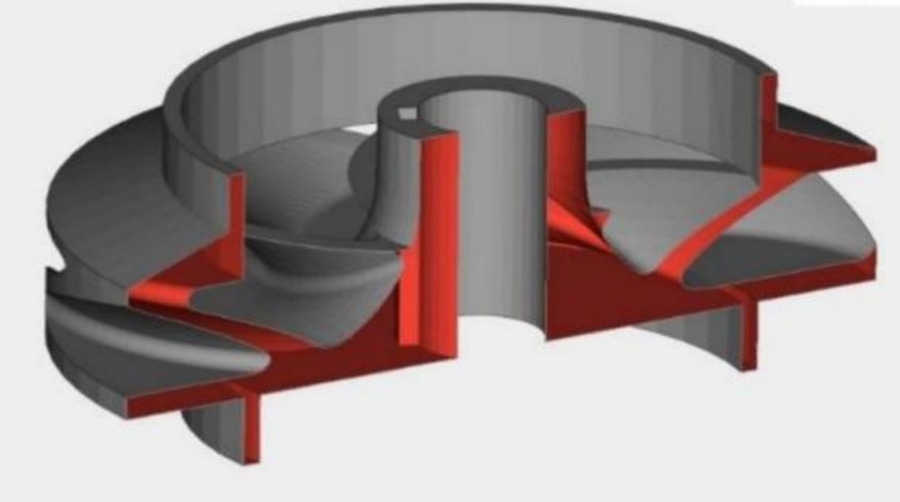
Automatische Übersetzung anzeigen
Dies ist eine automatisch generierte Übersetzung. Wenn Sie auf den englischen Originaltext zugreifen möchten, klicken Sie hier
#White Papers
Untersuchung der Herstellung eines geschlossenen Laufrads aus 316L-Edelstahl mit einer Eplus3D-Laser-Pulverbettfusionsmaschine
Unternehmensnachrichten
Yousef Alhorr1, Qusai Alkhalaf 2*
1PhD, Vorsitzender der Gulf Organization for Research and Development (GORD), QSTP, Doha, Katar
2PhD, Leiter des Zentrums für Additive Fertigung. Gulf Organization for Research and Development (GORD-3D), QSTP, Doha, Katar
Zusammenfassung: Die Herstellung von geschlossenen Laufrädern mittels Laser Powder Bed Fusion-Technologie ist mit einer gewissen Komplexität verbunden und erfordert eine sorgfältige Planung der Stützstruktur, der Bestimmung des Bauwinkels und der Energiedichte der Abwärtshäute, um eine erfolgreiche Produktion zu gewährleisten. In dieser Studie wird die Verwendung von Edelstahl 316L bei der Herstellung von geschlossenen Laufrädern mittels LPBF untersucht. Ziel ist es, den Einfluss von Prozessparametern und Bauwinkeln auf die Qualität der Laufradfertigung zu untersuchen. Außerdem wird die Auswirkung der Energiedichte auf die Oberflächenrauhigkeit und die Härte des Laufrads untersucht. In der Untersuchung werden Bauwinkel von 0˚, 30˚ und 90˚ für ein geschlossenes Laufrad geprüft, wobei sich herausstellt, dass ein Bauwinkel von 30˚ zu erfolgreichen gedruckten Teilen führt. Um fehlerfreie geschlossene Laufräder zu erhalten, muss die Energiedichte auf der Unterseite zwischen 80 % und 100 % der Energiedichte auf der Oberseite liegen. Die maximale Härte und die minimale Oberflächenrauhigkeit wurden bei 233 HV bzw. 12,79 µm gemessen, wenn die Energiedichte 41,66 J/mm³ bzw. 55,55 J/mm³ betrug. Die Neuheit dieser Studie liegt in der Herstellung von geschlossenen Laufrädern aus Edelstahl 316L durch Laser-Pulverbettschmelzen.
Stichwörter: additive Fertigung; Laser-Pulverbett-Fusion (LPBF); geschlossenes Laufrad; selektives Laserschmelzen (SLM)
1. Einleitung
Das Laufrad ist ein unverzichtbares Element in Pumpensystemen und spielt eine zentrale Rolle bei der Bestimmung der hydraulischen Kapazität und der Effizienz der Durchflussrate in Turbomaschinen [1]. Man unterscheidet vier geometrische Klassen, nämlich offene, geschlossene, halboffene und Schraubenlaufräder. Das geschlossene Laufrad (CI) stellt aufgrund seiner komplizierten inneren Merkmale eine besondere Herausforderung bei der Herstellung dar. Herkömmliche Methoden bestehen darin, die CI in Segmente wie Mantel, Nabe und Schaufeln zu zerlegen und mit Hilfe von Schweiß-, Löt- oder Niettechniken zusammenzufügen. Diese Verfahren führen jedoch zu Defekten und Verformungen und erweisen sich als ungeeignet für anspruchsvolle, leistungsstarke Anwendungen. Infolgedessen wird die Einführung von einteiligen KI zwingend erforderlich, wobei Fertigungstechniken wie Feinguss, Integralfräsen und Elektronenentladungsbearbeitung (EDM) zwar spezialisiert, aber zeitaufwändig sind und qualifizierte Arbeitskräfte sowie spezielle Vorrichtungen erfordern, was die Gesamtfertigungskosten erhöht [2].
