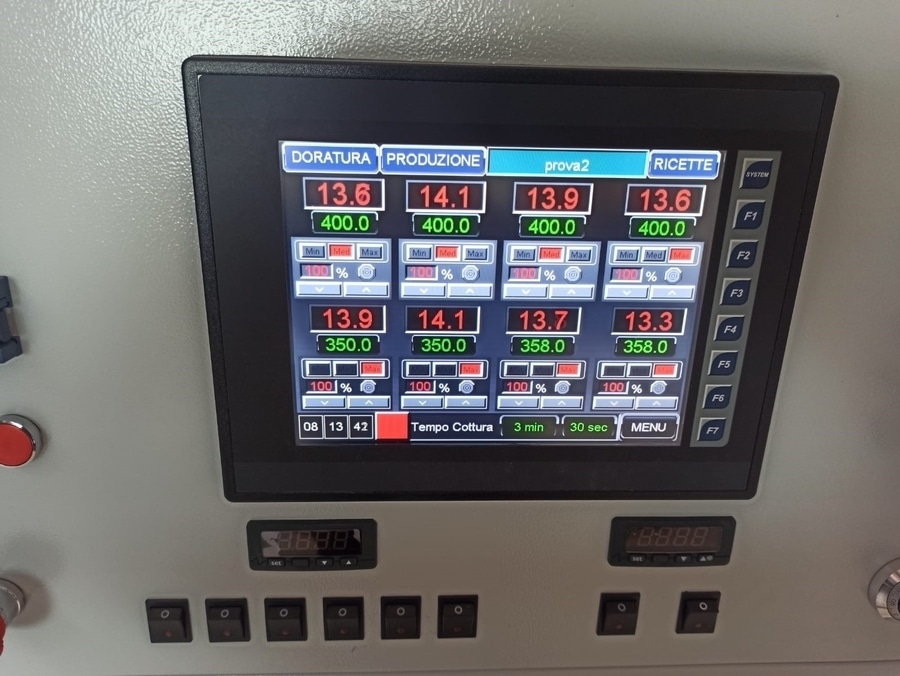
Automatische Übersetzung anzeigen
Dies ist eine automatisch generierte Übersetzung. Wenn Sie auf den englischen Originaltext zugreifen möchten, klicken Sie hier
#Neues aus der Industrie
Industrieller Pizza-Ofen mit Horner Automationstechnik
Dies war ein lohnendes, aber auch anspruchsvolles Projekt, dessen Umsetzung mehrere Monate dauerte. Ein Industrieofen wird in erster Linie zum Garen großer Mengen von Lebensmitteln benötigt, kann aber auch für kleinere Mengen von Lebensmitteln verwendet werden.
Einführung
Dieses Industrieofenprojekt fand in Massa, Italien, statt. Es war ein lohnendes, aber auch anspruchsvolles Projekt, dessen Umsetzung mehrere Monate dauerte. Ein Industrieofen wird in erster Linie zum Garen großer Mengen von Lebensmitteln in Chargen benötigt, kann aber auch für kleinere Mengen von Lebensmitteln verwendet werden. Dazu müssen Industrieöfen in der Lage sein, mehrere Temperaturen gleichzeitig mit verschiedenen Schaltern und Reglern zu steuern.
Projektziele
Eines der interessantesten Dinge an diesem Projekt war, dass es eine große Bandbreite an Zielen gab, die erreicht werden mussten, damit das Projekt als Erfolg angesehen werden konnte.
Das erste Ziel des Projekts bestand darin, die vorhandene Hardware an den Öfen zu aktualisieren. Die primäre Hardwareverbesserung bestand darin, die vorhandenen Temperaturregler an den Öfen zu ersetzen. Jede Ofengröße hat eine unterschiedliche Anzahl von Temperaturreglern, die ersetzt werden mussten.
Das zweite Projektziel war die Aktualisierung der vom Kunden verwendeten Software, um die Funktionalität und Flexibilität zu erhöhen. Dazu gehörte auch, dass der Benutzer ein Rezept speichern konnte. Dies würde bedeuten, dass ein bestimmter Satz von Einstellungen und Anweisungen gespeichert werden könnte und der Benutzer sie bei Bedarf wiederverwenden könnte, anstatt das Rezept bei jedem Gebrauch neu erstellen zu müssen.
Das primäre Geschäftsziel bestand darin, die Produktion mit dem verbesserten Ofen zu erhöhen und damit den Umsatz zu maximieren.
Herausforderungen
Die größte Herausforderung des Projekts bestand darin, die oben genannten Ziele zu erreichen und gleichzeitig die Branchenvorschriften einzuhalten. Die Vorschriften werden in jedem Fall vom Kunden festgelegt. Das liegt daran, dass jeder Kunde seine eigenen Bedürfnisse hat.
Horner weiß, wie wichtig es ist, flexibel zu sein, um seine Kunden zu bedienen. Die Einhaltung der Heizungsvorschriften ist ein Beispiel dafür. Horner kann flexibel sein, weil jedes Steuergerät über eine breite Palette von Funktionen verfügt.
Im Falle des OCS kann es die Temperatur an mehreren verschiedenen Stellen einer Maschine steuern. Der Techniker kann eine .csv-Datei für die Datenaufzeichnung erstellen. Diese Datei kann vom Kunden gelesen werden, und er kann sehen, wie die Temperatur im Ofen während des Erhitzungsprozesses kontrolliert wurde, und kann so seine eigene Produktion zertifizieren.
