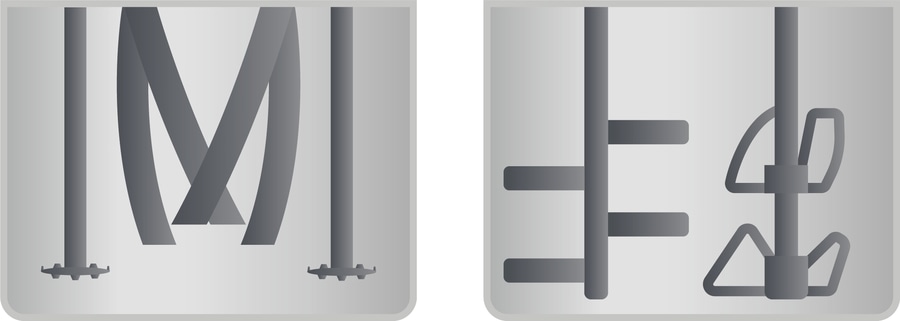
Automatische Übersetzung anzeigen
Dies ist eine automatisch generierte Übersetzung. Wenn Sie auf den englischen Originaltext zugreifen möchten, klicken Sie hier
#Neues aus der Industrie
Mischen von Batterie-Slurries mit NETZSCH-Planetenmischern reduziert die Mischzeit von Stunden auf Minuten
Der Mischprozess ist der erste Schritt bei der Herstellung von Lithium-Ionen-Batterie-Slurries. Er ist entscheidend für die Qualität der Batterie und hat einen erheblichen Einfluss auf die Leistung der Zelle.
Der Mischprozess ist der erste Schritt bei der Herstellung von Lithium-Ionen-Batterie-Slurries. Er ist entscheidend für die Qualität der Batterie und hat einen erheblichen Einfluss auf die Leistung der Zelle. Beim Mischprozess werden aktives Material, Bindemittel und leitfähige Zusätze mit einem Dispersionsmittel wie Wasser oder Lösungsmittel gemischt, um den Batterie-Slurry zu bilden.
Die Mischwerkzeuge müssen die Partikel homogen über das gesamte Volumen verteilen. Diese Mischwerkzeuge müssen auch andere wichtige Anforderungen erfüllen: Aufbrechen potenzieller Agglomerate, Benetzen und Beschichten der Partikel und Vermeiden lokaler Materialansammlungen auf mikroskopischer Ebene.
Derzeit werden viele konventionelle Planetenmischer zum Mischen von Batterieslurries für Kathoden und Anoden eingesetzt. Sie verwenden ähnliche Geometrien, und es gibt fast keine signifikanten Unterschiede in der Konstruktion dieser Maschinen.
Aber ist die Ausführung dieser Mischer die beste und effizienteste Methode zum Mischen von Batteriemassen?
In einer Batteriemischanlage wird das Mischen in die Kathoden- und die Anodenlinie unterteilt. Am kritischsten ist das Mischen für die Anode aufgrund der höheren Viskosität und der möglichen Beschädigung der Bindemittelstruktur. Die derzeitigen Mischzeiten liegen zwischen 4 und 6 Stunden. Während eines Validierungsschritts teilte ein potentieller Kunde seine Erfahrungen mit einem asiatischen Mischerlieferanten mit, der eine Gesamtmischzeit von 270 Minuten (4,5 Stunden) hatte.
Bei Tests im NETZSCH-Labor konnte die Mischzeit um den Faktor 2 reduziert werden. Die NETZSCH-Planetenmischer (PMH) mischten die Slurry in 120 Minuten und lieferten eine noch bessere Qualitätsleistung. Warum also waren die NETZSCH Planetenmischer so viel besser und wie funktioniert ein Planetenmischer?
Das Funktionsprinzip
Der NETZSCH PMH (Planetenmischer High Speed) arbeitet mit einem Planetengetriebe. Die selbstrotierenden Mischwerkzeuge, Low-Speed als Axialtraverse und High-Speed als Schmetterlingswerkzeug, führen in einem stehenden Behälter eine Drehbewegung aus und durchlaufen das gesamte Mischgut.
Durch die Vergrößerung des Durchmessers der Mischwerkzeuge erhöht sich die Leistungsaufnahme drastisch, was zu einer schnelleren, effizienteren und besseren Durchmischung sowie einer besseren Produktqualität führt. Die NETZSCH PMH-Werkzeuge haben im Vergleich zu herkömmlichen Planetenmischern einen wesentlich größeren Durchmesser.
Nicht nur der Durchmesser, sondern auch die Konstruktion ist entscheidend. Konventionelle Planetenmischer können durch die hohen Scherkräfte der Dispergierscheibe das Bindemittel beschädigen. Die NETZSCH-Mischwerkzeuge sind speziell so konstruiert, dass die Scherkräfte reduziert werden und eine weichere und bessere Knetung erzeugt wird. Dadurch kann das Mischwerkzeug mit höheren Geschwindigkeiten laufen, ohne die wichtige Binderstruktur des Batterieslurrys zu beschädigen.
