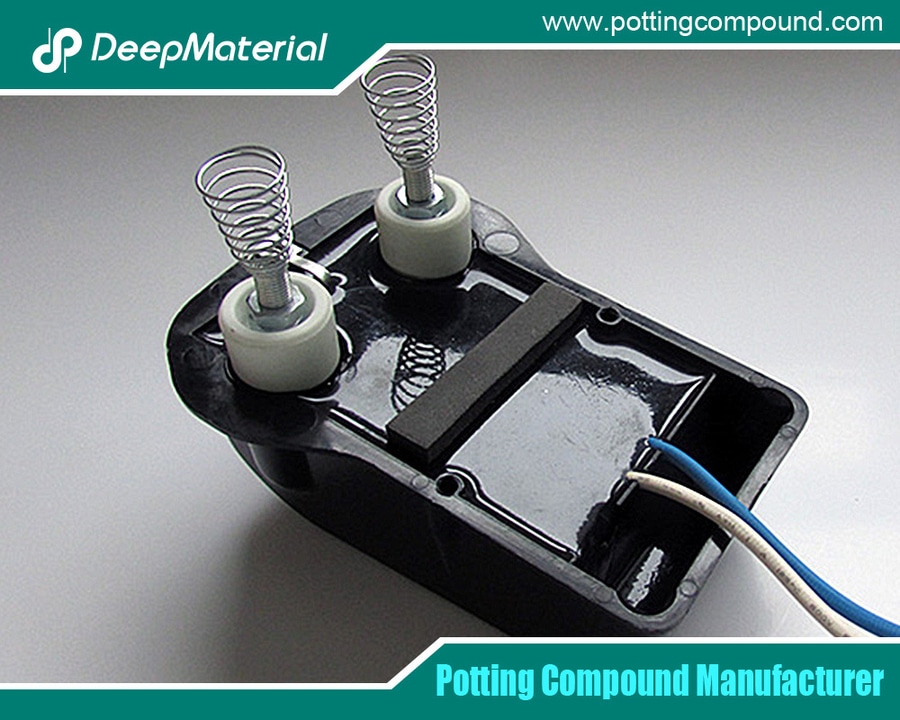
Automatische Übersetzung anzeigen
Dies ist eine automatisch generierte Übersetzung. Wenn Sie auf den englischen Originaltext zugreifen möchten, klicken Sie hier
#Neues aus der Industrie
Vergussmasse für Elektronik: Ein umfassender Leitfaden
Bester Vergussmasse-Kleber für Elektronikhersteller
Vergussmassen spielen eine entscheidende Rolle beim Schutz und bei der Verbesserung elektronischer Komponenten. Diese Materialien, die oft auch als Vergussmassen bezeichnet werden, bieten verschiedene Vorteile, darunter Isolierung, Schutz vor Umweltgefahren und mechanische Unterstützung. In diesem Artikel werden wir die Welt der Vergussmassen für die Elektronik erkunden und ihre Arten, Anwendungen, Vorteile und Auswahlkriterien erörtern.
Was ist eine Vergussmasse?
Vergussmassen kapseln elektronische Komponenten ein und versehen sie mit einer Schutzschicht. Diese Vergussmassen werden in der Regel in flüssiger Form aufgetragen, die dann aushärtet und eine feste, dauerhafte Hülle um die Komponenten bildet. Die Hauptaufgabe von Vergussmassen besteht darin, elektronische Baugruppen vor Feuchtigkeit, Staub, Chemikalien und mechanischen Stößen zu schützen und so die Langlebigkeit und Zuverlässigkeit des Geräts zu gewährleisten.
Arten von Vergussmassen
Es gibt verschiedene Arten von Vergussmassen, von denen jede über einzigartige Eigenschaften verfügt, die sie für bestimmte Anwendungen geeignet machen. Zu den gängigsten Arten von Vergussmassen gehören:
Epoxid-Vergussmassen
Epoxidharze gehören aufgrund ihrer hervorragenden mechanischen Festigkeit, chemischen Beständigkeit und thermischen Stabilität zu den am häufigsten verwendeten Vergussmassen. Sie bieten eine solide Verbindung mit verschiedenen Substraten und sind daher ideal für Anwendungen, die eine lange Lebensdauer und Schutz in rauen Umgebungen erfordern. Epoxidharz-Vergussmassen werden häufig in der Automobilelektronik, bei industriellen Steuerungen und Stromversorgungen eingesetzt.
