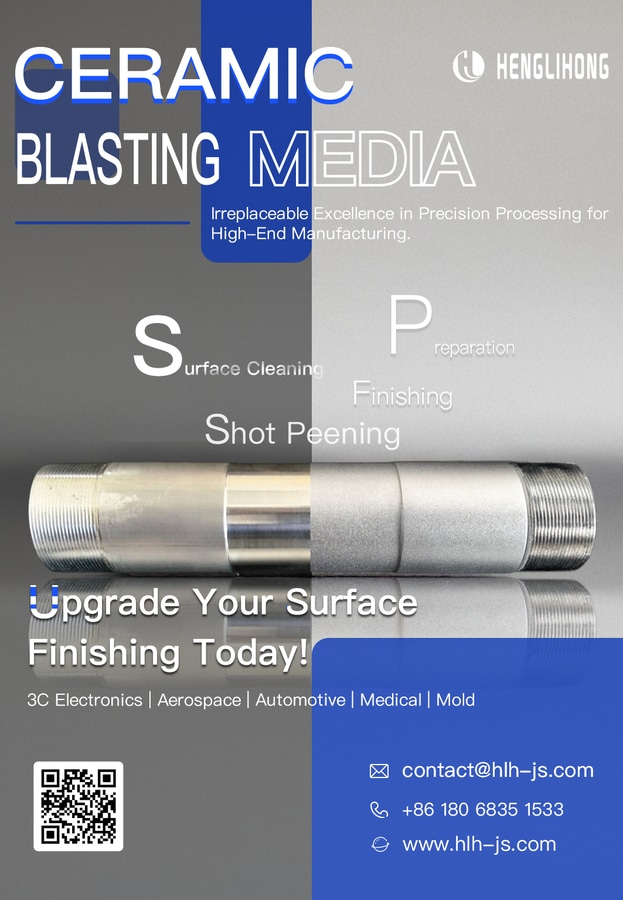
Automatische Übersetzung anzeigen
Dies ist eine automatisch generierte Übersetzung. Wenn Sie auf den englischen Originaltext zugreifen möchten, klicken Sie hier
#Neues aus der Industrie
Industrielle Anwendungen und Aussichten der keramischen Strahltechnik im Mikrometerbereich
Erkundung der Zukunft der Präzisionsoberflächenbehandlung in der Fertigung mit der Technologie des keramischen Perlstrahlens im Mikrometerbereich
Im Bereich der modernen Präzisionsfertigung spielt die Oberflächenbehandlungstechnologie eine entscheidende Rolle. Angesichts der steigenden Anforderungen an die Oberflächenqualität in Hightech-Branchen wie Elektronik, Luft- und Raumfahrt und Medizintechnik können herkömmliche Strahltechnologien die Bearbeitungsanforderungen im Mikrometerbereich nicht mehr erfüllen. Das keramische Strahlen im Mikrometerbereich, eine neue Methode der hochpräzisen Oberflächenbehandlung, wird allmählich zu einem unverzichtbaren Prozess in der Herstellung von Präzisionsteilen. In diesem Artikel werden die Grundsätze, Anwendungen und Entwicklungstrends dieser Technologie eingehend analysiert.