Die Additive Fertigung (AM) stellt eine neue Lösung für die Herstellung von Einzelteilen dar und bietet die Möglichkeit, Unsicherheiten bei der Vorlaufzeit zu verringern und die Designflexibilität zu erhöhen [3,4]. Laser Powder Bed Fusion (LPBF), eine bekannte AM-Technologie, schmilzt Pulver selektiv Schicht für Schicht mit Hilfe eines Lasers auf und ermöglicht so die Herstellung komplex geformter Teile mit einer hohen Auflösung von etwa 50 Mikrometern [6-9]. LPBF hat sich beim Drucken komplexer Teile aus einer Reihe von metallischen Werkstoffen wie Stählen, Nickellegierungen, Titanlegierungen und Inconel-Legierungen als sehr erfolgreich erwiesen [10-11].
Alternative Technologien wie das FDM-Verfahren (Fused Deposition Method) können zwar für den Druck von Laufrädern eingesetzt werden, ihre Eignung ist jedoch im Allgemeinen auf weniger komplexe Anwendungen beschränkt [12]. Im Gegensatz dazu ist LPBF mit Metalldruck unverzichtbar, um Hochleistungsfunktionalitäten zu erreichen [13]. Zahlreiche Studien unterstreichen den erfolgreichen Einsatz von LPBF beim Drucken von offenen Laufrädern. Sie umfassen Untersuchungen zu Materialeigenschaften, Vorhersagen zum thermischen Verlauf und die Optimierung der Prozessparameter [14-16]. Besonders hervorzuheben ist, dass LPBF die Herstellung von Laufrädern aus recycelten Materialien ermöglicht, was das Potenzial für nachhaltige Fertigungsverfahren unterstreicht [17]. Trotz dieser Fortschritte besteht die Herausforderung weiterhin darin, präzise und fehlerfreie 3D-Drucke zu erzielen. Geometrische Verformungen, wie z. B. dunkle Flecken und suboptimale metallurgische Verbindungen zwischen den Schichten, tragen zu vielfältigen Problemen bei, darunter geometrisches Versagen, Maßungenauigkeiten, unvollständige Strukturen und Behinderungen im Druckprozess [27]. Darüber hinaus führen Debris-Defekte, die durch den Rückstoßdruck des Metalldampfs während des Drucks entstehen, dazu, dass ungeschmolzenes Pulver oder geschmolzenes Metall abbricht und den Schmelzstatus in den nachfolgenden Schichten beeinflusst, was letztendlich die Zugfestigkeit und Ermüdungsleistung des gedruckten Teils beeinträchtigt [28-29].
Edelstahl gilt weithin als eine hervorragende Option für das Laser-Pulverbett-Schmelzdruckverfahren. Ein geschlossenes Laufrad aus Edelstahl hat zahlreiche Anwendungsmöglichkeiten, z. B. in Abwassersystemen. Beim Drucken von Edelstahl geht es vor allem darum, die Energiedichte zu steuern und den Winkel des Trägermaterials zu optimieren. Die Energiedichte gibt den Energieeinsatz pro Volumeneinheit während des Schichtschmelzprozesses an. Konkret ist die Energiedichte definiert als:
In der Gleichung steht P (W) für die Laserleistung, v für die Scangeschwindigkeit (mm/s), h (μm) für den Schraffurabstand und z (μm) für die Schichtdicke. Niedrige Energiewerte führen zu einer fehlenden Schmelzporosität, was bedeutet, dass die Energie für ein vollständiges Aufschmelzen des Pulvers nicht ausreicht, was zu weit verbreiteten unregelmäßigen Porositäten im gesamten Teil führt [31]. Hohe Energiedichtewerte führen zu einem Überschmelzen, das oft als Schlüssellochporosität bezeichnet wird [32-34]. In diesem Zustand fragmentieren die geschmolzenen Bahnen, was zu einer ungleichmäßigen Erstarrung und zu Defekten am fertigen Teil führt. Der stationäre Bereich gewährleistet das vollständige Aufschmelzen der Leiterbahnen und den Schichtverbund innerhalb der Energiedichtegrenzen. Die Komplexität des Impellerdrucks ist der Schlüssel zum Laser-Pulverbettschweißen, wobei die gängigen Metalle Inconel 625 und Inconel 718 sind.
Soweit den Autoren bekannt ist, gibt es keine Untersuchungen über die Anwendung von Edelstahl 316L beim Laser-Pulverbett-Schmelzdruck von geschlossenen Laufrädern. Daher soll diese Forschungsarbeit diese Lücke füllen, indem sie die Herstellung eines geschlossenen Laufrads durch Laser-Pulverbettschmelzen übernimmt. Unser Hauptziel ist es, die Auswirkungen von Variablen wie dem Trägermaterial, dem Konstruktionswinkel und der Energiedichte auf der Unterseite auf den Herstellungsprozess des geschlossenen Laufrads zu analysieren. Außerdem wollen wir die Auswirkungen der Energiedichte auf die Oberflächenrauheit und -härte untersuchen.
2. Methode und Experimentarbeit
Die hier angewandte Methode und die experimentellen Arbeiten zur Untersuchung des Winkels der Tragstruktur und der endgültigen mechanischen Eigenschaften des Laufrads sind in Abbildung 1 dargestellt. Die Methode ist in drei Phasen unterteilt. In der ersten Phase wird der geeignete Winkel der Stützstruktur zwischen 0°, 30° und 90° ausgewählt. Nach der Bestimmung des optimalen Winkels wird in Phase 2 die Mikrostruktur mittels REM-Scanning untersucht. In Phase III wird die Auswirkung der Energiedichte auf Rauheit und Härte untersucht.
