspannung sehr schnell ansteigt und fast augenblicklich abfällt, wenn der Funke auftritt - dies ist für ein kontinuierliches Prüfsystem nicht hilfreich, da die Spannung immer vorhanden sein muss und der Funke nur dann auftritt, wenn ein Fehler zwischen den Prüfelektroden passiert. Dementsprechend muss das Hochspannungssystem eine erhebliche Spannungsdifferenz zwischen den Prüfelektroden erzeugen und aufrechterhalten.
Es gibt zwei physikalische Phänomene, die der Aufrechterhaltung dieser Spannungsdifferenz entgegenwirken;
Das erste ist die Korona-Entladung. Dabei handelt es sich um einen Prozess, bei dem die Luft, die einen geladenen Körper wie die Elektrode umgibt, ionisiert wird und sich dadurch von dem geladenen Körper wegbewegt - dies verursacht einen kontinuierlichen Stromfluss von der Elektrode und ist weitgehend von der angelegten Spannung abhängig, wird aber auch erheblich von der Form des Körpers beeinflusst - spitze Gegenstände verursachen eine stärkere Entladung als kugelförmige - und Elektroden mit Metallbürsten sind für diesen Effekt besonders anfällig.
Der zweite Faktor ist die Materialverschleppung. Hochisolierende Materialien können als Kondensatoren wirken und halten eine dielektrische Ladung auf ihrer Oberfläche, insbesondere wenn auf der gegenüberliegenden Oberfläche eine Gegenladung vorhanden ist. Wenn das Material die Elektroden durchläuft, kommt es zu einer Ablagerung von Ladung auf der Materialoberfläche, die durch das durchlaufende Material von der Elektrode weggezogen wird, was einen weiteren Stromfluss von der Elektrode darstellt. Die Stärke dieses Stroms ist abhängig von dem zu prüfenden Material, der Breite der Elektrode und der Geschwindigkeit, mit der das Material die Elektrode passiert.
Es ist also zu erkennen, dass mit zunehmender Dicke des zu prüfenden Materials die erforderliche Spannung zunimmt, was zu einem Anstieg des Koronaentladungsstroms führt. Mit zunehmender Breite des Materials oder mit zunehmender Geschwindigkeit des Materials erhöht sich auch der Materialentladungsstrom. Diese Faktoren müssen bei der Spezifikation eines HV-Systems berücksichtigt werden. Die Summe des Koronastroms und des Materialentladungsstroms ist der Gesamt-Ruhestrom, Iq, der Einfachheit halber.
Buckleys hat die Möglichkeit, Materialtests durchzuführen und bietet gerne Ratschläge zu den zu erwartenden Korona- und Materialentladungsströmen für geplante Installationen an. Aufgrund der Natur der Entladungen und ihrer sehr spezifischen Abhängigkeit von der Umgebung und der Umwelt können diese Ratschläge jedoch immer nur allgemeiner Natur sein.
Grenzwerte für die Geräteleistung
Die DCCT-Geräte von Buckleys sind so konzipiert, dass sie einen begrenzten Ausgangsstrom liefern, vor allem um sicherzustellen, dass der Ausgang innerhalb der von der IEEE festgelegten Grenzwerte bleibt, um einen tödlichen Schlag für Personen zu verhindern, die versehentlich die Hochspannungselektroden oder die Verkabelung berühren. Dies hat zur Folge, dass die Ausgangsleistung bei einer bestimmten Spannung begrenzt wird, wie aus dem Diagramm in Abb. 3 ersichtlich ist.
Siehe Abb. 3, Typische Ausgangsleistung bei 40 kV
Die rote Linie im Diagramm in Abb. 3 zeigt die Leistungsgrenze als Grenzwert für den Dauerstrom über den Ausgangsspannungsbereich des DCCT-Geräts. Im Idealfall fällt der Strombedarf Iq bei der erforderlichen Spannung in den grün umrandeten Bereich. Ist der Bedarfsstrom Iq jedoch ausreichend hoch, führt er zu einem Absinken der Ausgangsspannung. Solange die resultierende Spannung ausreichend hoch bleibt, um die Prüfung zuverlässig durchzuführen, ist dies akzeptabel. Wenn es jedoch zu einer Spannung unterhalb des erforderlichen Minimums führt, werden Fehler bei der Prüfung möglicherweise nicht erkannt.
Dies führt unweigerlich dazu, dass einige Kombinationen von Materialdicke, Extrusionsbreite und Extrusionsgeschwindigkeit die Leistung eines einzelnen Geräts übersteigen.