In diesem Fall sind die gespeicherten Daten die Temperatur. Über Modbus TCP-Protokolle kann der Kunde Echtzeitdaten für seine interne Datenbank abrufen. WebMI erleichtert die Kontrolle des Ofens durch die Kommunikation mit dem OCS und zeigt, ob der Bediener das Richtige tut. Wenn der Bediener nicht das Richtige tut, wird er überstimmt, ein anderes Rezept geladen und die Produktion weiter überwacht.
Technische Details der Implementierung
Dank Datalogging, Rezepten im .csv-Format, Modbus TCP und WebMI ist der Ofen Industrie 4.0-konform.
Scada-Kommunikation über Ethernet mit Modbus TCP-Protokoll ist für viele Kunden eine Anforderung. Modbus RTU wird für die Steuerung der IOs und der Frequenzumrichter verwendet. Dies ist wichtig, weil Scada ein Systemmanager ist, mit dem eine Anlage aus der Ferne überwacht werden kann, normalerweise über das Intranet. Das Modbus-TCP-Protokoll ist eines der in SCADA-Paketen verfügbaren Kommunikationsprotokolle. Modbus RTU dient in diesem Fall zur Steuerung der Oven Remote I/O und der Frequenzumrichter.
Im Rahmen des Projekts wurde eine breite Palette von Horner Automation-Steuerungen eingesetzt. Zum Beispiel die XL6, EXL6e, XL7e, EXL10e und SmartMods.
Der Wert von Horner in dieser Anwendung
Der Hauptgrund dafür, dass eine solche Auswahl an Steuerungen benötigt wurde, lag in den unterschiedlichen Bildschirmgrößen der Öfen. Die Steuerungen wurden auch wegen ihres breiten Spektrums an E/A eingesetzt. Die XL7e verfügt beispielsweise über zwei Ethernet-Anschlüsse, ebenso wie die EXL10e. Das bedeutet, dass die Steuerungen über HTTP- (Envision RV), FTP- (Envision FX) und WebMI-Funktionen verfügen.
Ein weiteres nützliches Merkmal der Steuerungen sind die Kommunikationsfunktionen. So verfügen EXL6e, XL7e und EXL10e über RS-232 und RS-485, RS-232/RS-485-Anschlüsse und SPS-/Antriebsprotokolle. Sie haben auch USB-Anschlüsse und RTU/Modbus/Master/Slave/Seriell ASCII In/Out.
Die Cscape-Programmierung zur Fertigstellung dieses Projekts war eine erweiterte Kontaktplanprogrammierung. Die andere Horner-Software, die während des Projekts verwendet wurde, war WebMI.
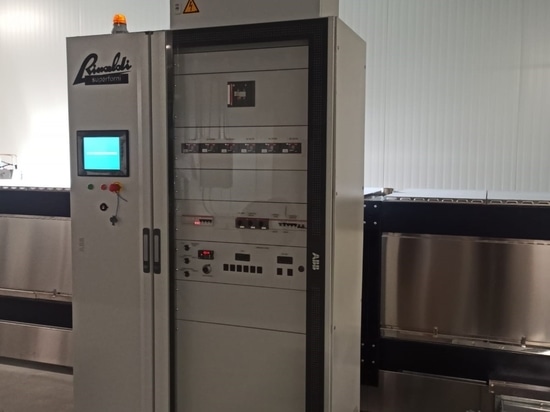
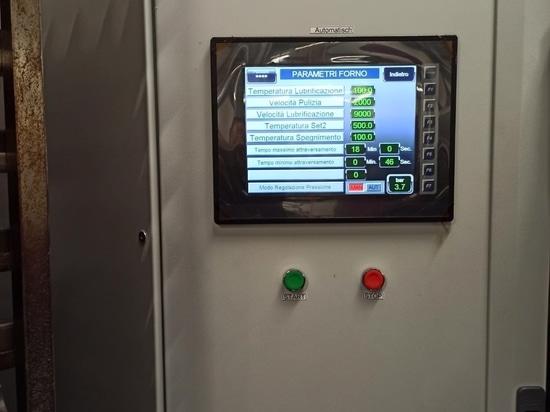
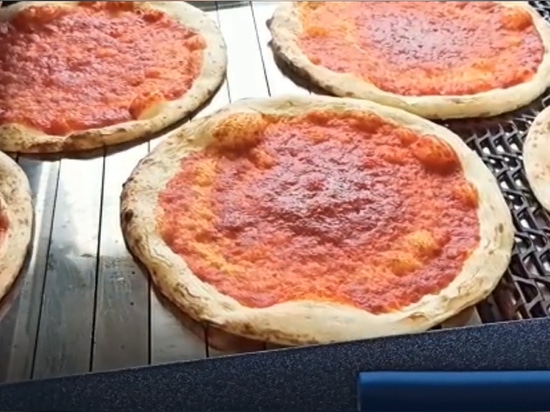
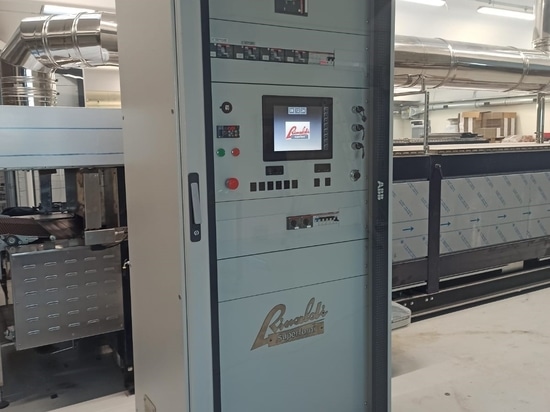