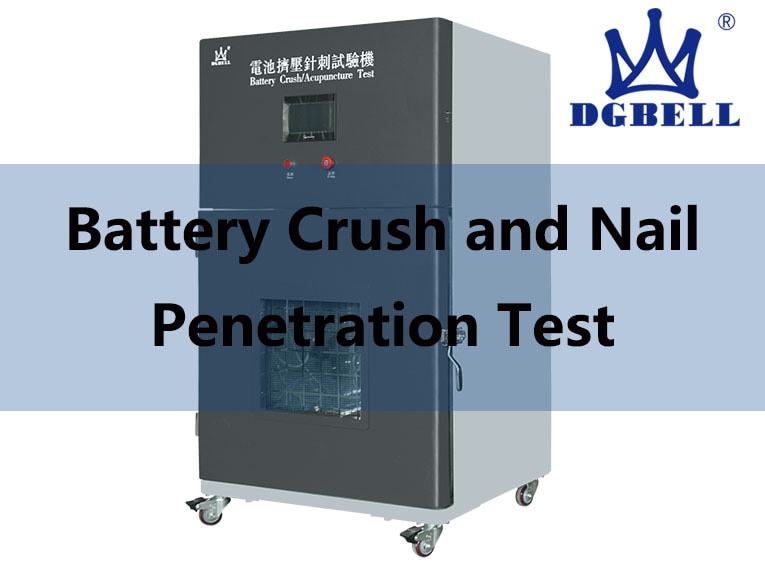
#Neues aus der Industrie
Batterie-Crush- und Nagelpenetrationstest
Batterie-Crush- und Nagelpenetrationstest
Mit der zunehmenden Anzahl von Fahrzeugen auf der Welt rücken die Probleme der Umweltverschmutzung und der mangelnden Verantwortung für die Ölressourcen immer stärker in den Vordergrund. Aufgrund der Vorteile des grünen Umweltschutzes, der Diversifizierung der Energiequellen und der hohen Energieeffizienz arbeiten alle Länder der Welt aktiv an der Erforschung und Entwicklung von Elektrofahrzeugen, die herkömmliche Fahrzeuge ersetzen können. Zu den Leistungsbatterien für Elektrofahrzeuge gehören derzeit Blei-Säure-Batterien, Lithium-Ionen-Batterien und Zink-Luft-Batterien. Unter ihnen ist die Lithium-Ionen-Batterie die neueste Hochleistungsbatterie, die am schnellsten erforscht und kommerzialisiert wurde. Aufgrund seiner hohen Spannung, hohen spezifischen Energie und guten Zyklenleistung wird es häufig in Energiebatterien für Elektrofahrzeuge verwendet. Aufgrund der häufigen Sicherheitsunfälle im tatsächlichen Verwendungsprozess wurde seiner Sicherheit jedoch immer mehr Aufmerksamkeit geschenkt.
Derzeit gibt es zwei Formen von Leistungsbatterien. Zum einen werden Batterien mit kleiner Kapazität parallel geschaltet, um Batterien mit großer Kapazität zu bilden. Der Vorteil besteht darin, dass die Energiereserven des kleinsten Energiespeichers (Einzelzelle) gering sind. Wenn es zu Verbrennungen und Explosionen kommt, sind die Folgen relativ gering. Seine Explosionsenergie wird keine Kettenreaktion auslösen und andere Energiespeichereinheiten werden nicht explodieren. Der Nachteil besteht darin, dass die Anzahl der kleinsten Energiespeicher zu groß und schwer zu verwalten ist. Die andere ist eine laminierte Batterie mit hoher Kapazität, die die Vorteile einer kompakten Struktur, eines kleinen Volumens und einer hohen Energiedichte bietet. Der Nachteil besteht darin, dass der einzelne Energiespeicher groß ist und die Folgen von Unfällen relativ schwerwiegend sind. Je nach Verpackungsform lässt es sich in „Weichverpackung“ und „Hartschale“ unterteilen. Der Vorteil einer „flexiblen Verpackung“ besteht darin, dass sie sich im Falle anormaler Bedingungen so weit ausdehnt, dass die äußere Verpackung zerbricht, was nicht leicht zu Unfällen wie einer Explosion führen kann; Der Nachteil ist, dass die Schale schwach ist. Scharfe Gegenstände können leicht in den Akku eindringen. Der Nachteil der „harten Schale“ besteht darin, dass sie im Vergleich zur „weichen Verpackung“ bei ungewöhnlichen Bedingungen leicht explodiert; Die Vorteile bestehen darin, dass die Schale relativ stark ist, scharfe Gegenstände nicht leicht zu durchdringen sind und der Akku besser geschützt ist.
