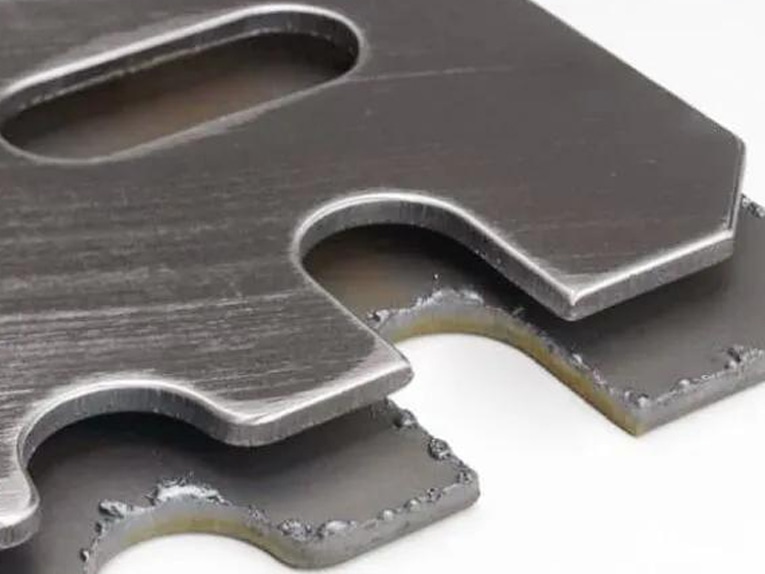
Automatische Übersetzung anzeigen
Dies ist eine automatisch generierte Übersetzung. Wenn Sie auf den englischen Originaltext zugreifen möchten, klicken Sie hier
#Neues aus der Industrie
Wie löst man das Problem der Kantengrate beim Faserlaserschneiden von Metall?
Wie löst man das Problem der Kantengrate beim Faserlaserschneiden von Metall?
Die Technologie des Faserlaserschneidens ist für ihre hohe Präzision und Effizienz bei der Metallbearbeitung bekannt, aber das Erzielen makelloser Schnittkanten ist zweifellos eine der größten Herausforderungen, wenn es darum geht, die überlegene Qualität und funktionale Integrität des Endprodukts zu gewährleisten. Kantengrate, ein häufiges Problem, mit dem viele Hersteller konfrontiert sind, beeinträchtigen nicht nur die Ästhetik eines Produkts, sondern auch seine Maßhaltigkeit und sogar seine Kernfunktionalität, die in direktem Zusammenhang mit der Kundenzufriedenheit und der Wettbewerbsfähigkeit auf dem Markt steht.
Wenn Sie also wissen wollen, wie Sie das Problem des Kantengrats beim Faserlaserschneiden von Metall vermeiden können, lesen Sie bitte diesen Artikel. In diesem Artikel finden Sie die Ursachen des Kantengrats und eine Reihe wissenschaftlicher und praktischer Lösungen.
Verständnis des Kantengrats beim Faserlaserschneiden
Zunächst einmal sollten wir verstehen, was Kantengrate sind. Kantengrate sind kleine, erhabene Metallpartikel, die sich während des Laserschneidens entlang der Schnittkante eines Werkstücks bilden. Sie variieren in Größe und Form von winzigen Fäden bis hin zu größeren rauen Vorsprüngen. Ihre Bildung ist zwar in gewissem Maße unvermeidlich, aber übermäßige Grate können auf ein Problem mit dem Schneidprozess, den Maschineneinstellungen oder den Materialeigenschaften hinweisen. An diesem Punkt kann der Benutzer dann überlegen, ob das Problem an der Maschine selbst liegt oder ob er sich beispielsweise während des Betriebs unangemessen verhält.
Ursachen für Kantengrate
Wenn man das Problem der Maschine selbst ausklammert, was sind dann die unsachgemäßen Handlungen, die zu Graten führen, wenn man die Faserlaserschneidmaschine im täglichen Betrieb einsetzt? Im Folgenden finden Sie eine Liste mit 5 Punkten:
Falsche Einstellung von Schneidgeschwindigkeit und Leistung: Eine falsche Laserleistung oder Schneidgeschwindigkeit kann zu einem unvollständigen Aufschmelzen des Materials und damit zu Graten führen.
