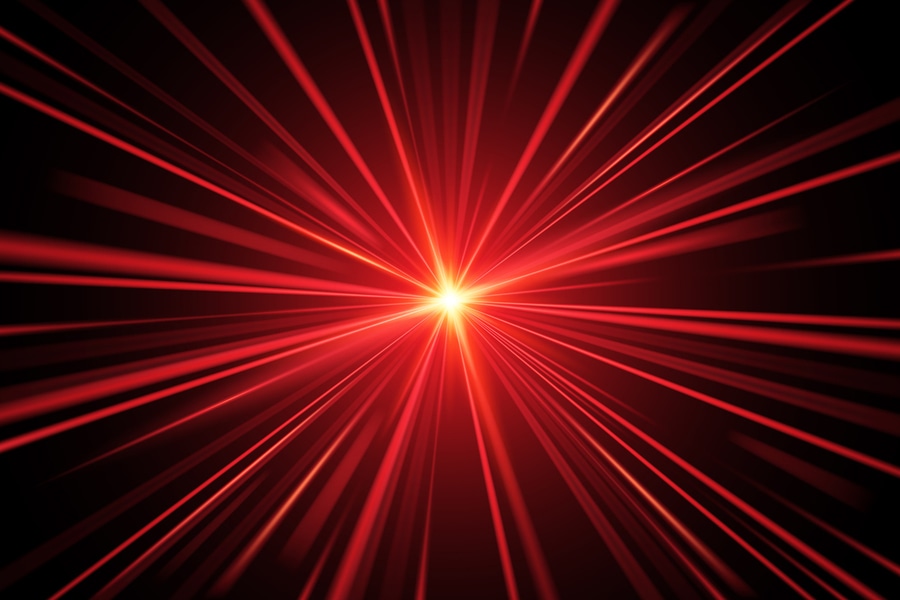
Automatische Übersetzung anzeigen
Dies ist eine automatisch generierte Übersetzung. Wenn Sie auf den englischen Originaltext zugreifen möchten, klicken Sie hier
#Neues aus der Industrie
GESCHICHTE | 60 Jahre Laser: Eine Lösung für so viele Probleme (Teil 1)
HISTORY | 60 Jahre Laser (1/2) - Vor 60 Jahren, 1960, wurde der Laser erfunden. Anlässlich des 60-jährigen Jubiläums erzählen Journalisten und Branchenexperten, welchen Einfluss die Lasertechnik in Deutschland hatte und bewerten ihre Zukunft.
Am 6. Mai 1964 brachte die New York Times ein Interview mit Theodor Maiman, dem Mann, der im Mai 1960 den ersten Laser gebaut hatte. 60 Jahre später wissen wir, wie viele Probleme seine Erfindung gelöst hat. Ohne Laser hätten wir kein Internet, keine Computer und keine Gensequenzierung, um nur einige wichtige Anwendungen zu nennen. Aber es brauchte 60 Jahre und viele brillante Köpfe rund um den Globus, um all diese Probleme mit Lasern zu lösen.
Von Nikolaus Fecht (Dipl.-Ing. bei der Deutschen Presse-Agentur) und Dr. Andreas Thoss (Geschäftsführer der THOSS Media GmbH)
Alles begann im Mai 1960 mit einem hellroten Punkt. In einem Labor in Malibu experimentierte der Physiker und Elektroingenieur Dr. Theodore H. Maiman mit einem synthetischen Rubin, der mehrere Zentimeter lang war. Dieser stabförmige Kristall hatte an jedem Ende einen Silberspiegel und war von einer spiralförmigen Xenon-Blitzlampe umgeben. Das intensive Licht dieser Lampe ließ den Stab rosa leuchten - physikalisch ausgedrückt: Es regte die Atome im Kristall an. Ein Lichtpuls prallte zwischen den Spiegeln hin und her und verließ den rosa Rubin als hellroter Lichtstrahl. Es war der erste offiziell dokumentierte Laserstrahl überhaupt
Todesstrahlen?