Die Norm legt fest, dass die Sicherheitstests Folgendes umfassen: Tiefentladung, Überladung, Kurzschluss, Fall, Erhitzen, Extrusion und Akupunktur. Nach einer Vielzahl von Tests und Statistiken ist die Qualifikationsrate für Sicherheitstests bei Batterien mit einer Kapazität von weniger als 30 Ah hoch, und die Probleme über 30 Ah konzentrieren sich hauptsächlich auf die Testpunkte wie Modulkurzschluss, Modulextrusion, Modul Akupunktur usw. Zusätzlich zu den oben genannten obligatorischen Inspektionspunkten. Unternehmen können je nach ihren eigenen Produktanforderungen auch F&E-Eintauchtests, Brandtests, Schießtests, Vibrationsentladungstests und andere Tests durchführen.
Basierend auf einer Vielzahl von Sicherheitstests für Leistungsbatterien wurden der Testprozess und die Ergebnisse analysiert und untersucht. Die Testproben umfassen Monomer und Modul (fünf oder mehr Monomere sind in Reihe geschaltet, und das in diesem Artikel vorgestellte Modul besteht aus fünf in Reihe geschalteten Monomeren).
1. Drucktest
Standardanforderungen: Der Extrusionstest umfasst Einzelextrusion und Modulextrusion. Bei der Einzelextrusion muss Druck senkrecht auf die Batterieelektrodenplatte ausgeübt werden und die Fläche des Extrusionskopfes darf nicht weniger als 20 cm betragen, bis das Batteriegehäuse zerbrochen oder intern kurzgeschlossen ist (die Batteriespannung beträgt 0 V). Während des Extrusionstests von Batteriezellen darf es weder zu Explosionen noch zu Bränden kommen. Bei der Modulextrusion muss Druck senkrecht zur Ausrichtungsrichtung der Batteriezellen ausgeübt werden. Der Extrusionskopf, dessen Größe den Standardanforderungen entspricht, muss 5 Minuten lang auf 85 % der ursprünglichen Größe des Batteriemoduls und dann auf 50 % der ursprünglichen Größe des Batteriemoduls extrudiert werden. Während des Extrusionstests des Batteriemoduls darf es weder zu Explosionen noch zu Bränden kommen.
Analyse und Recherche der Testergebnisse: Der Test wird beendet, wenn die Batteriezelle aufgrund eines Schalenbruchs oder eines internen Kurzschlusses extrudiert wird. Während des Tests werden Überwachungsgeräte wie Kameras verwendet, um zu erkennen, ob das Batteriegehäuse gebrochen ist, und Spannungserkennungsgeräte werden verwendet, um zu überwachen, ob die Batteriespannung 0 V beträgt. Die meisten Einzelbatterien explodieren nicht und fangen kein Feuer, wenn sie zusammengedrückt werden, und a Es brennen nur wenige Batterien. Die Endbedingungen des Tests des Batteriemoduls während des Extrusionsprozesses sind relativ rau. Beim Extrusionsprozess wird das Batteriemodul großflächig komprimiert, wodurch es zu einem großflächigen Kurzschluss im Inneren der Batterie kommt. Das Batteriemodul wird von starker Rauchentwicklung begleitet, Elektrolyt wird aus dem Sicherheitsventil ausgestoßen, es kommt zu einer Explosion und einem Brand. Unterschiedliche Batteriemodule haben unterschiedliche Explosions- und Brandstadien. In manchen Betrieben ist das Sicherheitsventil der Batterie zu fest eingestellt. Wenn das Batteriemodul kurzgeschlossen ist, kann es die Wärme nicht rechtzeitig abgeben, was zu einem thermischen Durchgehen und einem schnellen Temperaturanstieg führt. Dies ist einer der Gründe für die Explosion und den Brand der Batterie.
