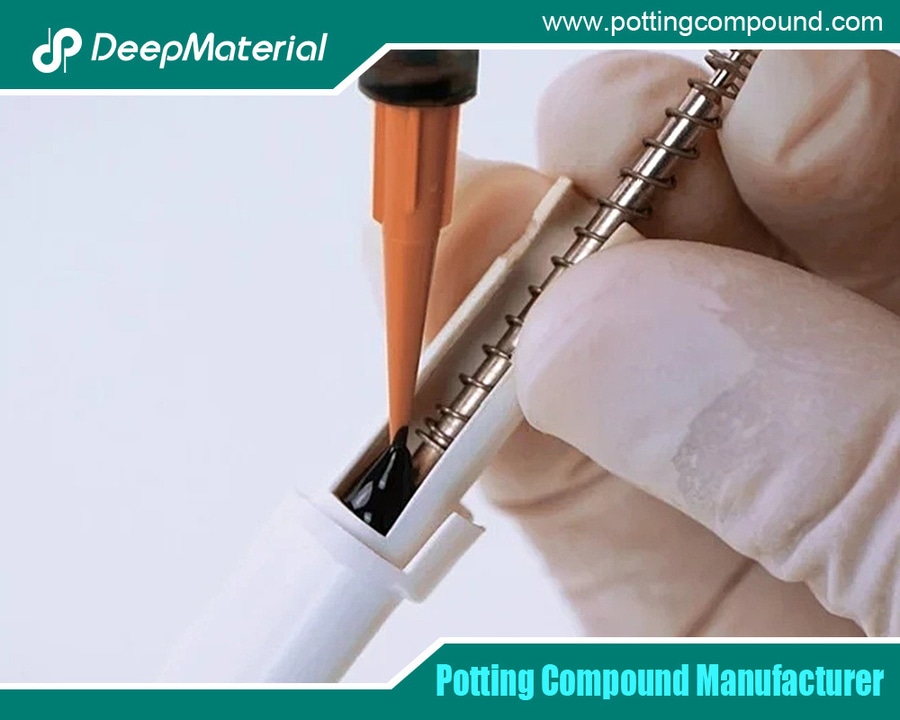
Automatische Übersetzung anzeigen
Dies ist eine automatisch generierte Übersetzung. Wenn Sie auf den englischen Originaltext zugreifen möchten, klicken Sie hier
#Neues aus der Industrie
Den Prozess des elektronischen Vergusses verstehen: Ein umfassender Leitfaden
Bester Hersteller von Klebstoff für den elektronischen Verguss
Der Vergussprozess spielt eine entscheidende Rolle für den Schutz und die Langlebigkeit elektronischer Komponenten. Dieser umfassende Leitfaden befasst sich mit den Feinheiten des Vergussverfahrens, seiner Bedeutung, den beteiligten Materialien und bewährten Verfahren. Egal, ob Sie in der Elektronikindustrie tätig sind oder einfach nur neugierig auf die Feinheiten dieses wichtigen Prozesses sind, dieser Artikel wird Ihnen einen tiefen Einblick in das Thema geben.
Was ist Electronic Potting?
Der elektronische Verguss ist ein Schutzverfahren, das in der Elektronikindustrie verwendet wird, um Komponenten in einem Harz oder Polymermaterial zu verkapseln. Der Hauptzweck des Vergusses besteht darin, empfindliche elektronische Bauteile vor Umwelteinflüssen wie Feuchtigkeit, Staub, Chemikalien, mechanischen Stößen und Vibrationen zu schützen. Die Verkapselung stellt eine Barriere für diese Elemente dar und gewährleistet die Zuverlässigkeit und Haltbarkeit elektronischer Geräte.
Der Verguss ist besonders wichtig bei Anwendungen, bei denen die Elektronik rauen Bedingungen ausgesetzt ist, wie z. B. im Automobilbau, in der Luft- und Raumfahrt, in der Schifffahrt und in industriellen Umgebungen. Durch die Einbettung der Komponenten in eine feste, schützende Masse können die Hersteller die Leistung und Langlebigkeit ihrer Produkte verbessern.
