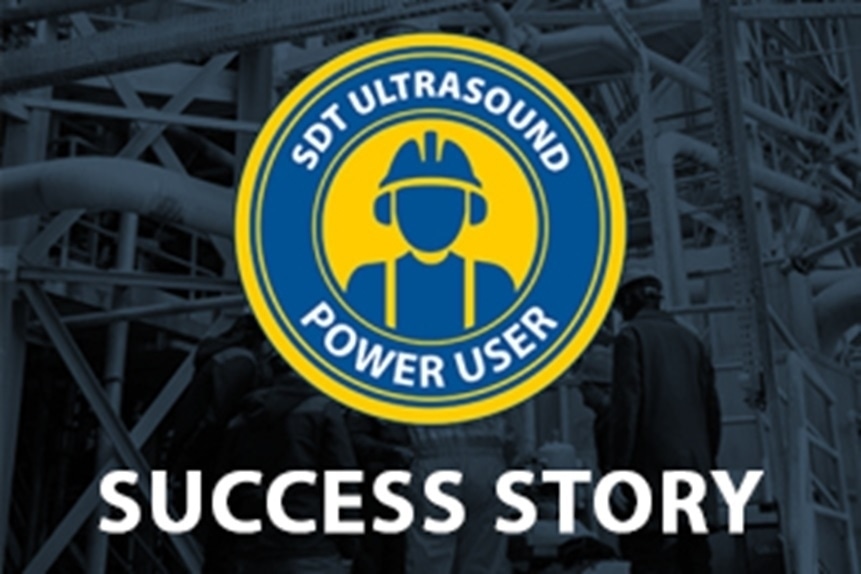
Automatische Übersetzung anzeigen
Dies ist eine automatisch generierte Übersetzung. Wenn Sie auf den englischen Originaltext zugreifen möchten, klicken Sie hier
#Neues aus der Industrie
Veränderung der Lagerzuverlässigkeit in einer griechischen Papierfabrik
In einer Papierfabrik in Griechenland verursachten häufige Lagerausfälle erhebliche Störungen, die zu unerwarteten Ausfallzeiten, erhöhten Wartungskosten und sinkender Produktionseffizienz führten.
Trotz mehrerer Versuche, das Problem zu beheben, einschließlich der Beratung durch externe Dienstleister, blieb das Problem bestehen. Erst als das Wartungsteam einen neuen Ansatz mit Hilfe von Ultraschalltechnologie wählte, konnte das Problem gelöst werden, was zu bemerkenswerten Verbesserungen im Betrieb führte.
Die Herausforderung: Ungeklärte Lagerausfälle
Die Wartungsabteilung der Papierfabrik kämpfte mit einem rätselhaften Problem. Lager, die eigentlich viel länger halten sollten, fielen nach nur einem Monat Betrieb aus. Dieser häufige Austausch verursachte nicht nur hohe Material- und Arbeitskosten, sondern auch beträchtliche Ausfallzeiten, die die Produktion unterbrachen und das Endergebnis des Unternehmens gefährdeten.
Zunächst vermutete das Team, dass die Art der verwendeten Lager das Problem sein könnte. Sie folgten dem Rat externer Dienstleister und wechselten zu Lagern mit geringerer Lagerluft. Diese Änderung löste das Problem jedoch nicht. Da die Ausfälle weiterhin in gleichem Maße auftraten, wurde klar, dass die Ursache woanders lag.
Die Entdeckung: Überschmierung als Übeltäter identifiziert
Der Durchbruch kam nach einer Präsentation von REA Hellas, die dem Wartungsteam das Potenzial der Ultraschalltechnologie zur Überwachung der Schmierung und des Zustands der Lager vorstellte. Die Papierfabrik war neugierig und beschloss, in ein Ultraschallgerät namens LUBEChecker zu investieren, und lud REA Hellas ein, eine Vor-Ort-Bewertung ihrer Schmierungspraktiken durchzuführen.
Die Bewertung ergab ein kritisches Problem: Alle Lager wurden überschmiert, was zu vorzeitigen Ausfällen führte. Diese Entdeckung war ein Wendepunkt. Das Team hatte nun einen klaren Weg vor sich: Durch eine Optimierung der Schmierung mittels präziser Überwachung konnte es die Lebensdauer seiner Lager erheblich verlängern und die damit verbundenen Kosten senken.