Nobelpreisträger Charles Townes, ein weiterer Laserpionier, berichtet in seinen Memoiren "How the Laser Happened", wie das zerstörerische Potenzial des Lasers die Phantasie der Militärs von Anfang an beflügelte. Es war die Rede von Todesstrahlen und davon, Raketen im Weltraum zum Absturz zu bringen. Sein Schwager und Miterfinder Arthur Schawlow förderte diese Idee eher, indem er öffentlich demonstrierte, wie man mit einem Laser Partyballons abschießen konnte
Solche Ideen führten schnell zu einem massiven Ausbau von Forschung und Entwicklung - in Ost und West. Die USA sahen im Laser "den größten Durchbruch im Waffenbereich seit der Atombombe" und pumpten ab 1960 Millionen von Dollar in die Forschung. In Deutschland waren die Budgets weitaus geringer, doch auch hier holte sich das Bundesverteidigungsministerium bald die Unterstützung der Industrie in Form von Firmen wie Leitz und Telefunken. Schnell wurde jedoch klar, dass die Hauptanwendung des Lasers im Bereich der Vermessung lag. Die Entwicklung von "Todesstrahlen" zum Abschuss von Raketen kam nie über die Testphase hinaus.
Zu den ersten am Tisch gehörten natürlich etablierte Unternehmen aus der optischen Industrie. Sowohl Carl Zeiss aus Oberkochen als auch der VEB Carl Zeiss aus Jena begannen Anfang der 1960er Jahre mit der Entwicklung, teilweise auf eigene Kosten. Bereits 1962 wurde in Oberkochen der erste Laser in Betrieb genommen, der VEB Carl Zeiss präsentierte 1965 ein erstes Labormodell eines laserbasierten Entfernungsmessers.
Die Arbeit an militärischen Projekten wurde bald von zivilen Anwendungen flankiert, nicht zuletzt in Deutschland. Bereits Mitte der 1960er Jahre hatte die Bauakademie der DDR den Einsatz von Baulasern - insgesamt etwa 20 Stück - zur hochpräzisen Vermessung beim Bau von z. B. Fernsehtürmen eingeführt
Lasergebohrte Diamant-Ziehbleche
Zeiss in Oberkochen entwickelte daraufhin gütegeschaltete Festkörperlaser mit einer Spitzenleistung im Megawattbereich. Sie waren zwar für die Materialbearbeitung ungeeignet, aber für Mess- und Vermessungszwecke mehr als ausreichend.
Durch eine Laune des Schicksals war es ein Feinmechaniker, der den Weg für die erste industrielle Anwendung ebnete. Dr. Paul Seiler, damals ein junger Laboringenieur, bekam von Dr. Siegfried Panzer, dem Leiter des Hochfrequenzlabors, freie Hand, um an der Lasertechnik zu arbeiten. Seiler, heute 82 Jahre alt, erinnert sich:
"Nach Sondierungsversuchen mit Mikroskopoptiken haben wir dann ein Laborgerät gebaut. Wir waren auf Neuland - nicht nur die Lasertechnik war neu, sondern auch die Optik und die Stromversorgung mit Kondensatorentladung."
Doch die Arbeit hat sich gelohnt, denn Zeiss konnte das Laborgerät zum Beispiel an den Glühbirnenhersteller Osram verkaufen, der damit Diamant-Ziehscheiben bohrte
Laserschweißen ersetzt das herkömmliche Klebeverfahren
Der entscheidende Schritt kam für Seiler mit einem anderen Kunden, CARL Haas aus Schramberg im Südwesten Deutschlands. Der Feinwerktechnik-Spezialist suchte nach einem Schweißverfahren, mit dem er bei mechanischen Uhren die Spiralfeder an der Unruh befestigen kann. Seiler entwickelte ein Laborsystem, das bei Schweißversuchen so gut abschnitt, dass Haas ihm einen Job anbot. Das war im Jahr 1971.
Seiler hatte das Gefühl, bei Zeiss eine einsame Furche zu pflügen, also wechselte er zu Haas nach Schramberg, wo er mit einem kleinen Team einen industrietauglichen Festkörperlaser entwickelte. Dieser Laser ersetzte dann das traditionelle Klebeverfahren zur Befestigung der Spiralfedern, das zehnmal so lange dauerte. Der endgültige Durchbruch für Seiler und sein Team folgte Ende der 70er Jahre, als die Lasertechnik den Weg zur automatisierten Fertigung von Schweißteilen für Kathodenstrahlröhren im neu entwickelten Farbfernseher ebnete. Später wurde Seiler zum Geschäftsführer der damals eigenständigen Haas Laser GmbH ernannt, die 1992 Teil der TRUMPF Gruppe wurde
Gaslaser vs. Festkörperlaser
Bei TRUMPF stand die Lasertechnik im Fokus eines jungen Managers - Berthold Leibinger. Zunächst Konstrukteur bei TRUMPF und ab 1966 technischer Geschäftsführer - flog er 1978 in die USA und besuchte eine Reihe von Laserherstellern. Nichts von dem, was er sah, war für industrielle Zwecke geeignet, aber er kaufte seinen ersten CO2-Laser. Nach einem Jahr intensiver Entwicklungsarbeit stellte er seine erste industrielle Laserschneidanlage vor.
