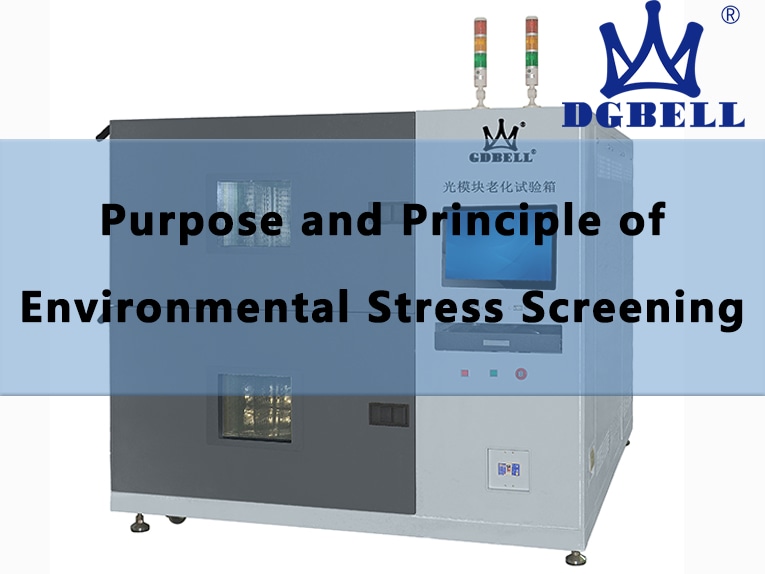
Automatische Übersetzung anzeigen
Dies ist eine automatisch generierte Übersetzung. Wenn Sie auf den englischen Originaltext zugreifen möchten, klicken Sie hier
#Neues aus der Industrie
Zweck und Prinzip des Umweltbelastungsscreenings
Zweck und Prinzip des Umweltbelastungsscreenings
Zweck des Umweltstress-Screenings
Der Zweck der Prüfung auf Umweltbelastungen besteht darin, das frühzeitige Versagen von Produkten zu erkennen und zu beseitigen, sie beim Verlassen des Werks in das Stadium des zufälligen Versagens zu überführen und sie mit einem inhärenten Zuverlässigkeitsniveau an die Benutzer zu liefern.
Das Prinzip des Umweltstress-Screenings
Beim Umweltstress-Screening werden die internen potenziellen Defekte durch die Anwendung angemessener Umweltbelastungen und elektrischer Spannungen auf elektronische Geräte beschleunigt zu Fehlern, so dass sie gefunden und beseitigt werden können.
Das Umweltstress-Screening ist ein technologisches Mittel der Geräteentwicklung und -produktion. Der Screening-Effekt hängt von der angewendeten Umweltbelastung, der Höhe der elektrischen Belastung und den Fähigkeiten der Erkennungsinstrumente ab. Das Ausmaß der angewandten Belastung bestimmt, ob potenzielle Defekte innerhalb einer bestimmten Zeit zu Fehlern beschleunigt werden können; die Erkennungsfähigkeit bestimmt, ob die potenziellen Defekte, die durch die Belastung zu Fehlern beschleunigt wurden, zur Fehlerbehebung gefunden werden können. Daher kann die Prüfung auf Umweltbelastungen als Erweiterung der Inspektion und des Prüfverfahrens für die Produktqualität angesehen werden. 2 Fehlerklassifizierung
Allgemeine Definitionen
Der Verlust der spezifizierten Funktion eines Produkts wird als Fehler bezeichnet. Reparierbare Produkte werden oft als Fehler bezeichnet. Bei den Geräten stellt jedes Qualitätsmerkmal, das nicht den festgelegten technischen Normen entspricht, einen Fehler dar.
