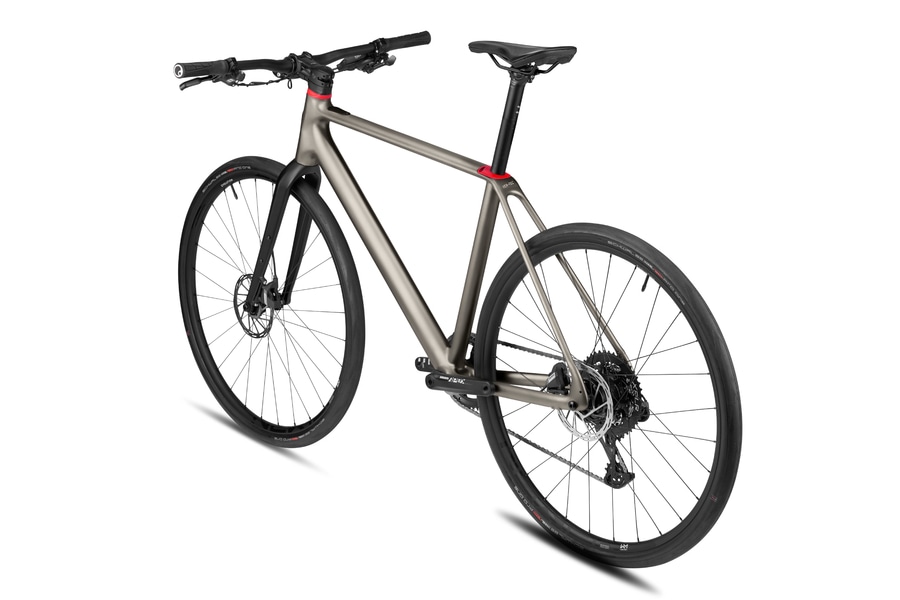
Automatische Übersetzung anzeigen
Dies ist eine automatisch generierte Übersetzung. Wenn Sie auf den englischen Originaltext zugreifen möchten, klicken Sie hier
#Neues aus der Industrie
Additive Fertigung von Metall - schnellere Innovation für die Fahrradindustrie
Unternehmensnachrichten
ABSTRACT
Bau des weltweit ersten Titan-Fahrradrahmens in Monocoque-Optik mit vollständiger Akku-Integration aus 3D-gedruckten Titan-Nasen.
Die Integration innovativer Technologien aus Asien nach Mitteleuropa, bei gleichzeitiger Wahrung der Kosteneffizienz, war eine große Herausforderung im Entwicklungsprozess.
Nach einer langen Geschichte entwickelte der Fahrradhersteller Möve das Prinzip der additiven Fertigung (AM), um die Verbindungen zwischen den Rohren eines Fahrradrahmens herzustellen. Nach der Evaluierung potenzieller Partner für diesen technologischen Durchbruch stellte Möve fest, dass eine hervorragende Zusammenarbeit und Expertise erforderlich ist, um Kosteneffizienz, Design und Leistung mit einem einzigen Hersteller in Einklang zu bringen.
Das Team von Eplus3D konzentrierte sich darauf, die Kostenstruktur für die Produktion von Steckverbindern zu optimieren und die Machbarkeit der Skalierung des Projekts in die Serienproduktion sicherzustellen. Durch die Umsetzung dieses Ansatzes und die Unterstützung von Möve bei den noch nie zuvor hergestellten Titanrohren für den Rahmen konnte das Projekt um mindestens vier Monate beschleunigt werden, was zur Schaffung eines neuen und unverwechselbaren E-Bike-Rahmens führte, bei dem das ursprünglich geplante Monocoque-Design erhalten blieb.