2. Nagelpenetrationstest
Standardanforderungen: Der Nagelpenetrationstest umfasst Einzelzellakupunktur und Modulakupunktur. Die einzelne Nadel muss senkrecht zur Richtung der Batterieplatte stehen und der Durchmesser der Nadel muss Φ 3 ~ 8 mm betragen. Geschwindigkeit 10 ~ 40 mm/s, Nadeldurchdringung durch die Batteriezelle; Die Batterie darf während des Nadeltests nicht explodieren oder Feuer fangen. Die Nadelung des Batteriemoduls muss senkrecht zur Richtung der Batterieelektrodenplatte erfolgen, der Durchmesser der Nadel muss 3 bis 8 mm betragen, die Geschwindigkeit muss 10 bis 40 mm/s betragen und der Nadelungsgrad muss mindestens drei durchdringen Batteriezellen: Während des Nadeltests des Batteriemoduls darf es weder zu Explosionen noch zu Bränden kommen.
Analyse und Recherche der Testergebnisse: Durchmesser Ф Eine 5 mm Stahlnadel mit einer Länge von 350 mm wurde mit einer Geschwindigkeit von 20 mm/s in die Batterie eingeführt. Beim Einführen der Stahlnadel in die Batterie kam es zu einem Kurzschluss in der Batterie und eine große Menge Rauch und Elektrolyt wurde aus dem Sicherheitsventil und der Nadeleinführposition freigesetzt. Die freigesetzte Wärme führt dazu, dass sich das Batteriegehäuse ausdehnt und verformt und sogar einen Teil der Kunststoffhülle schmilzt. Aufgrund des Austretens von Elektrolyt während des Tests ist die interne Hitze, die beim Kurzschluss der Batterie entsteht, extrem hoch und sogar die durchdringende Stahlnadel schmilzt. Wenn der Flammschutzgrad des für die Hülle verwendeten Materials nicht ausreicht, kann es zu einer Verbrennung kommen, und das offene Feuer entzündet den Elektrolyten, was die Verbrennung weiter verschlimmert. Die Batterie kann nicht sofort nach dem Einstechen der Nadel herausgezogen werden und sollte in der Batterie verbleiben. Wenn die Nadel sofort herausgezogen wird, wird die Nadel herausgezogen, nachdem die Batterie wieder die normale Temperatur erreicht hat, da die Batterie heftig reagiert und Sauerstoff an die Stelle gelangt, an der die Nadel eingestochen wird, was leicht zu einer Verbrennung führen kann.
Die Durchdringungsausrüstung des Mechanismus durchsticht die Batterie von oben nach unten. Da der Platzierungszustand der Batterie im Test nicht mit dem tatsächlichen Ladezustand übereinstimmt, schreibt die Norm nur die Akupunktur der vertikalen Polplatte vor und gibt nicht die Platzierungsrichtung an. Die horizontale Akupunktur ist der eigentliche Belastungszustand. Ob die Ergebnisse der horizontalen Akupunktur und der vertikalen Akupunktur konsistent sind, muss durch zahlreiche Tests überprüft werden. Es wird empfohlen, dass die Akupunkturrichtung der Batterie mit dem tatsächlichen Ladezustand übereinstimmt.
Die oben genannten Sicherheitstests wie Kurzschluss, Extrusion und Akupunktur dienen hauptsächlich dazu, die mögliche Situation der Leistungsbatterie unter ungewöhnlichen Umständen wie Autounfällen zu simulieren, wenn das Elektrofahrzeug mit hoher Geschwindigkeit fährt. Derzeit ist die Leistungsbatterie im Elektrofahrzeug in mehrere kleine Kästen unterteilt und an verschiedenen Positionen des Fahrzeugs installiert. Jede kleine Box ist durch Drähte verbunden. Um Kurzschlüsse zu verhindern, können Sicherungen zwischen mehreren Anwendungspools in Reihe geschaltet werden. Das Batteriemanagementsystem (BMS) erfasst die abnormale Spannung und warnt den Fahrer mit Ton und Licht auf dem Instrumentenbrett des Elektrofahrzeugs. Um zu verhindern, dass die Batterie beim Aufprall und Wegrollen des Fahrzeugs gequetscht wird, muss der Batteriekasten stabil sein und eine gute Wärmeableitung gewährleisten. Die Strukturfestigkeit des Gehäuses, in dem der Batteriekasten installiert ist, sollte hoch sein oder ein besonderer Schutz erforderlich sein.