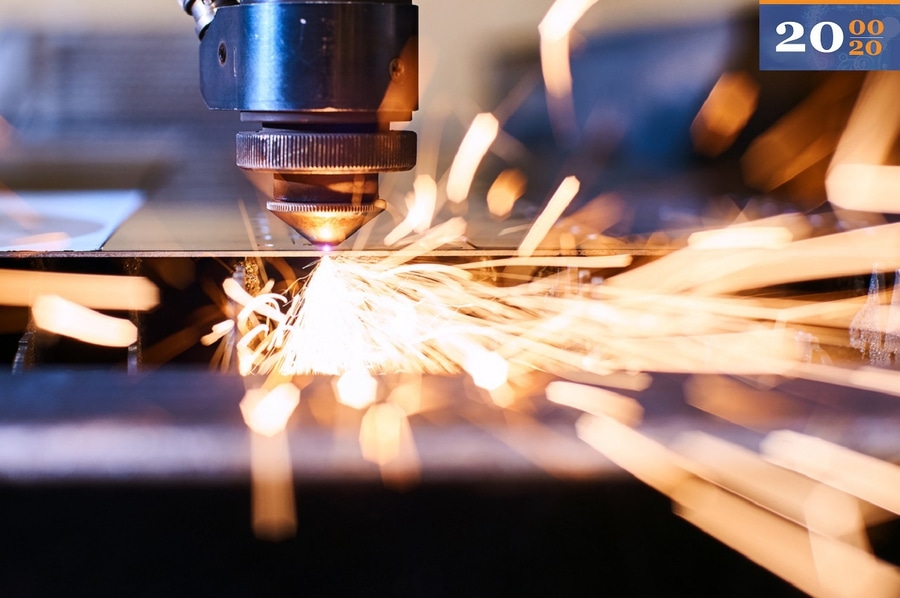
Automatische Übersetzung anzeigen
Dies ist eine automatisch generierte Übersetzung. Wenn Sie auf den englischen Originaltext zugreifen möchten, klicken Sie hier
#Neues aus der Industrie
CECIMO: "Die große Revolution für die Werkzeugmaschinenindustrie ist die Digitalisierung"
Anlässlich des 20-jährigen Jubiläums unseres Verlags, des branchenspezifischen Beschaffungsunternehmens DirectIndustry, feiern wir 20 Jahre industrielle Innovationen, indem wir den Akteuren das Wort erteilen, die diese Innovationen ins Leben gerufen haben.
In diesem Interview konzentrieren wir uns auf Werkzeugmaschinen. Filip GEERTS, Generaldirektor, CECIMO - Europäischer Verband der Werkzeugmaschinenindustrie und verwandter Fertigungstechnologien, gibt Einblicke in 20 Jahre Innovationen bei Werkzeugmaschinen.
20 Jahre MASCHINENWERKZEUGE mit CECIMO
Cecimo ist ein europäischer Dachverband der Werkzeugmaschinenhersteller, der aus 15 nationalen Verbänden besteht und etwa 1.300 Industrieunternehmen in Europa vertritt. Die Organisation konzentriert sich darauf, ideale wirtschaftliche Bedingungen für die Werkzeugmaschinenindustrie als Voraussetzung für Innovationen zu schaffen, mit dem Ziel, den europäischen Werkzeugmaschinenherstellern zu helfen, ihre weltweite Führungsposition auszubauen.
Zeitschrift DirectIndustry: Was war die große Revolution der Werkzeugmaschinen in den letzten 20 Jahren?
Filip GEERTS: Die GROSSE Revolution der letzten 20 Jahre ist die Digitalisierung. Die Digitalisierung (einschließlich künstlicher Intelligenz) schafft neue Möglichkeiten und verändert zunehmend alle Segmente der Fertigung, von der Konstruktion bis zur Wartung. Sie ist eine treibende Kraft bei der Optimierung der Geschäfts- und Energieeffizienz. Die Digitalisierung führt auch zur Entwicklung neuer Geschäftsmodelle und neuer datengesteuerter Dienste, zum Beispiel der vorausschauenden Wartung
Zeitschrift DirectIndustry: Werkzeugmaschinen sind eine Branche, die sich normalerweise langsam entwickelt. Aber es scheint, dass sich in 20 Jahren viel verändert hat. Was meinen Sie dazu?