Dieses Projekt veranschaulicht das Potenzial für die Fahrradindustrie durch den Einsatz des Metall-3D-Drucks und eine wertvolle Kombination aus technischer Arbeit aller Beteiligten. Das Erkennen der Herausforderungen ist für die Mobilitätsbranche von entscheidender Bedeutung und veranlasst sie dazu, die Herstellung von Teilen zu überdenken und neu zu gestalten, um ein hochwertiges und langlebiges Produkt zu liefern, das das Endnutzererlebnis verbessert.
MÖVE EINFÜHRUNG
Möve, ein Unternehmen mit langjähriger Präsenz in Thüringen, verbindet seit 1897 fortschrittliche Technik mit herausragender Fertigungsqualität. Derzeit befindet sich der Produktionsstandort in Katharinenberg, Thüringen. Das Unternehmen legt großen Wert auf das Label "Made in Germany" und stellt sicher, dass seine Produkte von Anfang an bis zum fertigen Produkt nach den höchsten Standards hergestellt werden. Möve entwirft, konstruiert und entwickelt innovative Lösungen von und für Menschen, um das perfekte E-Bike herzustellen, das sich den Bedürfnissen der Menschen anpasst. Die Anerkennung des Vier-Augen-Prinzips sichert die herausragende Möve-Qualität gemäß den technischen Standards.
DIE HERAUSFORDERUNG
Möve erkannte die Zwänge der Branche, wie z. B. den hohen Anteil an Handarbeit bei der konventionellen Rahmenkonstruktion, die hohen Werkzeugkosten für hoch standardisierte Fahrräder und (E-)Bike-Rahmen, das falsch geschätzte jährliche Fahrradrahmenvolumen, das zu einem Umsatzrückgang führt, und die Verschwendung von Verbundfaserrahmen.
Das Ziel, so kostengünstig wie ein in Asien hergestellter Fahrradrahmen zu sein, mit einer innovativen Technologie, die Arbeitsplätze in Mitteleuropa zurückbringt, kombiniert mit dem Leistungsziel eines Carbonrahmens, waren sicherlich die größten Herausforderungen, die es zu bewältigen galt. Während der Entwicklungsphase stellte die Beschaffung von ovalen Titanrohren mit geringer Toleranz ein großes Problem dar, sowohl in finanzieller als auch in zeitlicher Hinsicht. Um die hydrogeformten Rohre zu erhalten, hätten die erforderlichen Werkzeuge entwickelt und hergestellt werden müssen, was das Projekt hätte beenden können, bevor es endgültig in Gang gekommen war.
DIE LÖSUNG
Nachdem die anfänglichen Herausforderungen identifiziert worden waren, wurde der erste Entwurf für additiv hergestellte Verbindungsstücke zwischen den Rohren erstellt. Um die Materialmenge auf ein Minimum zu reduzieren, fand Möve in Eplus3D den besten Partner, der die fortschrittlichsten Druckparameter, das Know-how und die Designunterstützung bot, was zu einem angemessenen Preis pro Teil führte. An diesem Punkt erkannte der Ingenieur Tobias Spröte das volle Potenzial und die transformativen Vorteile von Metal AM als nächsten Schritt zur Entwicklung des weltweit ersten 3D-gedruckten Fahrradrahmens aus Titan. Als Ergebnis und nach gemeinsamer technischer Arbeit aller Beteiligten kam Möve zu dem Schluss, dass die Metal Powder Bed Fusion (MPBF™) 3D-Drucktechnologie in Kombination mit der Verwendung von hochfestem Ti6Al4V-Material als einzige in der Lage war, die angegebenen Design-, Leistungs- und Kostenanforderungen für die Herstellung der Ösen für das Fahrrad zu erfüllen.
Eplus3D unterstützte Möve bei der Beschaffung hochwertiger Titanrohre, die ebenfalls vollständig additiv mit dem großformatigen Metalldrucker EP-M650 von Eplus3D aus dem Material Ti6Al4V hergestellt wurden. Diese Rohre werden in der Serienproduktion durch hydrogeformte Titanrohre ersetzt, haben aber die fristgerechte Realisierung des Projekts um 6 Monate beschleunigt. Darüber hinaus konnten die sehr teuren und unflexiblen Werkzeugkosten reduziert werden.
