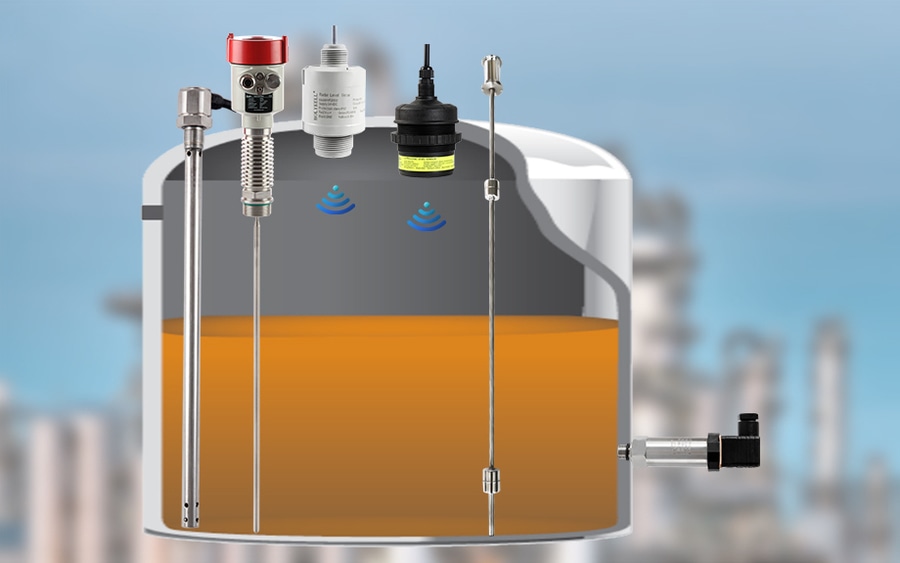
Automatische Übersetzung anzeigen
Dies ist eine automatisch generierte Übersetzung. Wenn Sie auf den englischen Originaltext zugreifen möchten, klicken Sie hier
#Neues aus der Industrie
Füllstandsmesstechnik für die Raffinerieindustrie
Eintauchbarer Drucksensor
Die Raffinerieindustrie befindet sich im Umbruch, da bestehende Raffinerien modernisiert werden, um wettbewerbsfähig zu bleiben. Ziel der Raffinerieanlagen ist es, die Energieeffizienz zu steigern, die Produktionsleistung zu maximieren und die Produktqualität zu verbessern. Die Raffinerien sehen sich jedoch während dieser Umstellung mit verschiedenen Herausforderungen konfrontiert, unter anderem mit der Notwendigkeit, die Energieeffizienz zu verbessern, die Betriebs- und Wartungskosten zu senken und die Sicherheit zu gewährleisten, während gleichzeitig strenge Umweltvorschriften eingehalten werden müssen. Diese Herausforderungen gelten auch für neue Raffinerien, die mit der Komplexität der Integration der Automatisierung zur Verarbeitung von billigerem, schwefelreichem oder schwerem Rohöl konfrontiert sind.
Im Raffineriebetrieb ist eine genaue Füllstandsmessung und -regelung von entscheidender Bedeutung. Bei täglichen Produktionsraten von bis zu 100.000 Barrel können Raffinerien über 1.000 Füllstandmesspunkte haben. Herkömmliche Methoden, wie z. B. schwimmerbasierte Systeme, sind anfällig für Ungenauigkeiten, die durch Schwankungen in der Dichte und Temperatur verschiedener Rohöle verursacht werden und die Zuverlässigkeit dieser Messungen beeinträchtigen. Diese Schwankungen können den Kontrollprozess beeinträchtigen und sich negativ auf die Produktivität und Produktqualität der Raffinerie auswirken. Daher gehen Raffinerien dazu über, präzisere und wartungsärmere Technologien einzusetzen, um genaue Messungen zu gewährleisten und die Prozesskontrolle insgesamt zu verbessern.
In diesem Artikel werden fünf fortschrittliche Technologien zur Füllstandmessung vorgestellt, die für die Raffinerieindustrie geeignet sind: Radar, Ultraschall, Differenzdruck, magnetostriktive und kapazitive Füllstandsensoren. Jede Technologie hat einzigartige Vorteile und Einschränkungen, die sie je nach Leistungsanforderungen, Betriebsbedingungen und Installationsbeschränkungen für unterschiedliche Anwendungen geeignet machen.
1. Füllstandmessgeräte mit geführtem Wellenradar (GWR)
Prinzip der Funktionsweise:
Füllstandmessgeräte mit geführtem Wellenradar (GWR), auch bekannt als Zeitbereichsreflektometer (TDR) oder Mikrowellenimpulsradar (MIR), ermöglichen eine kontinuierliche Füllstandmessung. Das Gerät sendet Mikrowellenimpulse mit geringer Leistung auf eine Sonde, die sich mit Lichtgeschwindigkeit fortbewegt. Die Impulse werden an der Flüssigkeits-Luft-Grenzfläche reflektiert, und die Zeitverzögerung zwischen Senden und Empfangen wird zur Berechnung des Abstands zur Flüssigkeitsoberfläche verwendet.
Vorteile:
Präzise und zuverlässig: Ermöglicht genaue Messungen bei schwierigen Anwendungen wie der Messung von Flüssig-Flüssig-Grenzflächen (z. B. Öl-Wasser-Grenzfläche) und durch Schaum hindurch.
Unbeeinflusst von Änderungen des Mediums: Änderungen der Dichte, Dielektrizitätskonstante oder Leitfähigkeit der Flüssigkeit haben keinen Einfluss auf die Messgenauigkeit.
Geringer Wartungsaufwand: Da es keine beweglichen Teile gibt, erfordern GWR-Geräte nur minimale Wartung und können leicht in bestehende Systeme integriert werden.
