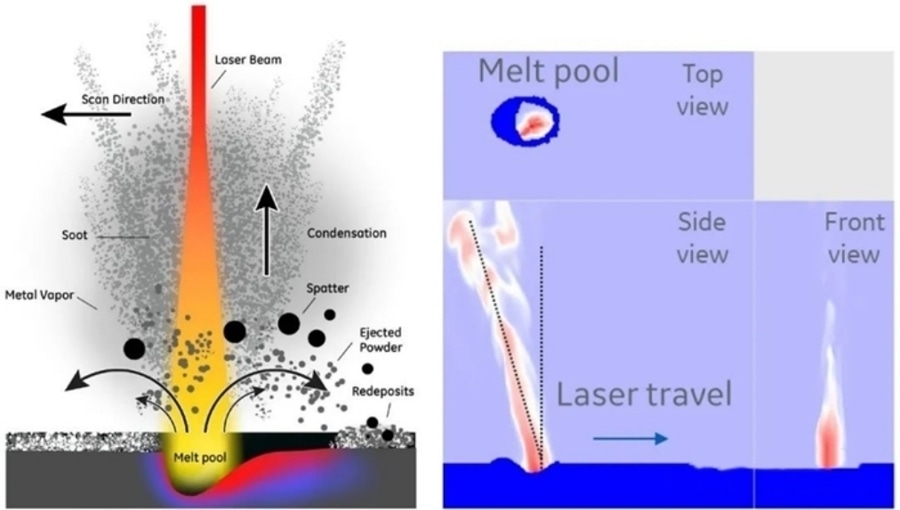
Automatische Übersetzung anzeigen
Dies ist eine automatisch generierte Übersetzung. Wenn Sie auf den englischen Originaltext zugreifen möchten, klicken Sie hier
#Produkttrends
Typische Defekte von 3D-gedruckten Metallteilen
Die Defekte beim Pulverbeschichtungsprozess und die Defekte beim Druckprozess
Die Defekte im MPBF-Prozess können in Defekte im Pulverbeschichtungsprozess und Defekte im Druckprozess unterteilt werden. Zu den Defekten bei der Pulverbeschichtung gehören unregelmäßige Pulverschichten, zu den Defekten beim Druckprozess gehören Spritzer, Balling-Phänomene, Gasporosität, Oberflächenrauhigkeit, Risse, geometrische Verformungen usw. Im Folgenden werden die Ursachen der verschiedenen Defekte vorgestellt und der Einfluss der verschiedenen Defekte auf die Anwendung von 3D-Druckteilen zusammengefasst.
Spritzer
Spritzer sind einer der häufigsten Defekte im MPBF-Prozess, die die Interaktion zwischen Laser und Pulverbett direkt beeinflussen und zu anderen Defekten führen. Die Ergebnisse zeigen, dass die Spritzer hauptsächlich durch die seitliche Inertgasströmung, die Fluktuation des Schmelzbades und den Rückspüldruck verursacht werden. Die Spritzer, die auf das Pulverbett fallen, lagern größere Metallpartikel ab, was zu unvollständigem Aufschmelzen und Gasporositätsdefekten führt, was sich ungünstig auf die Zugfestigkeit und die Ermüdungseigenschaften der Teile auswirkt. Außerdem beeinträchtigen die Spritzer, die auf die Oberfläche der erstarrten Schicht fallen, die Pulverbeschichtung der nächsten Schicht, was zu ungleichmäßigem Pulver in der nächsten Schicht führt oder sogar den Wiederbeschichter beschädigt.
Die Defekte im MPBF-Prozess können in Defekte im Pulverbeschichtungsprozess und Defekte im Druckprozess unterteilt werden. Zu den Defekten beim Pulverbeschichtungsprozess gehören unregelmäßige Pulverschichten, und zu den Defekten beim Druckprozess gehören Spritzer, Balling-Phänomene, Gasporosität, Oberflächenrauhigkeit, Risse, geometrische Verformungen usw. Im Folgenden werden die Ursachen der verschiedenen Defekte vorgestellt und der Einfluss der verschiedenen Defekte auf die Anwendung von 3D-Druckteilen zusammengefasst.