2.1 Entwurf des Laufrads
Es wurden zwei verschiedene Größen von geschlossenen Laufrädern entworfen: eines mit einem Durchmesser von 145 mm und das andere mit einem Durchmesser von 100 mm. Das Laufrad ist entlang seiner Konstruktionsrichtung in drei Hauptabschnitte unterteilt: den Grundkörper, den Mittelteil und den Leitwerksteil. Diese Abschnitte weisen komplexe Strukturen auf, darunter mehrere schräge, dünne Rippengeometrien, was die Herstellung zu einem schwierigen Prozess macht. Da sich der Querschnitt über die Höhe des Laufrads ändert, variiert der vom Laser abgetastete Bereich von Schicht zu Schicht. Die Struktur des Laufrads ist in Abbildung 2 dargestellt.
2.2 Gebäudewinkel und Tragstruktur für geschlossene Laufräder
Zur Bestimmung des optimalen Bauwinkels für ein geschlossenes Laufrad in der Baukammer der LPBF-Maschine wurden drei gängige Winkel (90˚, 30˚ und 0˚) ausgewählt, um ihre Auswirkungen auf den Fertigungsprozess zu bewerten. Die Auswahl der Stützen hängt von der Form des Laufrads ab, wobei blockförmige Stützen gewählt wurden, wie in Abbildung 3 dargestellt. Zahlreiche Studien haben gezeigt, dass die Verwendung von massiven oder blockförmigen Halterungen zu besseren mechanischen Eigenschaften der Proben und einer besseren Oberflächenbearbeitung führt, insbesondere bei überhängenden Oberflächen. Diese Halterungen ermöglichen eine wirksame Wärmeableitung und optimieren so die Ergebnisse. Abbildung 4 veranschaulicht die Ansicht einer Blockstütze mit zusätzlichen Baumstützen, um die Entfernung zu erleichtern. Zur Vorbereitung der Konstruktion wurde die Software MaterialsMagic für die Vorbereitung der Halterungen und SolidWorks für die Konstruktion verwendet.
2.3 LPBF-Verarbeitung
Die Laufräder wurden mit einer Eplus3D EP-M260 LPBF-Maschine aus Edelstahl 316L hergestellt. Die Eplus3D M260 befindet sich im 3D-Zentrum der Gulf Organisation for Research & Development (GORD 3D). Die aktuelle Ansicht der Eplus3D-Maschine ist in Abbildung 5 dargestellt. Die Laufräder wurden mit Durchmessern von 145 mm und 100 mm entworfen. Das Drucken eines Laufrads mit einem Durchmesser von 145 mm bei einem Bauwinkel von 90˚ dauert etwa 103 Stunden und erfordert 4 393 Schichten mit einer Dicke von 30 µm. Für ein Laufrad mit einem Durchmesser von 145 mm und einem Gebäudewinkel von 30˚ werden 53 Stunden benötigt, wobei 3.124 Schichten erforderlich sind. Für ein Laufrad mit einem Durchmesser von 100 mm und einem Bauwinkel von 0˚ werden etwa 38 Stunden und 1 833 Schichten benötigt.
Die Wahl der Parameter für den Druck geschlossener Laufräder ist von entscheidender Bedeutung, wobei die Energiedichte eine besonders wichtige Rolle spielt. Die Unterseite befindet sich in den ersten drei Schichten über dem Trägermaterial, das das Teil während des Druckvorgangs beschädigen kann. Daher ist die perfekte Wahl der Energiedichte der Unterseite von entscheidender Bedeutung, da sie als Brücke zwischen dem Trägermaterial und dem Kern des Laufrads dient. Die Energiedichte der Innenhaut hingegen bezieht sich auf den Kern des Laufrads. Nach der Literaturrecherche sollte die Energiedichte der Außenhaut im Idealfall zwischen 50 und 80 % der Energiedichte der Innenhaut liegen. In der vorliegenden Studie werden zwei Fälle für die Unterhaut-Energiedichte betrachtet: einer, bei dem die Energiedichte der Unterhaut gleich der Energiedichte der Innenhaut ist, und ein anderer, bei dem die Energiedichte der Unterhaut auf 20 % der Energiedichte der Innenhaut festgelegt wird. Die aktuelle Ansicht des Druckprozesses ist in Abbildung 6 dargestellt. Tabelle 2 enthält Einzelheiten zu den Prozessparametern mit diesen Energiedichtevariationen für jede Phase.
2.4 Härteprüfung
Vickers-Mikrohärteprüfungen wurden nach der ASTM-Norm E92-17 mit einer Vickers-Mikrohärteprüfmaschine durchgeführt. Mit einem pyramidenförmigen Diamanteindringkörper wurde eine bestimmte Kraft (300 gf, 2,94 N) 10 Sekunden lang pro Eindruck auf die Probenoberfläche ausgeübt. Jede Probe wurde dreimal eingedrückt, wobei Eindrücke innerhalb von Poren ausgeschlossen wurden. Der Vickers-Härtewert (HV) wurde durch Messung der Diagonalen jedes diamantförmigen Eindrucks ermittelt und mit Hilfe der Software des Geräts gemittelt. Der Durchschnitt dieser Messungen galt als Härte der Probe.
