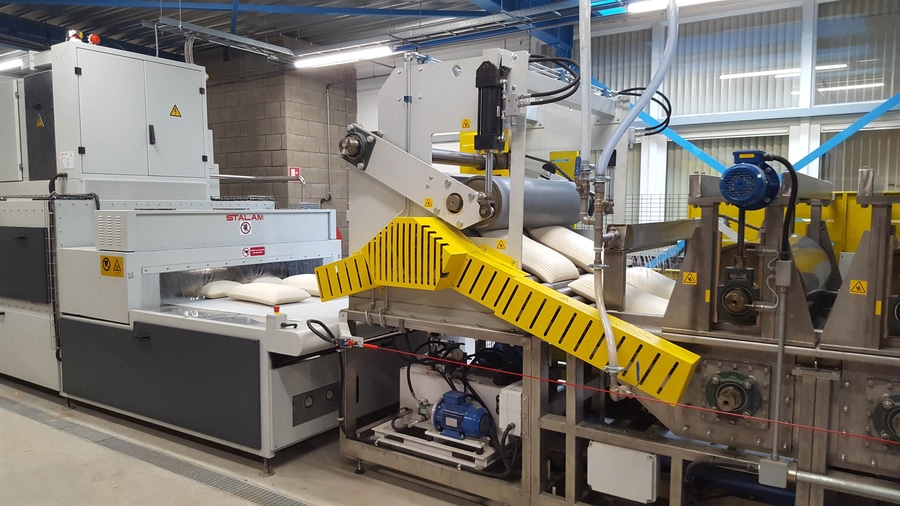
Automatische Übersetzung anzeigen
Dies ist eine automatisch generierte Übersetzung. Wenn Sie auf den englischen Originaltext zugreifen möchten, klicken Sie hier
#Produkttrends
Der Dunlop-Prozess: Wie können Effizienz und Qualität bei der Herstellung von Latexschaum verbessert werden?
Die Radiofrequenztechnologie überwindet die Hauptunannehmlichkeiten des traditionellen Dunlop-Verfahrens, da sie nicht auf Wärmeübertragung beruht...
Der Dunlop-Prozess: Wie können Effizienz und Qualität bei der Herstellung von Latexschaum verbessert werden?
Naturlatex ist eine flüssige Verbindung, die vom Kautschukbaum (Hevea Brasiliensis), dessen Hauptanbaugebiete in Südostasien liegen, geerntet wird. Sobald die Flüssigkeit vom Baum geerntet wurde, wird sie mit Ammoniak und TMTD/ZnO gemischt, um ihre Eigenschaften besser zu erhalten. Dieser standardisierte LA-Latex (ammoniakarmer Latex) wird als Rohmaterial zur Herstellung von Ballons, Handschuhen, Hygieneartikeln usw., aber auch von Latexschaumwaren wie Matratzenkernen und Kissen verwendet
DUNLOP-Prozess: die Ursprünge
1887 erfand der in Schottland geborene John Boyd Dunlop (1840-1921) den ersten aufblasbaren Reifen für das Dreirad seines Sohnes auf der Grundlage der thermischen Vulkanisierung von Naturkautschuk und ließ ihn am 7. Dezember 1888 patentieren. Zwei Jahre später wurde sein Patent jedoch offiziell für ungültig erklärt, da ein anderer schottischer Erfinder, Robert William Thomson (1822-1873), die gleiche Technologie bereits in Großbritannien, Frankreich (1846) und in den USA (1847) patentiert hatte. Dennoch wurde das Verfahren nach Dunlop benannt und zum Hauptsystem für die Vulkanisierung von Gummi- und Latexschaumprodukten.
Technologien werden zum Industriestandard: DUNLOP- und TALALAY-Verfahren
Derzeit gibt es zwei Standardmethoden für die Herstellung von Latexschaumartikeln: das DUNLOP- und das TALALAY-Verfahren. Das TALALAY-Verfahren, das Ende 1940 erfunden wurde, dauert länger und ist komplexer als das DUNLOP-Verfahren. Dieses System wird weltweit nur von wenigen Herstellern verwendet und hat nur einen kleinen Marktanteil. Die Basisrohstoffe in beiden Systemen sind Naturlatex (NL) oder SBR-Latex (Styrol-Butadien-Kautschuk) oder Mischungen aus beiden.
Das DUNLOP-Verfahren
Wenn reiner Naturlatex verwendet wird, wird die Latex-"Milch" mit den erforderlichen Chemikalien gemischt. Nach der Reifung wird die Masse mit einem mechanischen Mischer aufgeschäumt (SBR-Latex kann ohne Reifung aufgeschäumt werden) und in Metallformen gefüllt. Der Mischung wird ein Geliermittel zugesetzt, um eine schnelle Reaktion zu erzeugen, die die Schaumstruktur stabilisiert. Die Formen werden dann in einen Dampfofen oder Tunnel gelegt, um die Kerne zu vulkanisieren. Da geschäumte Produkte gute Wärmeisolatoren sind, werden die Formen mit einer großen Anzahl von Stiften versehen, um die Wärme in den Schaum selbst zu übertragen. Nach der Vulkanisierung wird der Kissen- oder Matratzenkern abgestreift, gewaschen, getrocknet und ist schließlich verkaufsfertig.
Die TALALALAY-Methode
Beim TALALALAY-Verfahren sind vor dem Vulkanisationsschritt drei weitere Phasen notwendig:
- die Form wird nur zu 40-60% gefüllt. Dann wird sie geschlossen und Luft herausgepumpt, um den Schaumstoff so zu expandieren, dass er das gesamte Volumen der Form ausfüllt;
- der Schaum wird auf -20°C eingefroren, um die Struktur zu stabilisieren;
- CO2 wird durch ein Ventil in die Form eingespritzt, um den Schaum zu gelieren.
