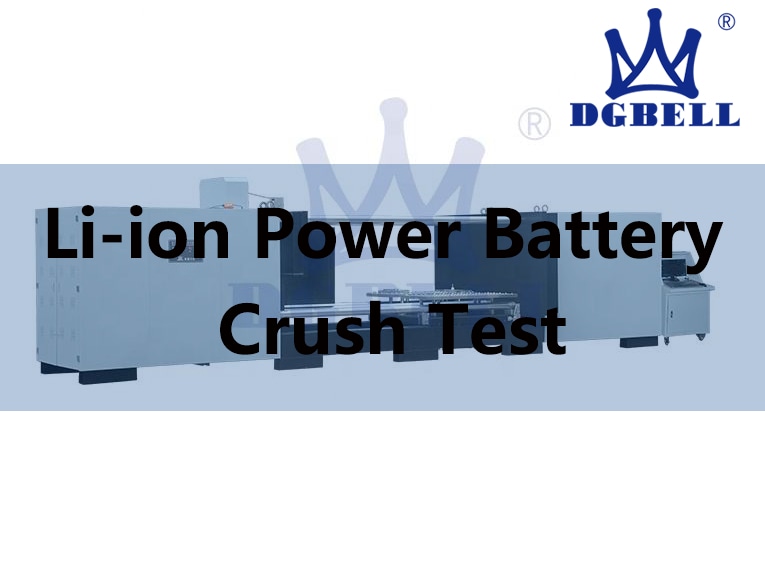
#Neues aus der Industrie
Li-Ion Power Battery Crush Test - Teil 2
Li-Ion Power Battery Crush Test - Teil 2
2.1 Testvorbereitung
Zylindrische und quadratische Batterien werden üblicherweise als Energiezellen verwendet. Das Forschungsobjekt dieser Arbeit ist eine quadratische Zelle, die hauptsächlich aus dem chemischen Materialsystem der positiven Nickel-Kobalt-Mangan-Elektrode und der negativen Graphitelektrode besteht. Einzelne Batteriegröße: X Y Z=B x L x H=27 mm x 148 mm x 94 mm, Nennspannung: 3,7 V, Nennkapazität: 37 Ah. Die Einzelbatterie ist im Modul in Form einer Überlagerung entlang der Breitenrichtung (X-Richtung) der Einzelbatterie angeordnet. In diesem Papier ist die Definition des Moduls Crush-Richtung ist im Einklang mit der von Monomer, und die Batterie Monomer und Modul sind in Abbildung 3 dargestellt. Die Verschiebung, Last, Spannung, Temperaturdaten und Videodaten des Quetschungsprozesses wurden gesammelt, indem die Zelle und das Modul mit dem Eindringkörper extrudiert wurden, und die Testergebnisse wurden analysiert.
2.2 Ergebnisse des Crushtests der Zelle
Führen Sie den XYZ-Crush-Arbeitstest für den elektrischen Kern in diesen drei Richtungen durch und vergleichen Sie die Steifigkeit in den drei Richtungen, wie in Abbildung 4 dargestellt.
Die Steifigkeit des elektrischen Kerns in X-Richtung ist am größten, und er kann bei gleicher Verformung einer größeren Druckkraft standhalten. Die Y- und Z-Richtung sind relativ schwach. Shenxin ist im Allgemeinen in X-Richtung im Modul in Reihe angeordnet. Bei einem Seitenaufprall des Fahrzeugs wird der elektrische Kern hauptsächlich in X- und Y-Richtung gequetscht und verformt.
Um den kritischen Punkt der Beschädigung der Schale und der Rissbildung unter den Bedingungen der Quetschung des elektrischen Kerns zu finden, wird der Quetschtest in der Y-Richtung des elektrischen Kerns durchgeführt. Jede Testgruppe wurde dreimal extrudiert, und die Stauchgeschwindigkeit betrug 0,2 mm/s.
In der ersten Testgruppe wird das Monomer kontinuierlich geladen, bis die Batterie die Kontrolle über die Wärme verliert und der Ladezustand (SOC) der Batterie 100% beträgt;
Die zweite Testgruppe dient dazu, den kritischen Punkt der Rissbildung in der Batteriehülle zu ermitteln. Um die Beobachtung zu erleichtern, wird die Batterie in Abschnitten gleichzeitig um jeweils 3 mm entladen und geladen, wobei jeder Abschnitt 200 Sekunden lang gehalten wird;
Die dritte Testgruppe wurde kontinuierlich bis zum kritischen Wert der Rissbildung in der Hülle belastet und dann stehen gelassen, um zu analysieren, ob die Gefahr eines thermischen Durchgehens besteht. Die erste Gruppe von Prüfkernen wird kontinuierlich bis zum Bruch der Schale belastet, wie in Abbildung 5 dargestellt.
Aus der vergleichenden Analyse der Tests geht hervor, dass die Versagensart des Quetschens des elektrischen Kerns mit Unsicherheit behaftet ist.
Bei der Quetschprüfung besteht der Versagensmodus des elektrischen Kerns darin, dass die Schale extrudiert und beschädigt wird, ohne dass es zu einem Brand oder einer Explosion kommt; die Schale wird ohne Beschädigung extrudiert, aber es kommt zu einer Rauch- oder Feuerexplosion; die Schale wird zerquetscht und beschädigt, was zu einem Brand oder einer Explosion führt.