2.5 Oberflächenvorbereitung und mikrostrukturelle Charakterisierung
Eine 5 mm dicke Probe wurde mit dem Impeller hergestellt. Die Proben wurden mit Siliziumkarbid-Schleifscheiben verschiedener Körnungen (200, 600, 800 und 1200) geschliffen. Die bearbeiteten Proben wurden anschließend unter dem Lichtmikroskop untersucht, um mikrostrukturelle Merkmale wie ungeschmolzenes Pulver und Risse zu ermitteln. Anschließend wurden sie mit einem Phenom ProX Desktop SEM analysiert, um die Substruktur und Morphologie zu untersuchen.
3. Ergebnis und Diskussion
3.1 Einfluss des Gebäudewinkels auf den Laufradbau
Stützstrukturen spielen eine wichtige Rolle bei der Ableitung von Wärme aus dem Schmelzbad, bei der Verringerung der thermischen Spannungen und beim Ausgleich der Kraft der Wiederbeschichtungsschaufel, die einen dynamischen Druck auf die Vorderkante der Schicht ausübt. Die Wärmeleitung variiert in Abhängigkeit von der relativen Dichte; sie ist in Pulverschichten mit geringerer Packungsdichte deutlich geringer als in Strukturen mit festem Träger. Verschiedene Trägerstrukturen leiten die Wärme in unterschiedlichem Maße ab; eine höhere Wärmeableitung, wie bei Blockträgern, erschwert jedoch die Entfernung. Massiv-/Blockträger ermöglichen bessere mechanische Eigenschaften und eine bessere Oberflächenbearbeitung auf überhängenden Flächen, allerdings bei höheren Kosten für Material, Druckzeit und Nachbearbeitung. Neben der Wärmeableitung stützen die Stützstrukturen die Teile und wirken den Zugkräften während der schnellen Abkühlung entgegen, wodurch das Risiko des Verziehens und der Delaminierung verringert wird. Eine unzureichende Unterstützung für nach unten gerichtete Oberflächen führt zu Problemen mit der Form- und Maßgenauigkeit. Daher ist die Auswahl der Parameter für die Stütz- und Abwärtsschichten von entscheidender Bedeutung, um innere Spannungen und Delaminationen zu vermindern. Es ist von entscheidender Bedeutung, einen "zuverlässigen Bauwinkel" zu ermitteln, d. h. den Mindestwinkel, der die Herstellung von Teilen ohne Krätzebildung und Ablösungen gewährleistet.
Wie im Abschnitt über die Methoden beschrieben, wurde das Laufrad während der Konstruktion bei drei Bauwinkeln untersucht: 90°, 30° und 0°. Im Fall von CI-A kam es zu einem erheblichen Versagen des Laufrads, das auf die vor dem Prozess gewählten schwachen Stützstrukturen zurückzuführen ist (siehe Abbildung 7). Die Kombination aus Blockstütze und Baumstütze erwies sich als unzureichend, um das Gewicht des Laufrads zu tragen, was zu einer Verformung der Stützstruktur führte, die besonders bei einem Gebäudewinkel von 90˚ auffiel. Die beobachtete Verformung ist auf das hohe Gewicht des Bauteils und des Recoaters während des Druckvorgangs zurückzuführen. Insbesondere der Recoater spielt eine entscheidende Rolle beim Schichtaufbau, indem er das Pulver auf dem Baubett verteilt. Diese sich wiederholende Aktion, vor allem während des Auftragens der nachfolgenden Schichten, kann jedoch eine übermäßige Kraft ausüben, die zu Schäden führt, insbesondere bei 90°-Winkeln, wo die Kanten des gedruckten Teils von Natur aus schwächer sind.
Im Fall von CI-B und CI-C wurde eine erfolgreiche Laufradkonstruktion mit weniger Defekten beobachtet. Die Herstellung eines kleineren und größeren Laufrads mit einem Bauwinkel von 30˚ führt zu einer deutlichen Verringerung der Defekte und Schäden während des Herstellungsprozesses und zeigt bessere Ergebnisse als die Fälle, in denen der Bauwinkel auf 90˚ eingestellt ist. Dieses Phänomen ist in Abbildung 8 deutlich zu erkennen. Bei einem Gebäudewinkel von 30˚ traten keine Schäden auf, wodurch das Gewicht des gedruckten Teils reduziert und die Leistung des Recoaters verbessert wurde. Bei einem 30°-Winkel kommt der Recoater bei jeder Streubewegung mit weniger Pulver entlang der Kanten in Berührung als bei einem Winkel von 90° und 0°. Der Erfolg der 30-Grad-Ausrichtung wird auf mehrere Schlüsselfaktoren zurückgeführt. Erstens minimiert der allmähliche Übergang im Querschnitt von Trägern zu festen Teilen innerhalb jeder Schicht Spannungskonzentrationen und potenzielle Defekte, was sie von Ausrichtungen wie 0 Grad unterscheidet, bei denen abrupte Änderungen auftreten. Zweitens trug das Fehlen massiver Stützen, die normalerweise für Überhänge in Ausrichtungen wie 90 Grad erforderlich sind, wesentlich zum Erfolg der 30-Grad-Ausrichtung bei. Durch den Wegfall der Stützen wurde nicht nur der Druckprozess gestrafft, sondern auch die mit der Nachbearbeitung und Oberflächenfehlern verbundenen Probleme verringert, was letztlich die Qualität und strukturelle Integrität der Teile verbesserte. Darüber hinaus wurde festgestellt, dass die in einer 30-Grad-Ausrichtung gedruckten Teile im Vergleich zu den in einem 90-Grad-Winkel gedruckten ein geringeres Gewicht aufwiesen. Diese Gewichtsreduzierung, die bei verschiedenen Anwendungen von Vorteil ist, unterstreicht die Wirksamkeit der 30-Grad-Ausrichtung. Insgesamt unterstreichen diese Ergebnisse die vielfältigen Vorteile der 30-Grad-Ausrichtung in der additiven Fertigung und bieten wertvolle Erkenntnisse für die Optimierung von Ausrichtungsstrategien in zukünftigen Anwendungen.