Das Versagen der meisten elektronischen Geräte wird als Fehler bezeichnet. Siehe Abbildung 2.11 für die Unterteilung nach der Fehlerursache. Aus der Abbildung ist ersichtlich, dass Gerätefehler in zufällige Fehler und Defektfehler unterteilt werden. Man geht davon aus, dass zufällige Ausfälle zufällige Ausfälle sind, die durch die inhärente Ausfallrate von Bauteilen und Komponenten verursacht werden, während defekte Ausfälle durch Rohmaterialfehler, Komponentendefekte, Montageprozessfehler und Konstruktionsfehler verursacht werden, Komponentendefekte selbst durch Defekte wie Struktur, Prozess und Materialien verursacht werden und Konstruktionsfehler Schaltungsdesignfehler, strukturelle Designfehler Prozessdesignfehler usw. umfassen.
Klassifizierung der visuellen Defekte von elektronischen Geräten
Im Hinblick auf die Auswirkungen und Folgen werden Defekte in tödliche Defekte, schwere Defekte und leichte Defekte eingeteilt: Aus visueller Sicht sind die wichtigsten Prozessarten von Defekten: Schweißen, nicht schweißbare Verbindungen, Überschuss an Drähten und Kabeln, Kurzschlussschutzlücken, Kontakte, Leiterplatten, Herstellung und Installation von Teilen, Komponenten, Wicklung, Kennzeichnung usw., von denen die meisten zu tödlichen Defekten oder schweren Defekten führen können, leichte Defekte sind häufig.
Als schwerwiegende Defekte gelten Defekte, die zu Schäden oder Unsicherheiten für das Personal führen können, z. B. bei der Verwendung, Wartung, dem Transport und der Lagerung von Ausrüstungen, oder die die taktische Leistung einiger wichtiger Ausrüstungen (z. B. Schiffe, Panzer, große Artillerie, Flugzeuge, Raketen usw.) beeinträchtigen können.
Ein schwerwiegender Defekt ist ein Fehler, der zu einem Ausfall führen oder die Leistungsfähigkeit des Geräts ernsthaft beeinträchtigen kann, aber kein tödlicher Fehler ist.
Leichte Defekte beziehen sich auf Defekte, die keine schweren Defekte darstellen, aber die Leistung des Geräts beeinträchtigen oder nicht den spezifizierten technischen Standards entsprechen und nur geringe Auswirkungen auf die Verwendung oder den Betrieb des Geräts haben.
Visuelle Mängel beziehen sich auf Mängel, die direkt mit den menschlichen Sehorganen wahrgenommen oder mit einfachen Mitteln anhand der Qualitätsmerkmale des Geräts beurteilt werden können.
Der Qualitätsprüfer der Fertigungseinheit kann die meisten sichtbaren Fehler finden und sie den zuständigen Abteilungen zur Beseitigung vorlegen. Nur unsichtbare Fehler können durch Umweltbelastungsprüfungen oder andere Methoden aufgespürt werden, da sonst die Zuverlässigkeit des Produkts beeinträchtigt wird.
Konstruktionsprinzip des Screening-Schemas für Umweltbelastungen
Das Konstruktionsprinzip des Prüfschemas für Umweltbelastungen besteht darin, dass die Prüfbeanspruchung die durch potenzielle Konstruktions-, Fertigungs- und Bauteilfehler verursachten Fehler stimulieren kann: Die angewandte Belastung muss nicht das vom Produkt vorgegebene Lebens-, Aufgaben- und Umweltprofil simulieren; bei der Prüfung sind verschiedene, durch die Konstruktion vorgegebene Betriebsarten zu simulieren.
Festlegung von Routine-Screening oder quantitativem Screening je nach Bedingungen und Notwendigkeit: Formulierung von Screening-Methoden je nach den verschiedenen Phasen und Produkteigenschaften des Falles.
Screening im Entwicklungsstadium
In der Entwicklungsphase wird das konventionelle Screening im Allgemeinen nach den aus der Erfahrung gewonnenen Screening-Methoden durchgeführt. Die wichtigsten Funktionen sind: Einerseits werden Informationen über die Art und Menge möglicher Produktfehler und die Wirkung von Screening-Methoden gesammelt; andererseits werden Routineprüfungen vor Zuverlässigkeits- und technischen Entwicklungstests durchgeführt, was Testzeit und -kosten sparen kann. Gleichzeitig ist es förderlich für die Entwicklung ausgereifter und schneller Entwicklungsprüfverfahren.