Vorteile:
Hohe mechanische Festigkeit
Ausgezeichnete chemische Beständigkeit
Gute thermische Stabilität
Starke Adhäsion auf verschiedenen Substraten
Benachteiligungen:
Längere Aushärtungszeiten
Kann in manchen Formulierungen spröde sein
Polyurethan-Vergussmassen
Polyurethan-Vergussmassen sind für ihre Flexibilität und Zähigkeit bekannt. Sie bieten eine ausgezeichnete Beständigkeit gegen Feuchtigkeit und werden häufig in Anwendungen eingesetzt, bei denen Vibrationen und Temperaturschwankungen ein Problem darstellen. Polyurethan-Vergussmassen werden häufig in der Unterhaltungselektronik, bei LED-Beleuchtungen und in der Automobilindustrie eingesetzt.
Vorteile:
Flexibel und zäh
Gute Beständigkeit gegen Feuchtigkeit
Geeignet für vibrationsgefährdete Umgebungen
Schnellere Aushärtungszeiten als bei Epoxid
Benachteiligungen:
Geringere chemische Beständigkeit im Vergleich zu Epoxidharz
Möglicherweise nicht für Hochtemperaturanwendungen geeignet
Silikon-Vergussmassen
Silicon-Vergussmassen werden wegen ihrer außergewöhnlichen thermischen Stabilität und Flexibilität geschätzt. Sie können extremen Temperaturen standhalten und werden häufig in Anwendungen eingesetzt, bei denen Temperaturschwankungen typisch sind. Silikonmassen sind auch für ihre hervorragenden dielektrischen Eigenschaften bekannt, die sie ideal für Hochspannungsanwendungen machen.
Vorteile:
Ausgezeichnete thermische Stabilität
Hohe Flexibilität
Gute dielektrische Eigenschaften
Widerstandsfähig gegen Feuchtigkeit und Chemikalien
Nachteilige Eigenschaften:
Höhere Kosten im Vergleich zu anderen Vergussmassen
Längere Aushärtungszeiten
Acryl-Vergussmassen
Acryl-Vergussmassen bieten ein ausgewogenes Verhältnis zwischen Flexibilität und Härte und eignen sich daher für eine Vielzahl von Anwendungen. Sie härten schnell aus und lassen sich leicht verarbeiten. Sie werden häufig in der Automobilelektronik, in Sensoren und in Verbrauchsgeräten eingesetzt.
Vorteile:
Schnelle Aushärtungszeiten
Gutes Gleichgewicht von Flexibilität und Härte
UV-beständig
Leicht zu verarbeiten
Benachteiligungen:
Geringere chemische Beständigkeit
Möglicherweise nicht für Umgebungen mit hohen Temperaturen geeignet
Anwendungen von Vergussmassen
Vergussmassen werden in einer Vielzahl von Anwendungen in unterschiedlichen Branchen eingesetzt. Ihre Fähigkeit, elektronische Komponenten zu schützen und zu verbessern, macht sie in den folgenden Bereichen unverzichtbar:
Kfz-Elektronik
Elektronische Bauteile sind in der Automobilindustrie rauen Umgebungen ausgesetzt, darunter extreme Temperaturen, Feuchtigkeit und Vibrationen. Vergussmassen schützen diese Komponenten und gewährleisten ihre Zuverlässigkeit und Langlebigkeit. Zu den Anwendungen gehören Motorsteuergeräte, Sensoren und Beleuchtungssysteme.
Unterhaltungselektronik
Vergussmassen werden häufig in der Unterhaltungselektronik eingesetzt, um empfindliche Komponenten vor Feuchtigkeit, Staub und mechanischen Beschädigungen zu schützen. Sie sind häufig in Smartphones, Tablets, tragbaren Geräten und LED-Beleuchtungen zu finden.
Industrielle Steuerungen
Industrielle Umgebungen sind oft rau, da sie Chemikalien, Feuchtigkeit und mechanischer Belastung ausgesetzt sind. Industrielle Steuerungen verwenden Vergussmassen, um empfindliche Elektronik vor diesen Gefahren zu schützen und so einen kontinuierlichen Betrieb zu gewährleisten und Ausfallzeiten zu reduzieren.
Medizinische Geräte
Medizinische Geräte erfordern ein hohes Maß an Zuverlässigkeit und Schutz. Vergussmassen werden in der Medizinelektronik eingesetzt, um Komponenten vor Feuchtigkeit, Sterilisationsprozessen und mechanischen Stößen zu schützen. Zu den Anwendungen gehören bildgebende Geräte, Diagnosegeräte und Patientenüberwachungssysteme.