Im Falle des CI-D, bei dem das geschlossene Laufrad klein ist, trat ein Versagen auf, wenn der Bauwinkel 0˚ betrug. Trotz der geringen Größe des CI war das Versagen bei diesem Winkel nicht auf seine Größe zurückzuführen, sondern eher auf die Schwäche der Stützstruktur, wie in Abbildung 9 dargestellt. Außerdem führte die hohe Scangeschwindigkeit von 900 mm/s zu einer Ansammlung von Ablagerungen auf der Laufradoberfläche, wie in Abbildung 9 dargestellt. Außerdem wurden Schäden entlang des Randes beobachtet, die durch die hohen Leistungseinstellungen in diesen Bereichen verursacht wurden.
3.2 Einfluss der Down-Skin-Parameter auf die Konstruktion des geschlossenen Laufrads
Als Deckschichten werden in der Regel 1 bis 4 Schichten bezeichnet, die sich über Stützen oder direkt auf dem Pulver befinden. In der Regel werden drei Schichten als "Down-Skin" bezeichnet und erfordern im Vergleich zu den "In-Skin"- oder "Core"-Schichten andere Verarbeitungsparameter. Parameter, die sich auf die untere Schicht beziehen, wie z. B. die Scangeschwindigkeit und die Leistung, gelten als kritisch für die Herstellung von Teilen mit der Laser-Pulverbett-Schmelztechnologie. Wenn die Energiedichte auf der Unterseite nur 20 % der Energiedichte auf der Oberseite beträgt, kommt es zu spürbaren Schäden am Bauteil. Selbst in Fällen, in denen keine Schäden zu beobachten sind, zeigen sich Anzeichen von Verbrennungen und Defekten auf der Oberfläche des geschlossenen Laufrads, besonders deutlich bei größeren geschlossenen Laufrädern wie CI-A, wie in Abbildung 7 dargestellt. Dies unterstreicht die Bedeutung von zwei Hauptfaktoren, die zum Versagen des Teils beitragen: die Unzulänglichkeit der Stützstruktur und die unzureichende Energiedichte der Außenhaut, die bei 12,15 J/mm³ liegt.
Mit abnehmendem Laufraddurchmesser, wie im Fall eines Laufrads mit 100 mm Durchmesser, nimmt die Wirkung der Unterschale ab, was besonders bei einem Gebäudewinkel von 30˚ deutlich wird. Obwohl die Energiedichte der Unterseite nur 20 % der Energiedichte der Oberseite ausmacht, kann es in bestimmten Bereichen des gedruckten Teils immer noch zu geringfügigen Verbrennungen kommen, wie in Abbildung 10 zu sehen ist. Darüber hinaus erhöht eine Vergrößerung des Durchmessers des Laufrads die Wahrscheinlichkeit einer Beschädigung des Teils. Die Ausrichtung der Energiedichte auf der Unterseite mit der Energiedichte auf der Innenseite in einem Winkel von 30˚ gewährleistet jedoch einen erfolgreichen Impellerdruck ohne Defekte, wie in Abbildung 10 zu sehen ist.
Die Energiedichte auf der Unterseite ist ein entscheidender Parameter im Prozess der Teileherstellung, der von der Komplexität und Größe des Teils abhängt. Bei kleineren Teilen ist ihr Einfluss weniger ausgeprägt als bei größeren Teilen. Um fehlerfreie Teile zu erhalten, sollte die Energiedichte unter der Haut im Idealfall zwischen 80 und 100 % der Energiedichte unter der Haut liegen.
3.3 Einfluss der volumetrischen Energiedichte (VED) auf die Mikrostruktur des Laufrads
Das gedruckte Laufrad mit einer Energiedichte von 35 J/mm³, die als niedrig angesehen wird, weist einen Mangel an Verschmelzung auf, der auf die hohe Scangeschwindigkeit zurückzuführen ist, was dazu führt, dass der Laser nicht genügend Zeit hat, um das Pulver aufzuschmelzen, wie in Abbildung 11 dargestellt. Durch die Erhöhung der Energiedichte auf 55,55 J/mm³ werden diese Probleme der mangelnden Verschmelzung und des fehlenden Klebstoffs aufgrund der optimalen Energiedichte verringert, so dass das Pulver ordnungsgemäß aufgeschmolzen werden kann, wie in Abbildung 12 dargestellt.
3.4 Einfluss der VED auf die Härte
Die Messungen der Vickershärte der gedruckten Proben lagen in einem Bereich von 226 bis 233 HV. Zwei Proben, die durch eine volumetrische Energiedichte (VED) von 40 J/mm³ gekennzeichnet waren, wiesen Härtewerte unter 230 HV auf. Dabei handelt es sich um die Proben CI-C-1 und CI-C-2 mit Energiedichten von 33,33 J/mm³ bzw. 37,037 J/mm³. Die Mehrzahl der Proben lag im Bereich von 220 bis 230 HV, wie aus Tabelle 3 hervorgeht. Vor allem die Probe CI-C-3 mit einer VED von 41,66 J/mm³ wies die höchste Härte von 233 HV auf.
