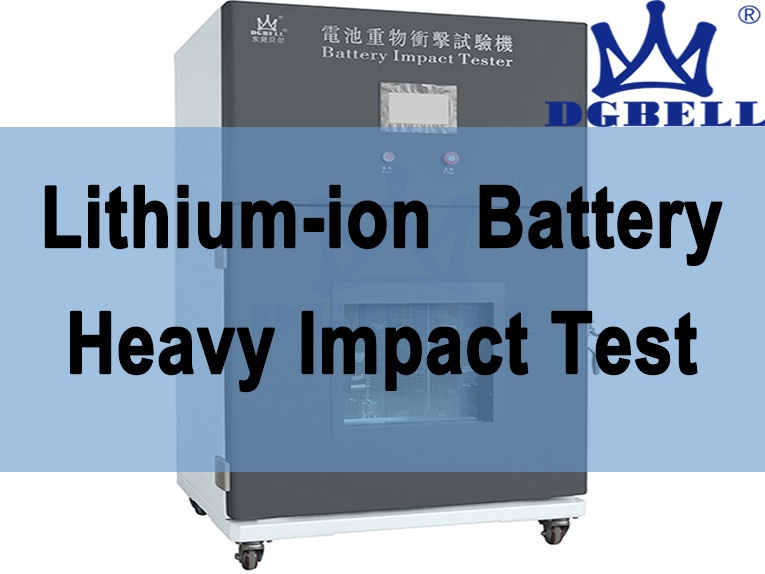
Automatische Übersetzung anzeigen
Dies ist eine automatisch generierte Übersetzung. Wenn Sie auf den englischen Originaltext zugreifen möchten, klicken Sie hier
#Neues aus der Industrie
Lithium-Ionen-Batterie Schwerer Stoßtest
Lithium-Ionen-Batterie Schwerer Stoßtest
Lithium-Ionen-Batterien sind aufgrund ihrer hohen spezifischen Energie und hohen Spannung zu einer der wichtigsten Energiequellen für tragbare elektronische Produkte wie Mobiltelefone und Laptops geworden. Unter missbräuchlichen Bedingungen wie Erhitzung, Überladung, Überentladung, Kurzschluss, Vibration, Kompression usw. kann es bei Lithium-Ionen-Batterien jedoch zu Zwischenfällen wie Bränden, Explosionen und sogar Personenschäden kommen, was dazu geführt hat, dass eine große Zahl von Lithium-Ionen-Batterien zurückgerufen wurde.
Daher ist die Verbesserung der Sicherheitsleistung von Lithium-Ionen-Batterien zu einer Schlüsselfrage bei ihrer Entwicklung geworden. Derzeit haben viele Länder oder Prüfinstitute entsprechende Sicherheitsprüfverfahren für Lithium-Ionen-Batterien entwickelt. Lithium-Ionen-Batterien müssen Sicherheitstests bestehen, um die Risiken bei ihrer Verwendung zu verringern. Zu den internationalen Normen für die Sicherheit von Lithium-Ionen-Batterien gehören vor allem IEC 62133, IEC 62281, UL 1642, UL 2054, UN 38.3 usw.
In den oben genannten Normen ist der Aufpralltest mit schweren Gegenständen ein Projekt, das den internen Kurzschluss von Lithium-Ionen-Batterien simuliert. In diesem Artikel wurden verschiedene Modelle von Lithium-Ionen-Batterien gemäß den Anforderungen der Norm einem Aufpralltest mit schweren Gegenständen unterzogen. Die Testergebnisse wurden verglichen und analysiert, indem die Batterie nach dem Versuch zerlegt wurde.
1 Test
1.1 Testausrüstung und -umgebung
Bei dem Prüfgerät handelt es sich um die explosionsgeschützte Schlagprüfkammer von DGBELL. Die Umgebungstemperatur wurde während des Versuchs stets auf (20 ± 5) ℃ gehalten.
1.2 Prüfmuster
Die in diesem Experiment verwendeten Lithium-Ionen-Batteriemuster sind wie folgt: 18650 zylindrische Lithium-Ionen-Batterie; quadratische Aluminiumschalen-Batterie; quadratische Lithium-Ionen-Polymer-Batterie
1.3 Testmethoden
Legen Sie Lithium-Ionen-Batterien unterschiedlicher Form auf eine ebene Fläche, platzieren Sie einen Eisenstab mit einem Durchmesser von 15,8 mm horizontal in der Mitte der Batterie und lassen Sie einen 9,1 kg schweren Hammer aus einer Höhe von (610 ± 15) m auf die Batterie fallen. Bei quadratischen Batterien sollten sie außerdem um 90 ° um die Längsachse gedreht werden, damit sie sowohl auf der breiten als auch auf der schmalen Seite starken Stößen standhalten. Die Temperatur an der Oberfläche der Batterie wird während des Versuchs mit einem Thermoelement überwacht, das an der Oberfläche der Batterie angebracht ist.
2 Ergebnisse
2.1 18650 Lithium-Ionen-Akkus
Nach einem Schlag mit einem schweren Gegenstand bleibt auf der Oberfläche der Batterie eine tiefe Delle zurück, die hauptsächlich durch die Kompression des Eisenstabs verursacht wird, der nach einem Schlag mit einem schweren Hammer auf die Oberfläche der Batterie gelegt wird. Auf der Oberfläche des Pluspols der Batterie ist Rost entstanden, der hauptsächlich auf das Öffnen des internen Überdruckventils während des Schlagversuchs zurückzuführen ist, wodurch etwas Elektrolyt ausgetreten ist. Der Elektrolyt produzierte beim Kontakt mit Luft korrosive Substanzen, was zur Korrosion der Pluspolkappe führte.