F.G.: In der Tat haben sich die Dinge in 20 Jahren sehr viel verändert. Um ein Beispiel zu nennen: Die Verwendung von Additive Manufacturing (AM) nimmt in vielen Sektoren zu, aber ihre Verwendung ist noch nicht weit verbreitet. Additive Technologien bieten ein großes Potenzial und viele Vorteile, zum Beispiel bei der Gewichtsreduzierung von Komponenten, der Möglichkeit, komplexe Teile herzustellen, und der kundenspezifischen Anpassung. Dennoch ist in vielen Fällen eine Art subtraktive Nachbearbeitung erforderlich, bevor das Teil fertiggestellt werden kann. AM wird die subtraktive Fertigung nicht ersetzen, aber es wird notwendig sein, von den Vorteilen sowohl der additiven Verfahren als auch der traditionellen Werkzeugmaschinen zu profitieren und sie in eine Prozesskette oder in Hybridmaschinen zu integrieren.
Zwei weitere Trends sind Robotik und Automatisierung, die die Fertigung in Richtung der so genannten "Fabriken der Zukunft" führen. In der Werkstatt können Roboter in den Produktionsprozess integriert werden, während die Kernbearbeitungs- und Zerspanungsaktivitäten der Werkzeugmaschine überlassen werden. Sie sind nützlich, um Techniker bei Aufgaben wie der Handhabung zu unterstützen, und können die Produktivität der gesamten Werkstatt steigern. Als eine Branche, die ständig auf Innovation setzt, sieht der europäische Werkzeugmaschinensektor diese Trends positiv. Alle Zutaten, um im Zentrum der Bühne der "Fabriken der Zukunft" zu stehen, sind in Europa vorhanden, wo eine ganze Reihe neuer Technologien, einschließlich der in Europa entwickelten, miteinander interagieren werden. Die Interaktion zwischen modernsten CNC-Maschinen und Robotern ist ein Beispiel dafür.
Zeitschrift DirectIndustry: Konzentrieren wir uns auf AM. Wie können Sie ihre Auswirkungen auf den Sektor bewerten?
F.G.: Neue Industrien haben begonnen, die AM zu nutzen, da sie die vielen Vorteile entdecken, die sie für ihr Geschäft mit sich bringt. Was die Anwendungen betrifft, so war die Luft- und Raumfahrt ein Early Adopter und wird auch weiterhin einer der wichtigsten Sektoren für AM sein. Viele Unternehmen in diesem Sektor haben die Flexibilität und Effizienz der von AM angebotenen Geometrie genutzt, um erhebliche Mengen an unnötigem Material zu eliminieren. Andere Sektoren, wie z.B. der Bau- und Energiesektor, haben damit begonnen, AM verstärkt einzusetzen und von der hohen Komplexität, Widerstandsfähigkeit und Qualität zu profitieren. AM kann die Lieferketten vieler Sektoren potenziell verändern. Zwei Aspekte, die einen wesentlichen Einfluss auf das künftige Wachstum von AM haben könnten, sind die Entwicklung harmonisierter Normen und qualifizierter Arbeitskräfte. Die Standardisierung ist ein entscheidendes Element für die Industrialisierung der AM in Europa. In der jüngsten Vergangenheit haben wir die wachsende Beteiligung mehrerer AM-Akteure an Normungsorganisationen (sowohl auf ISO- als auch auf CEN-Ebene) beobachtet, weshalb die Entwicklung von Normen einen großen Auftrieb erhalten hat. Der Mangel an Fähigkeiten im Bereich der AM bleibt eines der größten Hindernisse für das Wachstum des Sektors. Es besteht die dringende Notwendigkeit, den Pool der europäischen Arbeitnehmer, die mit AM-Maschinen arbeiten können, zu erweitern
Zeitschrift DirectIndustry: Hybridbearbeitung gab es vor 20 Jahren noch nicht. Was können Sie zu dieser Entwicklung sagen?
F.G.: Hybride Werkzeugmaschinen, die CNC und AM enthalten, könnten den nächsten Schritt in der Entwicklung der Werkzeugmaschinenindustrie darstellen. Der 3D-Druck nimmt rasch zu, und 3D-Drucker werden zu wichtigen CNC-Werkzeugen. Es gibt immer noch einige Einschränkungen, weil das 3D-Drucken mit Metallen im Allgemeinen voraussetzt, dass das Metall irgendwann im Prozess gesintert oder geschmolzen wird, was zu mechanischen Eigenschaften führt, die sich sehr von denen eines aus einer gewalzten oder wärmegehärteten Legierung bearbeiteten Stücks unterscheiden können. An diesem Punkt besteht die Herausforderung des 3D-Druckverfahrens darin, die präzisen Toleranzen einer hochpräzisen Bearbeitung einzuhalten. Daher ist es wahrscheinlicher, dass in der Werkstatt 3D-Drucker Seite an Seite mit traditionelleren CNC-Maschinen arbeiten, anstatt sie vollständig zu ersetzen. Es gibt jedoch auch einige bedeutende Vorteile: Kostensenkung (z.B. Verringerung des Materialausschusses, Verringerung des Arbeitsaufwands und die Möglichkeit mehrfacher Konstruktionsänderungen); verbesserte Funktionalität (z.B. die Möglichkeit, Werkzeugvorrichtungen herzustellen, die mit herkömmlichen Fertigungstechniken nicht realisierbar sind); und erhöhte Anpassungsfähigkeit.
