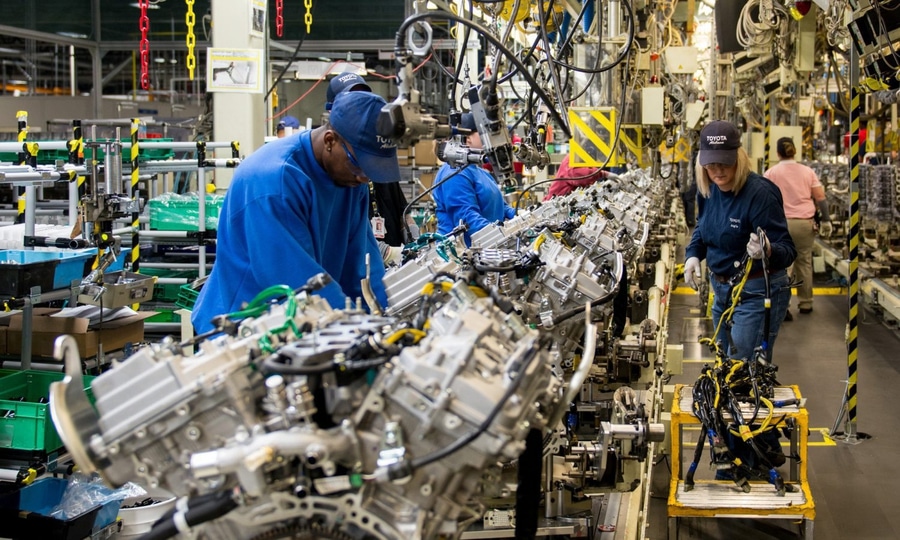
Automatische Übersetzung anzeigen
Dies ist eine automatisch generierte Übersetzung. Wenn Sie auf den englischen Originaltext zugreifen möchten, klicken Sie hier
#Neues aus der Industrie
Toyota-Motorenwerk senkt Energiekosten mit neuer Steuerung für Luftkompressoren
Neue Kontrollen sparen jährlich 1 Million Kilowattstunden ein und unterstützen die Null-Emissions-Ziele von Toyota.
Sie haben von emissionsfreien Fahrzeugen gehört. Aber was ist mit der emissionsfreien Fahrzeugproduktion? Das ist die Vision von Toyota, einem der größten Automobilhersteller der Welt. Seine Toyota-Umweltherausforderung 2050 fordert das Unternehmen auf, die CO2-Emissionen seiner weltweiten Produktionsstätten bis 2050 zu eliminieren.
Um diese ehrgeizigen Ziele zu erreichen, unternimmt Toyota Schritte zur Senkung seines Energieverbrauchs und zur Umstellung auf wiederverwendbare Energie. Und wie sich im Werk des Unternehmens in Huntsville, Alabama, zeigt, tragen diese Bemühungen dazu bei, dass Toyota nicht nur seinen ökologischen Fußabdruck verkleinert - sie kommen auch dem Endergebnis zugute.
Aufgeblasene Energiekosten
Das Werk in Huntsville stellt Motoren für beliebte Toyota-Fahrzeuge wie den Tacoma, Tundra und Highlander her. Die Arbeiter im Werk erhalten Motorkomponenten, die in anderen Werken gegossen wurden, um sie zu bearbeiten und zu den Motoren zusammenzubauen, die in die Fahrzeuge anderer Werke eingebaut werden.
Das Luftverdichtungssystem der Anlage ist für den Produktionsprozess von entscheidender Bedeutung. Das System besteht in erster Linie aus fünf großen Zentrifugal-Luftkompressoren und versorgt die 1,2 Millionen Quadratfuß große Anlage mit Luft für verschiedene Maschinenprozesse, Automatisierung und Trocknungsmotorkomponenten.
Druckluft-(CA)-Systeme sind von Natur aus energieintensiv. Das System im Werk Huntsville bildet da keine Ausnahme; es macht 25% der jährlichen Energiekosten des Werks aus.
Die veralteten Steuerungen machten das System zu einem noch größeren Energieverbraucher, als es nötig gewesen wäre. Die veralteten Steuerungen starteten die Kompressoren nur langsam und erlaubten es ihnen nicht, als integriertes System zusammenzuarbeiten, und sie verfügten nicht über genügend CA-Speicher, aus dem sie bei hohem Spitzenluftbedarf schöpfen konnten.
