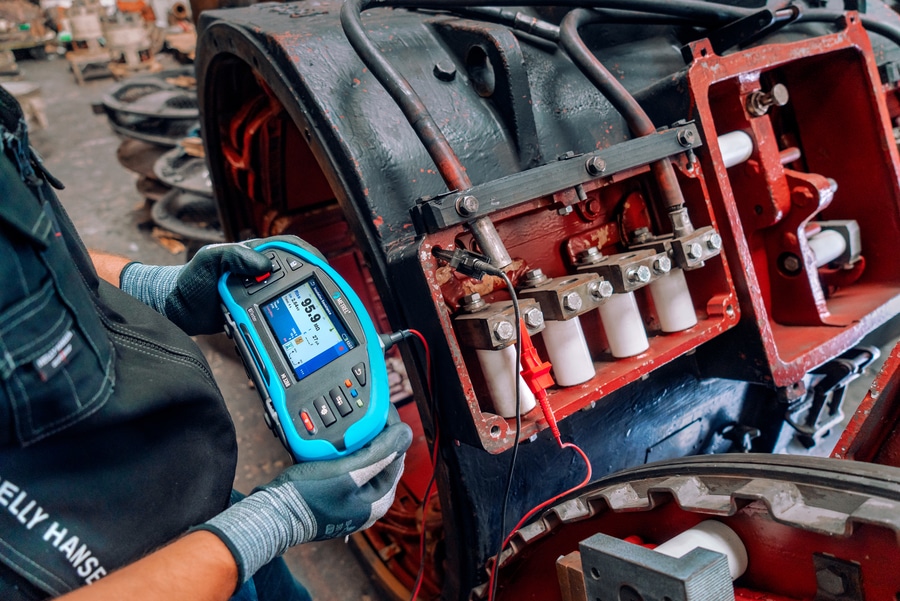
Automatische Übersetzung anzeigen
Dies ist eine automatisch generierte Übersetzung. Wenn Sie auf den englischen Originaltext zugreifen möchten, klicken Sie hier
#White Papers
Prüfung des Ständers eines Generators
MI 3288 Erdungsisolationstester
Die heutigen Isoliermaterialien für elektrische Leitungen haben sich seit den Tagen der Seide und Guttapercha (Naturlatex), die paradoxerweise feucht gehalten werden mussten, damit sie an der Leitung hafteten und nicht abfielen, weit entwickelt. Sie haben unvergleichlich bessere dielektrische Eigenschaften, sind billiger und haltbarer und können in jeder beliebigen Form hergestellt werden. Dennoch sind sie nicht immun gegen Einflüsse wie hohe und (sehr) niedrige Temperaturen, UV-Strahlung, Überspannung, Feuchtigkeit und mechanische Kräfte.
Angesichts der schwerwiegenden Folgen eines Materialversagens ist die Isolationsanalyse eine der grundlegenden Methoden zur Beurteilung der ordnungsgemäßen Funktion praktisch aller elektrischen Maschinen, Geräte, Anlagen oder Systeme. Die Anforderungen, Richtlinien und Normen unterscheiden sich jedoch stark voneinander. Generatoren und andere (große) rotierende elektrische Maschinen sind eindeutige Beispiele, da die Isolierung hier größeren Belastungen ausgesetzt ist als in anderen Anwendungen, insbesondere hohen Temperaturen und mechanischen Kräften. Dennoch ist sie anfällig für auf den ersten Blick banale Elemente wie Feuchtigkeit, die unter den richtigen Bedingungen verheerende Auswirkungen haben und die Maschine irreparabel beschädigen können.
Feuchtigkeit, Temperatur und Isolierung
Unabhängig vom verwendeten Isoliermaterial besteht die Hauptwirkung von Feuchtigkeit (neben der physikalischen Zersetzung des Materials durch verschiedene chemische Prozesse) in der Entstehung leitfähiger Kriechstrecken, die zu einer stark verminderten Durchschlagsfestigkeit und folglich zu einer erhöhten Wahrscheinlichkeit von (dielektrischen) Durchschlägen führen. Bei Generatoren kann Luftfeuchtigkeit durch Kühlöffnungen oder durch unauffällige Risse in das Innere der Maschine gezogen werden, wenn diese über ein spezielles, geschlossenes Kühlsystem (flüssigkeitsgekühlt) verfügt.
Temperaturschwankungen im Inneren der Maschine führen dazu, dass die Feuchtigkeit in flüssiger Form kondensiert und in die Isolierung der Wicklungen eindringt. Wenn es keine Möglichkeit gibt, die Wicklungen zu trocknen, oder niemand die Qualität der Isolierung überprüft hat, kann die Maschine eine sehr kurze Lebensdauer haben. Feuchtigkeit kann aber auch in die Maschine eindringen, wenn sie nicht in Betrieb ist, d. h. bei unsachgemäßer Lagerung, Sonneneinstrahlung und anderen schädlichen Umwelteinflüssen. Eine solche Maschine muss vor der Inbetriebnahme gründlich geprüft werden, und genau das musste ein Metrel angeschlossener Prüfer für elektrische Sicherheit bei einem 100-kW-Generator tun, bei dem der Verdacht bestand, dass er aufgrund der Lagerbedingungen mit Feuchtigkeit behaftet war.