Unter den vielen Anbietern zeichnete sich Eplus3D durch sein Engagement aus, über die reine Produktion hinauszugehen und die Herausforderungen, die sich in der Nachproduktionsphase ergeben, durchdacht anzugehen. Das Ingenieurteam von Möve arbeitete gemeinsam mit Eplus3D an der Entwicklung innovativer Lösungen und erkannte die Notwendigkeit eines effizienten Ausbaus und Recyclings der Stützstruktur.
In Zusammenarbeit mit Möve wurden diese Probleme angegangen, um die Serienproduktion zu verbessern. Durch die Konzentration auf die Reduzierung der Stützstrukturen wurden die Schlüsselparameter optimiert, um die Druckgeschwindigkeit mit den gewünschten Produkteigenschaften in Einklang zu bringen. Dieser strategische Ansatz optimierte nicht nur den Postproduktionsprozess, sondern stand auch im Einklang mit den Qualitäts- und Effizienzzielen von Möve. Darüber hinaus hat Möve eine sehr durchdachte Prozesskette für die Herstellung des gesamten Fahrrads an seinem Standort geschaffen. Dazu gehören die Nachbearbeitung der additiv gefertigten Komponenten wie Oberflächenbehandlung und maschinelle Bearbeitung sowie die Montage des Fahrrads mit einer patentierten Klebetechnologie. Dies hilft dem Nutzer, sein Fahrrad zu recyceln und es im Vergleich zu anderen Fahrrädern aus Karbonfasern viel wirtschaftlicher zu reparieren.
So erklärt Enis Jost, stellvertretender Geschäftsführer von Eplus3D Deutschland: "Die Kostenstruktur wird vor allem durch die Betriebszeit der Anlage, die Reife der verwendeten Verarbeitungsparameter und die damit verbundene Druckgeschwindigkeit bestimmt. Da für die Herstellung der Nasen nur wenige Gramm Material verwendet werden und die Maschinen von Eplus3D eine höhere Anlagenproduktivität bieten, fallen die Rohstoffkosten in diesem Fall weniger ins Gewicht. Allerdings sinken die Kosten für AM-Titanpulver, was zu einem noch besseren Business Case beiträgt. Gleichzeitig werden die Prozesse von Eplus3D immer produktiver."
DIE ERGEBNISSE
Die Einführung der Metall-3D-Drucktechnologie in Kombination mit dem 3D-Engineering-Fachwissen hat zu bemerkenswerten Vorteilen geführt, darunter Kosteneinsparungen, höhere Produktqualität, verbesserte Effizienz und Nachhaltigkeit.
KOSTENREDUKTION
Dieses Projekt ist besonders vorteilhaft für eine wirtschaftlich tragfähige Serienproduktion, da es die Vorlaufkosten für standardisierte Fahrrad- und E-Bike-Rahmen in hohen Stückzahlen reduziert. Mit höheren Schichtdicken-Parametersätzen und mehreren Optionen für die Maschinenkonfiguration bietet Eplus3D eine optimierte Lösung, die die Kundenbedürfnisse perfekt erfüllt und somit die Kosten für die Teilefertigung und die Lagerhaltung senkt und sogar die individuelle Fertigung von Fahrrädern auf Anfrage ermöglicht.
FORTSCHRITTE BEI DEN MATERIALIEN
Durch die genaue Analyse und den richtigen Einsatz von Materialien wie der Titanlegierung (Ti6Al4V) war Möve in der Lage, hohe Leistungsstandards während der Produktion aufrechtzuerhalten und die Stabilität, Funktionalität und Haltbarkeit des Endergebnisses zu gewährleisten. Das Material hat das beste Leistungsverhältnis und ist daher die beste Wahl für diese Art von Anwendung.