1. Technische Grundsätze
1.1 Materialeigenschaften von Keramikperlen im Mikronbereich
Keramikkugeln im Mikrometerbereich werden in erster Linie aus keramischen Materialien mit hoher Härte wie Zirkoniumoxid (ZrO₂), Aluminiumoxid (Al₂O₃) oder Siliziumkarbid (SiC) hergestellt, deren Durchmesser typischerweise zwischen 5 und 100 Mikrometern liegt. Diese Materialien weisen die folgenden Eigenschaften auf:
Ultrahohe Härte: Mohs-Härte von 8-9,5, die an die von Diamant heranreicht
Ausgezeichnete Sphärizität: Sphärizität von mehr als 98 %, wodurch gleichmäßige Kontaktflächen gewährleistet werden
Chemische Stabilität: Säure- und alkalibeständig, nicht reaktiv mit den meisten Metallen
Maßgenauigkeit: Gleichmäßige Partikelgrößenverteilung mit einer kontrollierten Standardabweichung von ±1μm
1.2 Arbeitsmechanik
Bei der Technologie des Keramikstrahlens im Mikronbereich wird ein Hochdruckluft- oder Flüssigkeitsstrom als Träger verwendet, um Keramikkugeln im Mikronbereich mit genau kontrollierten Geschwindigkeiten (20-120m/s) und Winkeln (15°-90°) auf die Werkstückoberfläche zu schleudern. Die mikroskopischen Aufpralleffekte, die durch den Aufprall der Keramikkugeln auf die Oberfläche entstehen, bewirken eine präzise Veränderung der Oberfläche:
Mikro-Schneiden: Die Kanten der Keramikkugeln führen Mikroschnitte an der Oberfläche durch und entfernen Oberflächenschichten im Nanometerbereich
Plastische Verformung: Aufprallkräfte erzeugen mikroskopisch kleine plastische Verformungen an der Materialoberfläche und erhöhen die Oberflächenhärte
Nanokompressive Spannung: Erzeugt ein Druckspannungsfeld in der Oberflächenschicht, das die Ermüdungsfestigkeit verbessert
Oberflächenaktivierung: Vergrößert die oberflächenaktiven Stellen und verbessert die spätere Beschichtungshaftung
2. ausrüstung und Prozessparameter
2.1 Hauptkomponenten der Ausrüstung
Moderne keramische Strahlsysteme im Mikronbereich umfassen in der Regel die folgenden Komponenten:
Hochpräzises Druckkontrollsystem: Druckschwankungen werden innerhalb von ±0,01 MPa kontrolliert
Vorrichtung zur Klassifizierung des Pulvers im Mikronbereich: Sorgt für gleichbleibende Partikelgröße
Digitales Düsensteuerungssystem: Präzise Steuerung von Projektionswinkel und -abstand
Optisches Echtzeit-Überwachungssystem: Überwacht die Verarbeitungseffekte und passt die Parameter in Echtzeit an
Umweltkontrolleinheit: Temperaturkontrolle bei 20±2℃, Luftfeuchtigkeit bei 45±5%
2.2 Wichtige Prozessparameter und Steuerung
Parameter, Regelbereich, Einflussfaktoren
Strahldruck: 0,1-0,8 MPa, Oberflächenrauhigkeit, Bearbeitungseffizienz
Perlendurchmesser: 5-100μm, Oberflächenmorphologie, Mikrostruktur
Projektionswinkel: 15°-90°, Richtung der Aufprallkraft, Materialabtragsrate
Projektionsabstand: 10-100mm, Energieverteilung, Behandlungsgleichmäßigkeit
Bearbeitungszeit: 5-300s, Oberflächenintegrität, Bearbeitungstiefe
Perlenflussdichte: 2-20g/min-cm², Bearbeitungseffizienz, Oberflächenqualität
Die präzise Steuerung dieser Parameter ist entscheidend für die Erzielung idealer Oberflächeneffekte. Moderne Systeme verwenden in der Regel KI-Algorithmen zur Unterstützung der Parameteroptimierung, die automatisch optimale Parameterkombinationen auf der Grundlage von Materialeigenschaften und Verarbeitungsanforderungen erzeugen.
