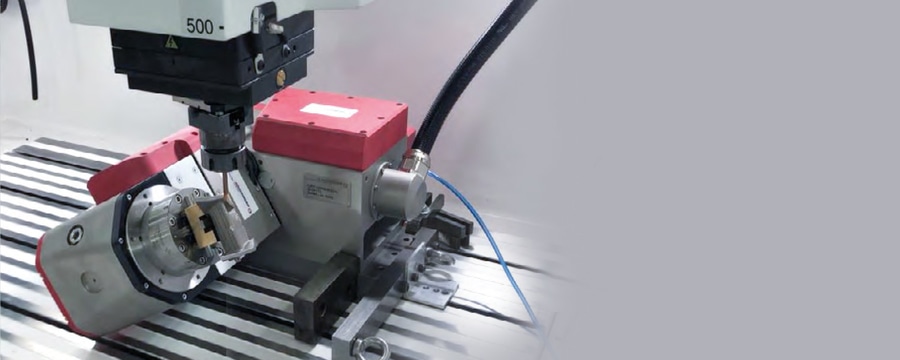
#Neues aus der Industrie
BOHREN VON DIFFUSORLÖCHERN in Turbinenschaufeln
Die Geschäftsstrategie von ONA in der Luftfahrtindustrie besteht hauptsächlich darin, Unternehmen maßgeschneiderte Lösungen mit hohem Mehrwert anzubieten.
Ein Beispiel hierfür war die Entwicklung einer kundenspezifischen Anwendung für einen bedeutenden Hersteller von hochwertigen Komponenten für die Luft- und Raumfahrt sowie die Energieindustrie. Ihr Bedarf an solch hochwertigen Produkten war ein Schlüsselfaktor für ihre Entscheidung, sich für ONA zu entscheiden.
Der Kunde benötigte eine Lösung zum Bohren von Diffusorlöchern in Turbinenschaufeln. Diese Löcher spielen eine wichtige Rolle bei der Belüftung und Kühlung. Schlechte Belüftung und Kühlung erhöhen die Turbinenlufteinlasstemperatur und verringern schließlich die Effizienz und Haltbarkeit der Komponente. In einer Stromerzeugungsturbine würde weniger Energie erzeugt, und in einer Antriebsturbine (z. B. einer Flugzeugturbine) würde mehr Kraftstoff verbraucht. Darüber hinaus können hohe Temperaturen auch dazu führen, dass die Verdichterschaufeln selbst beschädigt werden.
Die Löcher in den Klingen werden normalerweise mit unserer FAST HOLE (FH)-Maschine bearbeitet, die eine spezielle Technologie für schnellere Bearbeitungsgeschwindigkeiten verwendet. Die hohen Präzisions- und Qualitätsanforderungen des Herstellers beim Bohren der Löcher (mit unterschiedlichen geometrischen Formen: konisch, trapezförmig usw.) konnten jedoch von unserer FH-Ausrüstung nicht erfüllt werden, sodass ONA gebeten wurde, eine spezifische Lösung für dieses Problem bereitzustellen.
Der Vorschlag unserer Ingenieure bestand darin, eine Anwendung zu entwickeln, die die Kapazitäten zweier EDM-Technologien kombiniert: FAST HOLE und Senkerodieren. Zunächst werden mittels einer FH-Maschine und dann mittels einer ONA IRIS6-Maschine (XYZ-Achswege: 1000 x 750 x 650 mm; mit 2-Achs-Rundtisch und Kupferelektrode) zylindrische Löcher in das Werkstück gebohrt Löcher mit den erforderlichen geometrischen Formen werden auch in die ersten Löcher gebohrt. Die Achse einiger dieser Löcher ist möglicherweise nicht parallel zur Achse des ersten Lochs.
Wie wir das geschafft haben
Eine Schwierigkeit bei der Umsetzung dieses Projekts war die damalige globale Situation. Da wir uns mitten in der Covid-Pandemie befanden, waren persönliche Treffen zwischen dem Team von ONA und dem Kunden unmöglich. Diese Herausforderung wurde dank der hervorragenden Zusammenarbeit zwischen den verschiedenen Abteilungen von ONA und unserer digitalen Expertise gemeistert, die es uns ermöglichte, schließlich eine telematische Ausschreibung an den Endkunden zu senden.
