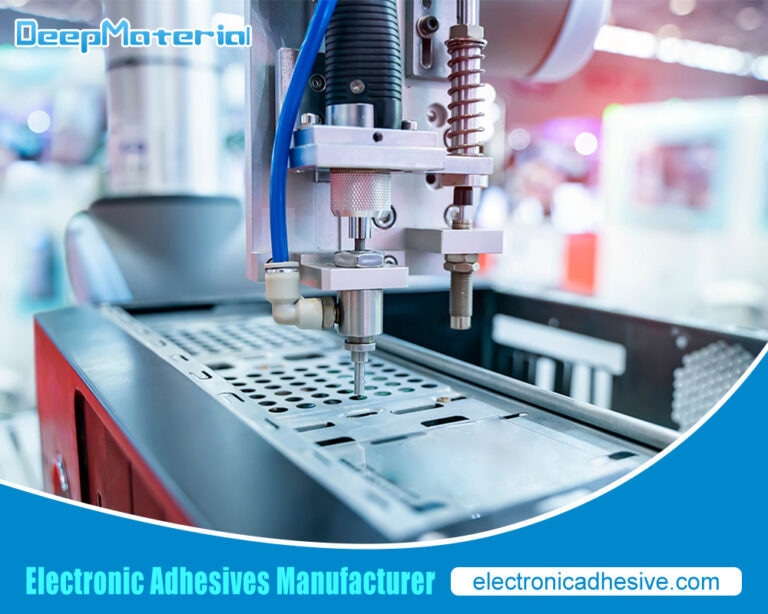
Automatische Übersetzung anzeigen
Dies ist eine automatisch generierte Übersetzung. Wenn Sie auf den englischen Originaltext zugreifen möchten, klicken Sie hier
#Neues aus der Industrie
Elektronik-Vergussmasse verstehen
Bester Elektronik-Vergussmasse-Kleber Hersteller
Elektronische Vergussmassen sind spezielle Materialien, die zum Verkapseln und Schützen elektronischer Komponenten und Baugruppen vor Umwelteinflüssen wie Feuchtigkeit, Staub, Chemikalien und mechanischer Belastung verwendet werden. Diese Vergussmassen sind in einer Vielzahl von Branchen unverzichtbar, z. B. in der Automobilindustrie, der Luft- und Raumfahrt, der Unterhaltungselektronik und der Industrieausrüstung, wo die Zuverlässigkeit und Langlebigkeit elektronischer Geräte entscheidend sind.
Beim Vergießen wird das Gehäuse eines elektronischen Geräts mit einer flüssigen Vergussmasse gefüllt, die dann aushärtet und eine Schutzbarriere um die Komponenten bildet. Diese Barriere schützt die Bauteile nicht nur vor äußeren Einflüssen, sondern verbessert auch die elektrische Isolierung, die Schwingungsdämpfung und das Wärmemanagement.
Arten von Vergussmassen
Es gibt verschiedene Arten von Vergussmassen, die jeweils spezifische, auf die verschiedenen Anwendungen zugeschnittene Eigenschaften aufweisen. Zu den am häufigsten verwendeten Typen gehören:
Epoxid-Vergussmassen: Epoxidharz ist aufgrund seiner hervorragenden Haftung, chemischen Beständigkeit und mechanischen Festigkeit eine der beliebtesten Vergussmassen. Epoxid-Vergussmassen sind ideal für Anwendungen, die eine hohe Haltbarkeit und Schutz gegen raue Umgebungen erfordern. Sie bieten eine starke elektrische Isolierung und sind beständig gegen Feuchtigkeit und Chemikalien. Sie können jedoch starr sein und eignen sich möglicherweise nicht für Anwendungen, bei denen Flexibilität erforderlich ist.