3. Anwendungsbereiche
3.1 Halbleiter- und Mikroelektronikindustrie
Präzise Leadframe-Verarbeitung: Erhöht die Haftfestigkeit um 30-50%
Reinigung von mikroelektromechanischen Systemen (MEMS): Entfernt mikroskopisch kleine Verunreinigungen und verbessert die Ausbeute um bis zu 15 %
Behandlung von Substraten für integrierte Schaltungen: Verbessert die Oberflächenbenetzbarkeit und damit die Zuverlässigkeit des Lötens
3.2 Luft- und Raumfahrtbereich
Verstärkung von Gasturbinenschaufeln: Erhöht die Lebensdauer der Schaufeln um bis zu 40%
Präzise Behandlung von Hydraulikkomponenten: Verringert den Reibungskoeffizienten und verlängert die Nutzungsdauer
Oberflächenbehandlung von Befestigungselementen für die Luft- und Raumfahrt: Verbessert die Wasserstoffversprödung und die Korrosionsbeständigkeit
3.3 Medizinische Geräte
Modifizierung der Implantatoberfläche: Verbessert die Osseointegration, verbessert die Biokompatibilität
Behandlung von Zahnimplantaten: Schaffung von Mikrostrukturen, die das Gewebewachstum fördern
Präzisionskomponenten für medizinische Geräte: Beseitigung von Mikrograten, Verbesserung der Sicherheit
4. technische Vorteile und Beschränkungen
4.1 Vorteile gegenüber herkömmlichen Sprengtechnologien
Verbesserte Bearbeitungspräzision: Oberflächenmodifikation im Nanometerbereich mit kontrollierbaren Ra-Werten von 0,05-1,2 μm möglich
Integrität der Oberfläche: Erzeugt praktisch keine Mikrorisse oder Spannungskonzentrationen
Reproduzierbarkeit: Konsistenz von Charge zu Charge von über 95
Umweltfreundlichkeit: Keramische Materialien können recycelt werden, wodurch weniger Abfall entsteht
Präzise Bereichskontrolle: Selektive Flächenbehandlung im Mikrometerbereich möglich
4.2 Technische Beschränkungen und Herausforderungen
Investitionskosten für die Ausrüstung: Professionelle Ausrüstung erfordert normalerweise eine Investition von 500.000-2.000.000 Yuan
Enges Prozessfenster: Hohe Anforderungen an die Parameterkontrolle, schwieriger Betrieb
Probleme mit der Anpassungsfähigkeit an bestimmte Materialien: Wie z. B. ultraweiche Materialien oder bestimmte Verbundwerkstoffe
Produktionseffizienz: Kleinere behandelte Fläche pro Zeiteinheit im Vergleich zu traditionellen Methoden
5. Neueste Trends in der Technologieentwicklung
5.1 Intelligenz und digitale Zwillinge
KI-gestützte Parameteroptimierung: Reduziert die Zeit für Versuche und Fehler um bis zu 85 %
Digitale Zwillingstechnologie: Simulation des Strahlprozesses in Echtzeit, Vorhersage der Oberflächenqualität
Adaptive Steuerungssysteme: Automatische Anpassung der Prozessparameter auf der Grundlage von Echtzeit-Feedback
5.2 Neue keramische Werkstoffe
Keramik-Mikroperlen mit Kern-Schale-Struktur: Kombination von hoher Härte und Zähigkeit
Nanokomposit-Keramik: Verbesserung der Verschleißfestigkeit und der chemischen Stabilität
Funktionalisierte Keramikkugeln: Oberflächenmodifikation mit spezifischen funktionellen Gruppen, um eine chemische Aktivierung zu erreichen
5.3 Integration von Verbundwerkstoffprozessen
Elektrochemisch gestütztes Mikrostrahlen: Kombination elektrochemischer Effekte zur Verbesserung der Abtragseffizienz
Laserunterstütztes keramisches Strahlen: Verbesserung der Bearbeitungsgenauigkeit durch Laservorbehandlung
Ultraschall-unterstützte Technologie: Verbesserung der Aufprallwirkung von Mikrokugeln bei gleichzeitiger Reduzierung des Projektionsdrucks
6. Fallstudie: Aero-Engine Blade Behandlung
Ein Hersteller von Flugzeugtriebwerken setzte Keramikkugeln im Mikrometerbereich (ZrO₂, 20±2μm) zur Behandlung von Turbinenschaufeln aus Hochtemperaturlegierungen ein und erzielte damit die folgenden bedeutenden Ergebnisse:
Die Oberflächenrauhigkeit wurde von Ra 1,8μm auf Ra 0,4μm optimiert
Die Oberflächenhärte wurde um 42 % erhöht, von HV320 auf HV455
Die Schichttiefe der Oberflächendruckspannung erreichte 25 μm, was die Ermüdungslebensdauer um 35 % erhöhte
Die Haftung der Wärmedämmschicht wurde um 50 % verbessert und die Lebensdauer um 2.000 Stunden verlängert
Die Produktionseffizienz wurde um 20 % gesteigert und die Nachbearbeitungsrate um 75 % gesenkt
Dieser Fall bestätigt die überlegene Leistung der Keramikstrahltechnologie im Mikrometerbereich bei der Oberflächenbehandlung hochwertiger Präzisionsteile.
