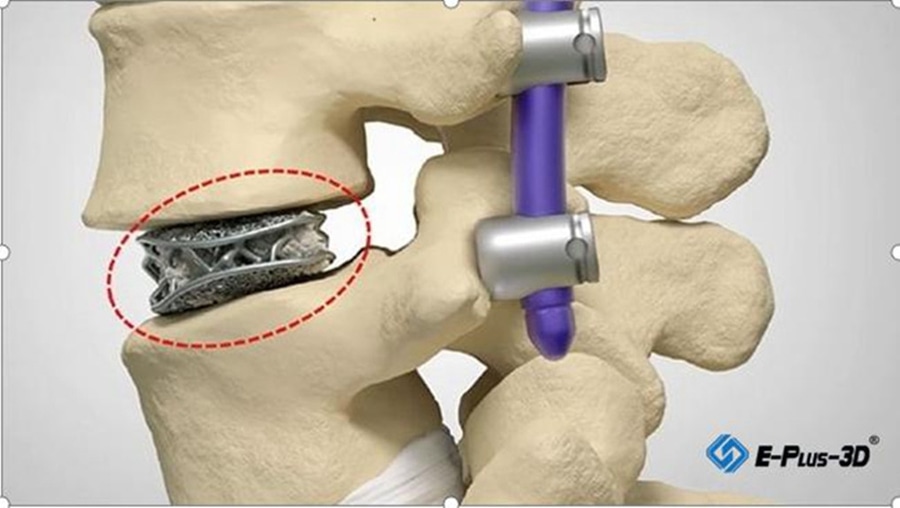
Automatische Übersetzung anzeigen
Dies ist eine automatisch generierte Übersetzung. Wenn Sie auf den englischen Originaltext zugreifen möchten, klicken Sie hier
#Neues aus der Industrie
Herstellung von Wirbelsäulenimplantaten mit dem EP-M250 Metall-3D-Drucker
Eplus3D Metall-3D-Drucker bieten Lösungen für Wirbelsäulenimplantate
Personalisierung der Verarbeitung durch additive Fertigung
Die Technologie der additiven Fertigung schreitet immer weiter voran und damit auch ihre Anwendung und Zugänglichkeit. Rapid Prototyping und Tooling stehen an der Spitze des 3D-Drucks, aber das Ziel war schon immer, direkt für die Produktion oder die Fertigung zu drucken. Die medizinische Welt ist da keine Ausnahme. Die ersten Anwendungen des 3D-Drucks in der Medizin waren Prototypen und Visualisierungshilfen, doch inzwischen hat diese Technologie mit Hilfe modernster 3D-Drucker das Stadium der individuellen Implantate erreicht.
Eplus3D bleibt seiner Vision treu, eine personalisierte 3D-Lösung für jedermann anzubieten. Mit seiner neuesten Produktlinie von 3D-Metalldruckern zieht Eplus3D die Aufmerksamkeit der medizinischen Partner auf sich, die diese Technologie in unglaublicher Weise nutzen. Einer der Pionierpartner bei der Herstellung und Verwendung medizinischer Implantate ist MANTIZ.
MANTIZ ist ein Medizintechnikunternehmen, das überlegene Technik und Technologie einsetzt, um ein aktives und schmerzfreies Leben für alle Patienten mit Wirbelsäulenerkrankungen zu ermöglichen. MANTIZ hat die KFDA-Zertifizierung (Zulassung von Medizinprodukten) erhalten und ist auf der HIRA-Liste (Health Insurance Review and Evaluation) in Südkorea aufgeführt. MANTIZ begann 2018 mit der Entwicklung von 3D-gedruckten Käfigimplantaten mit staatlicher Genehmigung und Finanzierung. Im Mai 2019 brachte das Unternehmen ein 3D-gedrucktes PANTHER-Cage-System für PLIF (Poster Lumbar Interbody Fusion) / TLIF / OLIF / ALIF-Operationen auf den Markt. Bei diesem Verfahren werden 3D-gedruckte Cage-Implantate verwendet, ohne dass der Herstellungsprozess an einen Dritten ausgelagert wird. Dies spart den Kunden Zeit und Geld und verringert das Risiko von Produktionsfehlern. MANTIZ verwendet den metallischen 3D-Drucker EP-M250 von Eplus3D zur Herstellung von 3D-gedruckten Cages aus Titan für den Einsatz in der Implantatchirurgie. Der gesamte Prozess der Formgebung des Implantats wird von MANTIZ intern durchgeführt. Der Cage wird nach den Vorgaben gestaltet. Größe, Material, Form und Porosität sind entscheidend für die Wirksamkeit des Implantats. Der komplette Entwurf des Cages wird in die Druckersoftware geladen und ist damit bereit für den Druck. Mit dem großen Druckbett des EP-M250 können mehr als 50 Einzelimplantate in einer Struktur gedruckt werden. Nach der Transplantation beginnen der Knochen und das umliegende Gewebe mit dem Implantat zu verwachsen, so dass eine stabile Struktur in der Wirbelsäule des Patienten entsteht. Hongwon Yoon (CTO von MANTIZ), der Erfinder des PANTHER 3D-Druck-Cage-Systems von MANTIZ, sagte: "Wir haben die Entwicklung eines verbesserten 3D-gedruckten Titan-Cage-Implantats mit dem 3D-Metalldrucker EP-M250 abgeschlossen. Die mechanischen Testergebnisse belegen die Sicherheit und Funktionalität des Implantats. 3D-Druck Der durchschnittliche geschlossene Porenanteil der festen Titankomponente beträgt 3 %, was die Bindung des Proteins für die Knochenfusion an die mesenchymalen Stammzellen fördert."