Aufgrund dieser Einschränkungen mussten die Teammitglieder die Kompressoren die meiste Zeit des Tages mehr als nötig in Betrieb halten, um genügend Luftkapazität für kurze, gelegentliche Nachfrageschübe in der Anlage zu gewährleisten. Eddy Kiggen, ein Anlagenspezialist bei Toyota, erklärt dies,
"Wir brauchen mindestens 81 PSI, damit die Maschinen ohne Unterbrechung laufen können. Aber weil die Kompressoren so viel Zeit zum Hochfahren brauchten, mussten wir 91 PSI beibehalten, nur um sicherzustellen, dass wir bei 81 PSI niedrigem CA-Druck nicht ausfallen
Der Stromvertrag für die Anlage brachte weitere Herausforderungen mit sich. Der Vertrag berechnet mehr für Energie, die während der Spitzenverbrauchszeiten verbraucht wird. Wenn die Teammitglieder in diesen Zeiten einen der großen Kompressoren starten mussten, um die Kapazität der Anlage aufrechtzuerhalten, konnte ein einziger Maschinenstart die Stromrechnung der Anlage um 100 % der Energiekosten für einen Tag erhöhen.
Lokale und anlagenweite Upgrades
Um zur Eindämmung der Energiekosten beizutragen und seine Energieinitiative 2050 zu unterstützen, beschloss Toyota Motor Manufacturing, Alabama (TMMAL), die Luftkompressor-Steuerungssysteme des Werks zu modernisieren.
Für die Aufgabe wandten sie sich an IZ Systems and Case Engineering, einen Maschinenbauer, der Partner im Rockwell Automation PartnerNetwork-Programm ist. Das Unternehmen lieferte eine zweiteilige Lösung, die lokale und anlagenweite Steuerungen umfasste.
Vor Ort migrierte Case die Steuerungen der fünf großen Kompressoren auf seine AirLogix-Steuerungslösung. Die Lösung basiert auf der CompactLogix-Steuerungsplattform und umfasst eine PanelView Plus 7-Bedienerschnittstelle, über die die Mitarbeiter Leistungs- und Diagnosedaten an jedem Kompressor abrufen können.
Auf Werksebene nutzte Case seine AirMaster-Lösung zur Lastverteilung, um ein Master-Luftregelungssystem zu schaffen. Diese Lösung basiert auf der ControlLogix-Plattform und verwendet die Software FactoryTalk View SE zur Datenerfassung und Visualisierung. Case arbeitete mit IZ Systems zusammen, die auch einen 5.000-Gallonen-Lagertank für eine erhöhte CA von 500 PSI installierten, um die Systemwiederherstellungszeit ohne Störungen zu ermöglichen.
Ein modulierendes Ventil liefert Luft während Zeiten mit hohem Luftbedarf. Diese gespeicherte Luft sorgt für einen reibungslosen Übergang, wenn eine zusätzliche Zentrifugenmaschine erforderlich ist, um den Luftbedarf der Anlage zu decken.
Ersparnisse aufleben lassen
Die neuen, effizienteren Luftkompressorsteuerungen haben dem Werk Huntsville geholfen, den jährlichen Energieverbrauch um fast 1 Million Kilowattstunden pro Jahr oder etwa 68.000 US-Dollar pro Jahr zu senken. Darin nicht eingeschlossen sind die Einsparungen, die durch die Vermeidung von Inbetriebnahmen während der Spitzenlastzeiten erzielt wurden.
Infolgedessen erholte sich das Werk schneller von seinen Investitionen in die neuen Steuerungen als das Ziel von zwei Jahren. Das sagte Kiggen,
"Wir konnten unseren Sollwert für das System von 91 auf 85 PSI reduzieren. Darin liegt der größte Teil der Einsparungen bei diesem Projekt"
Die aktualisierten Vor-Ort-Steuerungen tragen dazu bei, dass die Kompressoren effizienter als die alten Steuerungen arbeiten, indem sie die Drosselkapazität jeder Maschine erhöhen. Die neue Hauptsteuerung überwacht den Druck und der Luftstrom startet oder stoppt die Kompressoren entsprechend dem Bedarf. Sie entnimmt CA aus dem Hochdruckspeichertank, während ein Kompressor in Betrieb ist, durchläuft Bedarfsschwankungen und schützt vor potenziellen Problemen.
"So, wie es jetzt aufgebaut ist, haben wir immer genug Druck im Speichertank für eventuelle Einbrüche oder Kompressorausfälle. Selbst wenn der nächste Kompressor, den wir zu starten versuchen, ausfällt, können wir einen weiteren Kompressor starten, und die Leute im Werk werden nicht wissen, dass etwas passiert ist
Das neue System liefert den Arbeitern Trendinformationen zur Überwachung von Luftdruck und -fluss, Energieverbrauch und kritischen Daten an jeder Maschine, einschließlich Vibrationen. Und da diese Informationen nahezu in Echtzeit zur Verfügung stehen - etwas, worüber die Teammitglieder bisher nicht verfügten - hilft es bei der Analyse des CA-Systems und bei der Fehlersuche.