Luft- und Raumfahrt und Verteidigung
Elektronische Komponenten in der Luft- und Raumfahrt und im Verteidigungsbereich sind extremen Bedingungen ausgesetzt, darunter hohe Temperaturen, Vibrationen und Strahlung. Vergussmassen bieten den notwendigen Schutz und gewährleisten die Funktionalität und Zuverlässigkeit einsatzkritischer Systeme.
Vorteile der Verwendung von Vergussmassen
Vergussmassen in der Elektronik bieten mehrere Vorteile, die sie zu einem unverzichtbaren Bestandteil der modernen Elektronikentwicklung und -fertigung machen. Zu diesen Vorteilen gehören:
Schutz der Umwelt
Vergussmassen bilden eine robuste Barriere gegen Umweltfaktoren wie Feuchtigkeit, Staub, Chemikalien und Temperaturschwankungen. Dieser Schutz ist entscheidend für die Langlebigkeit und Zuverlässigkeit elektronischer Komponenten, insbesondere in rauen Umgebungen.
Mechanische Unterstützung
Vergussmassen bieten elektronischen Bauteilen mechanischen Halt und schützen sie vor physischen Schäden durch Vibrationen, Stöße oder Schläge. Dieser Schutz ist besonders wichtig bei Anwendungen, bei denen die Elektronik ständig in Bewegung ist oder belastet wird.
Elektrische Isolierung
Eine der Hauptfunktionen von Vergussmassen ist die elektrische Isolierung. Durch die Verkapselung der Komponenten verhindern Vergussmassen Kurzschlüsse und elektrische Ausfälle und gewährleisten so den sicheren Betrieb des Geräts.
Wärmemanagement
Bestimmte Vergussmassen, wie z. B. Silikone und Epoxidharze, haben eine ausgezeichnete Wärmeleitfähigkeit und helfen so, die von elektronischen Bauteilen erzeugte Wärme abzuleiten. Dieses Wärmemanagement ist wichtig, um Überhitzung zu vermeiden und den effizienten Betrieb des Geräts zu gewährleisten.
Verbesserte Zuverlässigkeit
Vergussmassen verbessern die Zuverlässigkeit elektronischer Geräte erheblich, indem sie sie vor Umwelteinflüssen, mechanischer Belastung und elektrischen Ausfällen schützen. Erhöhte Zuverlässigkeit bedeutet weniger Ausfälle, geringere Wartung und längere Nutzungsdauer.
Die Auswahl der richtigen Vergussmasse
Die Wahl der geeigneten Vergussmasse für Ihre Anwendung ist entscheidend für das Erreichen des gewünschten Schutz- und Leistungsniveaus. Bei der Auswahl einer Vergussmasse müssen mehrere Faktoren berücksichtigt werden, darunter:
Betriebsumgebung
Die Betriebsumgebung spielt eine wichtige Rolle bei der Bestimmung der zu verwendenden Vergussmasse. Faktoren wie Temperaturbereich, Feuchtigkeit, chemische Belastung und mechanische Beanspruchung müssen bei der Auswahl einer Vergussmasse berücksichtigt werden.
Temperaturbereich: Silikon- oder Epoxidverbindungen werden aufgrund ihrer thermischen Stabilität für Umgebungen mit hohen Temperaturen empfohlen.
Luftfeuchtigkeit: Polyurethanmischungen sind ideal für Anwendungen, bei denen Feuchtigkeitsbeständigkeit eine Priorität ist.
Chemische Belastung: Epoxidverbindungen bieten eine ausgezeichnete chemische Beständigkeit und sind für raue chemische Umgebungen geeignet.
Mechanische Eigenschaften
Die mechanischen Eigenschaften der Vergussmasse, wie Härte, Flexibilität und Zugfestigkeit, müssen den Anforderungen der Anwendung entsprechen.
Härte: Für Anwendungen, die einen festen Schutz erfordern, sind Epoxidverbindungen ideal.
Flexibilität: Polyurethan- und Silikonmassen bieten Flexibilität und eignen sich daher für Anwendungen, die Vibrationen oder Temperaturschwankungen ausgesetzt sind.
Elektrische Eigenschaften
Die elektrischen Eigenschaften der Vergussmasse, wie z. B. die Durchschlagfestigkeit und der Isolationswiderstand, sind entscheidend für Anwendungen mit hohen Spannungen oder empfindlicher Elektronik.