Die erzielten Vickershärte-Werte (HV) waren vergleichbar mit denen von durch Gießen hergestellten 316L-Teilen, die normalerweise eine Härte von 210 HV aufweisen. Die übrigen Werte waren jedoch höher als dieser Richtwert. Es wurde festgestellt, dass die Härte einer Probe umso geringer ist, je poröser sie ist, da das Vorhandensein von Poren ein tieferes Eindringen von Eindrücken ermöglicht, was zu größeren Eindrücken und folglich zu niedrigeren HV-Werten führt. In diesem Versuch wurde absichtlich versucht, Oberflächenporen bei jedem Eindruck zu vermeiden, was zu einer minimalen Korrelation zwischen Härte und Oberflächenporosität führte.
3.5 Oberflächenrauhigkeit
Die Oberflächenrauheit ist ein wichtiger Parameter beim Laser-Pulverbettschweißen, der von der Energiedichte beeinflusst wird. Eine Erhöhung der Energiedichte führt in der Regel zu einer Verringerung der durchschnittlichen Rauheit des Werkstücks. Diese Verringerung ist darauf zurückzuführen, dass eine höhere Energiedichte eine längere Einwirkung von hoher Energie und niedriger Geschwindigkeit ermöglicht, was ein besseres Aufschmelzen des Pulvers während des Prozesses begünstigt. Darüber hinaus wird durch die Verringerung der Scangeschwindigkeit die Energiedichte erhöht, wodurch der Balling-Effekt während der Bearbeitung verringert wird, was wiederum zu einer geringeren Oberflächenrauheit beiträgt. In Abbildung 13 wird beispielsweise die maximale Oberflächenrauheit bei 13,82 µm beobachtet, wenn die Energiedichte niedrig ist. Eine Erhöhung der Energiedichte auf 55 J/mm3 führt jedoch zu einem Rückgang der Oberflächenrauhigkeit auf 12,79 µm.
3.6 Vergleiche mit früheren Studien
Die Ergebnisse wurden mit der Literaturübersicht auf der Grundlage des Härtetests verglichen, insbesondere mit Eliasu et al[35]. Bei den mechanischen Eigenschaften wurden im Vergleich zu Eliasu et al.[35] geringe Unterschiede bei der Härteprüfung festgestellt, mit einer Änderung der Werte zwischen 2 und 5 HV, wie in Tabelle 4 dargestellt. Beim Vergleich der Mikrostruktur fällt auf, dass die Mikrostruktur von Eliasu et al. [35] besser ist als unser jetziges Ergebnis, was die beobachteten Veränderungen in der Härte verursacht haben könnte (siehe Abbildung 17).
4. Schlussfolgerungen
Das Drucken eines geschlossenen Laufrads mittels Laser-Pulverbettschmelzen erfordert sorgfältige Überlegungen zu den Druckparametern, um die mit dem Druckprozess verbundenen Komplexitäten zu mindern. Dazu gehören ein ausgeklügeltes Design für die richtige Auswahl des Gebäudewinkels und die Verwendung einer angemessenen Energiedichte der Außenhaut für eine erfolgreiche Herstellung. In dieser Studie wird rostfreier Stahl 316L für die Herstellung des geschlossenen Laufrads mittels LPBF-Technologie verwendet. Um erfolgreiche gedruckte Teile zu erhalten und die Gesamtqualität von geschlossenen Laufrädern zu verbessern, muss eine optimale Kombination mehrerer entscheidender Faktoren gewährleistet sein.
- Durch die Verwendung eines kleineren und größeren Laufrads mit einem Bauwinkel von 30˚ werden Defekte und Schäden während des Herstellungsprozesses deutlich reduziert, und es werden bessere Ergebnisse erzielt als bei einem Bauwinkel von 90˚.
- Die Angleichung der Energiedichte auf der Unterseite des Laufrads an die Energiedichte auf der Innenseite des Laufrads in einem Winkel von 30˚ gewährleistet einen erfolgreichen Laufraddruck ohne Defekte.
- Wenn die Energiedichte auf der Unterseite nur 20 % der Energiedichte auf der Innenseite ausmacht, kommt es zu spürbaren Schäden am Teil. Selbst in Fällen, in denen keine Schäden zu beobachten sind, zeigen sich auf der Oberfläche des geschlossenen Laufrads Anzeichen von Verbrennungen und Defekten, was besonders bei größeren geschlossenen Laufrädern deutlich wird.
- Eine Erhöhung der Energiedichte auf 55,55 J/mm3 führt zu einer Verringerung des nicht geschmolzenen Pulvers während des Prozesses.
- Durch die Erhöhung der Energiedichte sinkt die Oberflächenrauheit auf 12,79 µm bei einer Energiedichte von 55 J/mm3.
- Die Härte des Laufrads schwankt zwischen 226 und 233 HV und erreicht ein Maximum bei 233 HV, wenn die Energiedichte 41,66 J/mm3 beträgt.
Referenzen
[1] P. Sulzer, Physikalische Grundlagen, Zentrifugal Pump Handbook, 2010,pp. 1-26.
[2] J.J.M. Timothy, C. Allison, Aaron M. Rimpel, Jason C. Wilkes, Robert Pelton, Karl Wygant,
Manufacturing and Testing Experience with Direct Metal Laser Sintering for Closed Centrifugal Compressor Impellers, 43rd Turbomachinery & 30th Pump Users Symposia, Pump & Turbo 2014, Houston, TX, 2014.