In den folgenden Bildern sehen Sie den gesamten Prozess vom Entwurf über den Druck bis hin zur Einbettung. Die Welt des 3D-Drucks entwickelt sich ständig weiter, und mit den Fortschritten der Technologie wächst auch die direkte Anwendung. Individuelle Gestaltung zum Greifen nah, erschwinglicher als je zuvor. Die Automobil-, Luft- und Raumfahrt- sowie die medizinische Industrie setzen den 3D-Druck jetzt direkt in der Produktion ein, was nur ein Teil der Möglichkeiten dieser Technologie ist. Wenden Sie sich direkt an Eplus3D (info@eplus3d.com), um weitere Informationen darüber zu erhalten, wie Sie die additive Fertigung in Ihren täglichen Arbeitsablauf integrieren können.
3D-Design und Druckprozess:
Integriertes Design mit professioneller 3D-Software
Vorbereiten der Teile in der 3D-Drucksoftware
Verwendung des EP-M250 von Eplus3D für den 3D-Druck
3D-Druckverfahren für Metall in der Kammer
3D-gedruckte Käfige
Nachbearbeitung, einschließlich Wärmebehandlung, Entfernen von Halterungen, Oberflächenbehandlung, Desinfektion usw.
Erst nach einer Reihe von mechanischen Tests kann der 3D-gedruckte Käfig in der Chirurgie eingesetzt werden
Durch den Prozess "Design-3D-Druck-Post-Processing-Tests" kann der PANTHER in der Chirurgie eingesetzt werden. Derzeit wird der PANTHER bereits bei der Behandlung von Patienten eingesetzt.
Vorteil des 3D-gedruckten Titankäfigs:
PANTHER wurde entwickelt, um das Knochenwachstum bei Wirbelsäuleneingriffen zu optimieren, mit einer durchschnittlichen Porengröße von 630-730μm in der Kontaktfläche der Wirbelsäulenendplatten und einer durchschnittlichen Porosität des Netzabschnitts von 70-80%.
Das Potenzial ist durchschnittlich
Über Eplus3D
Eplus3D wurde 2014 gegründet. Das technische Kernteam verfügt über mehr als 25 Jahre Erfahrung in der AM-Technologie und beschäftigt sich mit der Erforschung und Entwicklung von Additive-Manufacturing-Systemen und Anwendungstechnologien in Industriequalität. Mit MPBF™ (Metal Powder Bed Fusion), PPBF™ (Polymer Powder Bed Fusion) und Stereolithographie-3D-Drucktechnologie bietet Eplus3D professionelle Anwendungslösungen für die Bereiche Luft- und Raumfahrt, Automotive, Werkzeugbau, Gesundheit, Dental, Konsumgüter, Präzisionsfertigung usw.
Eplus3D verfügt über zwei Standorte in Peking und Hangzhou und investiert jährlich mehr als 20 % seines Umsatzes in die wissenschaftliche Forschung. Das Unternehmen verfügt über umfassende Erfindungspatente, Gebrauchsmusterpatente, Software-Urheberrechte und Patente für das Erscheinungsbild. Das Unternehmen hat große Erfolge in den Bereichen Design, Ausrüstung, Verfahren, Software, Materialien und Nachbearbeitung für die additive Fertigung erzielt. Die Ausrüstung wurde in mehr als 40 Länder und Regionen wie Europa, Amerika, Japan, Südkorea und Südostasien usw. exportiert.