Die Teammitglieder können die Informationen als Teil ihrer routinemäßigen Betriebsüberwachung vor Ort an jeder Maschine einsehen. Toyota und Case Engineering können sie per Fernzugriff von überall her einsehen.
"Nach der Elektrizität ist die Luft unser wichtigster Energieträger, deshalb behalten wir sie genau im Auge. Ich schaue mir täglich die Daten an, um zu sehen, wie das System funktioniert und um seine Effizienz zu überprüfen. Ich erhalte eine Textnachricht, wenn wir ein Problem haben, wie z.B. einen Druckabfall oder wenn der Speichertank unter ein bestimmtes Niveau fällt. Wir mögen es auch, wenn Case angeschlossen ist und sie über ein Problem informiert, so dass sie online gehen können, um das Problem sofort zu beheben"
Toyota versucht, dieses Projekt an anderer Stelle zu replizieren, um ähnliche Energieeinsparungen zu erzielen und gleichzeitig weiterhin auf Null CO2-Emissionen hinzuarbeiten.
"Null CO2 beim Bau eines Fahrzeugs zu produzieren, ist eine sehr große Aufgabe. Im Moment versuchen wir, so viel Energie wie möglich zu sparen, bevor wir in die erneuerbaren Energien einsteigen. Und für diese Anlage sind diese Steuerungs-Upgrades die erfolgreichsten Energieprojekte, die wir seit langer Zeit durchgeführt haben
Die oben genannten Ergebnisse sind spezifisch für die Verwendung von Rockwell Automation-Produkten und -Dienstleistungen durch Toyota in Verbindung mit anderen Produkten
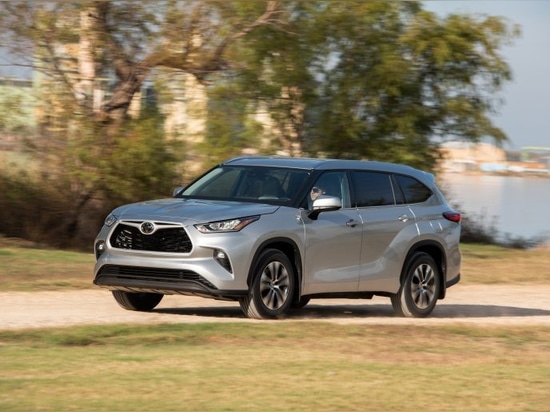
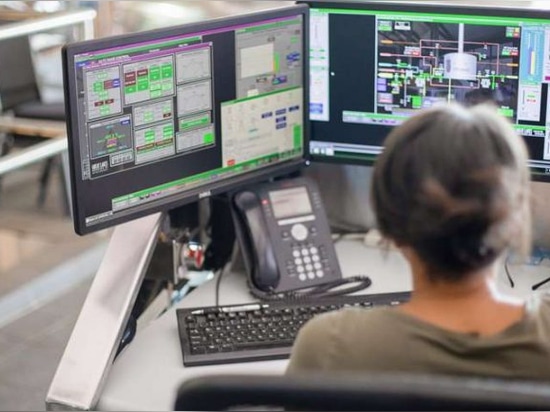
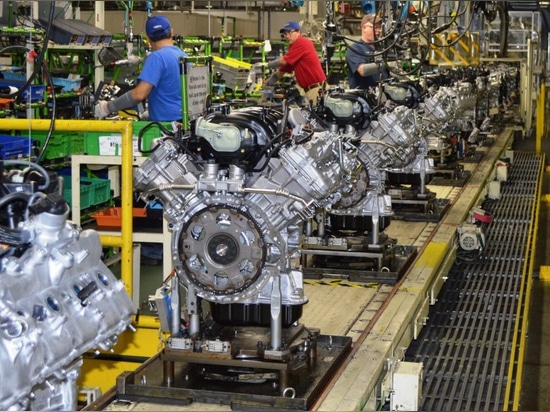
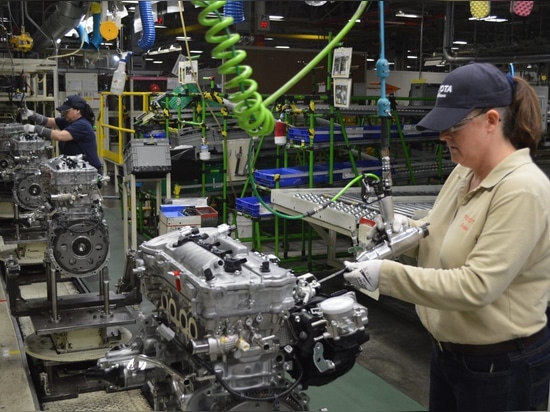