Beschränkungen:
Überlegungen zur Installation: Die Wahl des Sondentyps und der Einbauhöhe kann die Leistung einschränken, insbesondere bei Anwendungen mit dicken oder klebrigen Medien.
2. Berührungslose Radar-Füllstandstransmitter
Das Funktionsprinzip:
Berührungslose Radar-Füllstandmessgeräte senden Signale durch Dampf, um den Oberflächenabstand zu messen. Dieser Typ ist ideal für die Messung viskoser, klebriger und bewegter Flüssigkeiten in Tanks mit Mischern oder Rührwerken, da er den Sensor vollständig vom Prozessmedium isoliert.
Vorteile:
Kein physischer Kontakt: Geeignet für gefährliche oder korrosive Medien, da er nicht mit dem Prozessmaterial in Kontakt kommt.
Minimale Wartung: Da das Gerät nicht mit der Flüssigkeit in Berührung kommt, gibt es keine beweglichen Teile, die verschleißen könnten, was zu geringeren Wartungskosten führt.
Beschränkungen:
Herausforderungen bei der Installation: Für eine genaue Messung ist eine klare Sichtlinie auf die Oberfläche erforderlich. Raue oder turbulente Oberflächen können die Genauigkeit beeinträchtigen, und Oberflächenschaum oder Unruhe können zu Signalverlusten führen.
3. Ultraschall-Füllstandmessumformer
Das Funktionsprinzip:
Ultraschall-Füllstandmessgeräte verwenden Schallwellen, um den Abstand zur Flüssigkeitsoberfläche zu messen. Ein Impuls wird vom Messumformer ausgesendet, und die Zeit, die der Impuls benötigt, um zurück zu reflektieren, wird zur Bestimmung des Füllstands verwendet.
Vorteile:
Einfache Installation und Einrichtung: Einfach zu installieren und zu konfigurieren, daher für verschiedene Anwendungen geeignet, einschließlich Tanks und Silos.
Berührungslose Messung: Es ist kein direkter Kontakt mit dem Prozessmedium erforderlich, was den Wartungsaufwand reduziert.
Beschränkungen:
Temperaturempfindlichkeit: Änderungen der Prozesstemperatur können die Schallgeschwindigkeit beeinflussen, so dass für eine genaue Messung eine Temperaturkompensation erforderlich ist.
Oberflächenbedingungen: Schaum, Dampf oder turbulente Oberflächen können die Ultraschallwellen stören und die Messgenauigkeit verringern.
4. Druckmessumformer Füllstandmessung
Funktionsprinzip:
Druckmessumformer messen den Flüssigkeitsstand indirekt, indem sie den Druck messen, der von der Flüssigkeitssäule ausgeübt wird. Bei offenen Behältern entspricht der Druck am Boden des Behälters der Höhe der Flüssigkeitssäule. Bei druckbeaufschlagten Behältern werden Differenzdruckmessumformer eingesetzt, um den Innendruck zu kompensieren.
Vorteile:
Vielseitig: Geeignet für eine Vielzahl von Flüssigkeitstypen, einschließlich Schlämmen, und arbeitet effektiv in Hochdruck- und Hochtemperaturumgebungen.
Kostengünstig: Eine der kostengünstigsten Technologien zur Füllstandsmessung, ideal für Standardanwendungen.
Beschränkungen:
Schwankungen der Dichte: Druckmessumformer werden durch Änderungen der Flüssigkeitsdichte beeinflusst, was die Messgenauigkeit beeinträchtigen kann.
Nicht geeignet für korrosive oder viskose Flüssigkeiten: Unter Umständen sind spezielle Materialien oder Beschichtungen erforderlich, was den Wartungsaufwand erhöhen kann.
5. Kapazitive Füllstandstransmitter
Funktionsprinzip:
Kapazitive Füllstandssensoren messen die Änderungen der Kapazität, die durch das Vorhandensein von Flüssigkeit zwischen zwei leitenden Elektroden verursacht werden. Wenn sich der Füllstand der Flüssigkeit ändert, ändert sich auch die Kapazität, was eine genaue Füllstandsmessung ermöglicht.
Vorteile:
Ideal für kleine Tanks und Anwendungen mit geringem Volumen: Kapazitive Sensoren sind sehr effektiv bei der Messung des Füllstands in kleinen oder engen Behältern, wo andere Technologien möglicherweise nicht passen.
Berührungslos: Geeignet für saubere Flüssigkeiten, die keinen hohen Anteil an Partikeln oder Schaum aufweisen.
Beschränkungen:
Anfällig für Ablagerungen: Wenn die Flüssigkeit zähflüssig oder klebrig ist, können Ablagerungen auf dem Sensor die Genauigkeit beeinträchtigen.
Begrenzt auf bestimmte Medien: Am besten geeignet für nicht korrosive und saubere Flüssigkeiten; nicht ideal für stark turbulente oder schaumanfällige Substanzen
Schlussfolgerung:
In der Raffinerieindustrie ist eine genaue Füllstandmessung für die Aufrechterhaltung von Sicherheit, Effizienz und Produktqualität unerlässlich. Zwar bietet jede dieser fünf Technologien eindeutige Vorteile, doch die Wahl der richtigen Füllstandmesslösung hängt von der jeweiligen Anwendung, den Betriebsbedingungen und der Art der zu messenden Medien ab. Durch den Einsatz fortschrittlicher Technologien wie Radar-, Ultraschall-, Differenzdruck-, magnetostriktiver und kapazitiver Sensoren können Raffinerien zuverlässigere und präzisere Füllstandsmessungen gewährleisten, was zu einer besseren Betriebskontrolle und geringeren Wartungskosten führt.