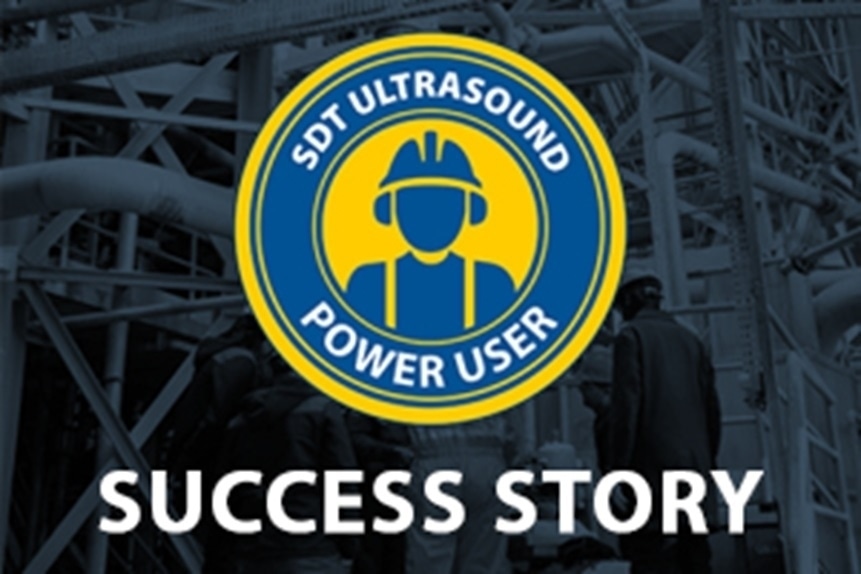
Automatische Übersetzung anzeigen
Dies ist eine automatisch generierte Übersetzung. Wenn Sie auf den englischen Originaltext zugreifen möchten, klicken Sie hier
#Neues aus der Industrie
Frühzeitige Erkennung von Lagerfehlern und Zustandsüberwachung in einer Produktionslinie für Babywindeln
In diesem Projekt wird die frühzeitige Erkennung von Lagerfehlern an zwei Motoren in einer Produktionslinie für Babywindeln mit Hilfe des SDT340-Ultraschallgeräts durchgeführt.
Ziel ist es, durch die frühzeitige Erkennung von Lagerfehlern eine planmäßige Wartung zu gewährleisten, Stillstandszeiten in der Produktionslinie zu vermeiden und die Wartungskosten zu senken. Der Zustand der Lager wird auf der Grundlage der erfassten Messungen und grafischen Daten analysiert.
1. Projektumfang
Überprüfte Ausrüstung:
Motor 1: Der Motor befindet sich in der Produktionslinie für Babywindeln.
Motor 2: Der Motor befindet sich zusammen mit seinem Gebläse in der Produktionslinie.
Verwendete Technologie: SDT340-Ultraschallgerät
Das SDT340-Gerät wird zur Früherkennung von Lagerfehlern und zur Überwachung des Schmierzustandes eingesetzt. Im Vergleich zur Schwingungsanalyse liefert es wesentlich empfindlichere Ergebnisse und ermöglicht die Verfolgung der Fehlerentwicklung.
2. Messverfahren und Datenerfassung
Messzeitraum: Die Lager werden monatlich mit dem SDT340-Ultraschallgerät gemessen. Die Ergebnisse werden jedes Mal analysiert, und Trendänderungen werden überwacht.
Erfasste Daten: Grafische Daten des Ultraschallspektrums und RMS-Geschwindigkeits-/Beschleunigungswerte der Lager. Anhand dieser Daten lässt sich das Stadium des Lagerschadens bestimmen.
3. Überprüfung und Interpretation der Diagramme
Während des Bewertungsprozesses werden die folgenden Schritte auf der Grundlage der Messdiagramme für jeden Motor durchgeführt:
Motor 1:
Messorte: Die Messungen an der Nicht-Antriebsseite von Motor 1 wurden untersucht.