ERHÖHTE DESIGNFLEXIBILITÄT
Der Einsatz der Metall-AM-Technologie in Verbindung mit dem technischen Fachwissen beider Parteien ermöglichte die Erstellung komplexer Geometrien und erleichterte das Monocoque-Design des E-Bike-Rahmens von Möve Avian. Dies wurde erreicht, ohne die Integration des Akkus zu beeinträchtigen, der diskret im Inneren des unteren Titanrohrs verborgen bleibt, wodurch sowohl das Design als auch die Funktionalität des E-Bikes verbessert werden. Das AM-Verfahren hat auch schnellere, iterative Entwürfe ermöglicht, die die gesamte Entwicklungszeit verkürzen und bei Bedarf die Herstellung eines fahrerspezifischen Fahrrads ermöglichen.
Diese Ergebnisse wurden durch das derzeit verfügbare und hochproduktive Ti6Al4V-Verfahren ermöglicht, das mindestens doppelt so schnell ist wie das unserer Mitbewerber auf dem Markt. Infolgedessen ist Eplus3D in der Lage, Kunden, die unsere Unterstützung bei der Verbesserung ihrer Prototyping-Fähigkeiten suchen, eine wesentlich attraktivere Kostenstruktur zu bieten, aber noch viel mehr, wenn sie mit dieser Technologie in die Serienproduktion einsteigen.
BEMERKENSWERTE MERKMALE DES MÖVE AVIAN, DER AUF METALL-3D-DRUCKTECHNOLOGIE BASIERT
HERGESTELLT IN DEUTSCHLAND
Jeder Schritt der Produktion, des Designs und der Konstruktion trägt das Gütesiegel "Made in Germany". Die Verlagerung der Lieferkette nach dem Prinzip des Nearshoring eröffnet der Fahrradindustrie neue Möglichkeiten, ihre Zulieferer besser zu kontrollieren. Zusammen mit dem hohen Automatisierungsgrad ermöglicht es den Herstellern, lokal, in hohen Stückzahlen und damit kostengünstig zu produzieren.
DIFFERENZIERTE TITAN-OBERFLÄCHE
Mit Hilfe der Strahltechnik wird die Titanoberfläche geglättet, was zu einem einheitlichen und matten Aussehen führt. Sie wird zum Markenzeichen des neuen Möve Avian.
GEWICHTSOPTIMIERUNG
Gewichtsreduzierung des Fahrrads durch den leichten Titanrahmen, indem die Stützstrukturen nach der Produktion reduziert werden. Dies wurde mit einem integrierten 250-Wh-Akku kombiniert, was zu einem Gewicht von 11,8 kg geführt hat.
ANWENDUNG DER FLEXFIT-TECHNOLOGIE
Die Klebstoffkammern für die Verklebung der Stollen und Rohre sowie deren Einspritzkanäle wurden von Möves' Team so konzipiert und optimiert, dass eine Füllung der Klebstoffkammern von über 98 % erreicht wurde.
ADDITIVE FERTIGUNG IST DIE ZUKUNFT DER FAHRRADINDUSTRIE
Der Einstieg von Möve in den Bereich der additiven Fertigung stellt nicht nur einen bedeutenden Wandel in der Art und Weise dar, wie Fahrradrahmen konstruiert werden, sondern zeigt auch der übrigen Industrie das Potenzial und die Qualitätsstandards, die mit dieser Technologie erreicht werden können. Möve setzt neue Maßstäbe in diesem Bereich, ebnet den Weg für zukünftige Innovationen und etabliert sich als Vorreiter in diesem Bereich.