Durchschlagfestigkeit: Silikonmassen sind für ihre hervorragenden dielektrischen Eigenschaften bekannt und eignen sich daher für Hochspannungsanwendungen.
Isolationswiderstand: Epoxidharzmassen bieten eine starke Isolierung, die elektrische Ausfälle verhindert.
Aushärtungszeit
Die Aushärtungszeit der Vergussmasse kann sich auf den Produktionsprozess auswirken. Je nach Anwendung kann eine schnellere oder langsamere Aushärtungszeit bevorzugt werden.
Schnelle Aushärtung: Acryl- und Polyurethanmassen härten schnell aus und eignen sich daher für die Produktion hoher Stückzahlen.
Langsame Aushärtung: Epoxid- und Silikonmassen können längere Aushärtungszeiten erfordern, was für bestimmte Anwendungen mit einer stärkeren Bindung notwendig sein kann.
Kostenüberlegungen
Die Kosten sind immer ein Faktor bei der Auswahl von Materialien. Qualitativ hochwertigere Vergussmassen bieten zwar eine bessere Leistung, sind aber auch mit höheren Kosten verbunden. Es ist wichtig, die Leistungsanforderungen mit den Budgetvorgaben in Einklang zu bringen.
Anwendungsverfahren für Vergussmassen
Das Anwendungsverfahren für Vergussmassen ist ein entscheidender Schritt, um den Schutz und die Leistung elektronischer Komponenten zu gewährleisten. Der Prozess umfasst in der Regel die folgenden Schritte:
Vorbereitung
Vor dem Auftragen der Vergussmasse müssen die elektronischen Bauteile und das Gehäuse gründlich gereinigt werden, um Verunreinigungen wie Staub, Öle oder Feuchtigkeit zu entfernen. Eine ordnungsgemäße Reinigung gewährleistet eine gute Haftung und verhindert mögliche Probleme wie Blasen oder Hohlräume.
Mischen
Handelt es sich bei der Vergussmasse um ein zweiteiliges System (z. B. Epoxid oder Polyurethan), müssen die Komponenten gemäß den Anweisungen des Herstellers gründlich gemischt werden. Ein genaues Mischen ist unerlässlich, um sicherzustellen, dass die Masse ordnungsgemäß aushärtet und die gewünschten Eigenschaften erzielt werden.
Dosierung
Die gemischte Vergussmasse wird dann mit einer Spritze, einem Dispenser oder einem automatischen Gerät in die elektronische Baugruppe eingebracht. Der Dosiervorgang sollte sorgfältig durchgeführt werden, um Luftblasen oder Hohlräume zu vermeiden, die den Schutz und die Leistung der Vergussmasse beeinträchtigen können.
Aushärten
Nach dem Dosieren muss die Vergussmasse entsprechend den Empfehlungen des Herstellers ausgehärtet werden. Je nach Art der Masse kann die Aushärtung bei Raumtemperatur oder mit Wärme erfolgen. Die ordnungsgemäße Aushärtung gewährleistet, dass die Masse vollständige mechanische, thermische und elektrische Eigenschaften aufweist.
Inspektion
Sobald die Vergussmasse vollständig ausgehärtet ist, sollte die Baugruppe auf Defekte wie Luftblasen, Hohlräume oder unvollständige Abdeckung geprüft werden. Alle Probleme sollten umgehend behoben werden, um den Schutz und die Leistung der elektronischen Komponenten zu gewährleisten.
Herausforderungen beim Verguss von Elektronik
Obwohl Vergussmassen zahlreiche Vorteile bieten, gibt es auch Herausforderungen, die mit ihrem Einsatz in elektronischen Anwendungen verbunden sind. Einige der häufigsten Herausforderungen sind:
Luftblasen und Hohlräume
Während des Dosier- oder Aushärtungsprozesses können sich Luftblasen und Hohlräume bilden, die den Schutz und die Leistung der Vergussmasse beeinträchtigen. Um diese Probleme zu minimieren, sind sorgfältige Misch-, Dosier- und Aushärtungsverfahren erforderlich.
Schrumpfung
Einige Vergussmassen, insbesondere Epoxidformulierungen, können während des Aushärtens schrumpfen. Die Schrumpfung kann zu mechanischen Spannungen an den Komponenten führen, die möglicherweise Schäden verursachen oder die Leistung beeinträchtigen. Die Auswahl einer Verbindung mit geringer Schrumpfung und die Einhaltung ordnungsgemäßer Aushärteverfahren können dazu beitragen, dieses Problem zu vermindern.
