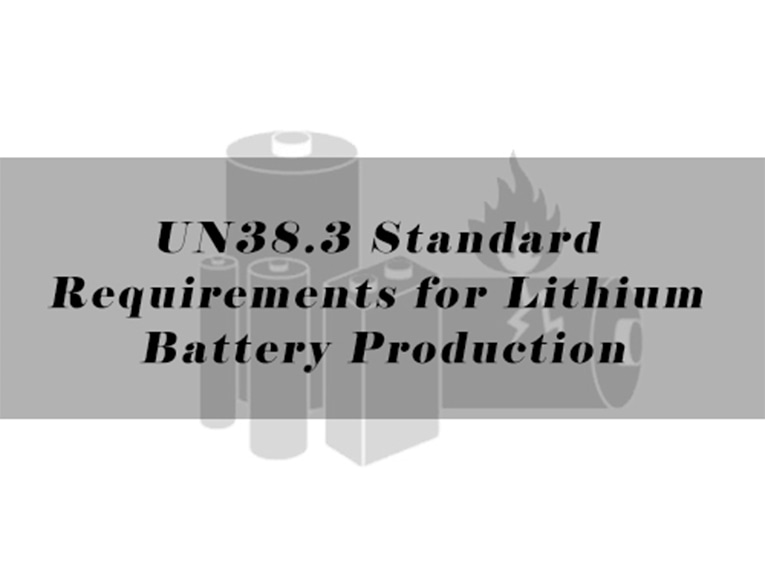
Automatische Übersetzung anzeigen
Dies ist eine automatisch generierte Übersetzung. Wenn Sie auf den englischen Originaltext zugreifen möchten, klicken Sie hier
#Neues aus der Industrie
UN38.3 Standardanforderungen für die Herstellung von Lithiumbatterien
DGBell informiert Sie über die Anforderungen der Norm UN38.3 für die Herstellung von Lithiumbatterien
UN38.3 Standardprüfgegenstände und -verfahren
Die Norm UN38.3 umfasst die folgenden 8 Nachweispositionen:
T1 Niederdruck,
T2 Temperaturzyklus,
T3-Schwingung,
T4-Schock,
T5 externer Kurzschluss,
T6 schwerer Objektaufprall (Lithium-Batteriekern),
T7 Überladung (Lithium-Batterie oder Lithium-Batterie )
T8-Zwangsentladung (Lithium-Batteriezellen).
Für Lithiumbatterien oder Lithiumbatteriesätze sind insgesamt 7 Prüfgegenstände T1 → T5, T6 und T7 erforderlich. Für Lithiumbatteriezellen sind jedoch die Prüfungen T1 → T5, T6 und T8 erforderlich. Unter ihnen müssen für die Tests T6, T7 und T8 separate Muster verwendet werden. Und bei T1 → T5-Tests muss dieselbe Probe nacheinander getestet werden.
Vergleich von UN38.3 & Internationalen Normen
Im Vergleich zu anderen internationalen Lithiumbatterienormen sind die in der Norm UN38.3 festgelegten Temperaturwechselbedingungen anspruchsvoller und länger. Andere Prüflinge der internationalen Norm verwenden im Allgemeinen separate Proben für die Prüfung. Der T1 → T5-Test in der UN3813-Norm prüft jedoch die gleiche Probe nacheinander. Die vorhergehende Prüfung kann sich negativ auf die nächste Prüfung auswirken und zum Nichtbestehen der Prüfung führen. Wenn die zur Prüfung vorgelegte Lithiumbatterie auf T1 → T5 in der Norm UN 38.3 geprüft wird, gibt es einen nicht qualifizierten Gegenstand. Die Unternehmen müssen die Norm UN3813 nach einer Prozessverbesserung erneut testen, was den Testzyklus erheblich verlängern wird.