Die Abbildungen 6 und 7 zeigen die Quetschverformung der Hülle des elektrischen Kerns nach der zweiten und dritten Testgruppe. Aus Abbildung 6 ist ersichtlich, dass die negative Seite des elektrischen Kerns geknackt wurde, die positive Seite jedoch nicht;
Wenn die erste Druckverformung 12 mm beträgt, bricht die negative Seite, die positive Seite jedoch nicht. Durch die Analyse der zweiten Versuchsgruppe wird vorläufig festgestellt, dass die Schale unter der Druckbedingung des elektrischen Kerns beschädigt ist und Risse aufweist
Der kritische Wert liegt bei 12 mm. Aus Abbildung 7 ist ersichtlich, dass bei einer gemessenen Quetschverschiebung von 12 mm die drei Testkerne keinen Bruch der Schale und kein Feuer oder eine Explosion aufwiesen. Nach dem Test verhielten sich die gemessenen Kerne normal, nachdem sie 24 Stunden lang gestanden hatten.
Diese Testgruppe bestätigte, dass der kritische Wert für das Versagen dieser Art von Elektrokernen mit 12 mm bestimmt werden kann. Durch die Analyse von drei Testgruppen wird festgestellt, dass der kritische Punkt des Versagensmodus der Beschädigung und Rissbildung der Hülle des elektrischen Kerns 12 mm beträgt, was unter dem Grenzwert liegt, so dass das Risiko der Rissbildung in der Hülle gering ist und Feuer und Explosion nicht auftreten;
Wird der Grenzwert überschritten, besteht eine gewisse Unsicherheit, ob der Kernmantel beschädigt oder gerissen ist, was immer noch ein hohes Sicherheitsrisiko darstellt; die Unsicherheit bezüglich des Versagens des elektrischen Kerns durch Feuer und Explosion ist groß, und die Versagensarten sind uneinheitlich. Daher kann festgestellt werden, dass die Beschädigungstoleranz der Zelle 12 mm beträgt, und der Betriebszustand der Zelle ist im Test relativ stabil. Die Bedingungen, unter denen die Batterie in der tatsächlichen Anwendung extrudiert wird, sind jedoch unterschiedlich. In Anbetracht der Tatsache, dass eine gewisse Sicherheitsspanne vorgesehen ist, wird die Schadenstoleranz für diesen Zellentyp auf 10 mm festgelegt.
2.3 Ergebnisse der Quetschprüfung des Moduls
Das Modul wird einem Stauchversuch in X- bzw. Y-Richtung unterzogen. Die Belastungsgeschwindigkeit beträgt 0,2 mm/s. Bei dem Test befindet sich das Modul im Volllastzustand, d. h. der SOC des Moduls beträgt 100 %. Die X- und Y-Richtung entspricht dem Quetschverhalten beim Seitenaufprall des Fahrzeugs. Wiederholen Sie den Quetschtest dreimal in zwei Quetschrichtungen, um die Wirksamkeit des Tests zu gewährleisten.
Abbildung 8 zeigt den Quetschungszustand des Moduls in verschiedenen Richtungen.
Abbildung 9 zeigt den Quetschungsprozess des Moduls in X- und Y-Richtung. Im Vergleich dazu ist der Prozess des thermischen Durchgehens, der durch das Zusammendrücken in verschiedenen Richtungen des Moduls verursacht wird, folgender: Das Batteriemodul verformt sich in der Anfangsphase, und Rauch oder Funken erscheinen, wenn die innere Beschädigung der Batterie mit der Druckbelastung zunimmt, was zu Feuer und Explosion führt.
Abbildung 10 zeigt die Temperatur- und Spannungsänderungskurven des Moduls in X- und Y-Richtung während der Quetschung. Für die Analyse werden die Module M2 (X-Crush) und M4 (Y-Crush) als Beispiele herangezogen.
In Abbildung 10 x Richtung, während 0~400s, wird das Modul allmählich verformt durch Quetschung, und die Modultemperatur und Spannung bleiben stabil; Wenn die Last 400s erreicht, beginnt die Spannung auf 0 V zu fallen, und die Temperatur steigt von 26 ℃ auf 156 ℃, zu diesem Zeitpunkt beginnt das Batteriemodul zu rauchen; Mit der weiteren Erhöhung der Quetschkraft, steigt die Temperatur auf 500 ℃, und dann das Batteriemodul brennt und explodiert.
In Abbildung 10 y-Richtung sind die Spannung und die Temperatur des Moduls innerhalb von 0~300s relativ stabil. Wenn die Temperatur von 300s auf 550 ℃ ansteigt, brennt und explodiert das Modul, und die Spannung fällt auf 0V. Durch den Vergleich und die Analyse der Temperatur- und Spannungskurven wird außerdem festgestellt, dass der thermische Durchbruch eher in der Y-Richtung der Module auftritt.
Anhand der Kurve der Verschiebungsbelastung, der Spannungs- und der Temperaturkurve, die bei der Prüfung ermittelt wurden, wird die Quetschungsdistanz beim Versagen des Batteriemoduls in XY-2-Richtung analysiert. In der X-Richtung beträgt der Quetschweg 40 mm, 42 mm bzw. 30 mm, wenn die Module M1, M2 und M3 versagen; Extrudieren in Y-Richtung. Wenn die Module M4, M5 und M6 versagen, beträgt die Quetschverschiebung 21 mm, 15 mm bzw. 24 mm. Aus dem Vergleich geht hervor, dass die Y-Richtung des Moduls nach dem Strangpressen anfälliger für ein Versagen ist als die X-Richtung.