Aus dem Lager, aber noch nicht in Betrieb
Ein 100-kW-Generator (3-phasig, 50 Hz, 400 V / 195 A, 1000 U/min) war etwa 10 Jahre lang in einem Kleinstwasserkraftwerk (Francis-Turbine) im Einsatz, bis die Anlage aufgrund von Problemen mit dem Wasserdurchfluss abgebaut wurde. Der Generator wurde dann in einer ziemlich baufälligen Lagerhalle gelagert, nicht weit vom ehemaligen Kraftwerk entfernt, aber in der Nähe eines kleinen Teiches, zusammen mit einigen anderen elektrischen Maschinen, darunter mehrere große Elektromotoren. Bei letzteren wurde festgestellt, dass sowohl der Stator (Anker) als auch der Rotor schlecht isoliert waren und repariert werden mussten, und es wurde vermutet, dass der Generator, der in ein neues (Wasserkraft-)Kraftwerk eingebaut werden sollte, ähnliche Probleme aufweisen könnte.
PI-, DAR- und DD-Tests
Der Generator wurde zu einer Reparaturwerkstatt eines Transformatorenherstellers transportiert. Starke elektromagnetische Störungen, wie sie in dieser und ähnlichen Umgebungen vorkommen, können beim Prüfen/Messen problematisch sein, aber das vom Inspektor verwendete Erdungsisolationsprüfgerät MI 3288 verfügt über abgeschirmte Messleitungen, die dieses Problem erheblich entschärfen. Darüber hinaus verfügt das Gerät über geschützte Eingangsklemmen und die Messleitungen sind mit entsprechenden Anschlusskabeln ausgestattet - so werden potenzielle Leckströme vermieden, die durch Oberflächenverschmutzung und Feuchtigkeit entstehen und die Genauigkeit der Messung beeinträchtigen können.
Bevor man sich jedoch auf eine Isolationswiderstandsmessung/-analyse einlässt, sollte man sich Gedanken über den gewünschten Mindestwiderstand für die jeweilige Maschine/das jeweilige System machen. Eine gute Faustregel ist ein Widerstand von mindestens 1 MΩ für jede kV. Allerdings gilt diese Zahl (1 MΩ) nur bei Raumtemperatur (20 °C). Bei höheren Temperaturen steigen die Anforderungen sehr schnell an - pro 10 °C erhöht sich der Widerstandsbedarf um mehr als 50 % (rotierende Maschinen der Klasse B). Bei 40 °C sollte der Widerstand z. B. mindestens 2,5 MΩ für jede (Nenn-)kV betragen.
Der Zusammenhang zwischen Feuchtigkeit und Widerstandsänderungen ist nicht so einfach und variiert stark bei den verschiedenen Isoliermaterialien, aber man kann dennoch ohne weiteres sagen, dass jede Feuchtigkeit den Isolierwiderstand verringert. Jedenfalls schloss der Prüfer die Rotor- und Statorwicklungen des Generators an das Erdungsisolationsprüfgerät MI 3288 an und führte jeweils drei separate Messungen durch: Zeitanstiegsmethode/Polarisationsindex (PI), dielektrisches Absorptionsverhältnis (DAR) und dielektrische Entladungsprüfung. Von diesen drei Verfahren ist der Test der dielektrischen Entladung (DD) die beste Wahl zur Beurteilung von Feuchtigkeitsschäden an der Isolierung.
Das geprüfte Objekt wird über einen längeren Zeitraum, in der Regel zwischen 10 und 30 Minuten, unter Hochspannung gehalten. Dann wird die Spannung abgeschaltet und der Entladungsstrom gemessen. Die gemessenen (Entladungs-)Ströme des Generators waren, wie ursprünglich vorhergesagt, sehr hoch, ebenso wie (offensichtlich) das DD-Ergebnis, das über 5 lag (ein guter Wert liegt im Allgemeinen unter 2).
Der Generator wurde daraufhin überholt; der Rotor wurde ausgebaut und gründlich gereinigt, ebenso der Stator. Beide wurden visuell auf Schäden überprüft und in einem beheizten Raum mit kontrollierter Atmosphäre gelagert, um vollständig auszutrocknen. Nach dem Zusammenbau wurde der Generator erneut mit dem Erdungsisolationstester MI 3288 geprüft und schnitt mit Bravour ab - die Isolierung wurde für gut befunden, und der Generator wurde in dem neuen Kraftwerk in Betrieb genommen.