Die Bedeutung des Vergusses in der Elektronik
Der Vergussprozess ist aus mehreren Gründen wichtig:
Schutz vor Umwelteinflüssen: Elektronische Bauteile sind oft anfällig für Umwelteinflüsse wie Feuchtigkeit, Temperaturschwankungen und ätzende Chemikalien. Durch den Verguss wird eine robuste Barriere geschaffen, die die Bauteile vor diesen Elementen schützt und so Schäden verhindert und eine gleichbleibende Leistung gewährleistet.
Mechanische Festigkeit: Der Verguss verleiht den Bauteilen mechanische Festigkeit und schützt sie vor physischen Belastungen, Vibrationen und Stößen. Dies ist besonders wichtig bei Anwendungen, bei denen die Elektronik ständigen Bewegungen oder rauen Betriebsbedingungen ausgesetzt ist.
Elektrische Isolierung: Die für den Verguss verwendeten Materialien bieten eine hervorragende elektrische Isolierung, verhindern Kurzschlüsse und schützen vor elektrischen Störungen. Dies gewährleistet die Stabilität und Zuverlässigkeit des elektronischen Geräts im Laufe der Zeit.
Wärmemanagement: Einige Vergussmaterialien sind so konzipiert, dass sie eine gute Wärmeleitfähigkeit aufweisen und so dazu beitragen, die von den elektronischen Bauteilen erzeugte Wärme abzuleiten. Dies ist wichtig, um eine Überhitzung zu verhindern und die Effizienz des Geräts zu erhalten.
Materialien für den Elektronikverguss
Die Wahl des Vergussmaterials ist entscheidend für den Erfolg des Prozesses. Das Material muss die spezifischen Anforderungen der Anwendung erfüllen, z. B. Wärmeleitfähigkeit, chemische Beständigkeit oder Flexibilität. Zu den am häufigsten verwendeten Vergussmaterialien gehören:
Epoxidharze: Epoxid ist aufgrund seiner hervorragenden Haftung, mechanischen Festigkeit und chemischen Beständigkeit eines der am häufigsten verwendeten Vergussmaterialien. Epoxidharze härten aus und bilden eine harte, steife Masse, die einen robusten Schutz für elektronische Komponenten bietet. Sie sind ideal für Anwendungen, die einen hohen mechanischen und umwelttechnischen Schutz erfordern.
Polyurethanharze: Polyurethan bietet mehr Flexibilität als Epoxidharz und eignet sich daher für Anwendungen, bei denen das Vergussmaterial mechanische Belastungen oder Vibrationen aufnehmen muss. Polyurethanharze bieten auch eine gute Beständigkeit gegen Feuchtigkeit und Chemikalien, was sie zu einer beliebten Wahl in verschiedenen Branchen macht.
Silikonharze: Silikon ist für seine Flexibilität und Hochtemperaturbeständigkeit bekannt. Silikon-Vergussmassen bleiben auch nach dem Aushärten flexibel und können so die Wärmeausdehnung und -kontraktion der Komponenten ausgleichen. Sie sind ideal für Hochtemperaturanwendungen und für Anwendungen, bei denen Flexibilität eine wichtige Voraussetzung ist.
Acrylharze: Acrylharze werden für Vergussanwendungen verwendet, bei denen Transparenz und UV-Beständigkeit wichtig sind. Diese Harze werden häufig in Außenanwendungen eingesetzt, bei denen die Bauteile dem Sonnenlicht ausgesetzt sind und ihr Aussehen und ihre Leistung über lange Zeit erhalten bleiben müssen.
Polyesterharze: Polyester ist ein weiteres Material, das für Vergusszwecke verwendet wird. Es bietet eine gute elektrische Isolierung und chemische Beständigkeit. Es ist jedoch weniger flexibel und spröder als andere Materialien, weshalb es in der Regel für Anwendungen verwendet wird, bei denen diese Eigenschaften akzeptabel sind.