7. Leitfaden zur Prozessimplementierung und Qualitätskontrolle
7.1 Arbeitsablauf der Prozessimplementierung< strong>
Vorbehandlung: Ultraschallreinigung zur Entfernung von Öl und Feinstaub
Auslegung der Parameter: Festlegung der Anfangsparameter auf der Grundlage der Materialeigenschaften und -anforderungen
Validierung der Proben: Kleinserienprüfung und Oberflächenanalyse
Formale Bearbeitung: Kontrolle der Umgebungsbedingungen, Durchführung von Strahlvorgängen
Qualitätsprüfung: Oberflächenrauhigkeit, Morphologie und Leistungstests
Nachbehandlung: Neutralisieren der Oberfläche, Entfernen von keramischen Restpartikeln
7.2 Qualitätskontrolle und Prüfverfahren
Prüfgegenstand, Prüfmittel, Kontrollstandard
Oberflächenrauhigkeit: Laser Konfokal / Mikroskop, Ra ±0,05μm
Morphologie der Oberfläche: Feldemissions-SEM, keine Mikrorisse, gleichmäßige Partikelverteilung
Druckspannungsschicht: Röntgenspannungsanalysator, Spannungswert -300±30MPa
Oberflächenhärte: Nanoindentationstester, Härteabweichung <5%
Oberflächenaktivität: Kontaktwinkelmesser, Kontaktwinkelverringerung >40%
Schlussfolgerung
Als modernes Verfahren für die Oberflächenbehandlung von Präzisionsteilen überwindet die Keramikstrahltechnik im Mikrometerbereich weiterhin die Grenzen der herkömmlichen Verfahren und bietet der High-Tech-Industrie eine leistungsstarke technische Unterstützung. Ihre Anwendungen in der Luft- und Raumfahrt, der Medizintechnik, der Halbleiterindustrie und anderen Bereichen haben den technologischen Fortschritt in diesen Branchen stark gefördert. Mit der Entwicklung intelligenter Fertigungs- und neuer Werkstofftechnologien wird die keramische Perlstrahltechnik im Mikrometerbereich fortschrittliche Konzepte wie künstliche Intelligenz und digitale Zwillinge integrieren, um eine höhere Präzision und effizientere Oberflächenbehandlung zu erreichen, was neue Entwicklungsmöglichkeiten für die Präzisionsfertigung eröffnet.
Bei der Einführung dieser Technologie müssen die Unternehmen die Investitionskosten, die technischen Anforderungen und die Anwendungsszenarien umfassend berücksichtigen, um angemessene Implementierungsstrategien zu formulieren und das Potenzial der Technologie zur Verbesserung der Produktqualität und zur Kostenoptimierung voll auszuschöpfen.
Stichworte: #MicronCeramicBeads #BlastingTechnology #SurfaceTreatment #PrecisionManufacturing #Aerospace #MedicalDevices