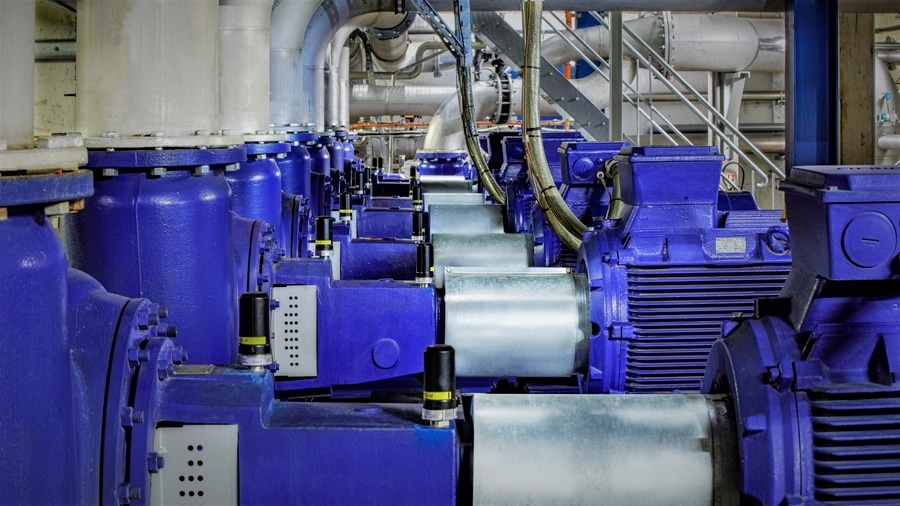
#Produkttrends
Mechanische Assets lernen sprechen
Von Preventive zu Predictive Maintenance
Durch die kontinuierliche Überwachung von Maschinenzuständen können Betriebsabläufe sicherer und effizienter gestaltet werden. Insbesondere bei kritischen Komponenten ist die zustandsorientierte oder sogar die vorausschauende Instandhaltung heute das Mittel der Wahl: Moderne intelligente Systemkomponenten übermitteln relevante Zustandsparameter an übergeordnete Instandhaltungsmanagementsysteme. Doch wie sieht es bei älteren Komponenten ohne entsprechende Diagnosefähigkeiten aus? Hier bietet eine durchdachte Kombination aus IIoT-Sensorik, Gateway-Einheiten und Cloud-Diensten eine ideale Lösung zum nachträglichen Aufrüsten. In einem Fertigungszentrum für Prozessinstrumentierung und -analytik erweist sich dieses Paket als äußerst kosteneffizient und vielseitig.
In Prozess- und Produktionsanlagen sind Instandhaltungsteams seit Jahrzehnten bestrebt, die Gesamtproduktivität der Anlagen zu erhöhen. Ein zentrales Element dieser Bemühungen ist die Entwicklung und Umsetzung effektiver Instandhaltungsstrategien. Der traditionelle Ansatz, Maschinen und Anlagen so lange laufen zu lassen, bis sie ausfallen (sog. „Run to Failure“), hat sich längst als zu ineffizient und zu teuer erwiesen. Ein wichtiger Schritt in der Entwicklung effektiverer Instandhaltungsstrategien war die Einführung der vorbeugenden Instandhaltung (Preventive Maintenance – PM). Darunter werden routinemäßige, nach festgelegten Zeitplänen durchgeführte Wartungs- und Inspektionsmaßnahmen, verstanden. Während PM dazu beiträgt, unerwartete Ausfälle zu vermeiden, kommt es allerdings auch zu unnötigen Instandhaltungsarbeiten, wenn die Ausrüstung eigentlich noch in gutem Zustand ist.
Als nächster Schritt in der Entwicklung effizienter Instandhaltungsstrategien gilt Predictive Maintenance (PdM), die vorausschauende Wartung. Dafür werden Daten über den Zustand der Ausrüstung gesammelt und analysiert, um vorherzusagen, wann eine Wartung notwendig sein könnte. Diese Methode zielt darauf ab, die Wartung genau dann durchzuführen, wenn sie erforderlich ist, und zwar auf der Grundlage des tatsächlichen Zustands der Ausrüstung und nicht nach einem festgelegten Zeitplan. Ein Schlüsselaspekt von PdM ist die zustandsorientierte Instandhaltung (Condition-Based Monitoring, CBM), die kontinuierliche Überwachung und Analyse des Zustands von Anlagen während des normalen Betriebs. Die erfolgreiche Implementierung zustandsbasierter Instandhaltung erfordert eine Reihe von Technologien und Ressourcen einschließlich geeigneter Sensoren, Datenübertragungs- und -verarbeitungssysteme und spezieller Analysesoftware. Ohne diese Mittel ist es unmöglich, Wartungen aufgrund aktueller Maschinenzustände durchzuführen. Das Nachrüsten solcher Technologien ist für rotierende oder vibrierende Anlagenkomponenten nun kostengünstig möglich, was folgendes Beispiel illustriert.