Strategische Umsetzung: Ein neuer Ansatz für die Instandhaltung
Mit diesem neu gewonnenen Wissen setzte das Wartungsteam einen strategischeren Ansatz für seine Arbeit um. Sie erkannten, dass die Lagerausfälle auf einen zeitbasierten Ausfallmodus zurückzuführen waren, der direkt mit Überschmierung zusammenhing. Durch die Behebung dieses spezifischen Problems konnten sie nicht nur die Lebensdauer der Lager erhöhen, sondern auch den Fettverbrauch und die damit verbundenen Kosten senken.
Der Einsatz von Ultraschalltechnologie wurde zum zentralen Bestandteil der Wartungsstrategie. Durch die kontinuierliche Überwachung des Lagerzustands und die entsprechende Anpassung der Schmierverfahren konnten sie Überschmierung und die dadurch verursachten vorzeitigen Ausfälle verhindern. Dieser proaktive Ansatz bedeutete eine deutliche Abkehr von den früheren reaktiven Wartungspraktiken.
Ausweitung der Wirkung: Über Lager hinaus
Ermutigt durch den Erfolg bei der Lösung des Lagerproblems beschloss das Wartungsteam, die Möglichkeit einer Ausweitung des Einsatzes der Ultraschalltechnologie auf andere Bereiche des Werks zu prüfen. Sie erwägten die Anschaffung fortschrittlicherer Ultraschallgeräte, wie z. B. des SDT340, das für eine breite Palette von Anwendungen eingesetzt werden kann, darunter elektrische Inspektionen, Ventil- und Kondensatableiterüberwachung und Gaslecksuche.
Um die Vorteile dieser Geräte voll ausschöpfen zu können, war dem Team klar, dass ständiges Lernen und die Entwicklung von Fähigkeiten unerlässlich waren. Ziel war es, ein umfassendes internes Überwachungsnetzwerk aufzubauen, mit dem Daten zu verschiedenen Aspekten des Anlagenbetriebs gesammelt und analysiert werden können. Dieser datengesteuerte Ansatz würde es ihnen ermöglichen, Wartungsmaßnahmen nur dann zu ergreifen, wenn sie notwendig sind, was die Effizienz weiter steigern und unnötige Kosten reduzieren würde.
Überwindung von Herausforderungen: Unterstützung durch das Management
Während die technischen Vorteile der Ultraschalltechnologie dem Instandhaltungsteam klar sind, bleibt es eine Herausforderung, die Zustimmung des Managements für weitere Investitionen in diese Instrumente und Verfahren zu erhalten. Um die potenziellen Vorteile zu demonstrieren, sollte der Leiter der Überwachungsabteilung eine Testphase vorschlagen. Durch die Einrichtung eines Rahmens für die Überwachung und den Vergleich der Ergebnisse nach sechs Monaten könnten sie ein überzeugendes Argument für weitere Investitionen liefern.
Das Team ist sich bewusst, wie wichtig es ist, technische Verbesserungen in finanzielle Kennzahlen zu übersetzen, die bei der Geschäftsleitung Anklang finden würden. Das Team plant, regelmäßig über die erzielten Kosteneinsparungen und Effizienzsteigerungen zu berichten und zu zeigen, wie der neue Ansatz direkt zur Rentabilität des Unternehmens beitragen kann. Die endgültige Entscheidung der Geschäftsleitung steht jedoch noch aus.
Das mögliche Ergebnis: Eine nachhaltige Veränderung der Zuverlässigkeit
Bei vollständiger Umsetzung könnte die Einführung der Ultraschalltechnologie zu einer tiefgreifenden Veränderung der Betriebsabläufe in der Papierfabrik führen. Durch die Reduzierung von Lagerausfällen würde die Fabrik weniger Ausfallzeiten, geringere Wartungskosten und eine verbesserte Produktionseffizienz verzeichnen. Der potenzielle Erfolg dieser Initiative könnte auch eine Kultur der proaktiven Wartung und kontinuierlichen Verbesserung innerhalb des Unternehmens fördern.
Der Weg der Papierfabrik von häufigen Lagerausfällen zu einem potenziell zuverlässigen und effizienten Betrieb ist ein Beweis für die Kraft innovativen Denkens und der richtigen Werkzeuge. Indem sie die Ursache ihres Problems angehen und einen strategischen, datengesteuerten Ansatz für die Instandhaltung in Betracht ziehen, haben sie die Möglichkeit, Ergebnisse zu erzielen, die ihr Unternehmen verändern könnten. Der Erfolg liegt nicht nur in der Lösung eines technischen Problems, sondern in der Schaffung einer nachhaltigen, langfristigen Verbesserung der Betriebsabläufe - vorausgesetzt, das Management gibt grünes Licht.