Polyurethan-Vergussmassen: Polyurethan-Vergussmassen sind für ihre Flexibilität und Elastizität bekannt und eignen sich daher für Anwendungen, bei denen sich die Komponenten bewegen oder thermisch ausdehnen können. Sie bieten eine gute Feuchtigkeitsbeständigkeit und elektrische Isolierung, obwohl sie nicht den gleichen Grad an chemischer Beständigkeit wie Epoxidverbindungen bieten. Polyurethan wird häufig in der Automobil- und Unterhaltungselektronik eingesetzt, wo Flexibilität eine wichtige Rolle spielt.
Silikon-Vergussmassen: Silikon-Vergussmassen sind hochflexibel und bieten eine ausgezeichnete thermische Stabilität, was sie ideal für Hochtemperaturanwendungen macht. Sie bieten eine gute elektrische Isolierung und Feuchtigkeitsbeständigkeit und werden häufig in der Automobil- und Luftfahrtindustrie eingesetzt. Silikonmassen werden auch für Anwendungen bevorzugt, bei denen die Komponenten extremen Temperaturschwankungen ausgesetzt sind.
Acryl-Vergussmassen: Acrylat-Vergussmassen sind für ihre einfache Anwendung und schnelle Aushärtung bekannt. Sie bieten eine mäßige Flexibilität und werden häufig bei Anwendungen eingesetzt, bei denen es auf eine schnelle Durchlaufzeit ankommt. Acrylverbindungen sind gut feuchtigkeitsbeständig, bieten aber in rauen Umgebungen möglicherweise nicht den gleichen Schutz wie Epoxid- oder Silikonverbindungen.
Urethan-Vergussmassen: Urethan-Vergussmassen bieten ein ausgewogenes Verhältnis zwischen Flexibilität und Zähigkeit. Sie bieten eine gute elektrische Isolierung und Feuchtigkeitsbeständigkeit und eignen sich daher für eine Vielzahl von Anwendungen. Urethan wird häufig in Industrie- und Automobilanwendungen eingesetzt, bei denen sowohl Haltbarkeit als auch Flexibilität erforderlich sind.
Anwendungen von Vergussmassen
Elektronische Vergussmassen werden in einer Vielzahl von Anwendungen eingesetzt, die jeweils spezifische Anforderungen an Schutz und Leistung stellen. Einige der wichtigsten Anwendungen sind:
Automobilelektronik: In der Automobilindustrie sind elektronische Komponenten extremen Bedingungen ausgesetzt, wie z. B. hohen Temperaturen, Vibrationen und chemischen Einflüssen. Vergussmassen werden verwendet, um Motorsteuergeräte (ECUs), Sensoren und andere wichtige elektronische Komponenten vor diesen rauen Bedingungen zu schützen und ihre Zuverlässigkeit und Langlebigkeit zu gewährleisten.
Elektronik für die Luft- und Raumfahrt: Anwendungen in der Luft- und Raumfahrt erfordern Komponenten, die extremen Temperaturen, Druckschwankungen und mechanischen Belastungen standhalten können. Vergussmassen werden zum Schutz von Avionik, Sensoren und anderen elektronischen Systemen in Flugzeugen und Raumfahrzeugen eingesetzt, um deren Leistungsfähigkeit in anspruchsvollen Umgebungen zu gewährleisten.
Unterhaltungselektronik: Vergussmassen werden in der Unterhaltungselektronik wie Smartphones, Tablets und tragbaren Geräten eingesetzt, um empfindliche Komponenten vor Feuchtigkeit, Staub und mechanischen Schäden zu schützen. Die Verwendung von Vergussmassen trägt dazu bei, die Lebensdauer dieser Geräte zu verlängern und ihre Zuverlässigkeit im täglichen Gebrauch zu gewährleisten.
Industrielle Ausrüstung: In industriellen Umgebungen sind elektronische Komponenten oft rauen Umgebungen ausgesetzt, darunter Chemikalien, Feuchtigkeit und mechanische Belastungen. Vergussmassen werden zum Schutz von Steuereinheiten, Sensoren und anderen elektronischen Bauteilen in Industrieanlagen verwendet, um deren kontinuierlichen Betrieb unter anspruchsvollen Bedingungen zu gewährleisten.
