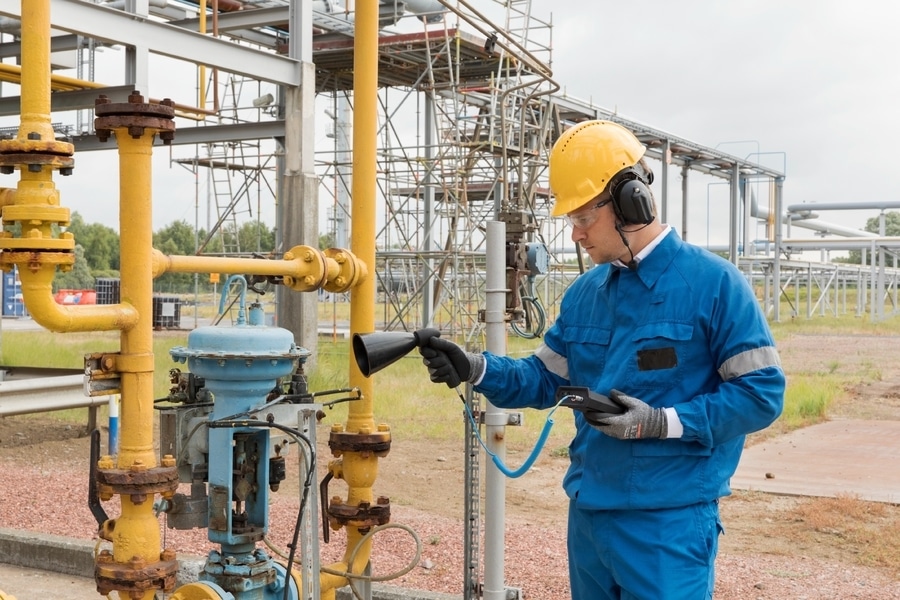
#Neues aus der Industrie
Die Reparatur eines einzelnen 2-mm-Lecks bei 8 bar könnte eine Einsparung von 3.000 Euro pro Jahr bedeuten!
Die Lecksuche sollte oberste Priorität haben, wenn wir wissen, dass Lecks ohne ein Lecksuchprogramm 30-40 % des verbrauchten Volumens ausmachen.
Leider neigen Wartungsmanager allzu oft dazu, das Problem zu ignorieren. Wie können Sie ein „Erkennungsprojekt“ gegenüber dem Management rechtfertigen? Hier einige Argumente …
Instandhaltungs- und Produktionsleiter wurden in den letzten Jahren mit außergewöhnlich komplexen Anforderungen konfrontiert. Tatsächlich scheinen die Ziele, ein Unternehmen wettbewerbsfähiger zu machen, oft widersprüchlich. Energiekosten müssen gesenkt, Wartungsinvestitionen verringert und mit weniger Personal ein besserer Service bereitgestellt werden, während gleichzeitig ein optimaler Anlagenbetrieb sichergestellt wird, um mehr, besser und billiger zu produzieren.
Druckluftlecks = schwerwiegende Folgen
Störungen und Ausfälle, die zu Mängeln in Produktionsanlagen führen, können erhebliche Folgen für Produktion und Logistik haben. Konsequenzen, die Wettbewerbsziele nicht mehr zulassen können! Unter diesen Umständen ist ein Predictive-Maintenance-Programm (oder zustandsorientierte Wartung, je nach verwendetem Vokabular) eine der entscheidenden und strategischen Prioritäten. Das Aufspüren und Reparieren selbst kleinster Druckluftlecks passt perfekt in diese Strategie. Zumal Druckluft sehr energieintensiv ist.
Weit verbreitet und energieintensiv
Druckluft ist einfach herzustellen. Es erzeugt keine Umweltverschmutzung oder Abfall. Es verwendet kostengünstige und robuste Komponenten und ist über kostengünstige Rohrleitungen einfach zu transportieren. Es besteht kein Risiko im Falle einer versehentlichen Leckage. Diese Vorteile erklären, warum Druckluft nach Strom, Erdgas und Wasser der vierthäufigste Energieträger in der Industrie ist. Im Durchschnitt macht er 13 % des industriellen Stromverbrauchs in Frankreich aus. Ihre Verwendung ist jedoch nicht ohne Nachteile. Luft wird in ihrem natürlichen Zustand nicht komprimiert. Es wird also Energie benötigt, um es künstlich zu komprimieren. Druckluft ist aufgrund ihres geringen Wirkungsgrades extrem energieintensiv. Die Optimierung der Drucklufterzeugung und -verteilung ist daher von entscheidender Bedeutung. In diesem Zusammenhang bleibt die Suche und Reparatur von Lecks kurzfristig die kostengünstigste Operation.