[3] A.A. Scot Laney, Derrick Bauer, Evaluation of Various Methods for Manufacturing One Piece, Small Tip Opening Centrifugal Compressor Impellers, Asia Turbomachinery and Pump Symposium, Marina Bay
Sands, Singapur, 2016.
[4] Meli, E.; Rindi, A.; Ridolfi, A.; Furferi, R.; Buonamici, F.; Iurisci, G.; Corbò, S.; Cangioli, F. Design and Production of Innovative Turbomachinery Components via Topology Optimization and Additive
Fertigung. Int. J. Rotating Mach. 2019, 2019, 1-12, https://doi.org/10.1155/2019/9546831.
[5] Lezama-Nicolás, R.; Rodríguez-Salvador, M.; Río-Belver, R.; Bildosola,I. Eine bibliometrische Methode zur Bewertung der technologischen Reife: der Fall der additiven Fertigung. Scientometrics 2018, 117, 1425- 1452, https://doi.org/10.1007/s11192-018-2941-1.
[6] Aota, L.S.; Bajaj, P.; Sandim, H.R.Z.; Jägle, E.A. Laser Powder-Bed Fusion as an Alloy Development Tool: Parameterauswahl für das In-Situ-Legieren mit elementaren Pulvern. Materialien 2020, 13, 3922, doi:10.3390/ma13183922.
[7] Keshavarzkermani, A.; Marzbanrad, E.; Esmaeilizadeh, R.; Mahmoodkhani, Y.; Ali, U.; Enrique, P.D.; Zhou, N.Y.; Bonakdar, A.; Toyserkani, E. An investigation into the effect of process parameters on melt pool geometry, cell spacing, and grain refinement during laser powder bed fusion. Opt. Laser
Technol. 2019, 116, 83-91, https://doi.org/10.1016/j.optlastec.2019.03.012.
[8] Qu, S.; Ding, J.; Fu, J.; Fu, M.; Zhang, B.; Song, X. High-precision laser powder bed fusion processing of pure copper. Addit. Manuf. 2021, 48, https://doi.org/10.1016/j.addma.2021.102417.
[9] Huang, S.; Narayan, R.L.; Tan, J.H.K.; Sing, S.L.; Yeong, W.Y. Resolving the porosity-unmelted
einschluss-Dilemma beim In-situ-Legieren von Ti34Nb durch Laser-Pulverbettschmelzen. Acta Mater. 2020, 204, 116522, https://doi.org/10.1016/j.actamat.2020.116522.
[10] Mukherjee, T., Wei, H.L., De, A. und DebRoy, T., 2018. Heat and fluid flow in additive manufacturing- Part II: Powder bed fusion of stainless steel, and titanium, nickel and aluminum base alloys.
Computational Materials Science, 150,pp.369-380.
[11] Aota, L.S.; Bajaj, P.; Sandim, H.R.Z.; Jägle, E.A. Laser Powder-Bed Fusion as an Alloy Development Tool: Parameterauswahl für das In-Situ-Legieren mit elementaren Pulvern. Materials 2020, 13, 3922, doi:10.3390/ma13183922.
[12] Fernández, S.; Jiménez, M.; Porras, J.; Romero, L.; Espinosa, M.M.; Domínguez, M. Additive
Herstellung und Leistung von funktionalen Hydraulikpumpenlaufrädern in der Fused Deposition Modeling Technologie. J. Mech. Des. 2015, 138, 024501, https://doi.org/10.1115/1.4032089.
[13] Ponticelli, G.S.; Tagliaferri, F.; Venettacci, S.; Horn, M.; Giannini, O.; Guarino, S. Re-Engineering of an Impeller for Submersible Electric Pump to Be Produced by Selective Laser Melting. Appl. Sci. 2021, 11, 7375, https://doi.org/10.3390/app11167375.
[14] Mikula, J.; Ahluwalia, R.; Laskowski, R.; Wang, K.; Vastola, G.; Zhang, Y.-W. Modellierung des Einflusses von Prozessparametern auf die Bildung von Ausscheidungen bei der additiven Fertigung im Pulverbettverfahren von
IN718. Mater. Des. 2021, 207, 109851, https://doi.org/10.1016/j.matdes.2021.109851.
[15] O'brien, J.; Montgomery, S.; Yaghi, A.; Afazov, S. Process chain simulation of laser powder bed fusion including heat treatment and surface hardening. CIRP J. Manuf. Sci. Technol. 2021, 32, 266-276,
https://doi.org/10.1016/j.cirpj.2021.01.006.
[16] Yavari, R.; Williams, R.; Riensche, A.; Hooper, P.A.; Cole, K.D.; Jacquemetton, L.; Halliday, H.(.; Rao, P.K. Thermal modeling in metal additive manufacturing using graph theory - Application to laser powder bed fusion of alarge volume impeller. Addit. Manuf. 2021, 41, 101956,
https://doi.org/10.1016/j.addma.2021.101956.
[17] Tupac-Yupanqui, H.; Armani, A. Additive Manufacturing of Functional Inconel 718 Parts from Recycled Materials. J. Mater. Eng. Perform. 2021, 30, 1177-1187, https://doi.org/10.1007/s11665-020-05402-8.
[18] Kladovasilakis, N.; Kontodina, T.; Charalampous, P.; Kostavelis, I.; Tzetzis, D.; Tzovaras, D. A Case Study on 3D Scanning, Digital Reparation and Rapid Metal Additive Manufacturing of a Centrifugal Impeller. In Proceedings of the 24th Innovative Manufacturing Engineering and Energy International Conference (IManEE), Athen, Griechenland, 14-15 Dezember 2020, https://doi.org/10.1088/1757-
899x/1037/1/012018.