Medizinische Geräte: Medizinische Geräte enthalten oft empfindliche elektronische Komponenten, die vor Feuchtigkeit, Chemikalien und mechanischer Beanspruchung geschützt werden müssen. Vergussmassen werden verwendet, um diese Komponenten zu verkapseln und zu schützen und so die Sicherheit und Zuverlässigkeit der Geräte zu gewährleisten.
Systeme für erneuerbare Energien: Bei Anwendungen im Bereich der erneuerbaren Energien, wie z. B. Solarzellen und Windturbinen, sind die elektronischen Komponenten extremen Umweltbedingungen ausgesetzt. Vergussmassen werden eingesetzt, um Wechselrichter, Steuereinheiten und andere Komponenten vor Feuchtigkeit, UV-Strahlung und Temperaturschwankungen zu schützen und so die Effizienz und Langlebigkeit der Systeme zu gewährleisten.
Vorteile der Verwendung von Vergussmassen
Der Einsatz von Vergussmassen bietet zahlreiche Vorteile, die sie zu einem unverzichtbaren Bestandteil der modernen Elektronikentwicklung und -fertigung machen. Einige der wichtigsten Vorteile sind:
Schutz der Umwelt: Vergussmassen bilden eine schützende Barriere, die elektronische Komponenten vor Umwelteinflüssen wie Feuchtigkeit, Staub und Chemikalien abschirmt. Dieser Schutz ist entscheidend für die Langlebigkeit und Zuverlässigkeit elektronischer Geräte in rauen Umgebungen.
Elektrische Isolierung: Vergussmassen verbessern die elektrische Isolierung von Bauteilen und verhindern so Kurzschlüsse und elektrische Ausfälle. Dies ist besonders wichtig bei Hochspannungsanwendungen, wo die Isolierung für die Sicherheit entscheidend ist.
Absorption von Vibrationen und Stößen: In Anwendungen, in denen elektronische Bauteile Vibrationen und mechanischen Belastungen ausgesetzt sind, tragen Vergussmassen dazu bei, diese Kräfte zu absorbieren und zu dämpfen und so das Risiko von Schäden zu verringern. Dies ist besonders wichtig für Anwendungen in der Automobil- und Luftfahrtindustrie.
Wärmemanagement: Vergussmassen können auch das Wärmemanagement verbessern, indem sie die Wärme von den kritischen Komponenten ableiten. Dies ist besonders wichtig bei Hochleistungsanwendungen, bei denen eine Überhitzung zum Ausfall von Komponenten führen kann.
Verbesserte Langlebigkeit: Durch die Verkapselung von Komponenten in einer Schutzmasse wird die Gesamtlebensdauer elektronischer Geräte erhöht. Dies ist besonders wichtig bei Anwendungen, bei denen die Zuverlässigkeit von entscheidender Bedeutung ist, wie z. B. bei medizinischen Geräten und Luft- und Raumfahrtsystemen.
Anpassungsfähigkeit: Vergussmassen können an die spezifischen Anforderungen verschiedener Anwendungen angepasst werden. Dazu gehört die Anpassung des Grads der Flexibilität, der Wärmeleitfähigkeit und der chemischen Beständigkeit an die Anforderungen des zu schützenden Geräts.
Auswahlkriterien für Vergussmassen
Die Auswahl der richtigen Vergussmasse für eine bestimmte Anwendung erfordert die sorgfältige Berücksichtigung mehrerer Faktoren. Einige der wichtigsten Kriterien, die zu berücksichtigen sind, sind
Umgebungsbedingungen: Die Umgebungsbedingungen, denen die elektronischen Bauteile ausgesetzt sind, spielen eine entscheidende Rolle bei der Auswahl der richtigen Vergussmasse. Faktoren wie Temperatur, Feuchtigkeit, chemische Belastung und mechanische Beanspruchung müssen berücksichtigt werden, um sicherzustellen, dass die Vergussmasse einen angemessenen Schutz bietet.
