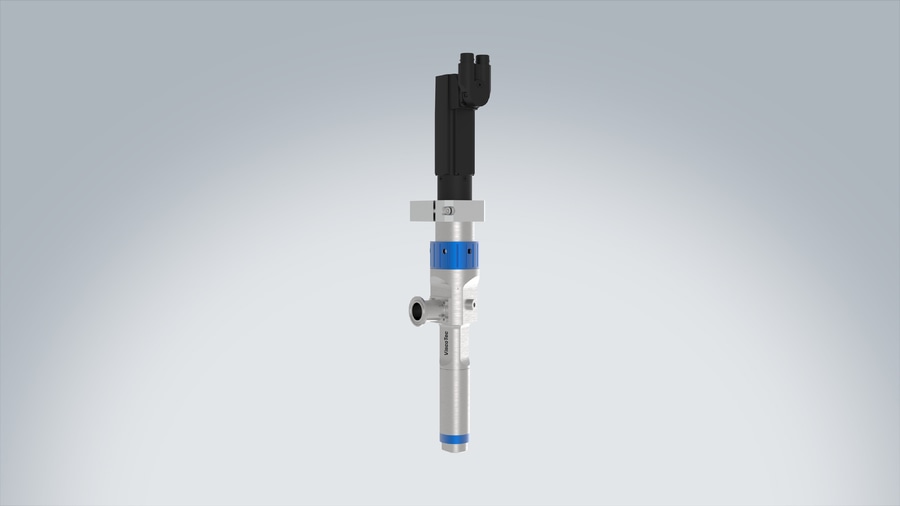
#Neues aus der Industrie
Einflussfaktoren bei der Produktion von Lithium-Ionen-Batterien
Kritische Parameter erfordern Entwicklungskompetenz bei Dosiertechnologien
Heute so, morgen anders: In Sachen Elektromobilität herrscht in der Gegenwart eine hohe Entwicklungsdynamik. Hersteller von Lithium-Ionen- Batterien und OEM wissen, dass bei allen technischen Änderungen eine Sache immer gleichbleiben muss, um im internationalen Wettbewerb zu bestehen: die Zellqualität. Damit die aber auch bei Veränderungen in den komplexen Fertigungsprozessen immer gewährleistet ist, braucht es interdisziplinäres gewachsenes Know-how. ViscoTec garantiert das und bietet im Bedarfsfall jedem Kunden individuelle technische Anpassungen. Das Ziel: Über eine Modifikation des Designs jedem Kunden die für ihn optimale Elektrolytbefüllung garantieren. Keine leichte Aufgabe, denn Elektrolyte sind ein komplexes Medium.
Gigafactories fertigen Zellen in immer kürzeren Taktzeiten – 40 Zellen pro Minute sind inzwischen keine Seltenheit mehr. Vor diesem Hintergrund sind Unternehmen gezwungen, der Befüllung und Benetzung besondere Aufmerksamkeit zu schenken, da beide Prozessschritte in der Zellassemblierung zu den zeit- und qualitätskritischsten zählen.
Während die Befüllung den Vorgang beschreibt, bei dem das Elektrolyt unter Vakuum in eine Batteriezelle eingefüllt wird, steht das so genannte Benetzen – auch Wetting genannt – für das Eindringen des Elektrolyten in die poröse Struktur von Elektrode und Separator – der elektrische Kontakt über Ionenaustausch entsteht.
Der Elektrolyt der Lithium-Ionen-Batteriezelle besteht aus einem Lösemittel in Form von Ethylen-Carbonat, Propylen-Carbonat oder Dimethyl-Carbonat, das mit Lithiumsalz ergänzt wird. Das am häufigsten verwendete Lithiumsalz Lithiumhexafluorphosphat (LiPF6), ist ein wichtiges Material in den Elektrolyten verschiedener Li-Ionen-Batterien und macht etwa 43 % der Gesamtkosten des Elektrolyten aus. Verglichen mit anderen Elektrolyten weist Lithiumhexafluorphosphat bessere Eigenschaften hinsichtlich Löslichkeit, Leitfähigkeit, Sicherheit und Umweltfreundlichkeit in organischen Lösungsmitteln auf und ist derzeit das beliebteste Lithiumsalz für Elektrolyte.