Das Routine-Screening in der Entwicklungsphase dient der Sammlung von Daten für das quantitative Screening in der Produktionsphase, der Vorbereitung des quantitativen Screenings und dem Entwurf des Rahmens für das quantitative Screening.
Screening im Produktionsstadium
Das Screening in der Produktionsphase dient in erster Linie der Umsetzung des in der Entwicklungsphase entworfenen quantitativen Screening-Konzepts. Durch den Vergleich der erfassten Fehlerniederschläge mit dem geschätzten Entwurfswert werden Maßnahmen zur Anpassung des Screening- und Herstellungsprozesses vorgeschlagen; Verbesserung oder Neuformulierung des quantitativen Screening-Konzepts unter Bezugnahme auf die Erfahrungsdaten zum quantitativen Screening von Produkten mit ähnlicher Struktur und Reife. Diese empirischen Daten umfassen hauptsächlich:
Modelle von Bauteilen und Bauteilen mit hoher Ausfallrate: Lieferanten von Produkten mit hoher Ausfallrate; Eingangsinspektions-, Test- und Screening-Daten von Bauteilen: Aufzeichnungen über frühere Screenings und Tests; Aufzeichnungen über Zuverlässigkeitssteigerungstests: andere Testaufzeichnungen.
Auswirkungen von Umweltbelastungen auf Fehler
Die Umweltbelastung im Feld ist der Hauptfaktor, der die Entwicklung von Fehlern zu Fehlern beeinflusst. Jeder Defekt, der sich zu einem Fehler entwickelt, muss einer bestimmten Belastung ausgesetzt werden. Nur wenn das Produkt einer Umweltbelastung ausgesetzt wird, die dem Schwellenwert entspricht oder diesen übersteigt, können einige Defekte nach einer gewissen Zeit zu Fehlern werden: Bei einigen milden Umweltbelastungen werden sich viele Defekte nicht zu Fehlern entwickeln. Daher kann der Zweck des Screenings nur erreicht werden, wenn als Screening-Bedingung eine Belastung gewählt wird, die einige Fehler aufdecken kann.
Schlussfolgerung
Die Prüfung der Umweltbelastung ist der technologische Prozess der Entwicklung und Produktion der gesamten Maschine. Jedes Produkt muss geprüft werden. Um Ressourcen und Zeit zu sparen, sollten wir versuchen, die Belastungsbedingungen mit hoher Effizienz und die Montagequalität mit niedrigen Kosten zu wählen. Zufallsvibrationsgeräte und Temperaturwechselgeräte sind notwendig, und der Hersteller sollte so schnell wie möglich damit ausgestattet werden. Vor der Ausstattung kann die Anlage in nahe gelegenen Einheiten mit diesen Bedingungen eingesetzt werden. Zu diesem Zeitpunkt ist es noch wichtiger, die Montageebene auszuwählen und zu prüfen.
Der Entwurf eines Schemas zur Überprüfung der Umweltbelastung ist eine umfassende Arbeit. Es ist notwendig, die Geschichte und die aktuelle Situation des Produktdesigns, des Prozesses und der Komponenten zu beherrschen und die notwendigen Daten zu sammeln: Bei der Auswahl des Umweltstress-Screenings oder des quantitativen Umweltstress-Screenings und der Auswahl der Screening-Baugruppenebene müssen einige Risiken abgezogen werden. Daher muss die Methode der Systemtechnik angewandt werden, um eine umfassende Abwägung der Anforderungen an die Produktzuverlässigkeit vorzunehmen.
Umweltbelastungs-Screening und Zuverlässigkeitssteigerungstests gehören zu den technischen Zuverlässigkeitstests. Sie haben die gleichen allgemeinen Ziele und ihre eigenen Merkmale. Sie können sich gegenseitig ergänzen, aber nicht ersetzen. Das Umweltstress-Screening kann zur Durchführung einiger Zuverlässigkeitssteigerungstests verwendet werden, um die Ergebnisse des Umweltstress-Screenings vollständig zu nutzen und die Testeffizienz zu verbessern.