Fertigungskompetenz bei Durchflussmessgeräten
Das Siemens-Werk im französischen Haguenau, das 2020 sein 50-jähriges Bestehen feierte, beschäftigt über 800 Mitarbeiterinnen und Mitarbeiter. Das Werk ist auf die Fertigung von Druckmessgeräten, Durchflussmessgeräten und Gasanalysatoren spezialisiert und wurde für seine innovativen Ansätze zur digitalen Transformation ausgezeichnet: Seit 2015 hat das Werk seine Produktion durch Automatisierung, Robotik und Digitalisierung kontinuierlich optimiert. Produktionsprozesse können nun in Echtzeit simuliert und effizienter gestaltet werden.
Hier koordiniert Robert Gerber die Instandhaltung, sein Kollege David Uhrig ist als Wartungsplaner zuständig. „In Sachen Instandhaltung haben wir in den letzten Jahren große Schritte nach vorne gemacht“, erklärt Uhrig, der seit 1995 zunächst als Wartungstechniker und dann als Wartungsplaner im Werk Haguenau arbeitet: „Unsere Instandhaltungsteams tragen dazu bei, dass sich die Effizienz der Anlagen von Jahr zu Jahr verbessert. Wir überwachen die Produktionsanlagen rund um die Uhr und profitieren heute von Diagnosemöglichkeiten, die die Ausrüstung vor einigen Jahren noch nicht bieten konnte.“ Die Wartungsstrategien variieren von Anlagenteil zu Anlagenteil, wie Gerber berichtet: „Man kann sagen, dass wir uns täglich im Spannungsfeld zwischen Wollen und Können befinden: Aufgrund von Kritikalitätsanalysen wissen wir natürlich, welche Anlagenteile bei einem Ausfall welche Auswirkungen auf die Betriebsleistung haben und worauf wir dementsprechend ein besonderes Augenmerk legen müssen. Andererseits können wir nicht für alle Anlagen vorausschauende Instandhaltungsstrategien entwickeln, da uns die Zustandsdaten fehlen.“
Bei den meisten kritischen Anlagenteilen liegen entsprechende Ersatzteile bereit, aber das allein schützt nicht vor Anlagenstillständen: „Nehmen wir unseren Autoklav als Beispiel“, erläutert Gerber: „Sämtliche Durchflussmesser haben eine spezielle Innenbeschichtung, die im Autoklav vulkanisiert wird. Fällt er aus, steht die Produktion. Kritisch ist hier der Motor für das Gebläse, also haben wir den bei uns im Lager. Das Problem bei plötzlichem Ausfall ist aber, dass das Lüfterrad ohne Kupplung auf der Motorachse befestigt ist. Das bedeutet trotz Ersatzteil zwei Tage Aufwand und der Einsatz von Spezialisten.“
Condition-Based Monitoring zum Nachrüsten
Für diesen Motor wünschten sich die beiden Instandhaltungsspezialisten eine zustandsorientierte Überwachungsmöglichkeit und wurden im eigenen Haus fündig: Sitrans Smart Condition Monitoring IQ (SCM IQ), entwickelt von der Siemens AG, ist ein intelligentes System zur kontinuierlichen Überwachung und Wartung von rotierenden oder vibrierenden Maschinenkomponenten. Es nutzt eine Kombination aus IIoT-Sensoren und künstlicher Intelligenz, um Schwingungs- und Temperaturdaten kontinuierlich zu erfassen und zu analysieren.
Die Multisensoren Sitrans MS200 werden direkt an den betreffenden Anlagenkomponenten montiert. Sie zeichnen sich durch ihre Robustheit und ihr IP 69-geschütztes Gehäuse aus, das einen sicheren Betrieb unter industriellen Bedingungen gewährleistet. Eine Verkabelung der batteriebetriebenen Sensoren ist nicht notwendig, da die Datenübertragung über Bluetooth Low Energy (BLE) zu den Sitrans CC220 Gateways erfolgt. Diese Gateways sammeln die Daten der Multisensoren und leiten sie an die Cloud-Anwendung weiter. Sie sind Teil der umfassenden systeminternen Security-Maßnahmen, die eine durchgängige Verschlüsselung von der Sensor- bis zur Anwendungsebene beinhalten.
Die oberste Ebene bildet die Cloud-Anwendung Sitrans SCM IQ App. Sie nutzt künstliche neuronale Netze, um die gesammelten Daten kontinuierlich zu analysieren und mögliche Abweichungen von den Normalwerten zu identifizieren. Wird eine solche Anomalie erkannt, die auf einen drohenden Ausfall hindeutet, gibt das System eine Warnung aus. Diese Früherkennung ermöglicht eine zustandsbasierte vorausschauende Wartung, die letztlich zu einer deutlichen Verbesserung der Anlagenleistung führt.
