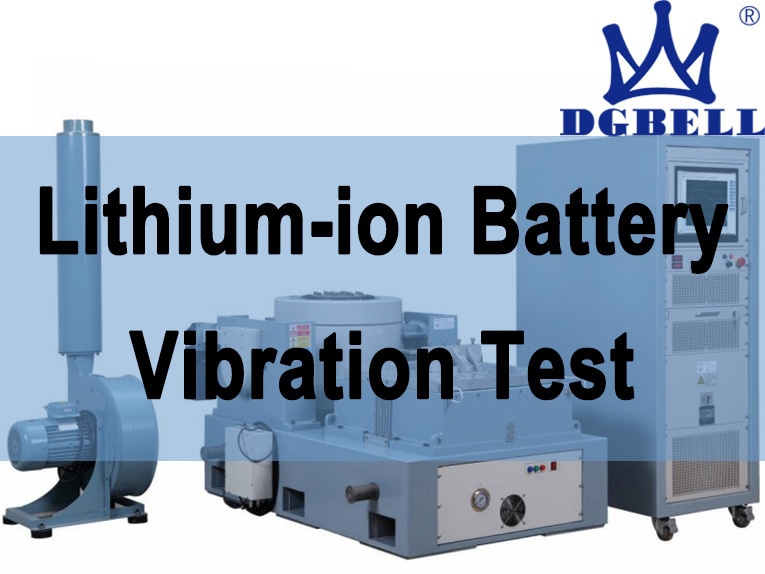
Automatische Übersetzung anzeigen
Dies ist eine automatisch generierte Übersetzung. Wenn Sie auf den englischen Originaltext zugreifen möchten, klicken Sie hier
#Neues aus der Industrie
Lithium-Ionen-Batterie Vibrationstest
Lithium-Ionen-Batterie Vibrationstest
Lithium-Ionen-Batterien stellen sowohl in der Zivilluftfahrt und im Straßenverkehr als auch in Verkehrsmitteln und Haushaltsgeräten ein Sicherheitsrisiko dar. Um Lösungen für diese Probleme zu finden, wurden die Auswirkungen mechanischer Schwingungen auf die Leistung und das thermische Durchgehen von Lithium-Ionen-Batterien unter Niederspannungsbedingungen untersucht. Unter Niederspannungsbedingungen führen mechanische Vibrationen zu einem Anstieg der Temperatur des thermischen Durchgehens von Lithium-Ionen-Batterien und zu einer erheblichen Veränderung der Ansprechzeit von Sicherheitsventilen.
Mechanische Schwingungen mit niedriger Frequenz und großer Amplitude beschleunigen den Prozess des Batteriekurzschlusses, während hochfrequente Schwingungen die Zündtemperatur und das Abgasvolumen von Lithiumbatterien erhöhen. Bei 18650 Lithium-Ionen-Batterien liegt die Temperatur, bei der das Sicherheitsventil herausspringt, zwischen 140 und 150 °C. Wenn das Sicherheitsventil herausspringt, ist die Intensität der Gasfreisetzung relativ hoch, und das Gassignal kann eine Schlüsselvariable für die Sicherheitswarnung von Lithiumbatterien sein. Nach Niederspannungsvibrationen ist die Entladekapazität von Lithium-Ionen-Batterien kleiner als die der Originalbatterie, und die Entladegeschwindigkeit ist schneller als die der Originalbatterie
1 Art des Ausfalls von Lithium-Ionen-Batterien
Die Lithium-Ionen-Batterien sind das "Herz" eines Autos und bestimmen die Fahrleistung des Fahrzeugs. Das Lithium-Ionen-Batteriesystem besteht aus vier Hauptkomponenten: Batteriemodule (Einzelzellen in Reihe und parallel), Batteriemanagementsystem (BMS), Wärmemanagementsystem sowie elektrische und mechanische Komponenten. Die Hauptfunktion des BMS ist die Überwachung der Batteriespannung, des Stroms und der Temperatur in Echtzeit durch Mantelsensoren, Aktoren, Hauptsteuerchips usw. Aufgrund der internen Alterung und des Verfalls jeder einzelnen Batterie im Akkupack sowie der Korrosion des Schaltkreises während des Akkugruppierungsprozesses kann ein unsachgemäßer Betrieb während der Nutzung jedoch zu abnormalen externen Faktoren wie Überladung und Entladung führen. Die kombinierte Wirkung dieser internen und externen Faktoren führt zu internen und externen Fehlern der Batterie. Die internen Fehler von Lithium-Ionen-Batterien lassen sich in Typen wie Überladung, Überentladung, interner Kurzschluss und thermisches Durchgehen einteilen.