Der Prozess des elektronischen Vergusses: Schritt für Schritt
Der Vergussprozess umfasst mehrere Schritte, von denen jeder einzelne sorgfältig kontrolliert werden muss, um das gewünschte Ergebnis zu erzielen. Im Folgenden finden Sie einen schrittweisen Überblick über den Vergussprozess für elektronische Bauteile:
Schritt 1: Vorbereitung der Komponenten
Reinigung: Die elektronischen Bauteile müssen vor dem Verguss gründlich gereinigt werden, um Verunreinigungen wie Staub, Öle oder Rückstände zu entfernen. Jegliche Verunreinigung kann die Haftung des Vergussmaterials beeinträchtigen und den Schutz, den es bietet, gefährden.
Abdecken: In manchen Fällen müssen bestimmte Bereiche des Bauteils von Vergussmaterial freigehalten werden. Abdeckband oder andere Schutzmaterialien decken diese Bereiche während des Vergusses ab.
Schritt 2: Auswahl des Vergussmaterials
Die Auswahl des Vergussmaterials richtet sich nach den spezifischen Anforderungen der Anwendung. Faktoren wie Wärmeleitfähigkeit, Flexibilität, chemische Beständigkeit und Aushärtungszeit werden bei der Auswahl des geeigneten Materials berücksichtigt.
Schritt 3: Mischen des Vergussmaterials
Vergussmaterialien werden oft in zweiteiligen Systemen geliefert, die vor der Anwendung gemischt werden müssen. Harz und Härter werden in einem bestimmten Verhältnis gemischt, und die Mischung wird gründlich gerührt, um eine gleichmäßige Konsistenz zu gewährleisten. Das richtige Mischen ist entscheidend, um die gewünschten Eigenschaften des ausgehärteten Materials zu erreichen.
Schritt 4: Auftragen des Vergussmaterials
Das gemischte Vergussmaterial wird über die elektronischen Bauteile gegossen, in der Regel in einer Form oder einem Gehäuse, in dem sie fixiert sind. Es muss darauf geachtet werden, dass keine Luftblasen eingeschlossen werden, keine Hohlräume entstehen und der Schutz nicht geschwächt wird. Das Vergussmaterial sollte gleichmäßig um die Bauteile fließen und sie vollständig umschließen.
Schritt 5: Aushärten
Nach dem Auftragen muss das Vergussmaterial aushärten. Die Aushärtung kann bei Raumtemperatur erfolgen oder durch Wärme beschleunigt werden, je nach verwendetem Material. Während des Aushärtungsprozesses härtet das Material aus und entwickelt seine Schutzeigenschaften. Die Aushärtezeit variiert je nach Material und den gewünschten Eigenschaften des Endprodukts.
Schritt 6: Inspektion und Prüfung
Nach dem Aushärten des Vergussmaterials werden die eingekapselten Komponenten inspiziert und getestet, um sicherzustellen, dass der Vergussprozess erfolgreich war. Dies kann die Überprüfung auf Hohlräume, Risse oder andere Defekte sowie die Prüfung der elektrischen Isolierung und der mechanischen Festigkeit der vergossenen Komponenten umfassen.
Schritt 7: Endmontage
Nachdem der Vergussprozess abgeschlossen ist und die Komponenten die Inspektion bestanden haben, werden sie in die Endmontage des Produkts integriert. Die vergossenen Bauteile sind für den Einsatz in der vorgesehenen Anwendung bereit und verfügen über einen verbesserten Schutz gegen Umwelteinflüsse und mechanische Belastungen.
Anwendungen des Elektronikvergusses
Elektronikverguss wird in einer Vielzahl von Branchen und Anwendungen eingesetzt. Einige der häufigsten Anwendungen sind:
Automobilelektronik: In der Automobilindustrie schützt der Elektronikverguss Sensoren, Steuergeräte und andere elektronische Komponenten, die rauen Bedingungen wie extremen Temperaturen, Feuchtigkeit und Vibrationen ausgesetzt sind. Der Verguss gewährleistet die Zuverlässigkeit und Langlebigkeit dieser wichtigen Komponenten.