ViscoTec hat die Dosiertechnik speziell auf diese Elektrolyte mit einer Viskosität von ~ 100 – 250 mPas @20°C und einer Dichte von ~1,1 – 1,3 g/cm³ ausgelegt und nutzt ausschließlich prozessfreundliche Materialien, die auch unter anspruchsvollen Bedingungen lange Standzeiten garantieren.
Das ist vor allem deshalb wichtig, da der Elektrolyt nicht ohne Nachteile ist: Er reagiert schon bei geringer Luftfeuchtigkeit und bildet dann die lebensgefährliche Flusssäure. Sie kann – da lipophil – selbst bei geringer Exposition über Haut oder Schleimhaut zu einem fast unmittelbaren Tod führen. In der Tiefe des Gewebes bildet sich schwer lösliches Calcium- und Magnesiumfluorid, was den Elektrolythaushalt massiv schädigt.
Deshalb findet die Elektrolytbefüllung in Trockenräumen statt. Die hier erzeugte trockene Luft entzieht den Materialien die Feuchtigkeit. Aufgrund ihrer technischen Auslegung sind diese Räume extrem kostenintensiv. Eine prozessstabile Dosiertechnologie mit langen Standzeiten ist vor diesem Hintergrund wichtiger Baustein für die Anlagenplanung und den Gesamtprozess, der mit dem Befüllen und Benetzen zwei Prozessschritte beinhaltet, deren Qualität maßgeblich durch die Dosiertechnologie beeinflusst werden kann.
Dabei weist das Befüllen von Hardcase-Zellen ein kritisches Momentum auf: Zeit.
Bei einem Metallgehäuse ist die Dosiergeschwindigkeit limitiert, um zu hohe Dosierdrücke zu vermeiden. Diese können zur Zerstörung der Zellwicklung führen. Anders bei Pouch Zellen: eine Erhöhung der Geschwindigkeit führt hier lediglich zur kurzzeitigen Ausdehnung der Hülle. Anlagenbauer müssen deshalb bei der Planung von Fertigungsstrecken für die Befüllung von Metallgehäusen Konzepte für die parallele oder mehrfache Befüllung einplanen.
Nicht weniger zeitkritisch ist das Benetzen: Aufgrund der Porosität der Elektroden und des Separators muss die vollständige Benetzung einer großen Fläche schnell erfolgen. In Abhängigkeit von der Zellgröße dauert dieser Vorgang aber zwischen 10 und durchaus auch 45 min und mehr (für größere prismatische- oder Pouchzellen). Deshalb entwickeln Zellhersteller Materialien für Separatoren, welche schneller aufnahmefähig sind.
Sowohl Befüllung als auch Benetzung beeinflussen die Leistung einer Batterie: Sind Bereiche nicht vollständig benetzt, kann kein Ladungsaustausch erfolgen – Bereiche sind dann inaktiv und Qualitätseinbußen die Folge. Nicht zu vergessen das Sicherheitsrisiko: Durch die nicht benetzten Bereiche fließen in der Zelle unterschiedliche Ströme. Die Folge: Dendritenwachstum, was zu Kurzschlüssen und zur Zerstörung der Zelle führen kann.
Davon ausgehend, dass die Nachfrage an Zellen weiter zunimmt, entwickelt der Dosierspezialist ViscoTec seine Technologien kontinuierlich weiter. Das Ziel: OEM und Zellhersteller sollen künftig die Fertigung von Li-Ionen Zellen sicherer, performanter und mit gleichbleibend hoher Qualität realisieren können.