Ein praktisches Beispiel für fortschrittliche Verarbeitungstechniken findet sich bei der Herstellung von Anodenslurry auf Wasserbasis. Diese Aufschlämmung enthält Carboxymethylcellulose (CMC), die sich durch ihre langen Polymerketten und ihre hohe Molekülmasse auszeichnet. Herkömmliche Planetenmischer, die mit Dispergierscheiben mit hoher Scherkraft ausgestattet sind, verursachen oft eine mechanische Belastung, die die CMC-Ketten fragmentiert. Diese Fragmentierung führt zu unerwünschten Viskositätsänderungen, wie z.B. einer Scherverdickung, wodurch die Slurry für nachfolgende Beschichtungsprozesse ungeeignet wird.
Die NETZSCH-Mischwerkzeuge hingegen sorgen für eine sanftere und effizientere Knetwirkung. Dies verhindert den Abbau von CMC-Ketten, sorgt für eine gleichmäßige Viskosität und ermöglicht eine gleichmäßige Durchmischung, was zu einer gleichmäßigen Beschichtung des aktiven Materials führt. Folglich verbessert diese Methode die Energiedichte der Elektrode und trägt letztlich zur Entwicklung von Hochleistungsbatterien bei. Diese Batterien weisen eine größere Reichweite und eine schnellere Ladefähigkeit auf, was die Bedeutung einer optimierten Slurry-Aufbereitung für den Fortschritt der Batterietechnologie unterstreicht.
Insgesamt führt der erhöhte Leistungseintrag zu deutlich kürzeren Mischzeiten von 120 Minuten für Anodenslurries. Für die Kathodenmischung, die normalerweise 480 Minuten (8 Stunden) benötigt, reduziert das NETZSCH-Mischen die Zeit auf eine Gesamtmischzeit von 180 Minuten (3 Stunden).
Wie kann man die Qualität messen?
Neben den kürzeren Mischzeiten wird auch die Qualität verbessert. Aber wie misst man die Qualität beim Mischen von Gülle? Der nächste wichtige Schritt nach der Aufschlämmung ist die Beschichtung. Für den Beschichtungsprozess ist die Fließfähigkeit der Slurrys entscheidend, um einen homogenen und verarbeitbaren Film auf der Stromabnehmerfolie zu erhalten. Diese kann durch die Viskosität bestimmt werden.
Der NETZSCH-Geschäftsbereich Analysieren & Prüfen misst das Fließverhalten mit dem Rotationsrheometer Kinexus. Die Abhängigkeit der Viskosität von verschiedenen Schergeschwindigkeiten ist wichtig und gibt Aufschluss über die Qualität. Ein Schlüsselfaktor ist die Stabilität der produzierten Slurry. Während der Produktion kann es zu Wartezeiten kommen, und die direkte Beschickung der Streichmaschine ist nicht immer gewährleistet. Es ist wichtig, dass der Schlamm nicht schnell sedimentiert und eine längere Lagerzeit hat, was durch eine höhere Viskosität bei niedrigeren Scherraten angezeigt wird. Dies ist auf eine bessere Benetzung und Dispersion der Partikel zurückzuführen, die durch einen höheren Energieeintrag aufgrund des einzigartigen Designs erreicht wird. Außerdem verbessert sich der Beschichtungsprozess, es entstehen schärfere Kanten und ein Verschmieren wird vermieden.
Ein weiterer wichtiger Faktor ist die Verarbeitbarkeit und Durchflussmenge. Der Schlamm wird über eine Schlitzdüse auf die Kollektorfolie übertragen. Um Verstopfungen zu vermeiden, ist eine scherverdünnende Wirkung wichtig. Die Schlitzdüse erzeugt hohe Schergeschwindigkeiten, und für einen schnellen Beschichtungsprozess ist ein steiler Viskositätsanstieg erforderlich. Es ist wichtig, eine hohe Steigung der Viskositätskurve zu haben, die zu einer niedrigeren Viskosität bei höheren Scherraten führt.
Zusammenfassung
Zusammenfassend lässt sich sagen, dass die NETZSCH Planetenmischer die Mischeffizienz und -qualität von Lithium-Ionen-Batterie-Slurrys durch innovatives Design und optimierte Leistungsaufnahme deutlich verbessern. Der PMH ist jedoch nicht auf eine einzige Technologie beschränkt. Durch sein spezielles Design und die hohe Flexibilität beim Wechsel der Mischwerkzeuge kann der Planetenmischer auch für verschiedene andere Anwendungen in der Batterieindustrie eingesetzt werden und gewährleistet somit Prozesssicherheit. Ein Mischer oder eine Anlage kann mehrere Anwendungen abdecken, darunter:
- Mischen von Feststoffbatterien mit hoher Viskosität
- Herstellung von thermischem Isoliermaterial für Batteriemodule
- Schnelles Mischen von trockenen Batterieelektroden ohne Lösungsmittel, mit flexibler Änderung der Geometrien
- Natrium-Ionen-Batterien