Diagramme:
Auswertung: Bei den Messungen an den Motorlagern wurden keine nennenswerten Probleme festgestellt, aber das Spektrum des Lagers an der Seite der Lüfterscheibe, gemessen bei 78 Grad, zeigt dominante 1x- und 2x-Signale, was auf ein mögliches Ausrichtungsproblem hinweist. Eine Überprüfung der Riemenspannung, der Ausrichtung und der Lagerachsen wäre von Vorteil.
Motor 2 (Lüfter NDE):
Messorte: Es wurden Messungen an der Nicht-Antriebsseite, der Antriebsseite und der Nicht-Antriebsseite des Lüfters von Motor 2 untersucht.
Diagramme:
Motor NDE
Motor NDE
Lüfter NDE
Auswertung: Die Temperatur des Motorkörpers wurde bei etwa 75 Grad gemessen, und während die Schwingungswerte innerhalb akzeptabler Bereiche liegen (etwa 2,5 bis 5 mm/s), liegen die Ultraschallwerte, die für den Zustand der Lager gemessen wurden, auf Warnniveau, wobei die dominanten Signale im Spektrum den Fehlerfrequenzen der Lagerkugel und des Außenrings entsprechen. Darüber hinaus deuten die Messungen am hinteren Lager des Ventilators auf ein frühes Stadium eines Lagerschadens hin. Es wird empfohlen, den Motor allgemein zu warten und das Lager auszutauschen, während das Ventilatorlager durch Zwischenmessungen überwacht werden sollte.
4. Analyse von Lagerfehlern und Folgemaßnahmen
Analyse-Methode:
Interpretation der Spitzenfrequenzen:
Niederfrequente Spitzenwerte: Weisen in der Regel auf unzureichende Schmierung oder allgemeinen Verschleiß hin. Diese durch Oberflächenreibung verursachten Schwingungen können durch eine ordnungsgemäße Schmierung reduziert werden.
Hochfrequente Spitzenwerte: Könnten ein Anzeichen für Schäden am Innenring, den Kugeln oder dem Außenring des Lagers sein. Je nach Schwere des Schadens kann ein Austausch des Lagers erforderlich sein.
Empfehlungen:
Für Motor 1: Nach Überprüfung der Riemenspannung, der Ausrichtung und der Lagerachsen auf mögliche Fehlausrichtung, wenn die Spitzen mit steigender Frequenz zunehmen, könnte ein Lagerschaden fortschreiten. Es wird empfohlen, den Motor neu zu schmieren und die Messungen zu wiederholen.
Für Motor 2: Wenn die Frequenzen sehr hoch und die Spitzen groß sind, sollte der Austausch der Lager geplant werden. Der Betrieb dieses Motors sollte überwacht und nach weiteren Messungen neu bewertet werden.
5. Überwachungs- und Wartungsmaßnahmen
Schmierung: Die Lager werden auf der Grundlage der Messergebnisse geschmiert. Das Schmierleitmodul des SDT340 kann verwendet werden, um die richtige Menge an Schmiermittel hinzuzufügen. Während der Schmierung werden auch Ultraschallmessungen durchgeführt, um festzustellen, ob der optimale Schmiergrad erreicht ist.
Austausch des Lagers: Wenn die Analyse zeigt, dass der Lagerschaden irreversibel ist, sollte ein geplanter Stillstand für den Austausch des Lagers organisiert werden.
6. Schlussfolgerung und Berichterstattung
Zustandsüberwachung: Anhand der aus den SDT340-Messungen gewonnenen Diagramme konnte die Entwicklung von Lagerfehlern beobachtet werden, und es wurden die notwendigen Eingriffe geplant.
Frühzeitige Erkennung: Lagerfehler wurden durch die Frequenzanalyse frühzeitig erkannt und kostspielige Ausfallzeiten vermieden.
Wartungsstrategie: Die Lebensdauer der Anlage wurde durch regelmäßige Ultraschallmessungen und Schmierstoffkontrollen verlängert.
7: Berechnung der Vorteile
Energieeinsparungen:
Erhöhte Effizienz: Der Energieverbrauch wird durch die Vermeidung von Verschleiß und Reibung in den Lagern reduziert.