Interne Fehler werden durch eine Fehlfunktion des BMS und des Sensors selbst verursacht, wodurch der Sensor nicht mehr richtig funktioniert. Andererseits werden sie durch elektrochemische Reaktionen und interne Kurzschlüsse in der internen Struktur der Batterie verursacht, was zum Phänomen der Lithium-Dendriten führt. Die Gefahr von externen Fehlern in Lithium-Ionen-Batterien ist jedoch in der Regel größer als die von internen Fehlern. Externe Fehler können eine Kettenreaktion interner Fehler auslösen, die schließlich zu einer unkontrollierten Erwärmung führt. Sensorausfälle werden oft am leichtesten übersehen, können aber schwerwiegende Folgen haben.
BMS stützt sich auf Sensoren, um Funktionen wie die Gleichgewichtssteuerung, die Fehlerdiagnose und die Abschätzung des Ladezustands (SOC) zu erfüllen. Wenn der Sensor Abweichungen aufweist, abdriftet oder nicht mehr funktioniert, kann er keine Echtzeitdaten erhalten und keine genauen und vernünftigen Aussagen über den aktuellen Zustand der Batterie machen. Dies kann nicht nur die Leistung beeinträchtigen, sondern auch zu schweren Sicherheitsunfällen führen. Aufgrund der hohen Verborgenheit der Sensoren ist die Diagnose jedoch schwierig, was auch der Schwerpunkt und die Schwierigkeit der aktuellen Sensorforschung ist.
Das BMS verwaltet Batteriepakete, die aus Hunderten oder gar Tausenden von Einzelbatterien bestehen. Aufgrund der ähnlichen Merkmale von Batteriezellen-, Sensor- und Steckverbinderfehlern sowie der Tatsache, dass viele Fehler im Wesentlichen klein und gut verborgen sind, ist es schwierig, sie schnell zu erkennen. Daher kommt es bei BMS gelegentlich zu Fehldiagnosen und Fehlbedienungen. Für die Sicherheit des Fahrzeugs ist es von entscheidender Bedeutung, dass mehrere Batteriefehler schnell erkannt und genau diagnostiziert werden. Der Prozess der Batteriefehlerdiagnose lässt sich grob in vier Aspekte unterteilen: Fehlererkennung, Fehlerklassifizierung, Fehlerlokalisierung und Fehlerisolierung. Die Datenverarbeitung von Batterien spielt eine grundlegende Rolle bei der Batteriefehlerdiagnose, und die Wirksamkeit der Entrauschung kann durch die Einbeziehung mathematischer morphologischer Filtermethoden effektiv überprüft werden.
2 Probleme mit Diagnoseverfahren zur Spannungsmessung
(1) In der Praxis können Batteriemanagementsysteme nur die Klemmenspannung jeder einzelnen Batterie im Batteriesatz messen. Damit der Spannungsmesswert auch die Spannung an den einzelnen Klemmen und die Spannung an den Steckern umfasst, müssen zusätzliche Messleitungen hinzugefügt werden, was die Komplexität der Anlage zweifellos erhöht. Wenn zu Beginn der Entwicklung des Batteriemanagementsystems die erfasste Spannung die Klemmenspannung und die Spannung an den Anschlüssen umfasst, ist das Batteriemanagementsystem nicht in der Lage, die Klemmenspannung der Batterie genau zu ermitteln und somit das Laden und Entladen der Batterie nicht wirksam zu steuern und zu kontrollieren, was zu Überladungs- und Entladungsfehlern führen kann
(2) Die durch Änderungen des Innenwiderstands der Batterie verursachten Spannungsänderungen ähneln den Spannungsänderungen bei Anschlussfehlern. Beide liegen in der gleichen Größenordnung, so dass Diagnosemethoden, die auf Spannungssignalen basieren, ebenfalls vor der Herausforderung stehen, zwischen Anschlussfehlern und Fehlern mit erhöhtem Innenwiderstand der Batterie zu unterscheiden.