[19] Tian, Y.; Ren, H.; He, J.; Zha, X.; Lin, K.; Zhou, M.; Xiong, Y. Surface roughness improvement of Ti- 6Al-4V alloy overhang structures via process optimization for laser-powder bed fusion. J. Manuf.
Process. 2024, 110, 434-446, https://doi.org/10.1016/j.jmapro.2024.01.008.
[20] Guo, J.; Wang, Y.; Wang, Y.; Peng, S.; Wang, F. Simulation Study on the Energy Utilization Efficiency of a Turbine Impeller Based on a Selective Laser Melting Process. Appl. Sci. 2023, 13, 10657,
https://doi.org/10.3390/app131910657.
[21] Yaghi, A.; Ayvar-Soberanis, S.; Moturu, S.; Bilkhu, R.; Afazov, S. Design against distortion for additive manufacturing. Addit. Manuf. 2019, 27, 224-235, https://doi.org/10.1016/j.addma.2019.03.010.
[22] Kumar, A.; Shandiz, M.A.; Sikan, F.; Brochu, M. Microstructural and mechanical properties of an internal support-free IN625 closed impeller manufactured via laser powder bed fusion (L-PBF). Mater. Sci. Eng.
A 2023, 874, https://doi.org/10.1016/j.msea.2023.145080.
[23] O.D. Ian Campbell, Kowen Joseph, Wohlers Terry, 3D Prinitng and Additive Manufacturing Global State of the Industry, Wholers Report, Wholers Associates, 2018.
[24] Herzog, D.; Asami, K.; Scholl, C.; Ohle, C.; Emmelmann, C.; Sharma, A.; Markovic, N.; Harris, A. Design guidelines for laser powder bed fusion in Inconel 718.J. Laser Appl. 2022, 34, 012015,
https://doi.org/10.2351/7.0000508.
[25] Rebaioli, L.; Fassi, I. A review on benchmark artifacts for evaluating the geometrical performance of additive manufacturing processes. Int. J. Adv. Manuf. Technol. 2017, 93, 2571-2598,
https://doi.org/10.1007/s00170-017-0570-0.
[26] Yang, S.; Tang, Y.; Zhao, Y.F. A new part consolidation method to embrace the design freedom of
additiven Fertigung zu nutzen. J. Manuf. Process. 2015, 20, 444-449, https://doi.org/10.1016/j.jmapro.2015.06.024.
[27] Grasso, M.; Laguzza, V.; Semeraro, Q.; Colosimo, B.M. In-Process Monitoring of Selective Laser
Schmelzen: Spatial Detection of Defects Via Image Data Analysis. J. Manuf. Sci. Eng. 2016, 139, 051001, https://doi.org/10.1115/1.4034715.
[28] Li, J.; Cao, L.; Xu, J.; Wang, S.; Zhou, Q. In situ porosity intelligent classification of selective laser melting based on coaxial monitoring and image processing. Measurement 2021, 187, 110232,
https://doi.org/10.1016/j.measurement.2021.110232.
[29] Leung, C.L.A.; Marussi, S.; Atwood, R.C.; Towrie, M.; Withers, P.J.; Lee, P.D. In-situ-Röntgenbildgebung von
defekt- und Schmelzbaddynamik in der laseradditiven Fertigung. Nat. Commun. 2018, 9, 1-9, https://doi.org/10.1038/s41467-018-03734-7.
[30] Cacace, S.; Pagani, L.; Colosimo, B.M.; Semeraro, Q. The effect of energy density and porosity structure
auf die Zugfestigkeitseigenschaften von rostfreiem Stahl 316L, hergestellt durch Laser-Pulverbettschmelzen. Prog. Addit. Manuf. 2022, 7, 1053-1070, https://doi.org/10.1007/s40964-022-00281-y.
[31] Sun, Z.J.; Tan, X.P.; Tor, S.B.; Yeong, W.Y. Selektives Laserschmelzen von rostfreiem Stahl 316L mit geringer
porosität und hohen Aufbauraten. Mater. Des. 2016, 104, 197-204, https://doi.org/10.1016/j.matdes.2016.05.035.
[32] Clijsters S, Craeghs T, Buls S, Kempen K, Kruth JP (2014) In situ quality control of the selective laser melting process using a high-speed, real-time melt pool monitoring system. Int J Adv Manuf Technol. https:// doi. org/ 10. 1007/ s00170-014-6214-8
[33] Lippolis, V., Irurhe, O., Porricelli, A. C. R., Cortese, M., Schena, R., Imafidon, T., et al. (2017). Natürliches gemeinsames Vorkommen von Aflatoxinen und Ochratoxin A in Ingwer (Zingiber officinale) aus Nigeria. Food Control 73, 1061-1067. https://doi.org/10.1016/j. foodcont.2016.10.026
[34] Gu, D.; Shen, Y. Balling phenomena in direct laser sintering of stainless steel powder: Metallurgische Mechanismen und Kontrollmethoden. Mater. Des. 2009, 30, 2903-2910,
https://doi.org/10.1016/j.matdes.2009.01.013.
[35] Eliasu, A.; Czekanski, A.; Boakye-Yiadom, S. Effect of laser powder bed fusion parameters on the
entwicklung des Mikrogefüges und der Härte von rostfreiem Stahl 316L. Int. J. Adv. Manuf. Technol. 2021, 113, 2651-2669, https://doi.org/10.1007/s00170-021-06818-9.