Wartungskosten:
Geringere Kosten: Frühzeitige Erkennung und ordnungsgemäße Schmierung helfen, Lagerschäden zu vermeiden und die Wartungskosten zu senken.
Lebensdauer der Ausrüstung:
Verlängerte Lebensdauer der Lager: Die Lebensdauer der Lager wird verlängert, was die Kosten für Ersatzteile und Arbeitskräfte reduziert.
8: Berichterstattung über die Investitionsrentabilität (ROI)
Kosteneinsparungen:
Innerhalb der ersten 6 Monate: Durch die frühzeitige Erkennung von Lagerfehlern mit dem SDT340 konnten die Reparaturkosten und Ausfallzeiten erheblich reduziert werden, was zu einer Einsparung von 30 % bei den Wartungskosten des Unternehmens führte.
Leistungsverbesserung:
Kontinuierliche Produktion: Durch die frühzeitige Fehlererkennung und die optimierte Schmierung liefen die Lager und Motoren reibungsloser. Unerwartete Stillstandszeiten in der Produktionslinie wurden um 50 % reduziert, was die Produktionseffizienz verbesserte.
ROI-Berechnung:
ROI: Vergleicht man die in das Projekt getätigten Investitionen (Gerätekauf, Mitarbeiterschulung, Analyseverfahren) mit den erzielten Vorteilen, so errechnet sich eine Kapitalrendite von 200 %. Dies zeigt, dass das investierte Kapital innerhalb eines Jahres zurückgewonnen werden konnte.
9: Berichterstattung über die kumulierte Hilfe
Erreichung der Ziele:
Verringerung der Lagerschäden: Das Ziel des Projekts, die Zahl der Lagerschäden um 80 % zu reduzieren, wurde durch den Einsatz des SDT340 erfolgreich erreicht. Frühzeitige Lagerschäden an den Motoren und Ventilatoren wurden weitgehend verhindert, so dass die Kontinuität des Betriebs der Anlagen gewährleistet ist.
Berichterstattung über die Ergebnisse:
Management-Bericht: Der Geschäftsleitung wurde ein detaillierter Bericht vorgelegt, in dem die durch den Einsatz des SDT340 erzielten Kosteneinsparungen, Verbesserungen der Produktionseffizienz und die Optimierung des Wartungsprozesses aufgezeigt wurden. Der Bericht beweist, wie effektiv das Gerät die Instandhaltungsstrategien des Unternehmens gestärkt hat.
Zusätzliche Verbesserungsvorschläge:
Künftige Schritte: Obwohl die Früherkennung erfolgreich durchgeführt wurde, müssen die Überwachungs- und Schmierprozesse weiter optimiert werden. Es wird auch empfohlen, andere Anlagen mit dem SDT340 zu überwachen.
Schlussfolgerung:
Das Projekt zur frühzeitigen Erkennung von Lagerfehlern, das an der Produktionslinie eines Herstellers von Babywindeln unter Verwendung des SDT340-Geräts durchgeführt wurde, führte zu erheblichen Verbesserungen bei den Motoren und Ventilatoren. Die frühzeitige Erkennung und die richtigen Schmierungsstrategien verlängerten die Lebensdauer der Anlagen, reduzierten die Wartungskosten und erhöhten die Produktionseffizienz. Das Projekt führte zu einer grundlegenden Veränderung der gesamten Wartungsprozesse des Unternehmens und gewährleistet die Zuverlässigkeit und Nachhaltigkeit der Produktionslinie.
Wichtigste Ergebnisse:
80 % der Lagerdefekte wurden frühzeitig erkannt und verhindert.
Unerwartete Produktionsausfälle wurden um 50 % reduziert.
30 % Einsparungen bei den Instandhaltungskosten wurden erzielt.
Die Investitionsrendite (ROI) erreichte 200 %.
Dieses Projekt verschaffte dem Unternehmen einen erheblichen Kostenvorteil, verbesserte die Wartungsprozesse und ermöglichte eine langfristige Produktion mit weniger Ausfällen.