Zeitschrift DirectIndustry: Zerspanung bedeutet Abfall und heute, im Vergleich zu vor 20 Jahren, ist die Erreichung einer klimaneutralen Industrie ein Ziel. Welche Technologien wurden eingesetzt, um Werkzeugmaschinen umweltfreundlicher zu machen?
F.G.: Der Werkzeugmaschinensektor ist ein Anbieter von fortschrittlichen Fertigungstechnologien, die zu einem kreisförmigeren und nachhaltigeren Sektor beitragen. Ein Beispiel für eine solche Entwicklung ist die Laser-Oberflächentexturierung. Mehr als 80% der Texturen in der Fertigung werden durch chemisches Ätzen erzeugt. Laser-Texturierungstechnologien bieten eine sauberere Alternative zu Ätzprozessen und erzeugen 3D-Texturen direkt aus digitalen Daten. Dies bedeutet keine Verwendung von Chemikalien, einen zu 100 % wiederholbaren und vereinfachten Prozess, einen geringeren Ausschuss und einen vollständig digitalen Prozess: all dies trägt zu einer nachhaltigeren Produktion und nachhaltigeren Produkten bei. Diese Entwicklungen tragen auch dazu bei, Teile während ihrer gesamten Lebensdauer mit überlegener Effizienz herzustellen. Ein Beispiel ist die Benzin-Direkteinspritzung (GDI). Die Entwicklung der GDI war nur mit der Entwicklung einer neuen Fertigungstechnologie, dem Femtosekunden-Laserbohren, möglich. Aber es sind nicht nur Hardware-Entwicklungen, die die zirkulare Fertigung vorantreiben können. Tatsächlich kommen die größten Entwicklungen von der Software. Durch Software-Entwicklungen konnten 30 bis 50% Effizienzgewinne erzielt werden.
Zeitschrift DirectIndustry: Neue Materialien wie Verbundwerkstoffe sind ebenfalls erschienen. Wie haben sie sich auf die Werkzeugmaschinenindustrie ausgewirkt?
F.G.: Neue Materialien stellen, wenn man die Hauptkunden der Hersteller, also den Automobilsektor, die Luft- und Raumfahrt und die Medizinbranche, als neue Herausforderungen, aber auch als Chancen betrachtet. Die ersten beiden Sektoren benötigen leichte und sehr widerstandsfähige technische Strukturen mit manchmal komplexer Form, um das Gewicht, den Materialbedarf und den Energieverbrauch ihres Endprodukts zu reduzieren. Der medizinische Sektor benötigt neue Materialien, die mit Beschichtungen auf Nanopartikel-Ebene biokompatibel sind. Die Herstellung dieser fortschrittlichen Teile wirkt sich auf jeden Aspekt des Produktionsprozesses aus: Massenanpassung, Entwicklung rekonfigurierbarer Maschinen, weitere Verbesserung der Sensoren, Automatisierung usw. Im Wesentlichen werden fortschrittlichere Materialien zweifellos zur Entwicklung innovativerer Maschinen führen
Zeitschrift DirectIndustry: Digitale Simulation gab es vor 20 Jahren auch noch nicht: Jetzt können wir Schnitte simulieren, bevor sie passieren.