Buckleys Lösung
Dementsprechend hat Buckleys eine modulare Bauweise des DCCT entwickelt, die es ermöglicht, bis zu vier Elektroden von einer einzigen Befehlsstation aus zu steuern. Die modularen Einheiten sind in einem 2U 19"-Rack-Gehäuse untergebracht und werden mit der notwendigen Hardware für die Installation geliefert.
Bei der herkömmlichen Methode war es notwendig, die Breite der Extrusion auf das Maß zu beschränken, das von einer einzigen Hochspannungsquelle abgetastet werden konnte, oder mehrere Geräte zu kaufen, um mehrere Elektroden anschließen zu können.
Mit dem modularen Buckleys DCCT Pro2 können mehrere Elektroden jeweils an eine eigene Quelle angeschlossen werden, mit einer einfachen gemeinsamen Steuerschnittstelle, die die Prüfung breiterer, dickerer Materialien bei höheren Liniengeschwindigkeiten ermöglicht. Darüber hinaus verfügt jede Ausgangsstufe über einen eigenen Relaistreiber, was eine präzisere Lokalisierung der erkannten Fehler ermöglicht.
In der nachstehenden Abbildung wurden zwei Zweikanalgeräte zur Ansteuerung von vier unabhängigen Elektroden verwendet. Eine der Einheiten enthält ein Bedienfeld, das jedoch auf Wunsch auch abgesetzt montiert werden kann.
Zusammenfassung und Schlussfolgerung
Die Dicke und Breite des extrudierten Materials sowie die Extrudergeschwindigkeit sind die drei wichtigsten Kriterien für die Auswahl eines Hochspannungs-Pinhole-Detection-Systems. Eine Erhöhung einer dieser Variablen führt zu einer erhöhten Anforderung an das System.
Die Grenzen der Instrumentierung werden aus Gründen der Sicherheit und Kompatibilität festgelegt. Einzelne Instrumente sind im Allgemeinen nicht für dicke, breite und schnelle Extrusion geeignet. Mehrere Instrumente können das Problem lösen, sind aber kostspielig und verbrauchen Produktionsfläche.
Die Verwendung eines modularen Systems ermöglicht eine erhebliche Steigerung der Systemkapazität auf kostengünstige, integrierte und leicht zu implementierende Weise.
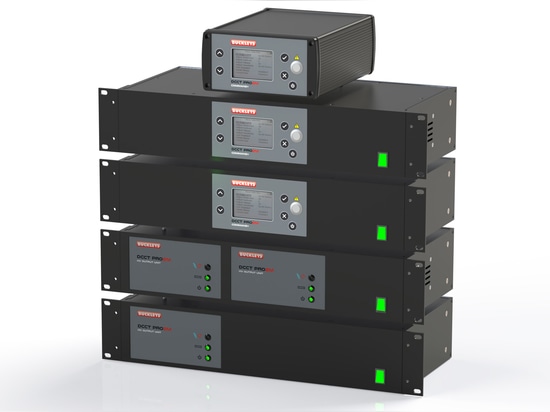
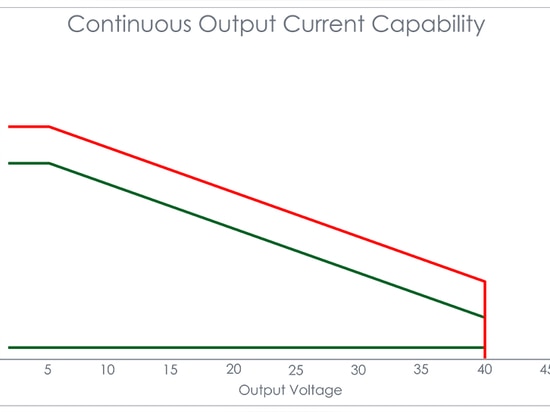
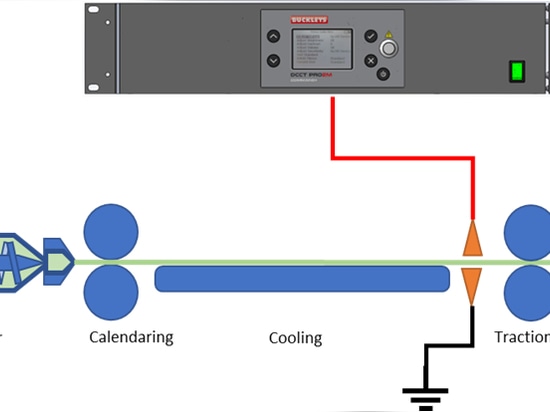