Der Rest des Prozesses folgt den gleichen Schritten des DUNLOP-Prozesses, d.h. Vulkanisieren, Abziehen, Waschen und Trocknen.
Der traditionelle Dunlop-Vulkanisationsprozess verwendet Dampf als Heizmittel, um die Vernetzungsreaktionen der Polymerketten zu aktivieren. Schaumstoff, der viele winzige Luftblasen enthält, ist von Natur aus ein schlechter Wärmeleiter, und daher ist es ein langsamer und ineffizienter Prozess, Wärme in dicke Matratzenkern- oder Kissenformen eindringen zu lassen. Teure und schwere Metallformen, die mit vielen Metallstiften versehen sind, werden tatsächlich verwendet, um den Prozess zu beschleunigen, aber er ist immer noch zeit- und energieaufwendig.
Im Laufe der Jahrzehnte wurden einige Chemikalien ersetzt, um den Gesamtprozess zu verbessern, aber der Grundprozess, d.h. die Vernetzung der Kautschukmoleküle mit Schwefel, hat sich bis heute nicht geändert, zusammen mit den typischen Nachteilen der konventionellen Wärmeübertragungsmethoden.
Langsamer Prozess, hohe Energieverluste. Gibt es eine Lösung? Ja, es gibt eine!
Der "neue Dunlop-Prozess"
Die Radiofrequenztechnologie überwindet die Hauptunannehmlichkeiten des traditionellen Dunlop-Verfahrens, da sie nicht auf Wärmeübertragung angewiesen ist, so dass selbst dicke, geformte und dichte Latexschaumartikel (Matratzenkerne, anatomische Kissen usw.) schnell erhitzt und vulkanisiert werden können: Tatsächlich wird die Radiofrequenz sofort in einer kontrollierten Menge (die je nach Bedarf von der Maschine selbst eingestellt wird) durch das im Schaumstoff enthaltene Wasser gleichmäßig im gesamten Volumen absorbiert. Die Erwärmung des Schaums und seine vollständige Vulkanisierung dauern daher nur wenige Minuten, sowohl im Zentrum als auch an der Oberfläche.
Die RF-Vulkanisationsmaschinen sind daher viel kleiner (kürzer) im Vergleich zu den herkömmlichen Karussellen oder Tunneln, die mit Dampf bei gleichem stündlichen Durchsatz arbeiten, und der Energieverbrauch kann um bis zu 50% gesenkt werden.
Die Formen können aus leichten und kostengünstigen Verbundwerkstoffen hergestellt werden, die im Vergleich zu herkömmlichen Metallformen eine Gewichtsreduzierung von über 60 % ermöglichen: die reduzierte Formmasse trägt wesentlich zum geringeren Energieverbrauch bei. Darüber hinaus ermöglichen geeignete Formmaterialien eine einfache und schnelle Entformung der vulkanisierten Gegenstände. Nicht zuletzt ist die Formkonstruktion flexibler, da sie nicht an das Vorhandensein von Stiften gebunden ist.
Es sollte auch erwähnt werden, dass die Radiofrequenztechnologie erfolgreich auch für die Herstellung von Endlos-Latexschaumplatten (LPC , Oberseite oder sogar eine echte Matratze) bis zu einer Dicke von 12 cm und mehr in einer viel kürzeren Zeit und mit einer erheblichen Reduzierung des Energieverbrauchs eingesetzt werden kann, wenn man auch bedenkt, dass die traditionelle Dampfvulkanisierung von Platten mit einer Dicke von mehr als etwa 5 cm aufgrund der fehlenden Wärmedurchdringung in Abwesenheit von Metallstiften eine fast unmögliche Aufgabe ist.
Was ist mit der Trocknung von Latexschaum nach dem Vulkanisieren, Waschen und Pressen?
Dieselben technischen Gründe, die Radiofrequenz im Vergleich zu den traditionellen dampfbasierten Vulkanisationsmethoden effizienter und kostengünstiger machen, lassen sich auch auf die abschließende Trocknungsphase von Latexschaumprodukten nach dem Waschen und Auspressen anwenden.
Die Vorteile des Einsatzes von Radiofrequenztrocknern anstelle von dampfbeheizten Trocknern lassen sich wie folgt zusammenfassen:
schnelle und gleichmäßige Trocknung: etwa 20 Minuten reichen aus, um auch dicke und dichte Matratzenkerne unter 1% Restfeuchte ohne Nassflecken zu trocknen; auch geformte Produkte wie Kissen und anatomische Sitze trocknen in dickeren Teilen wie in dünneren Portionen vollkommen gleichmäßig;
keine Vergilbung der Produktoberfläche aufgrund der niedrigen Temperatur im Trocknungstunnel (RF erwärmt den Produktkern, nicht seine äußere Oberfläche);
kurze Konditionierungszeit, so dass das Produkt nach dem Trocknen schnell für den Versand verpackt werden kann, ohne dass es auf dem Weg zum Kunden zu Schimmelbildung kommen kann;
erhebliche Verringerung des Platzbedarfs der Trocknungsanlage dank der kurzen Prozesszeit;
energieeffizienter Inline-Prozess, reduzierte Kosten für Trocknung und Produkthandhabung;
reduzierter Kohlenstoff-Fußabdruck, da es sich um eine elektrothermische Technologie handelt.
Man kann daher sagen, dass die Radiofrequenztechnologie eine echte Revolution in der Latexschaumindustrie darstellt, sowohl in der Vulkanisierungs- als auch in der Trocknungsphase, die den Latexschaumherstellern enorme Vorteile in Bezug auf Produktionseffizienz, Kosteneinsparungen und Produktqualität bietet.