1. Durchführbarkeitsstudie und abschließende Qualitätsbewertungsstudie.
Zunächst wurde eine Machbarkeits- und abschließende Qualitätsbewertungsstudie durchgeführt, um zu prüfen, ob der Test mit einer ONA-Maschine durchgeführt werden kann. Diese Simulation wurde in China an einer Maschine im Showroom der Tochtergesellschaft durchgeführt.
2. Eignung des ONA IRIS6-Geräts.
Eine der Schlussfolgerungen dieser vorläufigen Machbarkeitsstudie war die Eignung der ONA IRIS6-Maschine angesichts der Merkmale des Projekts: die Größe der Teile und die Notwendigkeit eines Drehtisches, um alle Löcher zu bohren und das Werkstück drehen zu können. Bei der Elektrode haben wir uns für die Verwendung von Kupfer entschieden, um ein hochwertigeres Finish zu erzielen.
3. Angebot auf Video.
Angesichts der Situation der Pandemie, der Einschränkungen und des Interesses des Kunden an der Fortsetzung des Projekts reichte ONA das Angebot per Video ein und drückte damit unser volles Vertrauen in die Qualität des endgültigen Werkstücks aus.
4. Ansicht und Verknüpfung mit CAD-CAM der neuen CNC.
Der Kunde wollte, dass ihm die neue CNC-Software und ihre Verknüpfung mit CAD/CAM gezeigt werden. ONA verwendet beide Softwaresysteme, um die beste Übereinstimmung zu erzielen, sodass das „ideale“ Teil, das von der CAD/CAM-Software erstellt wurde, von der CNC der Maschine verarbeitet wird und das Endergebnis eine exakte Kopie dessen ist, was entworfen wurde. In diesem speziellen Fall war es sehr wichtig, die bereits gebohrten Löcher zu lokalisieren, die genauen Koordinaten in Echtzeit zu bestimmen und sicherzustellen, dass die Maschine den Vorgang an der exakten Stelle ausführen kann. Entscheidend war das Aufrüsten des Werkstücks sowie das punktgenaue Positionieren, da die Form der Teile sehr komplex war.
5. Programmierung mit ONA Script.
Schließlich wurde die Programmierung mit unserem Softwaretool ONA Script durchgeführt, einem Workflow-Generator, der es der Maschine ermöglicht, den gesamten Prozess nahtlos auszuführen.
Bei dieser speziellen Aufgabenstellung handelte es sich um ein Turnkey-Projekt, bei dem zu jeder Zeit ein hohes Maß an Zusammenarbeit mit dem Kunden gegeben war. Dies machte es einfacher, das Endziel der direkten Herstellung eines Teils erfolgreich zu erreichen.
Schlussfolgerungen
Als Ergebnis all dieser harten Arbeit und früherer Studien konnten wir dem Kunden eine vollständig kundenspezifische Senkerodiermaschine zur Verfügung stellen, die gemäß seinen spezifischen Anforderungen für die Bearbeitung von Diffusorlöchern mit komplexer Geometrie in Turbinenschaufeln programmiert wurde. Wie der Kunde uns mitteilte, war unsere schlüsselfertige Lösung auch kostengünstiger als andere Alternativen auf dem Markt.
Die ONA IRIS6-Maschine enthält einen intelligenten digitalen Generator, eine bahnbrechende technologische Innovation in der EDM-Technologie. Er ist 30 % leistungsstärker als andere fortschrittlichere Generatoren. Er kann bis zu 400 Ampere erreichen, ist viermal leistungsstärker als der Standardgenerator, und wurde entwickelt, um den Senkerodierprozess zu optimieren, indem der Energieeintrag jeder Entladung gesteuert wird, wodurch der Elektrodenverschleiß um bis zu 500 % reduziert wird.