„Wir sind von der Benutzerfreundlichkeit des Systems begeistert“, berichtet Uhrig, „die Installation und Inbetriebnahme der Hardware dauert maximal eine Stunde. Sein Kollege Gerber ergänzt: „Danach macht das System alles selbstständig. Innerhalb von zwei bis vier Betriebswochen lernt Sitrans SCM IQ die typischen Betriebszustände der überwachten Anlagenkomponenten kennen. Dieses Wissen nutzt es, um Anomalien zu erkennen und entsprechende Warnungen auszugeben. Wird eine Anomalie erkannt, erhält der zuständige Wartungsspezialist eine Benachrichtigung“. In den meisten Fällen ist die Abweichung ein frühzeitiger Hinweis auf ein schleichend ernster werdendes Problem. Mit diesen Informationen kann Wartungsplaner Uhrig sein Team und die Instandhaltungsmaßnahmen rechtzeitig planen: „Nun kann ich den entsprechenden Spezialisten zum Austausch des Lüftermotors für unseren Autoklav frühzeitig buchen und den Austausch auf ein Wochenende legen. Damit ist die Produktion in keiner Weise unterbrochen.“
Kalibrierstände mit integrierter Pumpenüberwachung
Sitrans SCM IQ spielt in Haguenau auch an einem anderen kritischen Punkt der Produktion eine entscheidende Rolle, wie Gerber erklärt: „Die Kalibrierung unserer Durchflussmessgeräte ist ein unverzichtbarer Teil der Qualitätssicherung während der Produktion und vor der Auslieferung an den Kunden. Sie stellt sicher, dass jedes Gerät präzise Messungen vornimmt.“ Dieser Schritt erfolgt auf hoch spezialisierten Kalibrierständen, die so konstruiert sind, dass genaue und wiederholbare Bedingungen geschaffen werden, unter denen die Messfähigkeit der Durchflussmessgeräte geprüft werden kann.
„Dabei spielen bei uns acht Pumpen für unterschiedliche Durchflussmengen eine entscheidende Rolle“, erklärt Uhrig: „Sie sind dafür verantwortlich, dass die Flüssigkeit mit der vorgegebenen Rate durch das Messgerät fließt. Da die Genauigkeit des Kalibrierprozesses stark von der Präzision der Pumpe abhängt, setzen wir hochgenaue und sehr zuverlässige Pumpen ein, die zum Teil so viel kosten wie ein Mittelklassewagen - so etwas halten wir nicht auf Lager." Kollege Gerber weiß aus leidvoller Erfahrung: „Bei solchen Spezialpumpen und solchen Preisen ist ein ungeplanter Ausfall leider eine Sache von mehreren Wochen, denn auch die Pumpenhersteller haben solche Aggregate nicht auf Lager. Bis geliefert werden kann, steht bei uns ein Großteil der Produktion still, denn ohne Kalibrierung können wir unsere Geräte nicht ausliefern. In einer solchen Situation ist man also in einer denkbar schlechten Verhandlungsposition.“
Eine kontinuierliche zustandsorientierte oder gar vorausschauende Überwachung der Pumpen war bisher nicht möglich. Mit großem Aufwand wurden die Aggregate lediglich mithilfe mobiler Sensoren jährlich überprüft. Mit Sitrans SCM IQ ist dies nun ohne weiteres rund um die Uhr gegeben: „Wir sind jetzt beispielsweise in der Lage, eine Unwucht an der Motorwelle oder am Rotor durch die Analyse der Schwingungsdaten frühzeitig zu erkennen“, erklärt Instandhaltungsleiter Gerber: „Unwuchten führen mit der Zeit zu erhöhten Schwingungen und unruhigem Lauf, was wiederum zu erhöhtem Verschleiß und letztlich zum Ausfall des Motors führt. Unser nachgerüstetes Condition-Based Maintenance-System liefert uns heute sehr genaue Informationen und weist uns rechtzeitig auf solche Verschleißerscheinungen hin. Das hat unsere Instandhaltung, unser Ersatzteilmanagement und unsere gesamte Planung auf ein ganz neues, effizienteres Niveau gehoben."
Sitrans SCM IQ ist eine Komplettlösung, die von der Datenerfassung über die Analyse bis hin zur rechtzeitigen Benachrichtigung über Wartungsmaßnahmen eine effiziente, effektive und sichere Methode zur Überwachung rotierender oder vibrierender Maschinenkomponenten bietet. Sie verleiht den ansonsten stummen Anlagenkomponenten nun eine Stimme, die über den aktuellen Zustand genau informieren kann.