(3) Wenn eine leichte Verbindungslockerung innerhalb des Akkupacks auftritt, ist der Anstieg des Kontaktwiderstands sehr gering. Wenn der Arbeitsstrom des Akkupacks gering ist, führt ein solcher Verbindungsfehler nicht zu signifikanten Änderungen des Spannungssignals. Daher kann die oben erwähnte, auf dem Spannungssignal basierende Diagnosemethode möglicherweise nicht in der Lage sein, einen leichten Verbindungsfehler frühzeitig zu erkennen.
3 Der Einfluss von Vibrationen
Durchführung von Lade- und Entladetests bei Atmosphärendruck an Batterien, die einer Vibrationsbehandlung bei niedriger Spannung unterzogen wurden, um die Veränderungen in der Lade- und Entladeleistung von Lithiumbatterien nach einem Flugzeugtransport zu demonstrieren. Die Ergebnisse zeigten, dass nach einer Vibrationsfrequenzbehandlung bei 60 Hz und 80 Hz in einer Niederspannungsumgebung der Ladeeffekt geringer war als der der Originalbatterie, und die 60-Hz-Behandlung hatte den größten Einfluss auf die Kapazität der Lithiumbatterien;
Die anderen Vibrationsfrequenzen beschleunigen alle die Ladegeschwindigkeit, und die Veränderung ist bei 120 Hz signifikant. Während des Entladevorgangs weist die Kurve der Lithium-Ionen-Batterie mit 120-Hz-Vibrationsbehandlung die größte Abweichung auf, während die Kurve mit 200 Hz die kleinste Abweichung aufweist. Die übrigen Abweichungen reichen von gering bis groß, einschließlich 60 Hz, 80 Hz, 180 Hz, 160 Hz, 140 Hz und 100 Hz.
Es wurde festgestellt, dass es keine positive Korrelation zwischen der Schwingungsfrequenz und der Entladungssituation gibt, was darauf hindeuten könnte, dass die durch die Schwingungen verursachten Schäden an der Struktur mit der Reaktion der Batteriestruktur auf Frequenz und Amplitude zusammenhängen. Einige Schwingungsfrequenzen und -amplituden schädigen die Struktur von 18650-Lithiumbatterien stärker.
Aus dem Gesamtvergleich der Lade- und Entladekurven geht hervor, dass die Entladekapazität aller Batterien, die vibriert wurden, kleiner ist als die der Originalbatterie, und die Entladegeschwindigkeit ist schneller als die der Originalbatterie. Dies kann darauf hindeuten, dass die Kapazität und die Entladeleistung der Batterie durch mechanische Vibrationen beeinträchtigt werden.
In der Tat ändert sich der Kontaktgrad zwischen der positiven und der negativen Elektrode im Elektrolyten von Lithium-Ionen-Batterien, nachdem sie mechanischen Vibrationen ausgesetzt waren, was zu einer Veränderung der Kontaktfläche zwischen der Elektrode und der Elektrolytlösung führt, was die Übertragung von Lithiumionen auf die negative Elektrode während des Ladens und Entladens behindert und somit die Menge des in die negative Elektrode eingebetteten Lithiums verringert.
4 Schlussfolgerung
In diesem Artikel wird eine Methode zur Fehlerdiagnose für die Verbindungen von Lithium-Ionen-Batteriepacks auf der Grundlage von mechanischen Schwingungssignalen vorgeschlagen, und es werden folgende Schlussfolgerungen gezogen Die Verwendung verschiedener piezoelektrischer Keramikplatten zur Erzeugung von Schwingungsanregungen, zur Messung der Schwingungsantwort und zur Extraktion von Zeit-Frequenz-Merkmalen aus dem Antwortsignal kann die Klassifizierung von Ein-Punkt- und Mehr-Punkt-Verbindungsfehlermodi effektiv erreichen. Zukünftige Arbeiten werden die Anordnung der piezoelektrischen Keramikplatten optimieren, Schwingungssignale aus der Fahrzeugumgebung sammeln und diese Methode für die Diagnose von Verbindungsfehlern bei Lithium-Ionen-Batteriepacks in Fahrzeugen geeignet machen