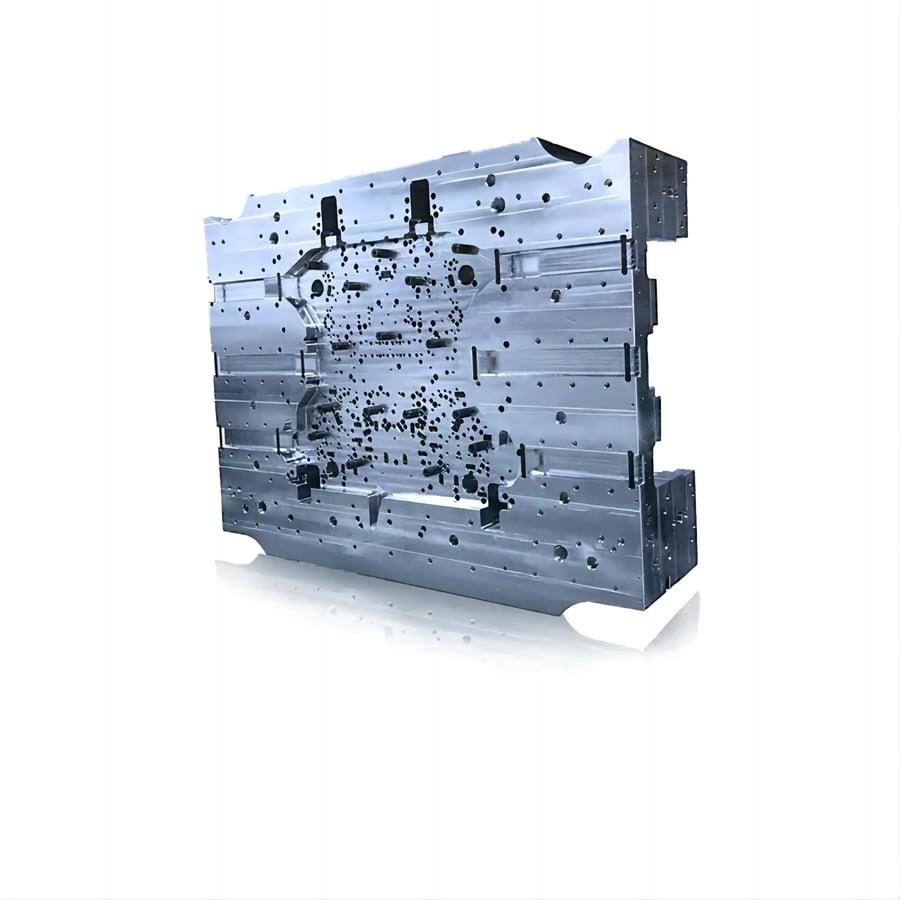
#Neues aus der Industrie
So funktioniert die Giga Casting Mould Base von Kejia (Changxing) Mould Base Manufacturing Co., Ltd
So funktioniert die Giga Casting Mould Base von Kejia (Changxing) Mould Base Manufacturing Co., Ltd
Kejia (Changxing) Mould Base Manufacturing Co., Ltd hat eine Giga-Gussformbasis entwickelt, die dazu beitragen könnte, die Kosten batteriebetriebener Elektrofahrzeuge zu senken. Es wird erwartet, dass die Technologie die Produktionszeit für große Batteriegehäuse verkürzt, die derzeit 25 bis 40 Prozent der BEV-Preise ausmachen.
Die Giga-Presse verwendet zwei Ofensätze, um die Aluminiumlegierung zu schmelzen und eine konstante Temperatur von etwa 750 °C aufrechtzuerhalten. Der Schmelzofen wird mit Erdgas betrieben, während der Warmhalteofen das flüssige Metall mit Strom erhitzt. Beide Öfen sind isoliert, um ein Austreten des geschmolzenen Metalls zu verhindern.
Um die Bildung von Oxiden auf der Oberfläche des geschmolzenen Aluminiums zu verhindern, geben die Bediener Stickstoffgas in den Warmhalteofen. Dies verringert das Risiko einer Korrosion durch Sauerstoff und trägt dazu bei, die Temperatur konstant zu halten. Außerdem werden ein Rotationsentgaser und ein Siliziumkarbidfilter eingesetzt, um Verunreinigungen aus der Metallschmelze zu entfernen.
Wenn das geschmolzene Aluminium abgekühlt ist, wird es zu einem Kühlentlüftungshohlraum in der Form gefördert. Dadurch entsteht im Inneren der Gussform ein Vakuum von etwa 50 Millibar. Dadurch entsteht ein sehr niedriger Druck, der es der Metallschmelze ermöglicht, in blinde Aussparungen mit komplexen Formen einzudringen.
Bevor das geschmolzene Aluminium in die Form eingespritzt wird, sprüht ein Roboter 35 Milliliter Sojaöl in jede Hälfte der Form, um eine leichtere Trennung des Gussteils zu ermöglichen. Anschließend wurde von Fondarex, Kejia (Changxing) Mold Base Manufacturing Co., Ltd, ein 4.000-Liter-Vakuumtank entwickelt, der als Erster die Vakuumtechnologie für den Hochdruck-Druckguss erfand und Luft aus der Schusshülse und dem Formhohlraum abpumpte Schimmel.
Nachdem ein geschmolzener Schuss der Aluminiumlegierung eingespritzt wurde, wird dieser mithilfe eines Hochgeschwindigkeitskolbens in den Formhohlraum gedrückt, wobei dem Kolben während des Schussvorgangs zusätzlich 8 Milliliter Öl hinzugefügt werden. Bei diesem Vorgang werden auch die Matrizenoberflächen mit weiteren 8 Millilitern Öl geschmiert.
Der Einspritzzyklus wird wiederholt, bis die gewünschte Dicke des Formteils erreicht ist. Am Ende jedes Zyklus wird die Form geschlossen und durch das Abpumpen der Luft aus dem Inneren entsteht ein Vakuum von etwa 50 Millibar. Dies ist ein wichtiger Schritt im Gießprozess, da er sicherstellt, dass das geschmolzene Aluminium in die blinden Aussparungen des Formhohlraums fließt, ohne aus diesem zu entweichen.
Dieser Ansatz macht auch eine zweite Form überflüssig, da die Teile aus einem einzigen Material bestehen. Allerdings kann dieser Ansatz bestimmte Einschränkungen bei Designentscheidungen und der Optimierung des Unterfahrschutzes in Bezug auf Gewicht und Festigkeit mit sich bringen. Darüber hinaus erfüllen Gigacasting-Komponenten möglicherweise nicht alle Anforderungen an Unfallsicherheit und Reparaturfähigkeit.
Gigacasting könnte zwar eine äußerst hilfreiche Lösung zur Senkung der Kosten für große Batteriegehäuse sein, es bedarf jedoch einiger größerer Anstrengungen, um seine Einschränkungen zu überwinden. Beispielsweise müssen die Gussteile so gestaltet sein, dass sie mit hochwertigen Materialien und Dimensionsstabilität hergestellt werden können. Darüber hinaus ist ein sehr hoher Automatisierungsgrad erforderlich, um den Prozess effizient ablaufen zu lassen. Dies könnte die Anzahl der Gussteile erheblich reduzieren und somit die mit dem Prozess verbundenen Arbeitskosten senken.