Ungleiche Wärmeausdehnung
Unterschiede in der Wärmeausdehnung zwischen der Vergussmasse und den elektronischen Komponenten können zu Spannungen und potenziellen Ausfällen führen, insbesondere bei Anwendungen mit starken Temperaturschwankungen. Die Auswahl einer Vergussmasse mit einem kompatiblen Wärmeausdehnungskoeffizienten (WAK) ist entscheidend, um diese Probleme zu vermeiden.
Kompatibilität mit Komponenten
Nicht alle Vergussmassen sind mit jedem elektronischen Bauteil oder Substrattyp kompatibel. Es muss sichergestellt werden, dass die gewählte Vergussmasse nicht negativ mit den in der Baugruppe verwendeten Materialien reagiert, z. B. Metalle korrodiert oder Kunststoffe zersetzt.
Entfernung und Nacharbeit
Sobald eine Vergussmasse ausgehärtet ist, kann es schwierig oder unmöglich sein, sie zu entfernen, was eine Nacharbeit oder Reparatur erschwert. Bei Anwendungen, bei denen Nacharbeiten zu erwarten sind, kann es von Vorteil sein, eine Verbindung zu wählen, die sich leichter entfernen lässt, wie z. B. eine Verbindung auf Silikonbasis.
Innovationen und zukünftige Trends bei Vergussmassen
Der Bereich der Vergussmassen für die Elektronik entwickelt sich ständig weiter, angetrieben durch den Bedarf an verbesserter Leistung, Umweltverträglichkeit und Kompatibilität mit neuen Technologien. Einige der aktuellen Trends und Innovationen sind:
Umweltverträgliche Compounds
Angesichts des wachsenden Umweltbewusstseins steigt die Nachfrage nach Vergussmassen, die weniger umweltschädlich sind. Dazu gehört die Entwicklung von Harzen auf Biobasis und von Verbindungen mit weniger flüchtigen organischen Verbindungen (VOC).
Fortschrittliches Wärmemanagement
Mit dem Aufkommen von Hochleistungselektronik, wie z. B. Elektrofahrzeugen und Systemen für erneuerbare Energien, steigt der Bedarf an Vergussmassen mit fortschrittlichen Wärmemanagementeigenschaften. Innovationen bei wärmeleitenden Materialien tragen dazu bei, diese Nachfrage zu befriedigen.
Intelligente Vergussmassen
Forscher erforschen die Entwicklung "intelligenter" Vergussmassen, die elektronische Komponenten in Echtzeit überwachen können. Diese Vergussmassen könnten Sensoren enthalten, die Veränderungen bei Temperatur, Feuchtigkeit oder anderen Umweltfaktoren erkennen und so eine proaktive Wartung und Fehlervermeidung ermöglichen.
Nanotechnologie
Die Einbindung von Nanomaterialien in Vergussmassen ist ein neuer Trend, der das Potenzial für verbesserte mechanische, thermische und elektrische Eigenschaften bietet. Die Nanotechnologie könnte zur Entwicklung von Vergussmassen mit überlegenen Leistungsmerkmalen führen, wie z. B. erhöhte Wärmeleitfähigkeit oder verbesserte Durchschlagsfestigkeit.
Schlussfolgerung
Vergussmassen für die Elektronik sind ein wesentlicher Bestandteil für den Schutz und die Leistung moderner elektronischer Geräte. Dank der großen Auswahl an Materialien wie Epoxid, Polyurethan, Silikon und Acryl ist es möglich, für fast jede Anwendung eine geeignete Mischung zu finden. Hersteller und Ingenieure können die Langlebigkeit, Zuverlässigkeit und Effizienz ihrer elektronischen Baugruppen sicherstellen, indem sie die Eigenschaften, Anwendungen und Auswahlkriterien für Vergussmassen kennen. Mit der Weiterentwicklung der Technologie werden sich auch die Materialien und Methoden für den Verguss weiterentwickeln, was zu weiteren bedeutenden Innovationen und Fortschritten im Bereich des Elektronikschutzes führen wird.
Wenn Sie mehr über die Auswahl der besten Vergussmasse für die Elektronik erfahren möchten: ein umfassender Leitfaden, besuchen Sie DeepMaterial unter https://www.pottingcompound.com/.