Aus Tabelle 1 ist bekannt, dass im Vergleich zur internationalen Norm IEC62133 die Hoch- und Tieftemperaturexpositionszeit des Temperaturwechselteils in der Norm UN3813 bis zu 6 Stunden und die Tieftemperatur-Prüftemperatur -40 ± 2 ° C beträgt. Es ist einfacher, die internen Materialien der Batteriezelle zur Zersetzung und Gasbildung zu veranlassen. Im Falle von Problemen im Produktionsprozess, wenn das während des Temperaturschocks erzeugte Gas einen bestimmten Druck erreicht, ist es wahrscheinlich, dass das Gas aus dem Schwachpunkt des Batteriegehäuses oder der internen Dichtung austritt, was zu minderwertigen Phänomenen wie Gas- und Flüssigkeitsaustritt führt.
Vergleich der Normen UN38.3 und IEC62133
Projektstandard Erkennungsmethode Akzeptanzmethode Akzeptanzkriterien Unterschiede zwischen Standards
Temperaturzyklus UN38.3 Standard Lagerung bei 75 ± 2 ℃ für mindestens 6 h und dann bei der Prüftemperatur-40 ± 2 ℃ für mindestens 6 h. Das maximale Zeitintervall zwischen zwei extremen Prüftemperaturen beträgt 30 min. Dieser Vorgang muss 10 Mal wiederholt werden. Alle Testzellen und Batteriepacks wurden bei einer Umgebungstemperatur von 20 ± 5 ℃ für 24 h gelagert. Kein Massenverlust, kein Auslaufen, kein Auspuff, kein Zerfall, keine Rissbildung und keine Verbrennung. Und die Leerlaufspannung jeder vollgeladenen Prüfzelle oder Batterie beträgt nach dem Test nicht weniger als 90% der Spannung vor dem Test.
Die Norm UN38.3 hat eine niedrigere Prüftemperatur. Und die Expositionszeit bei hoher Temperatur und niedriger Temperatur ist länger.
IEC62133 Norm 1. Platzieren Sie die einzelne Zelle oder den Akkupack bei einer Umgebungstemperatur von 75 °C ± 2 °C für 4 h
2. Reduzieren Sie die Umgebungstemperatur innerhalb von 30 Minuten auf 20 ℃ ± 5 ℃ und halten Sie sie mindestens 2H
3. Reduzieren Sie die Umgebungstemperatur innerhalb von 30 Minuten auf -20 ℃ ± 2 ℃ und halten Sie 4H
4. Erhöhen Sie die Umgebungstemperatur innerhalb von 30 Minuten auf 20 ℃ ± 5 ℃ und halten Sie sie für mindestens 2 Stunden
5. Wiederholen Sie die obigen Schritte für 4 Zyklen.
6. Nach dem 5. Zyklus ist die Batterie während einer Erholungsphase von mindestens 24 Stunden zu lagern und zu inspizieren.
Kein Feuer, keine Explosion, keine Leckage
Analyse von UN3813-Standard-Testergebnissen und -Ursachen
Erster Fall
In der Norm UN3813 sind die im Rahmen des Temperaturzyklusprojekts getesteten Lithiumbatterien voll geladen (100% SOC). Wenn sie einem langfristigen Temperaturschock ausgesetzt werden, können daher relativ schwerwiegende Nebenreaktionen innerhalb der Batterie auftreten, bei denen eine große Menge an Gas erzeugt wird. Wenn es ein Problem mit dem Herstellungsprozess der Batterie gibt, wenn eine bestimmte Menge an Luftdruck angesammelt wird, können das Gas und der Elektrolyt aus dem Spalt im Gehäuse oder an der Stelle, an der das Lot geschweißt wird, austreten.
Probleme im Herstellungsprozess können die folgenden Bedingungen haben:
Die Verschweißung des Batteriegehäuses und des Deckels ist nicht fest und nicht abgedichtet;
Es gibt fehlende Schweißnähte, falsche Schweißnähte und Risse, und die Schweißnähte haben Risse, Sprünge usw;
Wenn die Stahlkugel versiegelt ist, ist die Größe der Stahlkugel ungeeignet, und das Material der Stahlkugel ist ein anderes als das der Kappe;
Der positive Pol der Kappe ist nicht fest vernietet, und es entsteht ein Spalt;
Die Elastizität der Isolierdichtung ist ungeeignet, sie ist nicht korrosionsbeständig, und sie ist leicht zu altern.