Luft- und Raumfahrt und Verteidigung: In der Luft- und Raumfahrt und im Verteidigungsbereich müssen elektronische Komponenten extremen Bedingungen standhalten, darunter große Höhen, Temperaturschwankungen und mechanische Stöße. Der Verguss bietet den notwendigen Schutz, um die Leistung und Sicherheit dieser Komponenten in anspruchsvollen Umgebungen zu gewährleisten.
Industrieausrüstung: Industrieelektronik wie Steuersysteme, Sensoren und Stromversorgungen arbeiten oft in rauen Umgebungen, die Staub, Feuchtigkeit, Chemikalien und mechanischer Belastung ausgesetzt sind. Der Verguss schützt diese Komponenten und stellt sicher, dass sie in industriellen Umgebungen zuverlässig funktionieren.
Medizinische Geräte: Im medizinischen Bereich schützt der elektronische Verguss empfindliche Komponenten in Geräten wie Herzschrittmachern, Diagnosegeräten und Bildgebungssystemen. Der Verguss bietet eine Barriere gegen Feuchtigkeit und Verschmutzung und gewährleistet so die Sicherheit und Wirksamkeit dieser lebensrettenden Geräte.
Unterhaltungselektronik: Vergussmasse wird auch in der Unterhaltungselektronik eingesetzt, z. B. in Smartphones, Tablets und tragbaren Geräten, um Komponenten vor Wasser, Staub und Stößen zu schützen. Dadurch wird die Haltbarkeit und Langlebigkeit der Produkte im täglichen Gebrauch gewährleistet.
Schiffselektronik: Elektronik ist Salzwasser, Feuchtigkeit und extremen Bedingungen in der Meeresumgebung ausgesetzt. Der Verguss bietet den notwendigen Schutz, um Korrosion und Schäden zu verhindern und den zuverlässigen Betrieb von Schiffselektronik zu gewährleisten.
Herausforderungen und Überlegungen beim Vergussprozess
Obwohl der Verguss von Elektronik zahlreiche Vorteile bietet, gibt es auch einige Herausforderungen und Überlegungen, die zu beachten sind:
Materialkompatibilität: Das Vergussmaterial muss mit den elektronischen Komponenten und der Betriebsumgebung kompatibel sein. Inkompatible Materialien können zu Fehlern führen, wie z. B. Delamination oder Rissbildung.
Wärmeausdehnung: Verschiedene Materialien dehnen sich bei Temperaturschwankungen unterschiedlich schnell aus und ziehen sich zusammen. Das Vergussmaterial muss in der Lage sein, diese Änderungen auszugleichen, ohne die Komponenten zu belasten.
Aushärtezeit: Die Aushärtezeit des Vergussmaterials kann die Produktionspläne beeinflussen. Schneller aushärtende Materialien können für die Großserienproduktion wünschenswert sein, aber sie können auch Nachteile in Bezug auf die mechanischen Eigenschaften mit sich bringen.
Nacharbeit und Reparatur: Einmal vergossene Komponenten lassen sich oft nur schwer oder gar nicht mehr reparieren oder nacharbeiten. Daher muss sichergestellt werden, dass der Vergussprozess beim ersten Mal korrekt durchgeführt wird.
Kosten: Die Kosten für die Vergussmaterialien und das Verfahren selbst können erheblich sein. Die Hersteller müssen den Preis mit dem für die jeweilige Anwendung erforderlichen Schutzniveau abwägen.
Innovationen bei Vergussmaterialien und -techniken
Die Elektronikvergussbranche entwickelt sich ständig weiter, und es werden neue Materialien und Techniken entwickelt, um neue Herausforderungen zu bewältigen und die Leistung zu verbessern. Einige der jüngsten Innovationen sind:
Fortschrittliche Epoxidformulierungen: Neue Epoxidformulierungen bieten eine verbesserte Wärmeleitfähigkeit, kürzere Aushärtezeiten und eine bessere Haftung auf einer größeren Anzahl von Substraten. Diese Weiterentwicklungen ermöglichen effizientere und zuverlässigere Vergussverfahren.