Der Hauptkostenfaktor bei der Herstellung ist der Verbrauch von elektrischer Energie. Wenn das System beispielsweise 5 Jahre lang 6.000 Stunden pro Jahr verwendet wird (24/7-Betrieb), macht die verbrauchte Energie 75 % der Druckluftkosten aus. Bei einer intensiven Nutzung von 8.000 Stunden pro Jahr über 5 Jahre steigt dieser Wert auf 80 %.
Im Alltagsbetrieb beträgt die nutzbare Energie gerade einmal 8 %, insbesondere wenn keine Leckagekampagne stattfindet. Das erklärt, warum Druckluft so teuer ist. Die Erkennung und Reparatur von Lecks sollte oberste Priorität haben, wenn bekannt ist, dass Lecks ohne ein Lecksuchprogramm im Allgemeinen 30 bis 40 % des verbrauchten Volumens ausmachen.
Eine inakzeptable Verschwendung
Bevor Sie an Einsparungen am Druckluftsystem selbst denken, um die Effizienz zu steigern und die Energiekosten zu senken, sollten Sie zuerst daran denken, die durch Leckagen verursachten enormen Abfallmengen zu beheben. Die Reparatur eines einzelnen 2-mm-Lecks bei 8 bar bedeutet eine Einsparung von 3.000 Euro pro Jahr (oder sogar mehr, abhängig von den örtlichen Energiekosten). Es ist auch wichtig zu bedenken, dass Lecks überall im System auftreten können: Leitungsverbindungen, Siphons, Filter, Druckregler, Ventile, Schnellkupplungen, Gummischläuche usw. Und es gibt viele andere Stellen, an den verborgensten und unzugänglichsten Stellen.
Ein echtes proaktives Programm zur Jagd auf diese Art von Abfall ist mehr als notwendig, um den Verlust auf vernünftige 5 % des verbrauchten Volumens zu reduzieren. Ab einem Volumenverlust von 30 bis 40 % sind die Energie- und Kosteneinsparungen erheblich. Der internationale Durchschnittsverlust (Quelle: Plant Support & Evaluation Inc.) liegt bei 34 %. Das bedeutet, dass jeder dritte Kompressor nur noch zur Versorgung von Leckagen läuft!
Die Beseitigung von Leckagen hat absolute Priorität
Die Beseitigung von Leckagen ist nicht die einzige Möglichkeit, Druckluftkosten zu optimieren. Auch die Optimierung von Produktion (Regelung, Drehzahlregelung und Wärmerückgewinnung) und Aufbereitung (Trockner, Filter und Kondensator) darf nicht außer Acht gelassen werden. Im Bereich der pneumatischen Stellantriebe besteht daher noch ein großes Energieeinsparpotenzial bei den Anwendern.
Leckageerkennung sollte oberste Priorität haben. Die Lecksuche ist relativ einfach: Zwei Stunden reichen aus. Schließlich sind die Einsparungen für eine sofortige Kapitalrendite erheblich.
Welche Mittel stehen Ihnen zur Verfügung?
Es gibt verschiedene Arten von Ultraschalldetektoren, die zum Auffinden von Lecks verwendet werden können. Die effektivsten sind so konzipiert, dass sie sicher, einfach und unterhaltsam sind. Diese Detektoren können mit Zubehör und Sensoren ausgestattet werden, die auf der Grundlage von zwei Schlüsselparametern ausgewählt werden: Entfernung von der zu inspizierenden Ausrüstung und einfacher Zugang. Der interne Sensor, mit oder ohne Präzisionsspitzen, ist für leicht und direkt zugängliche Bereiche konzipiert, während der flexible Sensor für schwer zugängliche Bereiche oder zur Umgehung eines Hindernisses verwendet wird.