Probleme wie Massenverlust, Leckage und Auspuff während des UN38.3-Standardtemperaturzyklus hängen hauptsächlich mit dem Herstellungsprozess zusammen. Die Anatomie der ausgelaufenen Batterie ergab, dass die Batterie während des Zusammenbaus ungleichmäßiger Kraft ausgesetzt war, wodurch sich die innere Isolierplatte der Batterie verformte, was dazu führte, dass die Batterie an der Isolierplatte auslief.
Zweiter Fall
Darüber hinaus ergab der Test, dass einige Lithiumbatterien nach dem Temperaturzyklustest keinen Massenverlust, kein Auslaufen, keinen Auspuff, keinen Zerfall, keine Risse und keine Verbrennung aufweisen. Aufgrund der chemischen Reaktion zwischen den aktiven Materialien der positiven und negativen Elektrode und dem Elektrolyten im Inneren der Batterie während des Temperaturschocks wurde jedoch eine gewisse Menge Gas erzeugt, das während des Tests ein Ausbeulphänomen verursachte.
Allerdings ist es für die geschwollene Lithiumbatterie schwieriger, den Vibrationstest beim nächsten Hochbeschleunigungs- und Langzeit-Vibrationstest zu bestehen. Es ist wahrscheinlich, dass die Batterie Gaslecks und Lecks produziert, was zu übermäßigen Qualitätsverlusten führt und letztendlich den Vibrationstest nicht besteht. Dies erfordert von den Herstellern von Lithiumbatterien in der Forschungs- und Entwicklungsphase zusätzlich zur kontinuierlichen Verbesserung der elektrischen Leistung, muss aber auch die nachteiligen Auswirkungen von Temperaturschocks auf die Materialien von Lithiumbatterien voll berücksichtigen.
Ausgehend von Lithiumbatteriematerialien wurde die Stabilität jedes chemischen Materials bei der im Temperaturzyklus von 75 ℃,-40 ℃ spezifizierten Prüftemperatur und die Übergangspunkte zwischen 75 ℃ und -40 ℃ untersucht. Finden Sie heraus, welche Materialien bei der Testtemperatur zur Gasbildung neigen. Durch eine große Anzahl von Experimenten zur Verbesserung des Prozesses dieser Materialien oder zur Suche nach anderen alternativen Materialien, um ein besseres Gleichgewicht zwischen der elektrischen Leistung und der Sicherheitsleistung von Lithiumbatterien zu finden.
Dritter Fall
In einem anderen Fall bestand die Lithiumzelle, die während des Temperaturzyklus anschwoll, die anschließenden Vibrations- und Schockprüfungen. Die große Gasmenge, die während des Temperaturzyklus intern erzeugt wird, wirkt sich jedoch nachteilig auf die Schweißteile um die Hülle herum aus. Der Druckstoß des Gases führt in einigen Bereichen direkt zu einer Schwächung der Schweißfestigkeit. Beim externen Kurzschlusstest nach dem Aufpralltest erwärmte sich die Lithium-Einzelzellenbatterie schnell, und im Inneren des Gehäuses wurde weiterhin eine große Menge Gas erzeugt. Wenn der Innendruck der Schale auf einen bestimmten Wert ansteigt, wird das Gas aus dem Bereich, in dem die Schweißfestigkeit schwach wird, freigesetzt, was zum Bruch der Schale führt. Infolgedessen kann der externe Kurzschlusstest nicht bestanden werden.
Die folgenden Prüfkammern werden in der Norm UN38.3 verwendet:
Servocomputer-Batterie-Druckfestigkeitsprüfgerät
Schwingungsprüfsystem
Schock-Test-System
Batterie-Crush-Nagel-Penetrationstester
Höhensimulation Testkammer
Schwerer Schlagtester
Temperaturregelung Batterie-Kurzschluss-Prüfkammer
Batterie-Zerstörungsprüfkammer
Temperaturwechsel-Prüfkammer