Elektrische Eigenschaften: Die elektrischen Isolationseigenschaften der Vergussmasse sind entscheidend für die Vermeidung von Kurzschlüssen und die Gewährleistung eines zuverlässigen Betriebs des Geräts. Die Durchschlagfestigkeit, der Volumenwiderstand und die Dielektrizitätskonstante der Vergussmasse sollten auf der Grundlage der elektrischen Anforderungen der Anwendung bewertet werden.
Wärmemanagement: Bei Anwendungen, bei denen die Wärmeableitung wichtig ist, sollte die Wärmeleitfähigkeit der Vergussmasse berücksichtigt werden. Vergussmassen mit einer höheren Wärmeleitfähigkeit können die Wärme besser ableiten, eine Überhitzung verhindern und die Lebensdauer der Komponenten verlängern.
Mechanische Eigenschaften: Die mechanischen Eigenschaften der Vergussmasse, wie z. B. Härte, Flexibilität und Haftung, sind wichtig, um sicherzustellen, dass die Masse mechanischen Belastungen und Vibrationen standhält, ohne zu reißen oder abzublättern. Je nach den Anforderungen der Anwendung muss das richtige Gleichgewicht zwischen Steifigkeit und Flexibilität gefunden werden.
Aushärtezeit und -verfahren: Die Aushärtezeit und das Aushärteverfahren der Vergussmasse sind wichtige Faktoren, insbesondere in Produktionsumgebungen mit hohen Stückzahlen, in denen schnelle Durchlaufzeiten wichtig sind. Einige Vergussmassen müssen mit Wärme oder UV-Licht ausgehärtet werden, während andere bei Raumtemperatur aushärten können. Der Aushärtungsprozess sollte mit dem Produktionsprozess und dem Zeitplan vereinbar sein.
Kompatibilität mit Komponenten: Die Vergussmasse muss mit den in den elektronischen Komponenten und dem Gehäuse verwendeten Materialien kompatibel sein. Inkompatibilität kann zu Problemen wie schlechter Haftung, chemischen Reaktionen oder Beschädigung der Komponenten führen.
Kosten und Verfügbarkeit: Die Kosten und die Verfügbarkeit der Vergussmasse sind ebenfalls wichtige Faktoren, insbesondere bei der Großserienfertigung. Hochwertige Vergussmassen bieten zwar einen besseren Schutz, sind aber auch mit höheren Kosten verbunden. Bei der Wahl der Vergussmasse sollten Leistung und Kosteneffizienz je nach den Anforderungen der Anwendung abgewogen werden.
Verfahren zur Anwendung von Vergussmassen
Die Anwendung von Vergussmassen umfasst mehrere Schritte, von denen jeder sorgfältig kontrolliert werden muss, um den gewünschten Schutz und die gewünschte Leistung zu gewährleisten. Der allgemeine Prozess umfasst:
Vorbereitung des Bauteils: Bevor die Vergussmasse aufgetragen wird, müssen die Bauteile und das Gehäuse gründlich gereinigt und vorbereitet werden. Dazu gehört das Entfernen von Staub, Fett oder Verunreinigungen, die die Haftung beeinträchtigen könnten. In einigen Fällen kann ein Primer oder Haftvermittler aufgetragen werden, um die Haftung zu verbessern.
Mischen: Bei zweiteiligen Vergussmassen müssen Harz und Härter genau abgemessen und gründlich gemischt werden, um eine gleichmäßige und homogene Mischung zu gewährleisten. Das richtige Mischen ist entscheidend für das Erreichen der gewünschten Eigenschaften der ausgehärteten Masse.
Dosieren: Die Vergussmasse wird dann in das Gehäuse oder die Ummantelung eingebracht, wobei sichergestellt werden muss, dass die Bauteile vollständig bedeckt sind. Dies kann je nach Anwendung und Produktionsvolumen manuell oder mit Hilfe von automatischen Dosieranlagen erfolgen.
