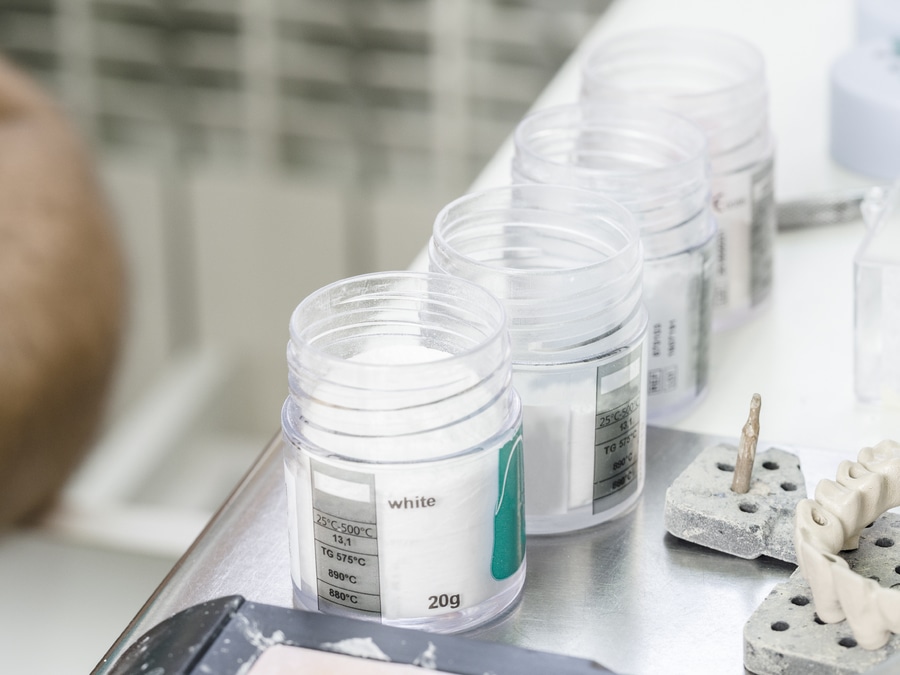
#Neues aus der Industrie
Vertikalmischer bereiten Hochleistungskeramik auf
Bei der Herstellung von technischer Keramik gibt es viele Parallelen zur Pulvermetallurgie. Die eingesetzten Rohstoffe sind teuer. Es handelt sich um Oxide, Nitride, Karbide oder Boride hochreiner Metalle.
Den keramischen Werkstoffen wird neben den Kunststoffen das größte Entwicklungspotential zugeschrieben, da sie in Bezug auf Festigkeit, Temperaturbeständigkeit und Härte als einzigartig gelten. Als hochtemperaturbeständiger Werkstoff in der Energieerzeugung wird Ingenieurkeramik ebenso eingesetzt wie als Korrosions-, Säure- und Verschleißschutz im Apparatebau oder als Hochfrequenzhalbleiter in der Nachrichtentechnik.
Bei der Herstellung von technischer Keramik gibt es viele Parallelen zur Pulvermetallurgie. Die eingesetzten Rohstoffe sind teuer. Es handelt sich um Oxide, Nitride, Karbide oder Boride hochreiner Metalle. Beispiele sind Aluminiumoxid, Aluminiumtitanat, Siliciumcarbid, Siliciumnitrid und Zirkonoxid. Aufgrund ihrer Sprödigkeit neigen keramische Bauteile zum „kritischen Versagen“. Bei der Herstellung von Hochleistungskeramiken ist daher auf höchste Reinheit zu achten.
Keramiken haben einzigartige Eigenschaften
Keramiken haben einzigartige spezifische Eigenschaften, die von keiner anderen Werkstoffgruppe erreicht werden: extreme Festigkeit, hohe Hitzebeständigkeit, Säurebeständigkeit, Duktilität, elektrische und thermische Leitfähigkeit, elektrische Isolation, optische Brechung, Transparenz, Farbtiefe usw.
Keramische Pulver werden mit größter Sorgfalt aufbereitet. In einigen Fällen werden die Ausgangskomponenten in einen Zustand mit extrem hoher spezifischer Oberfläche überführt. Die Partikelgrößen sind kleiner als 0,01 µm. Diese Art der Partikelzerkleinerung erfordert einen hohen Energieaufwand.
Derart kleine Partikel neigen dazu, spontan zu agglomerieren. Die Agglomerate müssen wieder in Primärpartikel aufgetrennt (desagglomeriert) werden, um eine gleichmäßige Gefügeausbildung des Sinterwerkstoffes zu gewährleisten. Die Prozesskette ist lang: Rohstoffgewinnung aus der chemischen Industrie, definierte Oberflächenvergrößerung, chemischer Aufschluss, Siebung, Dotierung, Homogenisierung, Dispergierung in der Nassphase, Fest-Flüssig-Trennung bis hin zur thermischen Trocknung, Homogenisierung/Vermischung. Die Stoffdiffusion erfolgt bei hohen Sintertemperaturen im Kalzinierofen. Die Abkühlung schließt den ersten Syntheseschritt ab. Danach folgen ähnliche oder andere Aufbereitungsschritte, die wieder mit dem Mahlen und Mischen beginnen. Wenn das Komposit Kunststoffpolymere enthält, können Synthesereaktionen trocken, feucht, nass und gasförmig im amixon® Mischer stattfinden.
Viele Kleinchargen werden in einer großen Charge homogenisiert
Die meisten Verfahren finden in kontinuierlich arbeitenden Prozessapparaten statt, deren Parametereinstellungen jeweils aus vorgeschalteten Stoffanalysen vorzunehmen sind. Insofern sind die kontinuierlich ablaufenden Einzelschritte jeweils abschnittsweise durchzuführen und die Zwischenprodukte jeweils als Charge in Containern, Silos, Mischern oder Big Bags zu sammeln. Repräsentative Analysen setzen voraus, dass die Gesamtmasse homogen vorliegt. Die in der Pulvermetallurgie zu homogenisierenden Chargengrößen variieren zwischen 5 l und 20 000 l. Zur Erzielung idealer Mischqualitäten werden amixon®-Mischer erfolgreich eingesetzt. Die dreidimensionale Umschichtungsströmung garantiert kurze Mischzeiten.
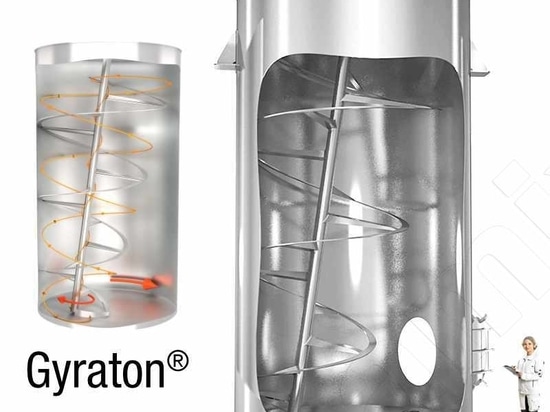