Dieser Wandel wird durch die gemeinsamen Anstrengungen und das Know-how von Möve und Eplus3D deutlich sichtbar. Gemeinsam verschieben wir die Grenzen dessen, was im Fahrradrahmendesign und in der weiteren Fertigung möglich ist, und zeigen damit unser Engagement für die Neugestaltung der Branchenlandschaft. Wie Enis Jost, stellvertretender Geschäftsführer von Eplus3D Deutschland, erklärt: "Das Potenzial von AM in der Fahrradindustrie kann voll ausgeschöpft werden, wenn traditionelle Hersteller anfangen, für die Prozess- und Benutzeranpassung zu entwerfen, ähnlich wie bei anderen emotional verbundenen Geräten wie Autos und Motorrädern. Zu den möglichen Materialien gehören Hochleistungswerkstoffe wie Scalmalloy® oder Titan, aber auch typische Gusslegierungen wie AlSi10Mg oder sogar Edelstahl." Dieses Verfahren kann insbesondere für Fahrradkomponenten - Hebel, Klemmen, Schaltvorrichtungen und Pedale - von Vorteil sein, die derzeit typischerweise bis zu 10.000 Teile pro Jahr umfassen.
Um den potenziellen Markt von MPBF™ zu erschließen, "ist das Ingenieurteam von Eplus3D bereit, jedes Mobilitätsunternehmen dabei zu unterstützen, seine Leistungs- und Kostenziele mit Metal AM zu erreichen, indem es einen Fertigungsprozess entwickelt, der auch dem Near-Shoring-Prinzip folgt und den großen Bedarf an personalisierten Produkten oder Inhouse-Produktion unterstützt", erklärt Enis Jost. Darüber hinaus werden für jeden Kunden eine Standardkostenkalkulation und eine grundlegende Designprüfung durchgeführt. Aufgrund der völlig offenen Systemarchitektur kann der Kunde mit Sicherheit sein eigenes geistiges Eigentum (IP) auf der Grundlage des Prozesses entwickeln, der mit der zu installierenden Maschine geliefert wird, und so sein Fachwissen auf diesem Gebiet weiter ausbauen und den Prozess verbessern.
ÜBER EPLUS3D
Seit der Gründung der ersten PBF-Maschine in China im Jahr 1993 befasst sich Eplus3D mit der Forschung und Entwicklung von Additive-Manufacturing-Systemen und Anwendungstechnologien in Industriequalität unter Verwendung der MPBF™ (Metal Powder Bed Fusion) und PPBF™ (Polymer Powder Bed Fusion) 3D-Drucktechnologie. Eplus3D bietet professionelle Anwendungslösungen für die Bereiche Luft- und Raumfahrt, Energie, Öl und Gas, Automotive, Werkzeugbau, Gesundheitswesen, Konsumgüter und Präzisionsfertigung.
Eplus3D verfügt über vier Standorte in Peking, Hangzhou, Stuttgart und Houston. Das Unternehmen investiert jährlich mehr als 20 % seines Umsatzes in die wissenschaftliche Forschung und verfügt über umfangreiche Erfindungs-, Gebrauchsmuster-, Software- und Erscheinungspatente. Das Unternehmen hat große Erfolge bei der Entwicklung von Design, Verfahren, Software, Materialien und Nachbearbeitung für die additive Fertigung erzielt und AM-Lösungen erfolgreich bei Kunden in mehr als 40 Ländern und Regionen wie Europa, Nord- und Südamerika, dem Nahen Osten, Ostasien und Südostasien eingeführt.
APAC-Hauptsitz
Eplus3D Tech Co., Ltd.
Hangzhou, China
P: +86-571-83819589
Nr. 118 Yanshankong Road, Wenyan, Xiaoshan, Hangzhou, Zhejiang, China, 311258
EMEA-Region
Eplus3D Tech GmbH
Ludwigsburg, Deutschland
P: +49-7141-3888118
Pflugfelder Str. 23, 71636 Ludwigsburg, Deutschland
Region Nord- und Südamerika
EPLUS 3D TECH INC
Houston, USA
P: +1 (281) 302-6160
12425 W Airport Blvd, Einheit 201, Sugar Land, TX, 77478