F.G.: Schnelle und genaue digitale Simulationen sind zu einem Muss für Hersteller geworden, die das Beste aus intelligenten Fertigungsinitiativen machen wollen. Hersteller müssen kostspielige Programmierfehler vermeiden, die katastrophale Schäden sowohl an Werkzeugmaschinen als auch an teuren Werkstücken verursachen könnten. Selbst ein kleiner Programmierfehler, zum Beispiel im Fall eines Luft- und Raumfahrtteils, kann zu einer großen Ausgabe werden. Um solche Fehler zu vermeiden, ist es entscheidend geworden, eine hohe Qualität durch den Einsatz der digitalen Simulation sicherzustellen, zum Beispiel um den Schnitt korrekt einzurichten. Einige der Hindernisse im Zusammenhang mit der digitalen Simulation betreffen jedoch den Zugang zu genauen Volumenmodellen der Werkzeugmaschinen, die hohe Anzahl von Optionen in der Maschinenhardware und Werkzeugbestückung sowie Leistung versus Genauigkeit. Zwei Trends, die derzeit in der digitalen Simulation an Dynamik gewinnen, sind das Maschinenbewusstsein und der Drang nach interaktiven Daten. Die Branche hat in den letzten Jahren dramatische Fortschritte in diesem Bereich erlebt, aber es bleibt noch einiges zu tun. Außerdem kann der Bediener durch die Prozessüberwachung und -steuerung den gesamten Prozess überwachen, anstatt das Teil am Ende des Prozesses zu prüfen. Der Prozess kann dann bei laufendem Betrieb korrigiert werden, was zu weniger Abfall und mehr Effizienz führt.
Zeitschrift DirectIndustry: Neue Akteure aus Taiwan, Südkorea und China sind auf dem Markt erschienen. Sind europäische und amerikanische Unternehmen noch marktführend?
F.G.: Die Werkzeugmaschinenindustrie ist ein dynamischer und stark internationalisierter Sektor. Viele Hersteller planen ihre Aktivitäten über verschiedene Länder hinweg, und die globale Lieferkette für Werkzeugmaschinen umfasst heute Europa und Nordamerika, die traditionell mit dem verarbeitenden Gewerbe verbunden sind, aber auch lateinamerikanische und asiatische Länder. Europäische und amerikanische Unternehmen sind nach wie vor marktführend und bleiben an der Spitze in Bezug auf Produktion und Innovation. Asiatische Unternehmen, insbesondere aus China, Südkorea und Taiwan, haben sich jedoch zunehmend in die internationale Werkzeugmaschinen-Wertschöpfungskette integriert, entweder als Zulieferer oder als Hersteller.
So hat sich beispielsweise Asien in Bezug auf die Produktion zu einer Schlüsselregion entwickelt: 2018 betrug der Anteil der chinesischen Werkzeugmaschinenproduktion an der weltweiten Gesamtproduktion von Werkzeugmaschinen 28%, während die südkoreanische und taiwanesische MT-Produktion bei 6,6% bzw. 5% lag. Betrachten wir den Handel, so stellen wir fest, dass die regionalen Märkte in hohem Maße voneinander abhängig geworden sind. Der größte Kunde der europäischen Hersteller außerhalb Europas ist China, auf das 25 % ihrer Gesamtexporte in externe Märkte entfallen. Japan und Taiwan sind unterdessen die Hauptlieferanten der europäischen Hersteller, auf die 37% bzw. 15% der gesamten außereuropäischen Werkzeugmaschinenimporte entfallen. Insgesamt expandiert die Werkzeugmaschinenindustrie weiterhin nach außen, angetrieben von sehr wettbewerbsfähigen und global ausgerichteten Unternehmen.
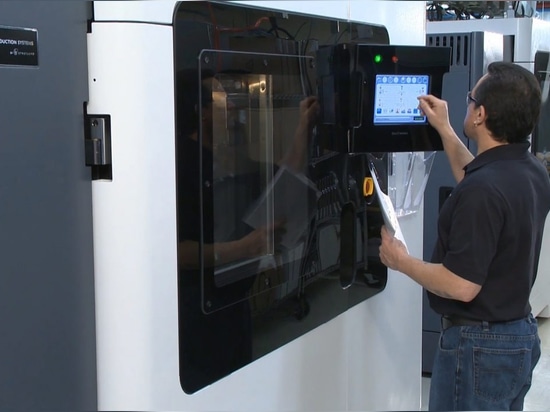
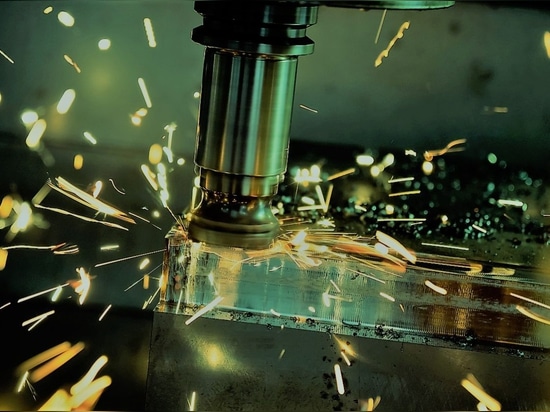