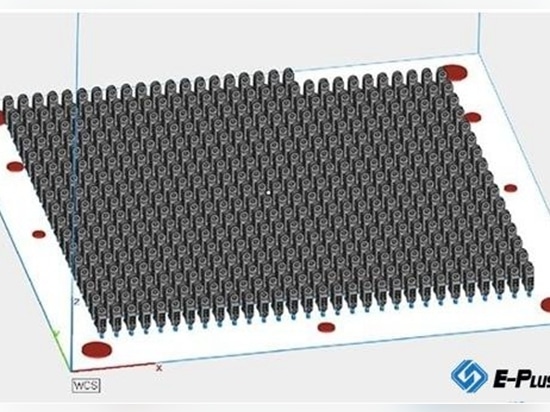
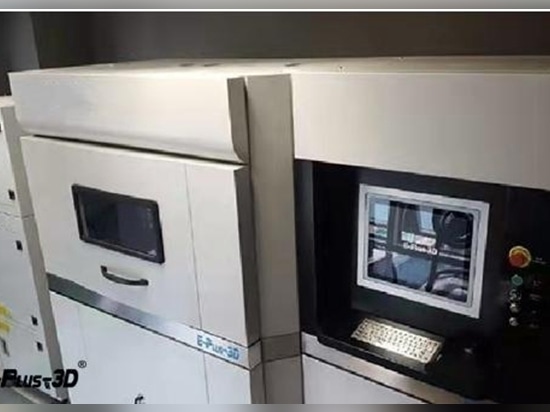
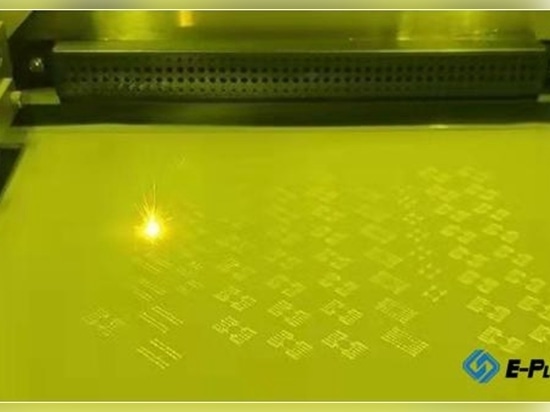
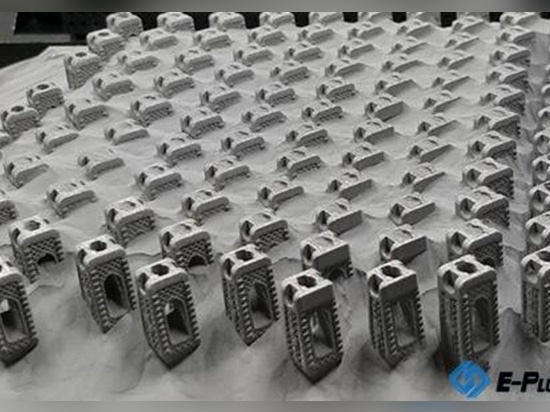
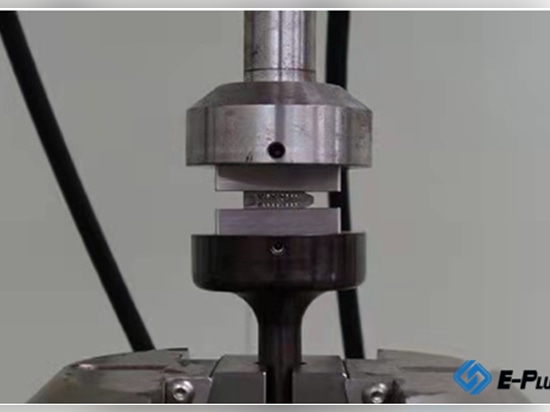
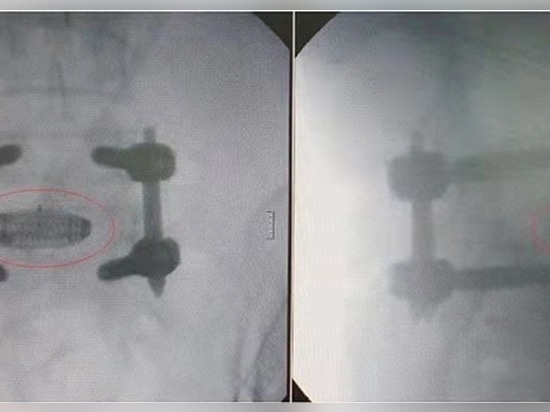
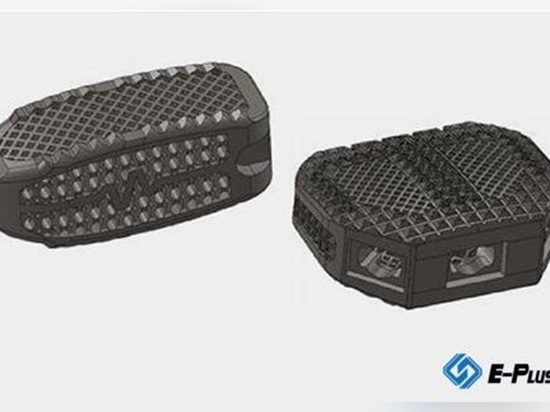