Die Ingenieure waren fasziniert von den Unterschieden zwischen Gas- und Festkörperlasern, erklärt Christian Schmitz, Geschäftsführer für Lasertechnik bei TRUMPF:
"Der CO2-Laser war tatsächlich der erste Laser überhaupt, der im Dauerbetrieb eine hohe Ausgangsleistung liefern konnte, während der Festkörperlaser im Pulsbetrieb eine hohe Ausgangsleistung hatte, was ihn ideal für das Aufbringen von Schweißpunkten in elektronischen Bauteilen machte."
Doch für die nächsten 20 Jahre sollte das Schneiden und Schweißen von Blechteilen die Domäne des CO2-Lasers bleiben. Erst um die Jahrhundertwende, mit der Entwicklung immer leistungsfähigerer Diodenlaser, gelang der Festkörpertechnologie der Durchbruch.
Maßgeschneidertes Licht mit großem Wellenlängenbereich
Die 1980er Jahre brachten eine neue Generation von Wissenschaftlern und eine Reihe von neuen Forschungsinstituten. Einer dieser aufstrebenden Forscher war Reinhart Poprawe. Inspiriert von einer Besichtigung des Lawrence Livermore National Laboratory in Kalifornien, studierte und promovierte er bei Professor Gerd Herziger an der Technischen Universität Darmstadt. Gemeinsam mit Herziger gründete er dann 1985 das Fraunhofer-Institut für Lasertechnik ILT in Aachen. Damals war Poprawe Geschäftsführer der Thyssen Laser Technik GmbH, die sich mit der Entwicklung der ersten großtechnischen Laserschneidanlagen für Dickbleche und der nächsten Generation von Tailored Blanks für die Automobilindustrie einen Namen gemacht hatte. Nach ein paar weiteren Jahren wechselte er jedoch in die Leitung des Fraunhofer ILT
Am Fraunhofer ILT konnte Poprawe miterleben, wie die Lasertechnik in immer neuen Variationen nach und nach in der Fertigungsindustrie Fuß fasste. Rückblickend hebt er einige Highlights hervor: die Entwicklung des Ultrakurzpulslasers, des InnoSlab-Lasers und nicht zuletzt das Konzept des "Tailored Light" - Lasertechnik, die perfekt auf die jeweilige Anwendung zugeschnittenes Licht liefert
Additive Fertigung: Der lange Weg zur industriellen Anwendung
Nach der Euphorie der Anfangsjahre musste die Lasertechnik dann beweisen, dass sie die konventionellen Verfahren bei Qualität und Kosten schlagen kann. Das Aufkommen der additiven Fertigung für Metallteile ist ein gutes Beispiel dafür, wie konkurrierende Technologien um die Vorherrschaft kämpften. TRUMPF, so Schmitz, habe diese Technologie "miterfunden". Es war 2004/05, als TRUMPF die ersten Maschinen für die Laser Metal Deposition (LMD) auf den Markt brachte. Schmitz erinnert sich:
"Etwa zur gleichen Zeit kamen aber auch die ersten wirklich schnellen Fünf-Achs-Fräsmaschinen auf den Markt. Und bei der additiven Fertigung mussten die Teile immer ein wenig nachbearbeitet werden. Also dachte man, es sei besser, sie aus einem einzigen Stück Material zu fräsen."
Während die Entwicklung von LMD weiterging, stellte TRUMPF die Arbeit am Laser-Metallschmelzen (LMF) ein. Die Produktion der Trumaform - der ersten LMF-Maschine von TRUMPF - wurde gestoppt und erst 2013/14 wieder aufgenommen, in Kooperation mit der italienischen Firma Sisma.
Dann wurde in Aachen eine neue Idee entwickelt, die sich als bahnbrechend erweisen sollte: die extreme Hochgeschwindigkeits-Lasermaterialbeschichtung - auch bekannt unter dem Kürzel EHLA. Entwickelt und patentiert wurde es am Fraunhofer ILT in Zusammenarbeit mit dem Lehrstuhl für Digital Additive Production (DAP) der RWTH Aachen University. Damit konnte die Abscheidegeschwindigkeit von maximal 2 Metern auf mehrere hundert Meter pro Minute gesteigert werden. In enger Zusammenarbeit mit dem niederländischen Ingenieurbüro Hornet Laser Cladding und mit ACunity, einer Ausgründung des Fraunhofer ILT, wurde die EHLA-Technologie dann weltweit für die industrielle Produktion ausgerollt. Auch der Laserpionier TRUMPF war von den hohen Beschichtungsgeschwindigkeiten, die die EHLA-Technologie ermöglicht, überzeugt und startete 2017 die Produktion seiner sehr erfolgreichen TruLaser Cell-Reihe von EHLA-Maschinen zur Bearbeitung von Bauteilen unterschiedlicher Größe. Derzeit wird die Idee auf echte 3D-Prozesse ausgerollt.