Niedrigviskose Materialien: Niedrigviskose Vergussmaterialien sind so konzipiert, dass sie leichter in kleine Räume und um komplexe Geometrien fließen. Dadurch wird das Risiko von Hohlräumen verringert und eine vollständige Verkapselung der Komponenten gewährleistet.
UV-aushärtende Vergussmassen: UV-aushärtende Vergussmassen ermöglichen eine schnelle Aushärtung unter ultraviolettem Licht, was die Produktionszeiten verkürzt und den Durchsatz erhöht. Diese Materialien sind vorteilhaft für Anwendungen, bei denen es auf Geschwindigkeit ankommt.
Umweltfreundliche Optionen: Angesichts des wachsenden Umweltbewusstseins entwickeln die Hersteller Vergussmaterialien, die nachhaltiger sind und eine geringere Umweltbelastung aufweisen. Diese Materialien sind weniger giftig, leichter zu entsorgen und energieeffizienter in der Herstellung.
Intelligente Vergussmaterialien: Forscher erforschen den Einsatz intelligenter Materialien, die ihre Eigenschaften als Reaktion auf äußere Reize wie Temperatur oder Stress verändern können. Diese Materialien könnten verbesserten Schutz und Anpassungsfähigkeit in dynamischen Umgebungen bieten.
Bewährte Praktiken für erfolgreiches Vergießen
Um die besten Ergebnisse beim Verguss von elektronischen Bauteilen zu erzielen, sollten Hersteller die folgenden Best Practices befolgen:
Richtige Materialauswahl: Wählen Sie das Vergussmaterial, das am besten zu den Anforderungen der Anwendung passt. Berücksichtigen Sie Faktoren wie Wärmeleitfähigkeit, Flexibilität und chemische Beständigkeit.
Gründliche Vorbereitung der Komponenten: Stellen Sie sicher, dass alle Komponenten sauber und frei von Verunreinigungen sind, bevor Sie sie vergießen. Eine ordnungsgemäße Vorbereitung ist entscheidend für eine gute Haftung und den Gesamterfolg.
Kontrolle der Vergussumgebung: Führen Sie den Vergussprozess in einer kontrollierten Umgebung durch, um das Risiko von Verunreinigungen zu minimieren und gleichbleibende Ergebnisse zu gewährleisten.
Sorgfältiges Auftragen: Tragen Sie das Vergussmaterial sorgfältig auf, um das Einschließen von Luftblasen zu vermeiden und eine vollständige Verkapselung der Komponenten sicherzustellen.
Aushärtungszeitmanagement: Befolgen Sie die Empfehlungen des Herstellers für Aushärtungszeiten und -temperaturen, um die gewünschten Eigenschaften des Endprodukts zu erzielen.
Qualitätskontrolle: Prüfen und testen Sie die vergossenen Komponenten, um die erforderlichen Standards zu erfüllen. Dazu gehört auch die Überprüfung auf Hohlräume, Risse und die richtige Isolierung.
Fazit
Der Vergussprozess ist für den Schutz und die Verbesserung der Leistung elektronischer Komponenten von entscheidender Bedeutung. Hersteller können die Zuverlässigkeit, Langlebigkeit und Sicherheit ihrer Produkte in verschiedenen Anwendungen gewährleisten, wenn sie die Materialien, Techniken und bewährten Verfahren für den Verguss kennen. Im Zuge des technologischen Fortschritts werden Innovationen bei den Vergussmaterialien und -methoden den Prozess weiter verbessern und einen noch besseren Schutz für die Elektronik, die unsere Welt versorgt, bieten.
Wenn Sie mehr über den Prozess des Vergusses von Elektronik erfahren möchten: ein umfassender Leitfaden, besuchen Sie DeepMaterial unter https://www.pottingcompound.com/.