Nach der Demontage des Batteriegehäuses zeigten sich Risse an der Oberfläche der Batteriezellen. Dies ist hauptsächlich auf die Ausdehnung und Verformung der Elektroden zurückzuführen, die durch den Eisenstab verursacht wurde, der auf die Batterie drückte. Die Batteriezelle wurde aufgeklappt, und sowohl die Elektrode als auch die Öffnungsfolie brachen an der Stelle, an der der Eisenstab zusammengedrückt wurde. Die Beschichtungsmaterialien der positiven und negativen Elektroden haben sich abgelöst.
2.2 Quadratische Batterie
(1) Batterie mit Aluminiumgehäuse
Für quadratische Lithium-Ionen-Batterien gibt es im Allgemeinen zwei Verpackungsformen: Aluminiumschale und Aluminium-Kunststoff.
Die Batterie wies durch die Kompression des Eisenstabs ebenfalls Dellen auf und wurde in der Mitte sehr dünn. Nach der Demontage der Aluminiumhülle ist zu erkennen, dass die internen Batteriezellen in zwei Hälften geteilt wurden. Beim Aufklappen der Batteriezelle ist zu erkennen, dass die Beschichtung des Batteriematerials abgeblättert ist und die Elektroden Falten aufweisen. Dies ist auf den Aufprall des Eisenstabs auf das Innere der Batterie zurückzuführen, der eine Quetschkraft in der Ebene erzeugt. Außerdem behindert die hohe Härte der Aluminiumhülle die Ausdehnung der Batteriezelle in horizontaler Richtung, was zu Faltenbildung an den Elektroden führt.
Nach dem Schmalflächentest der quadratischen Batterie ist die Schmalfläche der Batterie vollständig gequetscht und verformt worden. Nach der Demontage des Batteriegehäuses wurde festgestellt, dass die inneren Batteriezellen schwere Brüche aufwiesen. Beim Aufklappen der Elektrode wurde festgestellt, dass das aktive Material abgefallen und das Diaphragma gerissen war.
(2) Lithium-Ionen-Polymer-Batterien
Für Lithium-Ionen-Polymer-Batterien, die in Aluminium-Kunststoff verpackt sind. Die Ergebnisse des Batterietests sind ähnlich wie die von Batterien mit Aluminiumhülle. Aufgrund der thermischen Versiegelung der Aluminium-Kunststoff-Hülle sind die internen Batteriezellen jedoch nach dem Batterietest äußeren Kräften ausgesetzt. Zweitens wurde die Batterie aufgrund der geringen Dicke der Aluminium-Kunststoff-Verpackung bei äußeren Einwirkungen in zwei Teile geteilt.
2.3 Diskussion der Testergebnisse
Aus den obigen Testergebnissen geht hervor, dass der Aufpralltest mit schweren Gegenständen den internen Kurzschluss von Lithium-Ionen-Batterien simulieren kann. Beim Aufpralltest mit schweren Gegenständen wurde die Batterie externen Kräften ausgesetzt, was zu einer Verformung des Batteriegehäuses führte. Außerdem wurde die Batteriezelle verformt, was zu Spannungen an den Elektroden und dem Separator führte. Unter dieser Belastung löst sich das Elektrodenmaterial ab, und die Membran reißt aufgrund ihrer geringen Dicke, was zu einer direkten elektronischen Leitung zwischen dem positiven und dem negativen Elektrodenmaterial oder zu einem Kontakt zwischen dem Kupfer- (Aluminium-) Kollektor und dem positiven (negativen) Elektrodenmaterial (d. h. zu einem internen Kurzschluss) führt, was einen lokal hohen Entladestrom und Ohmsche Wärme zur Folge hat.
Da interne Kurzschlüsse an mehreren Stellen auftreten, führt die erzeugte Wärme zu weiteren Nebenreaktionen, wie der Zersetzung der Elektrode und des Elektrolyten. Während des Experiments kam es zu einem deutlichen Anstieg der Batterietemperatur. Beim Lithium-Ionen-Akkumodell 18650 führte ein interner Kurzschluss zu einer beträchtlichen Gasmenge, die einen Anstieg des Innendrucks verursachte. Nach Erreichen eines bestimmten Wertes öffnete sich das Überdruckventil der Batterie, um das saure Gas abzulassen, wodurch letztlich Sicherheitsunfälle vermieden wurden. Bei quadratischen Lithium-Ionen-Batterien ist ihre Dicke relativ gering. Im Falle eines äußeren Stoßes kann die Batterie zerbrechen oder in zwei Hälften geteilt werden. Bei einem internen Kurzschluss sind die internen Komponenten der Batterie direkt der Luft ausgesetzt und reagieren.
3 Schlussfolgerung
Anhand von Aufpralltests mit schweren Gegenständen an verschiedenen Typen von Lithium-Ionen-Batterien lässt sich feststellen, dass diese Testmethode die Situation von internen Kurzschlüssen in Batterien wirksam simulieren kann. Die Analyse der verschiedenen Batterietypen ergab, dass die Elektroden und die Membranen im Inneren der Batterien gebrochen waren, was zu internen Kurzschlüssen in den Batterien führte. Die Analyse und das Verständnis dieses experimentellen Phänomens wird den Batterieherstellern helfen, die Prüfstandards für Batterien zu verstehen und dadurch die Produktqualität von Lithium-Ionen-Batterien zu verbessern und ihre Sicherheit zu erhöhen.