Nach 20 Jahren des Auf und Ab haben die laserbasierten additiven Fertigungsverfahren endlich den Marktdurchbruch geschafft.
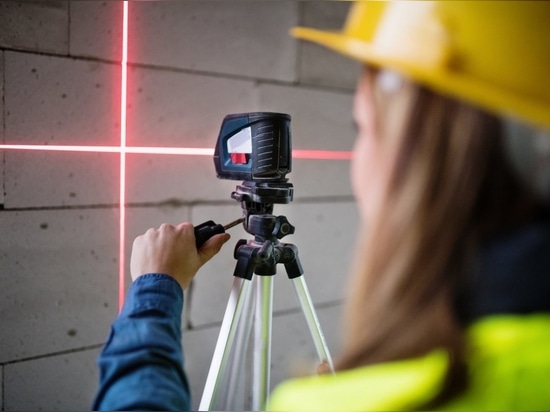
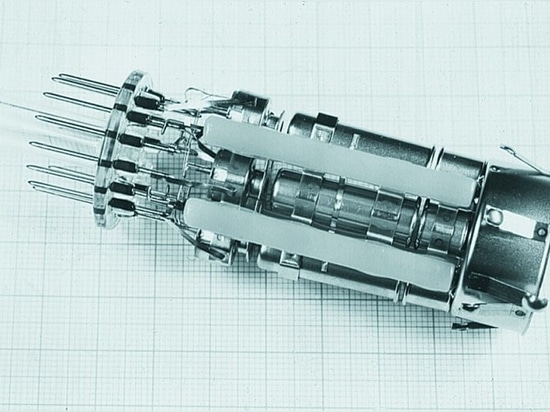
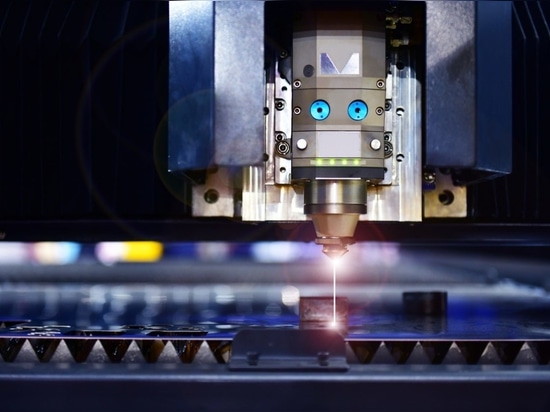
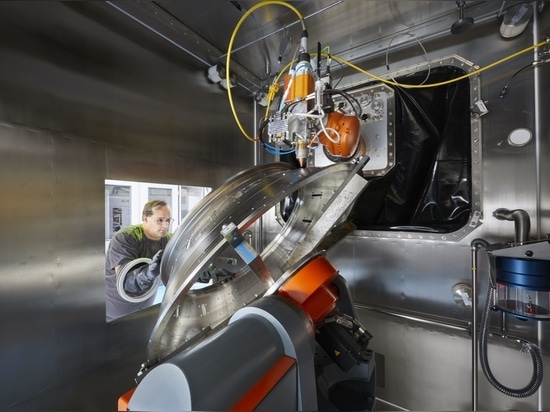
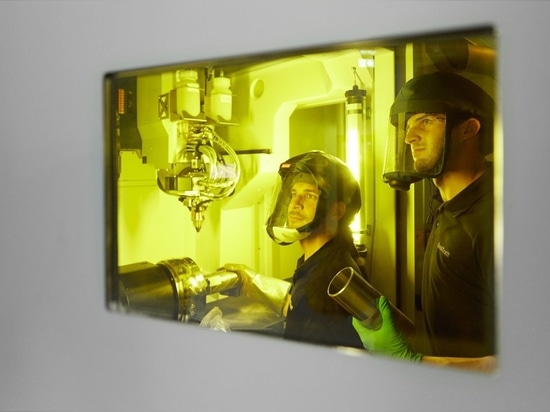