Gasdruck und Durchflussmenge: Unzureichender oder zu hoher Druck und Durchfluss des Hilfsgases (in der Regel Stickstoff oder Sauerstoff) können die Qualität des Schnitts beeinträchtigen und zu Gratbildung führen.
Fokus-Einstellung: Eine falsche Fokussierung des Laserstrahls auf die Materialoberfläche kann zu ungleichmäßiger Erwärmung und Schmelzen führen, was wiederum Gratbildung zur Folge haben kann.
Materialeigenschaften: Art, Dicke und Oberflächenbeschaffenheit des Metalls können sich erheblich auf den Schneidprozess und die Gratbildung auswirken.
Maschinenkalibrierung und -wartung: Schlecht kalibrierte Maschinen oder verschlissene Teile wie Linsen und Düsen können die Schnittqualität beeinträchtigen.
Lösungen zur Reduzierung und Beseitigung von Kantengraten
Wenn die Ursachen für Kantengrate bekannt sind, was kann man tun, um sie zu vermeiden? In diesem Artikel werden die folgenden Lösungen vorgestellt:
1. Optimieren der Schneidparameter
Laserleistung und -geschwindigkeit anpassen: Kalibrieren Sie die Laserleistung und die Schneidgeschwindigkeit sorgfältig auf die Eigenschaften und die Dicke des Materials. Dickere Materialien erfordern möglicherweise eine höhere Leistung und langsamere Geschwindigkeiten, während dünnere Materialien eine niedrigere Leistung und schnellere Geschwindigkeiten erfordern können.
Feinabstimmung der Gaseinstellungen: Experimentieren Sie mit verschiedenen Gasdrücken und Durchflussraten, um die beste Einstellung für einen sauberen Schnitt zu finden. Sauerstoff kann die Schnittgeschwindigkeit erhöhen, kann aber bei manchen Materialien zu Gratbildung führen; Stickstoff wird in der Regel zur Gratreduzierung bevorzugt.
2. Verbessern der Fokuspositionierung
Sorgen Sie für eine präzise Fokussierung: Überprüfen und justieren Sie regelmäßig den Fokus des Laserstrahls, um sicherzustellen, dass er genau auf die Materialoberfläche ausgerichtet ist. Dies gewährleistet eine gleichmäßige Erwärmung und ein gleichmäßiges Aufschmelzen, was die Gratbildung erheblich reduziert.
3. Berücksichtigung von Materialfaktoren
Materialvorbereitung: Stellen Sie sicher, dass das Werkstück sauber, eben und frei von Verunreinigungen oder Oberflächenfehlern ist, die die Qualität des Schnitts beeinträchtigen könnten.
Auswahl des Materials: Berücksichtigen Sie die Eignung des Materials für das Laserschneiden und wählen Sie eine Materialqualität, die einen sauberen Schnitt mit minimaler Gratbildung ermöglicht.
4. Verbesserte Kalibrierung und Wartung der Maschine
Regelmäßige Kalibrierung: Führen Sie eine regelmäßige Maschinenkalibrierung durch, um sicherzustellen, dass alle Komponenten ordnungsgemäß funktionieren und genau ausgerichtet sind.
Vorbeugende Wartung: Implementieren Sie ein robustes Wartungsprogramm, das die Reinigung der Linsen, den Austausch verschlissener Düsen und die Überprüfung des Gesamtzustands der mechanischen und elektrischen Systeme der Maschine umfasst.
5. Einsatz fortschrittlicher Technologie
CNC-Programmierung: Eine fortschrittliche CNC-Programmiersoftware sorgt für eine präzise Steuerung der Schneidparameter und eine Optimierung der Bahn, wodurch die Wahrscheinlichkeit der Gratbildung verringert wird.
Automatisierte Qualitätskontrolle: Integration eines automatisierten Qualitätskontrollsystems zur Überprüfung der Schnittkanten auf Grate und andere Defekte, so dass sofort Korrekturmaßnahmen ergriffen werden können.