Spritzer
Spritzer sind einer der häufigsten Defekte im MPBF-Prozess, die die Interaktion zwischen Laser und Pulverbett direkt beeinflussen und zu anderen Defekten führen. Die Ergebnisse zeigen, dass die Spritzer hauptsächlich durch die seitliche Inertgasströmung, die Fluktuation des Schmelzbades und den Rückspüldruck verursacht werden. Die Spritzer, die auf das Pulverbett fallen, lagern größere Metallpartikel ab, was zu unvollständigem Aufschmelzen und Gasporositätsdefekten führt, was sich ungünstig auf die Zugfestigkeit und die Ermüdungseigenschaften der Teile auswirkt. Außerdem beeinträchtigen die Spritzer, die auf die Oberfläche der erstarrten Schicht fallen, die Pulverbeschichtung der nächsten Schicht, was zu ungleichmäßigem Pulver in der nächsten Schicht führt oder sogar den Wiederbeschichter beschädigt.
Die Gasporosität ist einer der wichtigsten Defekte im MPBF-Prozess, der die mechanischen Eigenschaften der 3D-Druckteile beeinträchtigt. Im MPBF-Prozess führen das schnelle Schmelzen und Erstarren des Materials und die heftigen Fluktuationen des Schmelzbads zur Gasporosität. Die Größe, Menge, Form und Position der Gasporosität haben einen wichtigen Einfluss auf die mechanischen Eigenschaften der Teile. Je höher die Gasporosität ist, desto kürzer ist die Ermüdungslebensdauer der Bauteile, und der Einfluss der Gasporosität in der Nähe der Oberfläche auf die Ermüdungseigenschaften der Bauteile ist größer als an anderen Positionen. Je nach dem Entstehungsmechanismus der Gasporosität kann man sie in rohstoffbedingte Gasporosität und durch Lasereinwirkung verursachte Gasporosität unterteilen.
Die Ursache der Gasporosität ist sehr kompliziert und hängt eng mit den Prozessparametern zusammen. Ein vernünftiger Druckprozess und eine kontinuierliche Prozessoptimierung sind immer noch wichtige Voraussetzungen, um das Auftreten von Gasporosität zu vermeiden.
Oberflächenrauhigkeit
Mit der Entwicklung der MPBF-Technologie werden die Arten von 3D-Druckmaterialien immer zahlreicher, und die mechanischen Eigenschaften der Bauteile wurden stark verbessert. Die relativ schlechte Oberflächenqualität ist jedoch immer noch eines der größten Hindernisse für die Entwicklung und industrielle Anwendung von MPBF. Die Oberflächenrauheit der mittleren Schicht wirkt sich auf die Pulverqualität der nächsten Schicht aus, was zu internen Defekten führt. Die Oberflächenrauhigkeit der Aufbaufläche wird die Ermüdungsleistung der Teile ernsthaft beeinträchtigen.
Die Oberflächenqualität ist eng mit der Fließfähigkeit des Schmelzbades verbunden. Durch Anpassung der Laserleistung, der Scangeschwindigkeit, der Pulverschichtdicke und anderer Prozessparameter kann die Oberflächenqualität effektiv verbessert werden. Eine Nachbehandlung kann ebenfalls zur Verbesserung der Oberflächenqualität von Teilen eingesetzt werden, erhöht aber die Kosten und verringert die Effizienz.
Risse
Risse im MPBF-Prozess hängen mit der Temperaturverteilung, Eigenspannungen und unvollständiger Verschmelzung zusammen. Risse, die durch Eigenspannungen verursacht werden, können in Erstarrungsrisse und Verflüssigungsrisse unterteilt werden, die sich auf die Materialien beziehen. Die Erstarrungsrisse werden durch den großen Temperaturgradienten zwischen dem Schmelzbad und dem erstarrten Metall verursacht, was zu einer großen Verformung des Schmelzbades führt. Die unzureichende Fließfähigkeit der Flüssigkeit kann jedoch die durch das Schmelzbad verursachte Verformung nicht ergänzen. Der Verflüssigungsriss erscheint in der Teilschmelzzone und hängt mit dem Verflüssigungsbereich, der Kornstruktur, der thermischen Dehnung und der Schrumpfung des Metallmaterials zusammen.