Aushärten: Nach dem Auftragen muss die Vergussmasse gemäß den Anweisungen des Herstellers ausgehärtet werden. Die Aushärtung kann durch Wärmeeinwirkung, UV-Licht oder einfach durch Aushärten bei Raumtemperatur erfolgen. Der Aushärtungsprozess sollte sorgfältig kontrolliert werden, um Probleme wie unvollständige Aushärtung, Hohlräume oder Blasen in der Masse zu vermeiden.
Inspektion und Prüfung: Sobald die Masse ausgehärtet ist, sollte die vergossene Baugruppe auf Defekte wie Hohlräume, Blasen oder Risse untersucht werden. Es können auch elektrische und mechanische Tests durchgeführt werden, um sicherzustellen, dass die Masse das gewünschte Schutzniveau und die gewünschte Leistung bietet.
Herausforderungen und Überlegungen beim Verguss
Obwohl Vergussmassen zahlreiche Vorteile bieten, gibt es auch Herausforderungen und Überlegungen, die für eine erfolgreiche Anwendung und Leistung berücksichtigt werden müssen:
Materialauswahl: Die Auswahl der richtigen Vergussmasse für eine bestimmte Anwendung kann aufgrund des breiten Spektrums an verfügbaren Materialien und der unterschiedlichen Anforderungen der verschiedenen Anwendungen eine Herausforderung darstellen. Eine sorgfältige Bewertung und Prüfung ist erforderlich, um sicherzustellen, dass die gewählte Masse die Anforderungen der Anwendung erfüllt.
Probleme bei der Aushärtung: Unvollständige Aushärtung, Hohlräume oder Blasen können auftreten, wenn der Aushärtungsprozess nicht richtig kontrolliert wird. Diese Probleme können den Schutz und die Leistung der Vergussmasse beeinträchtigen. Um diese Probleme zu vermeiden, ist eine ordnungsgemäße Misch-, Dosier- und Aushärtungstechnik erforderlich.
Thermische Ausdehnung: Bei Anwendungen, bei denen die Komponenten Temperaturschwankungen ausgesetzt sind, muss die Wärmeausdehnung der Vergussmasse und der Komponenten kompatibel sein. Eine unangepasste Wärmeausdehnung kann zu Rissen, Delamination oder anderen Problemen führen.
Nacharbeit und Reparatur: Sobald die Komponenten vergossen sind, können Nacharbeiten und Reparaturen schwierig oder unmöglich sein. Daher muss sichergestellt werden, dass die Komponenten vor dem Verguss korrekt funktionieren und dass der Vergussprozess korrekt durchgeführt wird.
Kostenaspekte: Hochleistungs-Vergussmassen können teuer sein, so dass Kostenüberlegungen wichtig sind, vor allem bei der Großserienproduktion. Das Gleichgewicht zwischen Leistung und Kosteneffizienz ist entscheidend, um den gewünschten Schutz zu erreichen, ohne das Budget zu sprengen.
Fazit
Elektronik-Vergussmassen spielen eine wichtige Rolle beim Schutz und bei der Verbesserung der Leistung elektronischer Komponenten in einer Vielzahl von Anwendungen. Durch den Schutz vor Umwelteinflüssen, die elektrische Isolierung und die mechanische Stabilität gewährleisten Vergussmassen die Zuverlässigkeit und Langlebigkeit elektronischer Geräte selbst unter den schwierigsten Bedingungen. Bei der Auswahl und Anwendung von Vergussmassen müssen Faktoren wie Umweltbedingungen, elektrische Eigenschaften, Wärmemanagement und mechanische Anforderungen sorgfältig berücksichtigt werden. Mit der richtigen Vergussmasse können Hersteller das gewünschte Schutz- und Leistungsniveau erreichen und so den Erfolg ihrer elektronischen Produkte sicherstellen.
Wenn Sie mehr über elektronische Vergussmassen erfahren möchten, können Sie DeepMaterial unter https://www.electronicadhesive.com/ besuchen, um weitere Informationen zu erhalten.