Darüber hinaus kann auch eine unvollständige Verschmelzung zu Rissen führen, was sich fatal auf das mechanische Verhalten und die Ermüdungslebensdauer von 3D-Druckteilen auswirkt. Aufschmelzrisse treten in der Regel zwischen benachbarten Abtastkanälen oder zwischen Ablagerungsschichten auf, die hauptsächlich durch unvollständiges Schmelzen des Metallpulvers verursacht werden. Wenn die Risse schwerwiegend sind, können sie zu Delaminationsdefekten führen.
Geometrische Verformung
Aufgrund der geometrischen Merkmale, der Wärmeakkumulation, der Spannungskonzentration und anderer Gründe von Teilen im MPBF-Prozess können sich geometrische Defekte in unterschiedlichem Ausmaß bilden. Ein geringer Grad kann zu Verformungen und Maßfehlern führen, ein schwerer Grad kann zu einer unvollständigen Struktur oder sogar zum Versagen der Konstruktion führen.
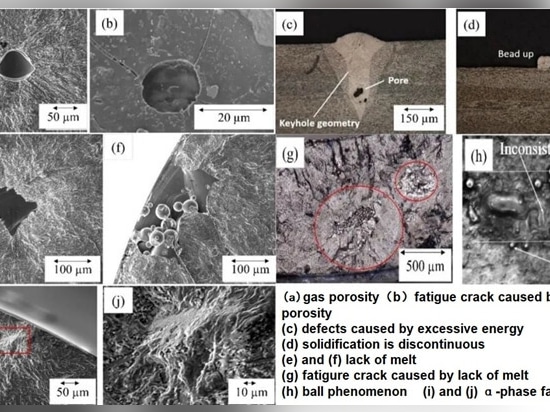
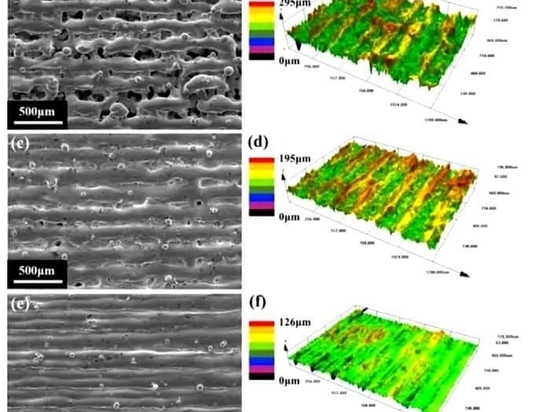
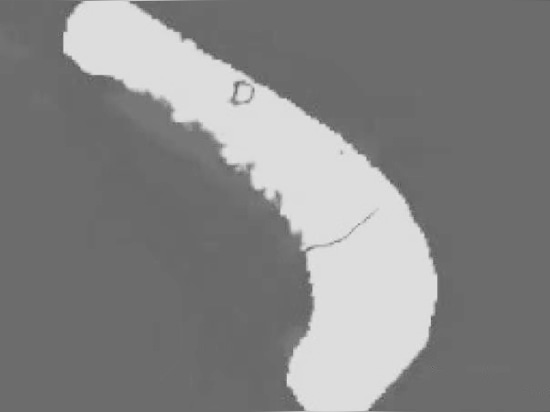
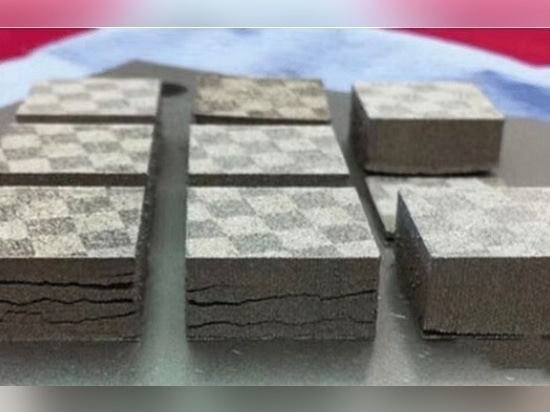